Hartlöten und Löten sind beides Methoden zum Verbinden von Metallen, sie unterscheiden sich jedoch erheblich hinsichtlich der erforderlichen Temperaturen und der Eigenschaften der verwendeten Zusatzwerkstoffe. Beim Hartlöten sind in der Regel höhere Temperaturen erforderlich als beim Löten, da Füllmetalle verwendet werden, die über 450 °C (840 °F) schmelzen, während beim Löten Füllmetalle zum Einsatz kommen, die unterhalb dieser Schwelle schmelzen. Dieser Temperaturunterschied wirkt sich auf die Festigkeit, Haltbarkeit und Anwendung der mit jeder Methode hergestellten Verbindungen aus. Im Folgenden untersuchen wir die wichtigsten Unterschiede zwischen Hartlöten und Weichlöten und konzentrieren uns dabei auf Temperaturanforderungen, Füllmaterialien und die daraus resultierenden Verbindungseigenschaften.
Wichtige Punkte erklärt:
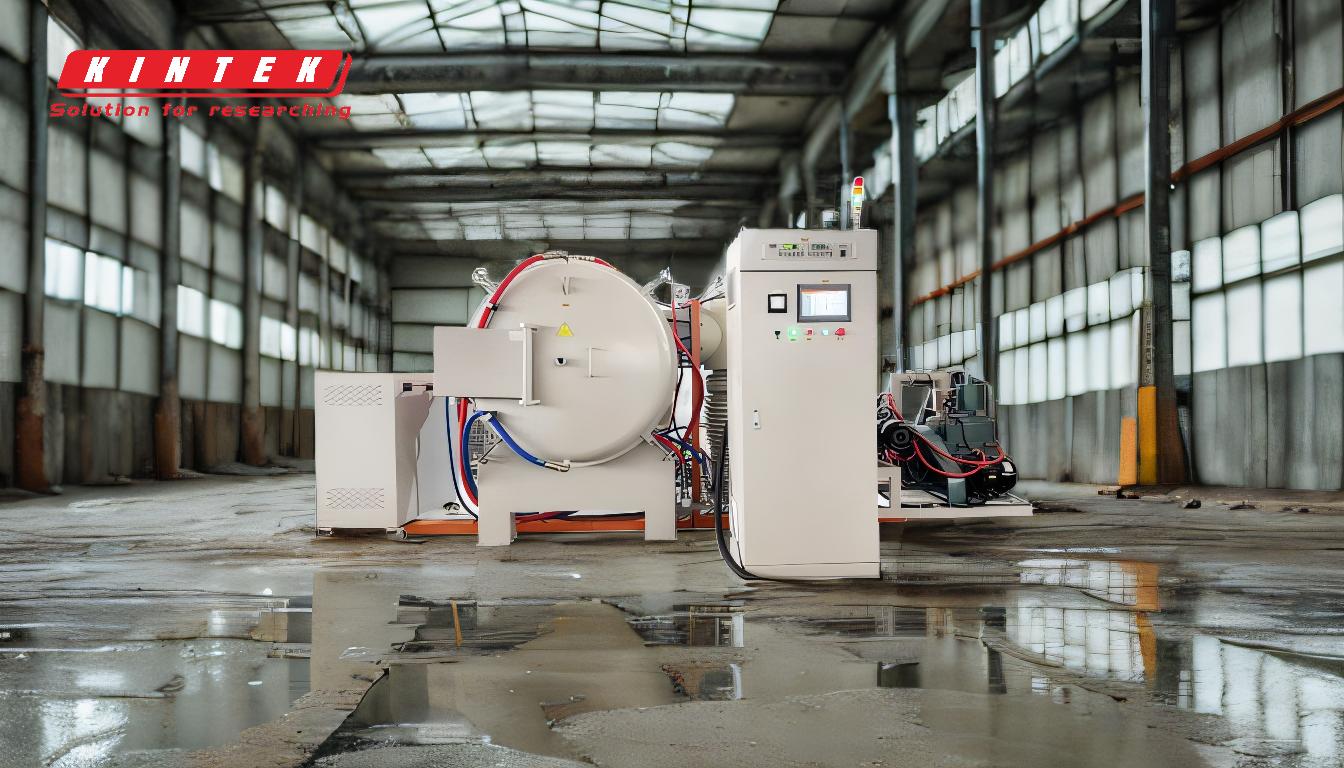
-
Temperaturanforderungen:
- Hartlöten: Löten erfordert höhere Temperaturen, typischerweise über 450 °C (840 °F). Dies liegt daran, dass die beim Hartlöten verwendeten Zusatzmetalle höhere Schmelzpunkte haben, wodurch mit dem Verfahren stärkere und haltbarere Verbindungen hergestellt werden können. Durch die hohen Temperaturen kann das Zusatzwerkstoff zudem durch Kapillarwirkung in die Verbindung fließen und so eine starke Verbindung gewährleisten.
- Löten: Das Löten hingegen erfolgt bei niedrigeren Temperaturen, unter 450°C. Die beim Löten verwendeten Zusatzmetalle haben niedrigere Schmelzpunkte, wodurch sich das Verfahren für empfindliche oder wärmeempfindliche Materialien eignet. Allerdings sind die resultierenden Verbindungen im Allgemeinen weniger stark als die durch Hartlöten hergestellten Verbindungen.
