Härteprozesse sind in der Getriebeherstellung und anderen Branchen von entscheidender Bedeutung, um die mechanischen Eigenschaften von Materialien, insbesondere ihre Härte und Verschleißfestigkeit, zu verbessern. Häufig verwendete Härteverfahren lassen sich grob in drei Haupttypen einteilen: durch Härten, Einsatzhärten (einschließlich Aufkohlen, Karbonitrieren, Nitrieren und Nitrocarburieren) und Härten durch angewandte Energie (wie Flammen-, Laser- und Induktionshärten). Jede Methode verfügt über unterschiedliche Mechanismen, Anwendungen und Vorteile, sodass sie für unterschiedliche Materialtypen und industrielle Anforderungen geeignet sind.
Wichtige Punkte erklärt:
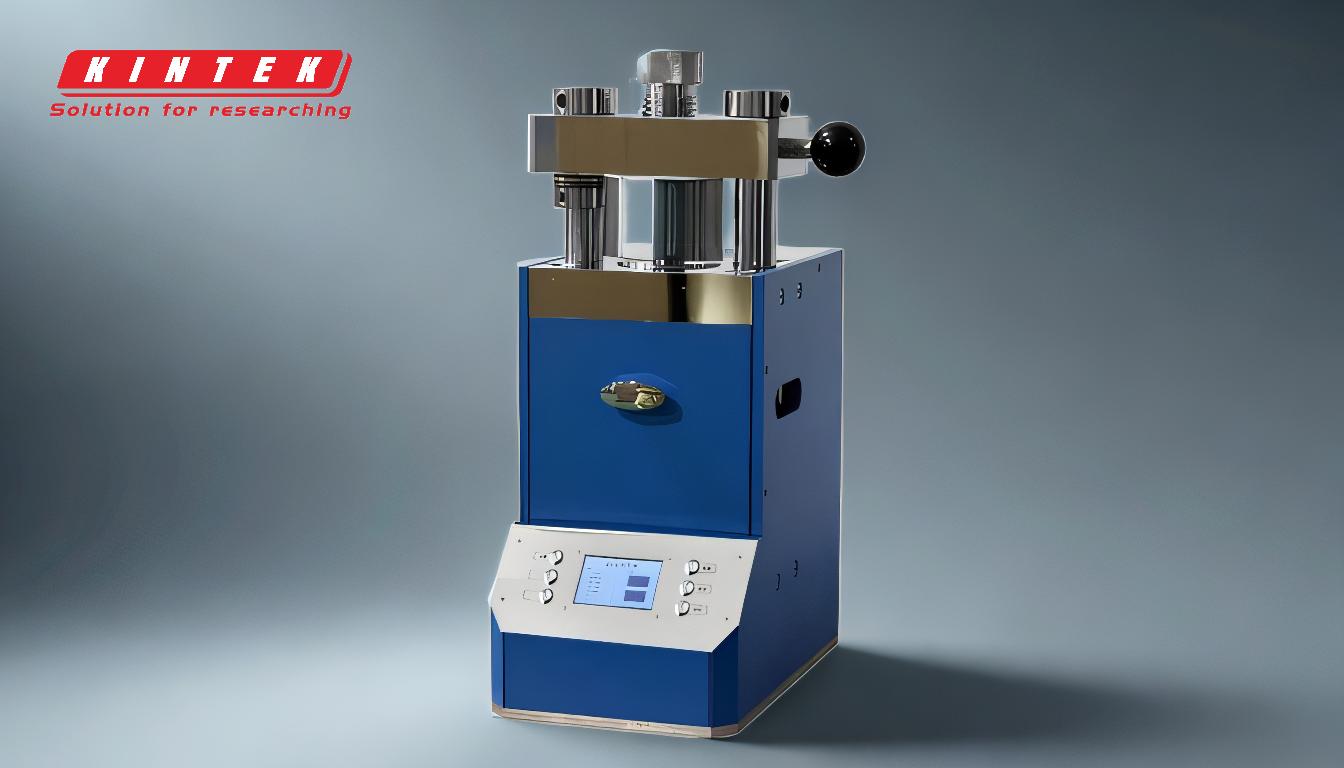
-
Durch Härten
- Definition: Beim Durchhärten, auch Massenhärten genannt, wird das gesamte Material auf eine bestimmte Temperatur erhitzt, über einen festgelegten Zeitraum gehalten und anschließend schnell abgekühlt (Abschrecken), um eine gleichmäßige Härte im gesamten Material zu erreichen.
- Verfahren: Das Material wird in einem Ofen auf eine Temperatur erhitzt, die seine innere Struktur umwandelt (normalerweise über der Austenitisierungstemperatur), ohne es zu schmelzen. Anschließend wird es für eine bestimmte Zeit (z. B. eine Stunde pro Zoll Dicke) auf dieser Temperatur gehalten und in Öl, Wasser oder Luft abgeschreckt.
- Anwendungen: Geeignet für Materialien, die in ihrer gesamten Struktur eine gleichmäßige Härte und Festigkeit erfordern, wie z. B. Zahnräder, Wellen und Werkzeuge.
- Vorteile: Sorgt für eine gleichmäßige Härte der gesamten Komponente und verbessert so die allgemeine Haltbarkeit und Verschleißfestigkeit.
- Einschränkungen: Kann bei einigen Materialien zu Sprödigkeit führen und erfordert ein Anlassen, um innere Spannungen zu reduzieren.
