Das PVD-Beschichtungsverfahren (Physical Vapor Deposition, physikalische Gasphasenabscheidung) ist eine hochentwickelte Technik zum Aufbringen dünner, haltbarer Schichten auf verschiedene Materialien, vor allem Metalle.Die Dauer des Verfahrens kann erheblich variieren und liegt in der Regel zwischen 30 Minuten und 2 Stunden, abhängig von Faktoren wie der gewünschten Schichtdicke, der Größe des Werkstücks und der Art des verwendeten PVD-Verfahrens.Die Schichtdicke liegt in der Regel zwischen 0,25 und 5 Mikrometern, und der Prozess umfasst mehrere wichtige Schritte:Verdampfung, Reaktion und Abscheidung.Jeder Schritt spielt eine entscheidende Rolle bei der Bestimmung der endgültigen Eigenschaften der Beschichtung, wie z. B. Härte, Farbe und Beständigkeit gegen Korrosion und Oxidation.
Die wichtigsten Punkte werden erklärt:
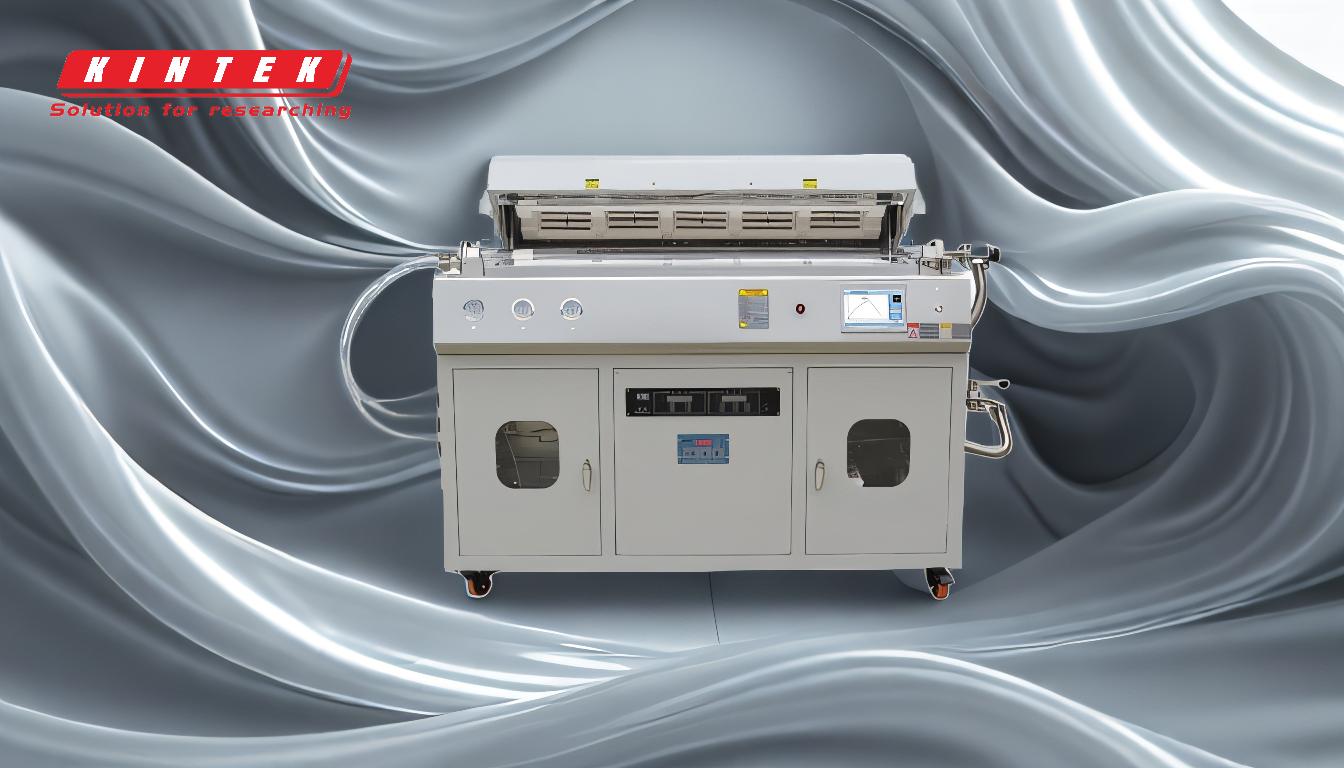
-
Dauer des PVD-Beschichtungsprozesses:
- Das PVD-Beschichtungsverfahren dauert im Allgemeinen zwischen 30 Minuten und 2 Stunden.Kleinere oder einfachere Teile können weniger Zeit benötigen, während größere oder komplexere Teile länger dauern können.
