Die Sintertemperatur ist typischerweise viel niedriger als die Schmelztemperatur des zu sinternden Materials. Dies liegt daran, dass beim Sintern die Anwendung von Wärme und Druck erforderlich ist, um die Partikel miteinander zu verschmelzen, ohne dass sie den Punkt der Verflüssigung erreichen. Durch den Betrieb unterhalb des Schmelzpunkts bewahrt das Sintern die strukturelle Integrität des Materials, spart Energie und ermöglicht eine bessere Kontrolle über das Endprodukt. Diese Unterscheidung ist für Materialien mit hohem Schmelzpunkt von entscheidender Bedeutung, da das Sintern eine energieeffizientere und praktischere Alternative zum Schmelzen darstellt.
Wichtige Punkte erklärt:
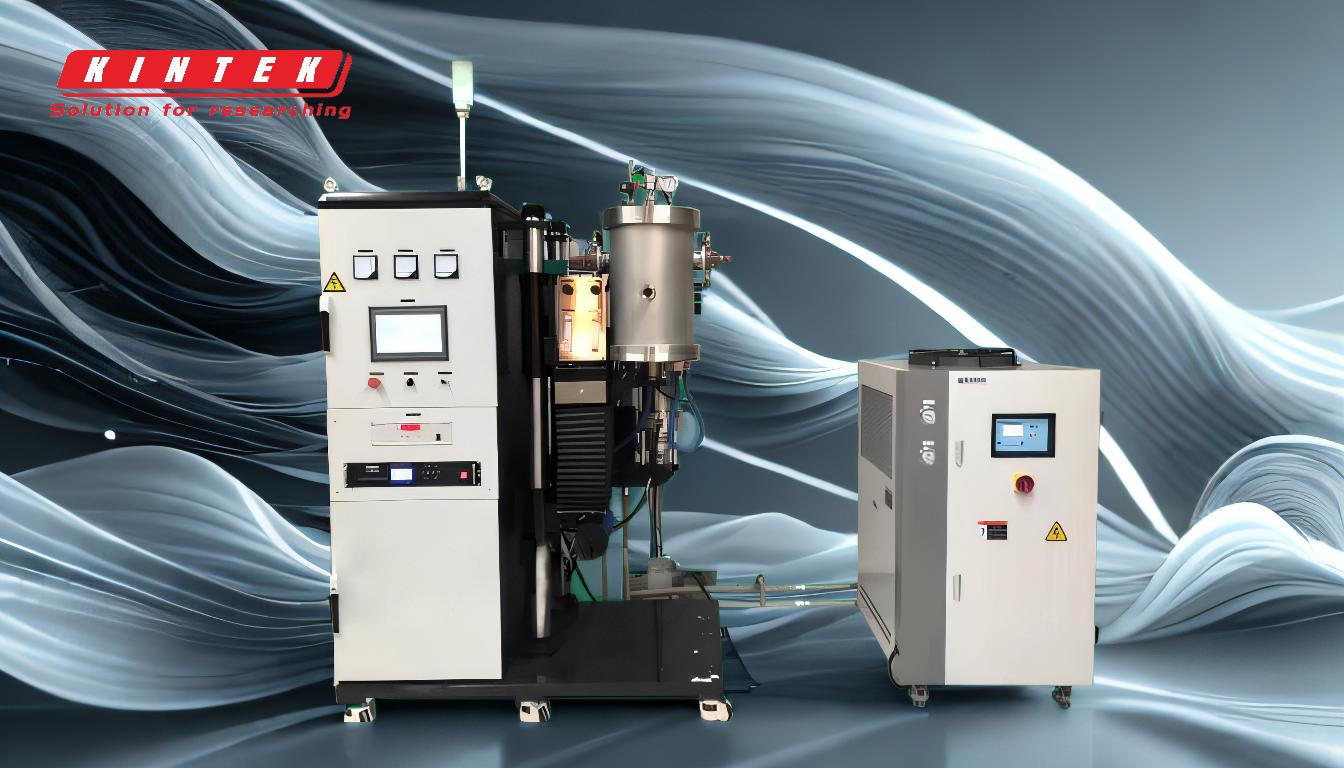
-
Die Sintertemperatur liegt unter der Schmelztemperatur:
- Das Sintern erfolgt bei Temperaturen, die deutlich unter dem Schmelzpunkt des Materials liegen. Dies ist ein grundlegendes Merkmal des Sinterprozesses, da er eine Verflüssigung vermeidet und dennoch eine Partikelverschmelzung ermöglicht.