-
Füllmaterialien:
- Hartlöten: Die beim Hartlöten verwendeten Zusatzmetalle sind typischerweise Legierungen aus Kupfer, Silber oder Nickel. Diese Materialien haben hohe Schmelzpunkte und bieten eine hervorragende Festigkeit und Korrosionsbeständigkeit. Zu den gängigen Lotlegierungen gehören Füllstoffe auf Silberbasis und Kupfer-Phosphor-Legierungen.
- Löten: Beim Löten werden Zusatzmetalle wie Zinn-Blei-Legierungen, Zinn-Silber oder Zinn-Kupfer verwendet. Diese Materialien haben niedrigere Schmelzpunkte und werden aufgrund ihrer Fähigkeit ausgewählt, elektrische Verbindungen herzustellen oder dünne, empfindliche Komponenten zu verbinden, ohne diese zu beschädigen.
-
Gelenkstärke und Anwendungen:
- Hartlöten: Aufgrund der höheren Temperaturen und festeren Zusatzstoffe sind Lötverbindungen robuster und halten höheren mechanischen Belastungen und thermischen Belastungen stand. Dadurch eignet sich das Hartlöten für Anwendungen in Branchen wie der Automobilindustrie, der Luft- und Raumfahrt sowie der Heizungs-, Lüftungs- und Klimatechnik, wo starke, leckagefreie Verbindungen unerlässlich sind.
- Löten: Lötverbindungen sind weniger stark, eignen sich aber ideal für Anwendungen, bei denen elektrische Leitfähigkeit erforderlich ist, beispielsweise in der Elektronik- und Leiterplattenmontage. Aufgrund der niedrigeren Temperaturen eignet sich das Löten auch besser zum Verbinden wärmeempfindlicher Materialien.
-
Prozessunterschiede:
- Hartlöten: Beim Lötprozess werden die Grundmetalle auf eine Temperatur erhitzt, die über dem Schmelzpunkt des Zusatzmetalls, aber unter dem Schmelzpunkt der Grundmetalle liegt. Das Zusatzmetall wird dann durch Kapillarwirkung in die Verbindung gezogen und bildet beim Abkühlen eine starke Verbindung.
- Löten: Beim Löten werden die Grundmetalle erhitzt und das Zusatzmetall aufgetragen, das schmilzt und in die Verbindung fließt. Der Prozess ist in der Regel schneller und erfordert weniger Energie als das Hartlöten, wodurch er sich besser für kleine oder heikle Arbeiten eignet.
-
Vorteile und Einschränkungen:
- Hartlöten: Der Hauptvorteil des Hartlötens ist die Festigkeit und Haltbarkeit der dadurch hergestellten Verbindungen. Die erforderlichen höheren Temperaturen können jedoch die Verwendung bei wärmeempfindlichen Materialien einschränken und erfordern möglicherweise spezielle Ausrüstung.
- Löten: Löten ist aufgrund seiner geringeren Temperaturanforderungen und seiner Eignung für elektrische Verbindungen vorteilhaft. Allerdings sind die Verbindungen weniger stabil und möglicherweise nicht für Anwendungen mit hoher Belastung geeignet.
Zusammenfassend lässt sich sagen, dass beim Hartlöten aufgrund der unterschiedlichen Schmelzpunkte der verwendeten Zusatzwerkstoffe höhere Temperaturen erforderlich sind als beim Weichlöten. Diese Unterscheidung beeinflusst die Festigkeit, Haltbarkeit und Anwendungen der mit jeder Methode hergestellten Verbindungen. Hartlöten wird für hochfeste Anwendungen bevorzugt, während Löten ideal für elektrische und filigrane Arbeiten ist. Das Verständnis dieser Unterschiede ist entscheidend für die Auswahl der geeigneten Verbindungsmethode basierend auf den spezifischen Anforderungen des Projekts.
Übersichtstabelle:
Aspekt | Hartlöten | Löten |
---|---|---|
Temperatur | Über 450 °C (840 °F) | Unter 450°C |
Füllmaterialien | Kupfer-, Silber- oder Nickellegierungen (z. B. auf Silberbasis, Kupfer-Phosphor) | Zinn-Blei-, Zinn-Silber- oder Zinn-Kupfer-Legierungen |
Gemeinsame Stärke | Robust, langlebig und für Anwendungen mit hoher Beanspruchung geeignet | Weniger stark, ideal für elektrische Verbindungen und empfindliche Komponenten |
Anwendungen | Automobil, Luft- und Raumfahrt, HVAC (auslaufsichere Verbindungen) | Elektronik, Leiterplattenbestückung, wärmeempfindliche Materialien |
Verfahren | Höhere Energie, Kapillarwirkung für starke Bindungen | Geringerer Energieverbrauch, schneller und für Arbeiten im kleinen Maßstab geeignet |
Benötigen Sie Hilfe bei der Auswahl zwischen Hartlöten und Weichlöten für Ihr Projekt? Kontaktieren Sie noch heute unsere Experten!