Glühen ist ein Wärmebehandlungsprozess, bei dem Metalle auf eine bestimmte Temperatur erhitzt, auf dieser Temperatur gehalten und dann langsam abgekühlt werden. Dieses Verfahren bietet mehrere Vorteile, wie z. B. eine Verbesserung der Duktilität, eine Verringerung der Härte, eine Entlastung innerer Spannungen sowie eine Verbesserung der Bearbeitbarkeit und der elektrischen Eigenschaften. Es hat jedoch auch Nachteile, darunter geringe Produktivität, lange Abkühlzeiten, ungleichmäßige Erwärmung und Empfindlichkeit gegenüber Temperaturschwankungen, die sich auf die Materialqualität und die Geräteleistung auswirken können. Der Prozess erfordert einen sorgfältigen Umgang mit der Nachbehandlung, da die Materialien sehr empfindlich gegenüber Stößen und Belastungen sind.
Wichtige Punkte erklärt:
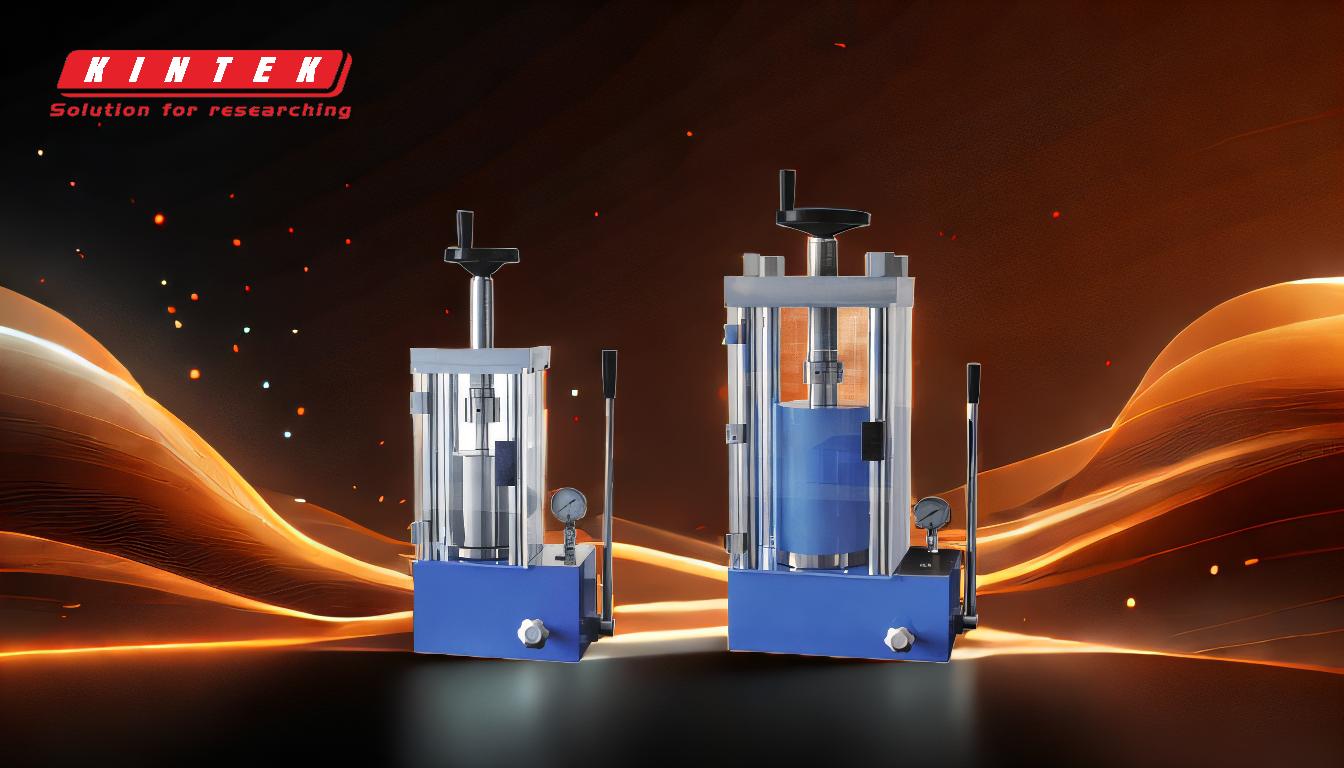
-
Vorteile des Glühens:
- Verbesserte Duktilität und Verarbeitbarkeit: Durch das Glühen werden Metalle duktiler, sodass sie ohne Rissbildung geformt werden können. Dies ist besonders nützlich bei Herstellungsprozessen, bei denen Metalle gebogen, gedehnt oder in komplexe Formen gebracht werden müssen.
- Reduzierung der Härte: Durch die Verringerung der Härte lassen sich Metalle durch das Glühen leichter bearbeiten, schneiden oder bohren, was in Branchen, in denen eine präzise Metallbearbeitung erforderlich ist, von Vorteil ist.
- Stressabbau: Beim Glühen werden innere Spannungen abgebaut, die durch vorherige Herstellungsprozesse wie Schweißen oder Kaltumformung verursacht wurden. Dies verhindert Materialverformungen oder -ausfälle während des Gebrauchs.
