Die physikalische Gasphasenabscheidung (PVD) ist eine hochentwickelte Technik zur Abscheidung dünner Materialschichten auf ein Substrat.Bei diesem Verfahren wird ein festes Zielmaterial in eine Dampfphase umgewandelt, die dann auf dem Substrat kondensiert und eine dünne, haltbare und oft hochspezialisierte Beschichtung bildet.Diese Methode ist in Branchen, die Hochleistungsbeschichtungen benötigen, weit verbreitet, z. B. in der Elektronik, Optik und Luft- und Raumfahrt.Das PVD-Verfahren wird in einer speziellen Kammer durchgeführt, die eine entscheidende Komponente des Systems darstellt.Die Kammer arbeitet unter niedrigem Druck und kontrollierten Bedingungen, um die präzise Abscheidung von Materialien zu gewährleisten.Zu den Schlüsselelementen der PVD-Kammer gehören die Prozesskammer, das Pumpsystem und die Steuerelektronik, die alle zusammenarbeiten, um die gewünschten Beschichtungseigenschaften zu erzielen.
Die wichtigsten Punkte werden erklärt:
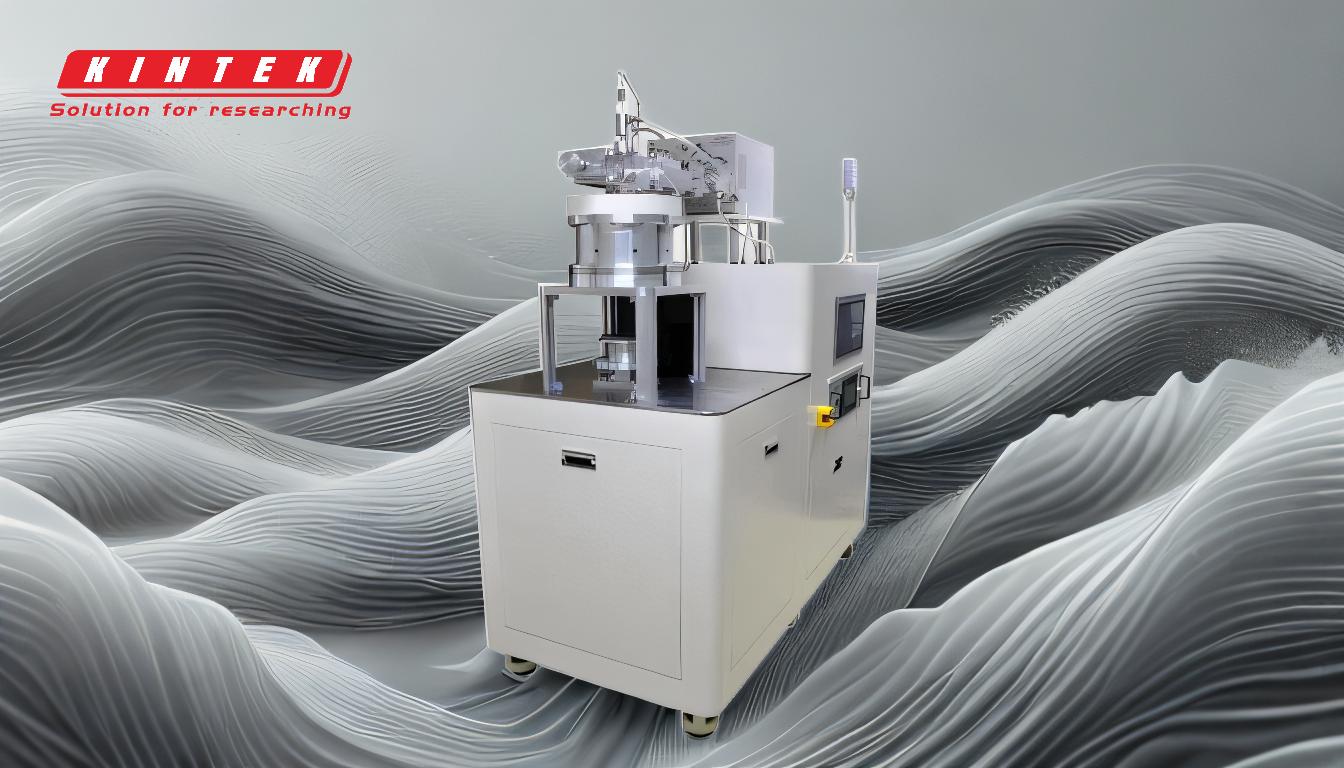
-
Umwandlung von der festen in die dampfförmige Phase
- Das PVD-Verfahren beginnt mit der Umwandlung eines festen Zielmaterials in eine Dampfphase.Dies wird durch Verfahren wie Sputtern, thermische Verdampfung oder Kathodenbogen erreicht.
- Unter Sputtern Beim Sputtern beschießen hochenergetische Ionen das Zielmaterial, lösen Atome ab und wandeln sie in Dampf um.
- Bei thermischen Verdampfung Bei der thermischen Verdampfung wird das Zielmaterial auf hohe Temperaturen erhitzt, bis es verdampft.
- Der Kathodenbogen Bei der Kathodenbogenmethode wird das Zielmaterial durch einen elektrischen Lichtbogen verdampft.
- Die Wahl des Verfahrens hängt von den Materialeigenschaften und den gewünschten Beschichtungseigenschaften ab.
