Das Metall-Lasersintern (MLS) ist ein hochentwickeltes additives Fertigungsverfahren, bei dem ein Hochleistungslaser verwendet wird, um Metallpulverpartikel Schicht für Schicht zu einem festen, dreidimensionalen Objekt zu verschmelzen.Dieses Verfahren ist in Branchen wie der Luft- und Raumfahrt, der Automobilindustrie und der Medizintechnik weit verbreitet, da es komplexe Geometrien mit hoher Präzision und Materialeffizienz herstellen kann.Das Verfahren umfasst mehrere wichtige Schritte, darunter die Pulveraufbereitung, das Lasersintern und die Nachbearbeitung, von denen jeder eine entscheidende Rolle für die gewünschten Eigenschaften des Endprodukts spielt.
Die wichtigsten Punkte erklärt:
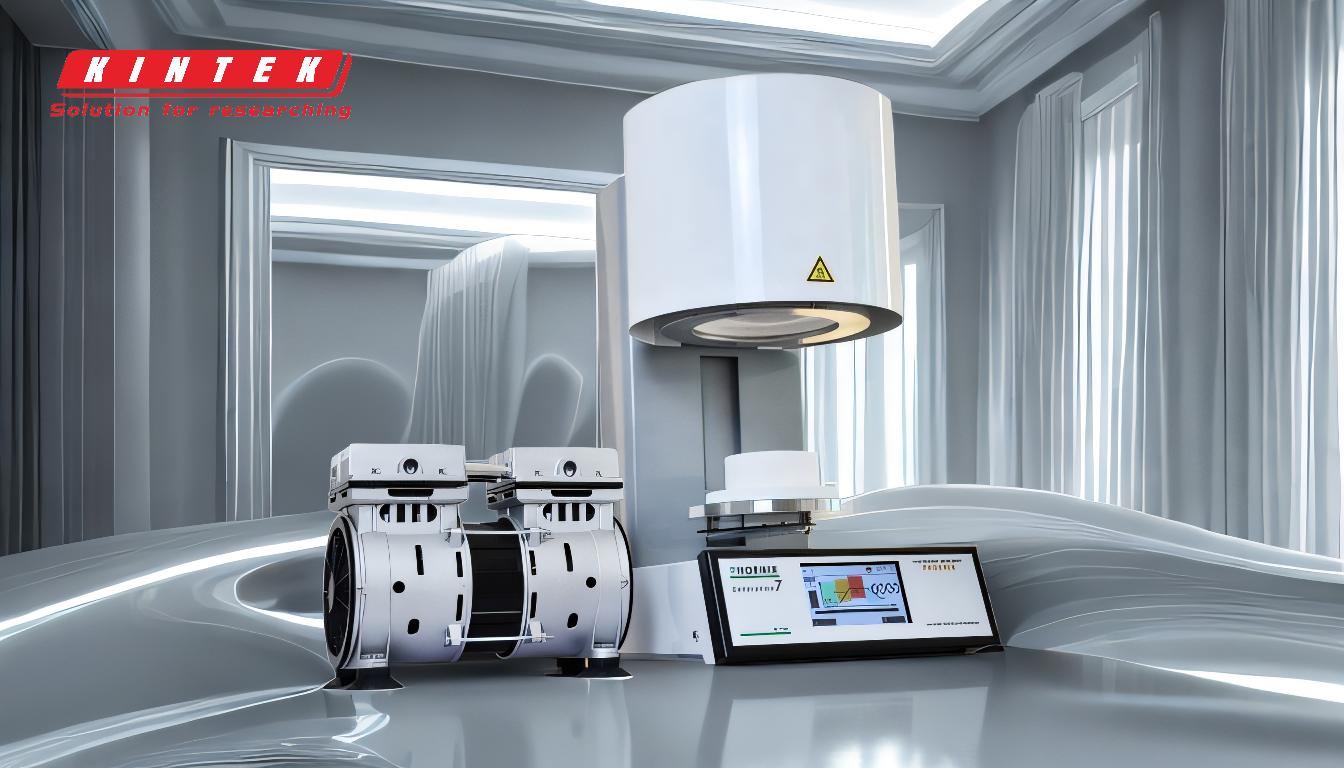
-
Vorbereitung des Pulvers:
- Auswahl der Materialien:Das Verfahren beginnt mit der Auswahl der geeigneten Metallpulver.Zu den gängigen Materialien gehören Titan, Aluminium, Edelstahl und Nickelbasislegierungen.Die Wahl des Materials hängt von den gewünschten Eigenschaften des Endprodukts ab, wie Festigkeit, Haltbarkeit und Wärmebeständigkeit.
- Pulvermischung:Die Metallpulver werden häufig mit Legierungselementen und Zusatzstoffen vermischt, um bestimmte Eigenschaften zu verbessern.Diese Mischung gewährleistet ein homogenes Gemisch, das zu einem einheitlichen Endprodukt führt.
-
Prozess des Lasersinterns:
- Schichtabscheidung:Eine dünne Schicht des Metallpulvers wird gleichmäßig auf die Bauplattform aufgetragen.Die Dicke dieser Schicht liegt in der Regel im Bereich von 20-100 Mikrometern, je nach gewünschter Auflösung und spezifischer Anwendung.
