Die chemische Gasphasenabscheidung (CVD) ist ein vielseitiges Verfahren, mit dem durch die Reaktion gasförmiger Vorläufer dünne Materialfilme auf Substraten abgeschieden werden. Die Dicke von CVD-Beschichtungen kann je nach Anwendung erheblich variieren und von Nanometern bis zu Mikrometern reichen. Der Prozess umfasst mehrere Schlüsselkomponenten, darunter Gaszufuhrsysteme, Reaktionskammern und Energiequellen, die zusammenarbeiten, um eine präzise Steuerung des Abscheidungsprozesses zu gewährleisten. CVD-Beschichtungen werden häufig verwendet, um die elektrischen, mechanischen, optischen, thermischen und Korrosionsbeständigkeitseigenschaften von Substraten zu verbessern, was sie in Branchen wie Halbleitern, Optik und Schutzbeschichtungen unverzichtbar macht.
Wichtige Punkte erklärt:
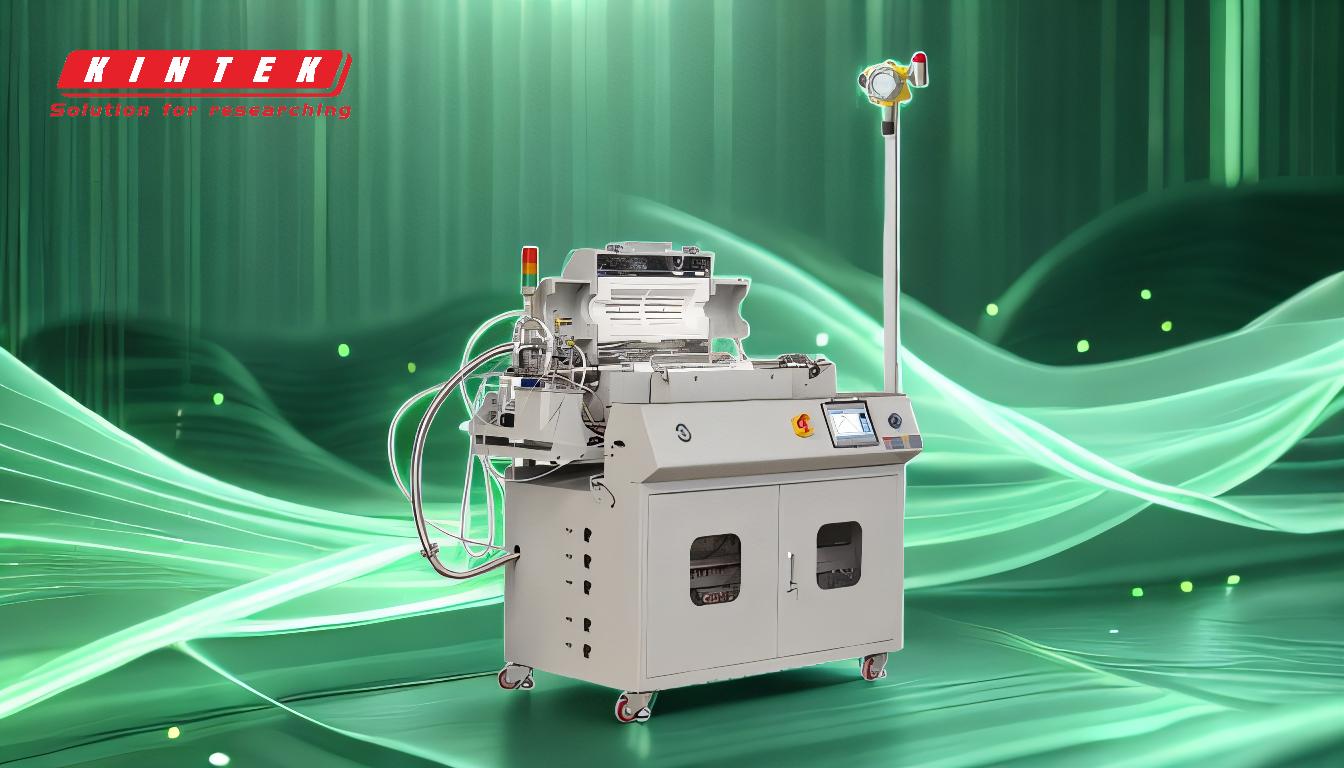
-
Definition und Zweck von CVD:
- Chemische Gasphasenabscheidung (CVD) ist ein Prozess, bei dem feste Materialien durch die Reaktion gasförmiger Vorläufer auf einem Substrat abgeschieden werden. Mit dieser Methode werden dünne Filme mit spezifischen Eigenschaften hergestellt, beispielsweise einer verbesserten elektrischen Leitfähigkeit, mechanischen Festigkeit oder Korrosionsbeständigkeit. Die Dicke dieser Filme kann je nach Anwendung zwischen wenigen Nanometern und mehreren Mikrometern liegen.
-
Faktoren, die die CVD-Dicke beeinflussen:
- Vorläufergase: Die Art und Konzentration der im CVD-Prozess verwendeten Vorläufergase können die Dicke des abgeschiedenen Films erheblich beeinflussen. Verschiedene Gase reagieren unterschiedlich schnell, was zu unterschiedlichen Abscheidungsraten führt.
- Temperatur und Druck: Die Temperatur und der Druck innerhalb der Reaktionskammer spielen eine entscheidende Rolle bei der Bestimmung der Dicke der CVD-Beschichtung. Höhere Temperaturen und Drücke erhöhen im Allgemeinen die Abscheidungsrate, was zu dickeren Filmen führt.