- Wenn ein Metall beispielsweise einen Schmelzpunkt von 1500 °C hat, kann das Sintern je nach Material und Prozessanforderungen bei 1200 °C oder niedriger durchgeführt werden.
-
Energieeffizienz:
- Da beim Sintern bei niedrigeren Temperaturen gearbeitet wird, verbraucht es weniger Energie im Vergleich zum Schmelzen, bei dem das Material auf seinen vollen Schmelzpunkt erhitzt werden muss.
- Dies macht das Sintern zu einer nachhaltigeren und kostengünstigeren Methode, insbesondere für Materialien mit hohen Schmelzpunkten.
-
Wahrung der strukturellen Integrität:
- Durch die Vermeidung einer Verflüssigung verhindert das Sintern, dass das Material seine Form oder Struktureigenschaften verliert. Dies ist besonders wichtig, um komplexe Formen zu erstellen oder bestimmte Materialeigenschaften beizubehalten.
- In der Pulvermetallurgie beispielsweise ermöglicht das Sintern die Herstellung starker, langlebiger Komponenten, ohne dass das Design beeinträchtigt wird.
-
Rolle des Drucks beim Sintern:
- Beim Sintern wird Wärme mit Druck kombiniert, um die Partikelbindung zu erleichtern. Die Anwendung von Druck gleicht die niedrigere Temperatur aus und sorgt so für eine effektive Fusion, ohne dass ein Schmelzen erforderlich ist.
- Diese Kombination aus Hitze und Druck unterscheidet das Sintern von anderen Verfahren wie Schmelzen oder Gießen.
-
Kontrolle über das Endprodukt:
- Der Betrieb unterhalb des Schmelzpunkts bietet eine bessere Kontrolle über die Mikrostruktur und die Eigenschaften des Endprodukts. Dies ist von entscheidender Bedeutung für Anwendungen, die präzise Materialeigenschaften erfordern, beispielsweise in der Luft- und Raumfahrt oder bei medizinischen Geräten.
- Beispielsweise kann das Sintern fein abgestimmt werden, um bestimmte Dichten, Porositäten oder mechanische Eigenschaften zu erreichen.
-
Praktische Anwendungen:
- Sintern wird häufig in Branchen eingesetzt, in denen hohe Schmelzpunkte oder Materialintegrität von entscheidender Bedeutung sind. Beispiele hierfür sind die Keramikherstellung, die Metallpulververarbeitung und die Herstellung von Verbundwerkstoffen.
- Seine Fähigkeit, mit Materialien mit hohem Schmelzpunkt wie Wolfram oder Keramik zu arbeiten, macht es für die moderne Fertigung unverzichtbar.
-
Vergleich mit Schmelzen:
- Zum Schmelzen sind Temperaturen erforderlich, die über dem Schmelzpunkt des Materials liegen und zu einer vollständigen Verflüssigung führen. Dieser Prozess ist energieintensiv und führt häufig zum Verlust der strukturellen Kontrolle.
- Im Gegensatz dazu bietet das Sintern eine kontrollierte und effizientere Alternative, insbesondere für Materialien, die schwer oder unpraktisch zu schmelzen sind.
Durch das Verständnis der Beziehung zwischen Sintertemperatur und Schmelztemperatur können Hersteller ihre Prozesse hinsichtlich Energieeffizienz, Materialintegrität und Produktqualität optimieren. Diese Unterscheidung ist der Schlüssel zur Nutzung des Sinterns als vielseitige und effektive Fertigungstechnik.
Übersichtstabelle:
Schlüsselaspekt | Einzelheiten |
---|---|
Temperaturbereich | Das Sintern erfolgt unterhalb des Schmelzpunkts, z. B. 1200 °C gegenüber 1500 °C bei Metallen. |
Energieeffizienz | Niedrigere Temperaturen reduzieren den Energieverbrauch im Vergleich zum Schmelzen. |
Strukturelle Integrität | Verhindert Verflüssigung und bewahrt Form und Materialeigenschaften. |
Rolle des Drucks | Kombiniert Hitze und Druck für eine effektive Partikelbindung. |
Kontrolle über das Endprodukt | Ermöglicht die Feinabstimmung von Dichte, Porosität und mechanischen Eigenschaften. |
Anwendungen | Wird in Keramik, Metallpulvern und Verbundwerkstoffen für hochschmelzende Materialien verwendet. |
Vergleich mit Schmelzen | Energieeffizienter und praktischer für Materialien mit hohen Schmelzpunkten. |
Sie möchten Ihren Sinterprozess optimieren? Kontaktieren Sie noch heute unsere Experten für maßgeschneiderte Lösungen!