- Laserschmelzen:Ein Hochleistungslaserstrahl wird auf das Pulverbett gerichtet und schmilzt die Pulverpartikel entsprechend dem digitalen 3D-Modell des Teils selektiv auf.Die Energie des Lasers wird präzise gesteuert, um sicherzustellen, dass die Metallpartikel miteinander verschmelzen, ohne übermäßige thermische Verformungen zu verursachen.
- Layer Bonding:Jede gesinterte Schicht verbindet sich mit den vorher gesinterten Schichten darunter.Dieser schichtweise Ansatz ermöglicht die Herstellung komplexer Geometrien und innerer Strukturen, die mit herkömmlichen Herstellungsverfahren nur schwer oder gar nicht zu erreichen wären.
-
Kontrollierte Atmosphäre:
- Inertes Gas Umgebung:Der Sinterprozess findet in der Regel in einer kontrollierten Atmosphäre statt, die häufig mit Inertgasen wie Argon oder Stickstoff gefüllt ist.Diese Umgebung verhindert Oxidation und Verunreinigung des Metalls und gewährleistet die Integrität und Qualität des Endprodukts.
- Temperaturkontrolle:Der Sinterofen hält eine präzise Temperatur aufrecht, die in der Regel knapp unter dem Schmelzpunkt des Metalls liegt, um die atomare Diffusion und Bindung zwischen den Partikeln zu erleichtern, ohne dass diese vollständig schmelzen.
-
Nachbearbeiten:
- Entfernung von überschüssigem Puder:Nach Abschluss des Sinterprozesses wird das überschüssige Pulver, das nicht durch den Laser geschmolzen wurde, entfernt.Dieses Pulver kann häufig recycelt und bei späteren Aufträgen wiederverwendet werden.
- Wärmebehandlung:Je nach Werkstoff und gewünschten Eigenschaften kann das Sinterteil zusätzlichen Wärmebehandlungen wie Glühen oder Spannungsarmglühen unterzogen werden, um seine mechanischen Eigenschaften zu verbessern.
- Oberflächenveredelung:Der letzte Schritt umfasst häufig Oberflächenbehandlungen wie Bearbeiten, Polieren oder Beschichten, um die gewünschte Oberflächenqualität und Maßhaltigkeit zu erreichen.
-
Vorteile und Anwendungen:
- Komplexe Geometrien:MLS ermöglicht die Herstellung von Teilen mit komplexen inneren Strukturen und komplizierten Details, die mit herkömmlichen Fertigungsmethoden nicht machbar sind.
- Effizienz des Materials:Das Verfahren ist äußerst materialsparend, da nur die Menge an Pulver verwendet wird, die für die Herstellung des Teils erforderlich ist, wodurch der Abfall minimiert wird.
- Kundenspezifische Anpassung und Prototyping:MLS ist besonders wertvoll für das Rapid Prototyping und die kundenspezifische Fertigung und ermöglicht eine schnelle Iteration und Anpassung von Designs.
- Industrie Anwendungen:Die Technologie ist in Branchen, die Hochleistungskomponenten benötigen, weit verbreitet, z. B. in der Luft- und Raumfahrt für Leichtbaustrukturen, in der Automobilindustrie für Spezialteile und in der Medizintechnik für patientenspezifische Implantate.
Zusammenfassend lässt sich sagen, dass das Metall-Lasersintern ein vielseitiges und präzises Fertigungsverfahren ist, bei dem Metallpulver mit Hilfe von Lasern zu komplexen, leistungsstarken Teilen verschmolzen wird.Das Verfahren erfordert eine sorgfältige Vorbereitung der Werkstoffe, eine präzise Steuerung der Sinterumgebung und eine gründliche Nachbearbeitung, um die gewünschten Eigenschaften und das gewünschte Finish zu erzielen.Diese Technologie revolutioniert weiterhin die Fertigung, da sie die Herstellung von Teilen ermöglicht, die mit herkömmlichen Methoden nicht zu realisieren waren.
Zusammenfassende Tabelle:
Wichtige Schritte | Einzelheiten |
---|---|
Vorbereitung des Pulvers | - Materialauswahl (z. B. Titan, Aluminium, Edelstahl). |
- Pulvermischung für einheitliche Eigenschaften. | |
Laser-Sintern | - Schichtabscheidung (20-100 Mikrometer). |
- Laserschmelzen für präzises Schmelzen.
- Schichtverleimung für komplexe Geometrien.| | Kontrollierte Atmosphäre
- | - Inertgasumgebung (Argon oder Stickstoff). Präzise Temperaturkontrolle.| |
- Nachbearbeitung
- | - Entfernung von überschüssigem Pulver. Wärmebehandlung (Glühen, Spannungsarmglühen). Oberflächenveredelung (Bearbeiten, Polieren).|
- |
- Vorteile | - Komplexe Geometrien. Materialeffizienz.
Schnelles Prototyping und kundenspezifische Anpassung.| | Anwendungen