-
Einsatzhärten
- Definition: Einsatzhärtung ist ein Oberflächenhärtungsprozess, der die Härte der äußeren Schicht (Hülle) des Materials erhöht und gleichzeitig einen weicheren, härteren Kern erhält. Dies wird durch das Einbringen von Kohlenstoff oder Stickstoff in die Oberflächenschicht erreicht.
-
Arten der Einsatzhärtung:
- Aufkohlen: Beinhaltet das Einbringen von Kohlenstoff in die Oberflächenschicht durch Erhitzen des Materials in einer kohlenstoffreichen Umgebung (z. B. Gas-, Flüssigkeits- oder Feststoffaufkohlung). Der Kohlenstoff diffundiert in die Oberfläche und erzeugt ein hartes, verschleißfestes Gehäuse.
- Karbonitrieren: Ähnlich wie beim Aufkohlen, bei dem jedoch sowohl Kohlenstoff als auch Stickstoff in die Oberflächenschicht eingebracht werden. Dieses Verfahren wird häufig für Stähle mit niedrigem Kohlenstoffgehalt verwendet und sorgt für eine härtere Hülle mit verbesserter Verschleißfestigkeit.
- Nitrieren: Beinhaltet das Einbringen von Stickstoff in die Oberflächenschicht durch Erhitzen des Materials in einer stickstoffreichen Umgebung (z. B. Gas- oder Plasmanitrieren). Das Nitrieren erfolgt bei niedrigeren Temperaturen als das Aufkohlen und erfordert kein Abschrecken.
- Nitrocarburieren: Kombiniert Nitrieren und Aufkohlen, um sowohl Stickstoff als auch Kohlenstoff in die Oberflächenschicht einzubringen. Dieses Verfahren wird häufig für Bauteile eingesetzt, die eine hohe Verschleißfestigkeit und Dauerfestigkeit erfordern.
- Anwendungen: Ideal für Komponenten, die eine harte, verschleißfeste Oberfläche und einen robusten Kern erfordern, wie z. B. Zahnräder, Nockenwellen und Lager.
- Vorteile: Verbessert die Oberflächenhärte und Verschleißfestigkeit bei gleichzeitiger Beibehaltung der Zähigkeit des Kerns.
- Einschränkungen: Beschränkt auf die Oberflächenhärtung, und der Prozess kann zeitaufwändig und teuer sein.
-
Härten durch angewandte Energie
- Definition: Diese Kategorie umfasst lokalisierte Härtungsprozesse, bei denen konzentrierte Energiequellen zum Erhitzen bestimmter Bereiche des Materials verwendet werden, gefolgt von einer schnellen Abkühlung.
-
Arten der angewandten Energiehärtung:
- Flammhärten: Verwendet eine Sauerstoff-Acetylen-Flamme, um die Oberfläche des Materials zu erhitzen, gefolgt von einem Abschrecken. Diese Methode eignet sich für große Bauteile und unregelmäßige Formen.
- Laserhärten: Verwendet einen hochenergetischen Laserstrahl, um die Oberfläche des Materials zu erhitzen und anschließend schnell abzukühlen. Diese Methode ermöglicht eine präzise Kontrolle des gehärteten Bereichs und eignet sich für komplexe Geometrien.
- Induktionshärten: Verwendet elektromagnetische Induktion, um die Oberfläche des Materials zu erhitzen und anschließend abzuschrecken. Diese Methode ist hocheffizient und für die Massenproduktion geeignet.
- Anwendungen: Wird für Komponenten verwendet, die eine lokale Härtung erfordern, wie z. B. Zahnradzähne, Kurbelwellen und Nockenwellen.
- Vorteile: Bietet eine präzise Kontrolle über den gehärteten Bereich, minimiert Verzerrungen und ist für die Massenproduktion geeignet.
- Einschränkungen: Beschränkt sich auf die Oberflächenhärtung und erfordert spezielle Ausrüstung.
Zusammenfassend hängt die Wahl des Härteverfahrens von der Materialart, dem Bauteildesign und den gewünschten mechanischen Eigenschaften ab. Durchhärtung ist ideal für gleichmäßige Härte, Einsatzhärtung eignet sich für Oberflächenhärte mit zähem Kern und Härtung durch Energieeinwirkung eignet sich perfekt für lokales Härten mit minimalem Verzug. Jede Methode bietet einzigartige Vorteile und Einschränkungen, wodurch sie für bestimmte industrielle Anwendungen geeignet ist.
Übersichtstabelle:
Härteprozess | Definition | Anwendungen | Vorteile | Einschränkungen |
---|---|---|---|---|
Durch Härten | Gleichmäßiges Erhitzen und Abschrecken für gleichmäßige Härte im gesamten Material. | Zahnräder, Wellen, Werkzeuge. | Gleichbleibende Härte, verbesserte Haltbarkeit. | Kann spröde werden, erfordert Anlassen. |
Einsatzhärten | Oberflächenhärtung mit zähem Kern durch Einbringen von Kohlenstoff oder Stickstoff. | Zahnräder, Nockenwellen, Lager. | Harte Oberfläche, zäher Kern, erhöhte Verschleißfestigkeit. | Zeitaufwändig, teuer, auf Oberflächenhärtung beschränkt. |
Härten durch angewandte Energie | Lokalisiertes Härten mithilfe von Energiequellen wie Flamme, Laser oder Induktion. | Verzahnungen, Kurbelwellen, Nockenwellen. | Präzise Steuerung, minimale Verzerrung, hohe Effizienz. | Erfordert spezielle Ausrüstung, die auf die Oberflächenhärtung beschränkt ist. |
Benötigen Sie Hilfe bei der Auswahl des richtigen Härteverfahrens für Ihre Anwendung? Kontaktieren Sie noch heute unsere Experten !