-
Die Rolle der PVD-Kammer
- Die PVD-Kammer ist eine vakuumversiegelte Umgebung, in der der Beschichtungsprozess stattfindet.Sie ist so konzipiert, dass ein niedriger Druck aufrechterhalten wird, der normalerweise im Bereich von 10^-6 bis 10^-3 Torr liegt, um die Verunreinigung durch Hintergrundgase zu minimieren.
- In der Kammer befinden sich das Zielmaterial, das Substrat und die für die Verdampfung und Abscheidung erforderlichen Komponenten.
- Sie ist ausgestattet mit einem Pumpsystem um die erforderlichen Vakuumniveaus zu erreichen und aufrechtzuerhalten.Größere Kammern erfordern leistungsstärkere Pumpsysteme, um einen effizienten Betrieb zu gewährleisten.
-
Abscheidungsprozess
- Sobald das Zielmaterial verdampft ist, bewegen sich die Atome oder Ionen in einer "Sichtlinie" durch die Kammer.
- Das verdampfte Material kondensiert auf dem Substrat und bildet einen dünnen Film.Die Dicke und Gleichmäßigkeit des Films wird mit einem Quarzkristall-Ratenkontrolle .
- Das Substrat wird häufig in der Kammer gedreht oder bewegt, um eine gleichmäßige Verteilung der Beschichtung zu gewährleisten.
-
Steuerelektronik und Prozessregelung
- Das PVD-System wird von einer hochentwickelten Steuerelektronik gesteuert, die Parameter wie Temperatur, Druck und Abscheidungsrate regelt.
- Diese Steuerungen gewährleisten, dass der Prozess stabil und wiederholbar ist und Beschichtungen mit präzisen Eigenschaften erzeugt werden können.
- Die Elektronik überwacht auch den Zustand der Kammer und des Pumpensystems und alarmiert die Bediener bei Abweichungen von den gewünschten Bedingungen.
-
Anwendungen und Vorteile von PVD
- PVD wird zur Herstellung von Beschichtungen verwendet, die äußerst haltbar und korrosionsbeständig sind und auch extremen Temperaturen standhalten können.
-
Zu den üblichen Anwendungen gehören:
- Elektronik:Dünne Schichten für Halbleiter und Mikrochips.
- Optik:Antireflexions- und Schutzbeschichtungen für Linsen.
- Luft- und Raumfahrt:Verschleißfeste Beschichtungen für Turbinenschaufeln und andere Bauteile.
- Das Verfahren ermöglicht die Abscheidung von Schichten in Nanogröße mit außergewöhnlicher Präzision und ist damit ideal für die High-Tech-Industrie.
-
Überlegungen zur Konstruktion der PVD-Kammer
-
Bei der Konstruktion der PVD-Kammer müssen die spezifischen Anforderungen des Abscheidungsprozesses berücksichtigt werden, darunter:
- Größe und Geometrie:Größere Kammern können größere Substrate aufnehmen, erfordern aber auch leistungsfähigere Pumpsysteme.
- Material-Kompatibilität:Die Kammer muss aus Materialien gefertigt sein, die hohen Temperaturen und korrosiven Umgebungen standhalten können.
- Temperaturkontrolle:Die Kammer arbeitet bei Temperaturen von 50 bis 600 Grad Celsius, je nach Prozess.
- Die richtige Konstruktion der Kammer gewährleistet eine effiziente Materialausnutzung, minimale Verunreinigung und eine gleichbleibende Beschichtungsqualität.
-
Bei der Konstruktion der PVD-Kammer müssen die spezifischen Anforderungen des Abscheidungsprozesses berücksichtigt werden, darunter:
-
Vergleich von PVD-Verfahren
- Sputtern:Ideal für die Abscheidung von Metallen, Legierungen und Keramiken.Sorgt für eine hervorragende Gleichmäßigkeit und Haftung des Films.
- Thermische Verdampfung:Am besten geeignet für Materialien mit niedrigem Schmelzpunkt.Bietet hohe Abscheidungsraten, kann aber zu weniger gleichmäßigen Beschichtungen führen.
- Kathodenbogen:Geeignet für harte Beschichtungen wie Titannitrid.Erzeugt dichte, hochwertige Schichten, kann aber Partikel erzeugen.
Zusammenfassend lässt sich sagen, dass die PVD-Kammer das Herzstück des Physical Vapor Deposition-Verfahrens ist und die präzise und kontrollierte Abscheidung von dünnen Schichten ermöglicht.Wenn man die Schlüsselkomponenten und die beteiligten Prozesse versteht, kann man die Komplexität und Vielseitigkeit dieser Technologie, die weiterhin eine wichtige Rolle bei der Weiterentwicklung der Materialwissenschaft und der industriellen Anwendungen spielt, nachvollziehen.
Zusammenfassende Tabelle:
Aspekt | Einzelheiten |
---|---|
Prozess | Umwandlung von festem Zielmaterial in Dampf, der auf einem Substrat kondensiert. |
Verfahren | Kathodenzerstäubung, thermische Verdampfung, Kathodenbogen. |
Rolle der Kammer | Vakuumversiegelte Umgebung für präzise Abscheidung. |
Wichtige Komponenten | Prozesskammer, Pumpsystem, Steuerelektronik. |
Anwendungen | Elektronik, Optik, Luft- und Raumfahrt und mehr. |
Vorteile | Langlebige, korrosionsbeständige, hochpräzise Beschichtungen. |
Entdecken Sie, wie PVD Ihre industriellen Anwendungen verbessern kann. Kontaktieren Sie unsere Experten noch heute !