- Die benötigte Zeit kann auch von der gewünschten Beschichtungsdicke abhängen, wobei dickere Beschichtungen eine längere Bearbeitungszeit erfordern.
-
Dicke der Beschichtung:
- PVD-Beschichtungen sind in der Regel sehr dünn und reichen von 0,25 bis 5 Mikrometer.Diese dünne Schicht reicht aus, um Eigenschaften wie Härte, Korrosionsbeständigkeit und ästhetisches Erscheinungsbild deutlich zu verbessern.
- Die Dicke der Beschichtung ist ein entscheidender Faktor für die Gesamtlebensdauer und Leistung des beschichteten Materials.
-
Arten von PVD-Beschichtungsprozessen:
- Sputter-Beschichtung: Beschuss eines Zielmaterials mit hochenergetischen Ionen, um Atome auszustoßen, die sich dann auf dem Substrat ablagern.
- Thermische Verdampfung: Das Beschichtungsmaterial wird durch Hitze verdampft und kondensiert dann auf dem Substrat.
- Elektronenstrahl-Verdampfung: Mit Hilfe eines Elektronenstrahls wird das Beschichtungsmaterial erhitzt und verdampft.
- Ionenbeschichtung: Kombiniert Verdampfung mit Ionenbeschuss, um die Haftung und Dichte der Beschichtung zu verbessern.
- Jedes Verfahren hat seine eigenen Merkmale und Vorteile und eignet sich daher für unterschiedliche Anwendungen und Materialien.
-
Schritte im PVD-Beschichtungsprozess:
- Verdampfung: Das Zielmaterial wird durch verschiedene Methoden wie Sputtern oder Verdampfen in Dampf umgewandelt.
- Reaktion: Das verdampfte Material reagiert mit den Gasen in der Kammer und bildet Verbindungen, die die Eigenschaften der Beschichtung bestimmen, z. B. Härte und Farbe.
- Abscheidung: Das verdampfte und umgesetzte Material lagert sich auf dem Substrat ab und bildet eine dünne, gleichmäßige Schicht.
-
Eigenschaften und Anwendungen:
- PVD-Beschichtungen sind äußerst korrosions- und oxidationsbeständig und eignen sich daher ideal für den Einsatz in rauen Umgebungen.
- Die Härte der Beschichtung ist ein entscheidender Faktor für ihre Haltbarkeit, wobei Materialien wie TiN (Titannitrid) die Ermüdungsgrenze und die Lebensdauer des Substrats deutlich erhöhen.
- PVD-Beschichtungen werden in der Regel auf Edelstahl aufgebracht und bieten je nach Oberflächenvorbereitung eine Vielzahl von Oberflächen wie poliert, gebürstet, satiniert oder matt.
-
Oberflächenvorbereitung:
- Die Oberflächenbeschaffenheit des Substrats ist entscheidend für das Erreichen der gewünschten Oberfläche.Polierte oder spiegelnde Oberflächen werden für polierte PVD-Beschichtungen verwendet, während gebürstete oder satinierte Oberflächen für satinierte oder matte Beschichtungen verwendet werden.
- PVD-Beschichtungen gleichen Oberflächenunebenheiten nicht aus, so dass das Substrat vor dem Beschichtungsprozess entsprechend vorbereitet werden muss.
Die Kenntnis dieser wichtigen Punkte kann bei der Auswahl des geeigneten PVD-Beschichtungsprozesses und der Parameter für bestimmte Anwendungen helfen, um eine optimale Leistung und Langlebigkeit der beschichteten Materialien zu gewährleisten.
Zusammenfassende Tabelle:
Aspekt | Einzelheiten |
---|---|
Dauer | 30 Minuten bis 2 Stunden, je nach Werkstückgröße und Schichtdicke. |
Dicke der Beschichtung | 0,25 Mikrometer bis 5 Mikrometer, bietet Härte, Korrosionsbeständigkeit und mehr. |
Verfahrensarten | Sputterbeschichtung, thermische Verdampfung, Elektronenstrahlverdampfung, Ionenplattierung. |
Wichtigste Schritte | Verdampfung, Reaktion, Abscheidung. |
Anwendungen | Korrosionsbeständigkeit, verbesserte Härte und ästhetische Oberflächen für Metalle. |
Optimieren Sie Ihre Werkstoffe mit PVD-Beschichtungen - Kontaktieren Sie unsere Experten noch heute für maßgeschneiderte Lösungen!