- Reaktionszeit: Die Dauer des CVD-Prozesses hat direkten Einfluss auf die Dicke der Beschichtung. Durch längere Reaktionszeiten kann mehr Material abgeschieden werden, wodurch sich die Gesamtdicke erhöht.
-
Anwendungen und Dickenanforderungen:
- Halbleiter: In der Halbleiterindustrie wird CVD verwendet, um dünne Schichten aus Materialien wie Siliziumdioxid und Siliziumnitrid abzuscheiden, deren Dicke typischerweise zwischen einigen Nanometern und einigen Mikrometern liegt. Diese Filme sind für Isolierschichten, Gate-Dielektrika und Passivierungsschichten von entscheidender Bedeutung.
- Optische Beschichtungen: CVD wird auch zur Herstellung optischer Beschichtungen eingesetzt, beispielsweise zur Antireflexbeschichtung von Linsen. Um die gewünschten optischen Eigenschaften zu erzielen, sind diese Beschichtungen in der Regel sehr dünn, oft im Bereich von mehreren zehn bis hundert Nanometern.
- Schutzbeschichtungen: Bei Schutzbeschichtungen, wie sie beispielsweise zur Erhöhung der Korrosionsbeständigkeit eingesetzt werden, kann die Dicke stärker variieren. Abhängig vom Substrat und der Umgebung, der es ausgesetzt ist, können die Beschichtungen zwischen einigen Mikrometern und mehreren zehn Mikrometern liegen.
-
Geräte- und Prozesskontrolle:
- Gasversorgungssystem: Das Gaszufuhrsystem sorgt dafür, dass die Vorläufergase kontrolliert in die Reaktionskammer eingeleitet werden. Dieses System ist entscheidend für die Aufrechterhaltung konstanter Abscheidungsraten und damit einer gleichmäßigen Filmdicke.
- Reaktionskammer: In der Reaktionskammer bzw. dem Reaktor findet die eigentliche Abscheidung statt. Das Design der Kammer, einschließlich ihrer Größe und Form, kann die Gleichmäßigkeit und Dicke des abgeschiedenen Films beeinflussen.
- Energiequelle: Die Energiequelle, oft in Form von Wärme oder Plasma, liefert die Energie, die für die Durchführung der chemischen Reaktionen erforderlich ist. Die Intensität und Verteilung dieser Energie kann die Abscheidungsrate und die Filmdicke beeinflussen.
- Vakuumsystem: Ein Vakuumsystem wird verwendet, um den Druck in der Reaktionskammer zu kontrollieren. Niedrigere Drücke können zu dünneren, gleichmäßigeren Filmen führen, während höhere Drücke zu dickeren, weniger gleichmäßigen Beschichtungen führen können.
- Automatisches Prozesskontrollsystem: Dieses System überwacht und steuert verschiedene Parameter wie Temperatur, Druck und Gasdurchflussraten, um eine gleichmäßige Abscheidung und die gewünschte Filmdicke sicherzustellen.
- Abgasbehandlungssystem: Nach dem Abscheidungsprozess werden die Abgase behandelt, um schädliche Nebenprodukte zu entfernen und so sicherzustellen, dass der Prozess umweltfreundlich ist.
-
Herausforderungen und Überlegungen:
- Gleichmäßigkeit: Das Erreichen einer gleichmäßigen Dicke über das gesamte Substrat kann eine Herausforderung sein, insbesondere bei großen oder komplexen Formen. Schwankungen des Gasflusses, der Temperatur und des Drucks können zu einer ungleichmäßigen Abscheidung führen.
- Haftung: Die Haftung des abgeschiedenen Films auf dem Untergrund ist entscheidend für die Leistung der Beschichtung. Eine schlechte Haftung kann zur Delaminierung und zum Versagen der Beschichtung führen.
- Mängel: Defekte wie Nadellöcher, Risse oder Verunreinigungen können die Qualität und Dicke der CVD-Beschichtung beeinträchtigen. Um diese Mängel zu minimieren, ist eine sorgfältige Kontrolle der Prozessparameter erforderlich.
Zusammenfassend lässt sich sagen, dass die Dicke von Beschichtungen durch chemische Gasphasenabscheidung je nach Anwendung stark variieren kann, wobei typische Dicken zwischen Nanometern und Mikrometern liegen. Der Prozess erfordert die präzise Steuerung verschiedener Parameter, einschließlich Vorläufergasen, Temperatur, Druck und Reaktionszeit, um die gewünschten Filmeigenschaften zu erreichen. CVD ist eine entscheidende Technologie in Branchen wie Halbleiter, Optik und Schutzbeschichtungen, wo sie zur Verbesserung der Leistung von Materialien durch die Abscheidung dünner Filme eingesetzt wird.
Übersichtstabelle:
Aspekt | Einzelheiten |
---|---|
Typische Dicke | Nanometer bis Mikrometer, je nach Anwendung. |
Wichtige Einflussfaktoren | Vorläufergase, Temperatur, Druck und Reaktionszeit. |
Anwendungen | Halbleiter, optische Beschichtungen und Schutzbeschichtungen. |
Ausrüstung | Gaszufuhrsystem, Reaktionskammer, Energiequelle und Vakuumsystem. |
Herausforderungen | Gleichmäßigkeit, Haftung und Fehlerkontrolle. |
Entdecken Sie, wie CVD-Beschichtungen Ihre Materialien verbessern können – Kontaktieren Sie noch heute unsere Experten für maßgeschneiderte Lösungen!