- Verbesserte elektrische Eigenschaften: Durch das Glühen wird die Kristallstruktur von Metallen verfeinert und ihre elektrische Leitfähigkeit verbessert. Dies ist von entscheidender Bedeutung für Materialien, die in elektrischen Anwendungen wie Kabeln oder Transformatoren verwendet werden.
- Verbesserte mechanische Eigenschaften: Der Prozess verbessert mechanische Eigenschaften wie Zähigkeit und Festigkeit und macht Materialien haltbarer und verschleißfester.
-
Nachteile des Glühens:
- Geringe Produktivität: Herkömmliche Glühmethoden wie das Vakuumglühen weisen aufgrund langer Aufheiz- und Abkühlzyklen häufig eine geringe Produktivität auf.
- Ungleichmäßige Erwärmung: Bei Materialien, insbesondere bei großen oder komplexen Formen, kann es zu einer ungleichmäßigen Erwärmung kommen, was zu inkonsistenten Materialeigenschaften und Qualitätsproblemen führt.
- Temperaturempfindlichkeit: Temperaturschwankungen während des Glühprozesses (zwischen 5 und 25 °C) können die Stabilität und Konsistenz des Endprodukts beeinträchtigen.
- Geräteverschlechterung: Häufiges Wechseln zwischen Vakuum- und Normaldruckumgebungen kann zu Verschleiß an der Ausrüstung führen und deren Lebensdauer verkürzen.
- Empfindlichkeit nach der Behandlung: Geglühte Materialien reagieren sehr empfindlich auf Stöße, Vibrationen und Spannungen und erfordern eine sorgfältige Handhabung, um Schäden zu vermeiden.
-
Anwendungen und Überlegungen:
- Materialspezifische Effekte: Beispielsweise erhöht das Glühen bei 200 °C für 12 Stunden bei X80-Pipelinestahl die Streckgrenze um 10 %, verringert jedoch die Dehnung um 20 %. Dies ist auf die Bildung einer Cottrell-Atmosphäre zurückzuführen, die Versetzungen festhält und die Dichte beweglicher Versetzungen verringert.
- Verwendung inerter Atmosphären: Beim Glühen werden häufig Stickstoffgasmischungen verwendet, um Oxidation und unerwünschte chemische Reaktionen zu verhindern und sicherzustellen, dass das Material seine gewünschten Eigenschaften behält.
- Kühlprozess: Langsames Abkühlen ist wichtig, um die gewünschte Kristallstruktur zu erreichen und die Wiedereinführung von Spannungen oder Defekten zu vermeiden.
-
Herausforderungen bei der industriellen Umsetzung:
- Inkonsistente Qualität: Herkömmliche Methoden können zu einer schlechten inhärenten Qualitätskonsistenz führen, was die Herstellung einheitlicher Materialchargen erschwert.
- Probleme mit thermischer Belastung und Schichten: Insbesondere bei Materialien wie Aluminiumfolienrollen können Probleme wie thermischer Stress, Schichtkanalisierung und lose Schichten auftreten, die deren Verwendbarkeit und Leistung beeinträchtigen.
Zusammenfassend lässt sich sagen, dass das Glühen ein wertvoller Prozess zur Verbesserung der Materialeigenschaften ist, der jedoch mit Herausforderungen verbunden ist, die ein sorgfältiges Management von Temperatur, Ausrüstung und Nachbehandlungshandhabung erfordern, um konsistente und qualitativ hochwertige Ergebnisse zu erzielen.
Übersichtstabelle:
Aspekt | Vorteile | Nachteile |
---|---|---|
Duktilität | Verbessert die Duktilität und erleichtert die Formgebung von Metallen ohne Rissbildung. | N / A |
Härte | Reduziert die Härte und verbessert die Bearbeitbarkeit und Schnittpräzision. | N / A |
Stressabbau | Entlastet innere Spannungen und beugt Verformungen oder Ausfällen vor. | N / A |
Elektrische Eigenschaften | Verbessert die elektrische Leitfähigkeit, ideal für Kabel und Transformatoren. | N / A |
Mechanische Eigenschaften | Verbessert Zähigkeit, Festigkeit und Verschleißfestigkeit. | N / A |
Produktivität | N / A | Geringe Produktivität aufgrund langer Heiz- und Kühlzyklen. |
Gleichmäßige Erwärmung | N / A | Eine ungleichmäßige Erwärmung kann zu inkonsistenten Materialeigenschaften führen. |
Temperaturempfindlichkeit | N / A | Empfindlich gegenüber Temperaturschwankungen (5–25 °C), was die Stabilität beeinträchtigt. |
Lebensdauer der Ausrüstung | N / A | Häufiges Radfahren führt zu Verschleiß und verringert die Lebensdauer der Ausrüstung. |
Handhabung nach der Behandlung | N / A | Materialien reagieren sehr empfindlich auf Stöße und Belastungen und erfordern eine sorgfältige Handhabung. |
Benötigen Sie kompetente Beratung zu Glühprozessen? Kontaktieren Sie uns noch heute zur Optimierung Ihrer Metallwärmebehandlung!