Das Sintern in der Pulvermetallurgie ist ein äußerst vorteilhaftes Herstellungsverfahren, das zahlreiche Vorteile bietet, darunter die Fähigkeit, komplexe Formen mit hoher Präzision, verbesserten Materialeigenschaften, Kosteneffizienz und Umweltverträglichkeit herzustellen.Bei diesem Verfahren werden Metallpulver in die gewünschte Form gepresst und anschließend unter ihren Schmelzpunkt erhitzt, um die Partikel miteinander zu verbinden.Das Ergebnis ist ein starkes, haltbares und präzises Bauteil, das auf spezifische Anwendungen zugeschnitten werden kann.Zu den wichtigsten Vorteilen gehören die Möglichkeit, mit hochschmelzenden Metallen zu arbeiten, die Porosität zu verringern, die mechanischen und thermischen Eigenschaften zu verbessern und eine hohe Wiederholgenauigkeit bei der Herstellung zu erreichen.
Die wichtigsten Punkte werden erklärt:
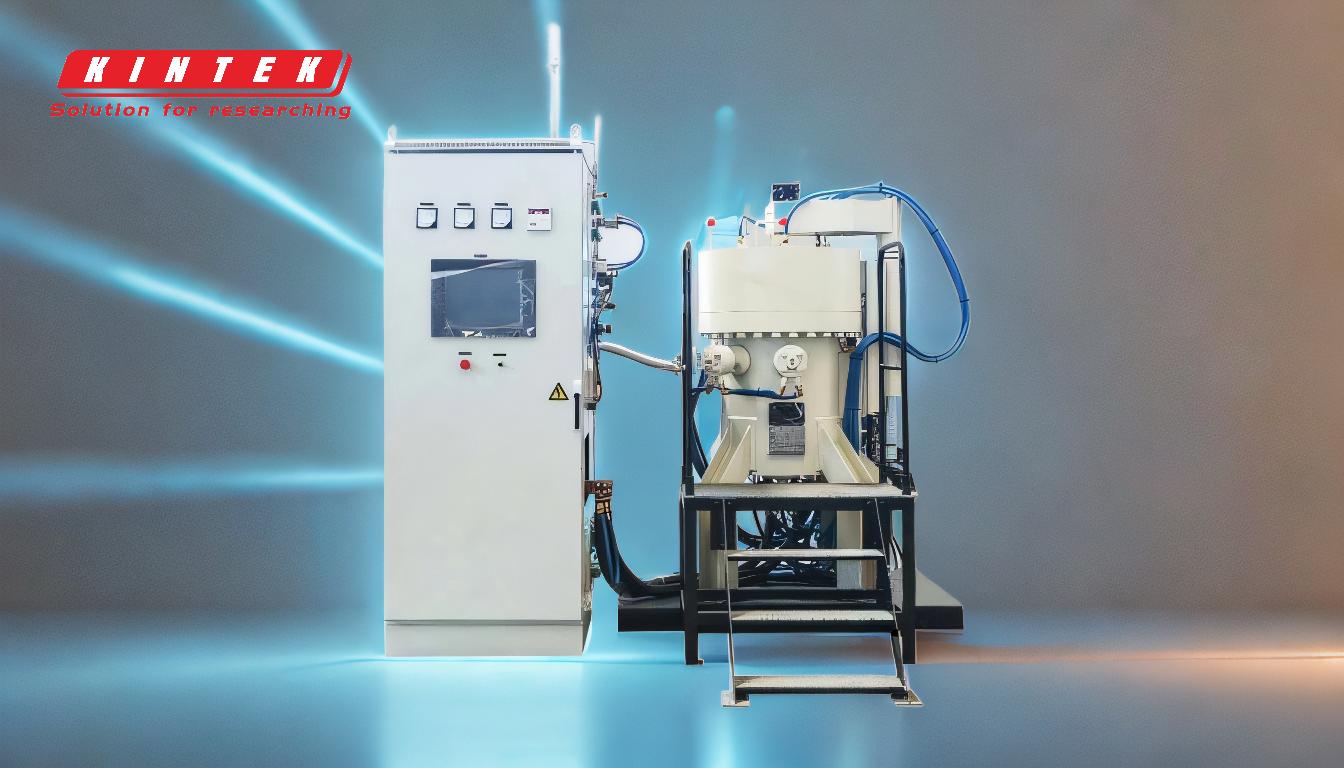
-
Herstellung komplexer Formen mit hoher Präzision
- Das Sintern ermöglicht die Herstellung komplizierter Außen- und Innengeometrien, die mit herkömmlichen Fertigungsmethoden nur schwer oder gar nicht zu erreichen wären.
- Erleichtert wird dies durch den Einsatz von Formen und Gesenken, die mit dem Drahterodierverfahren (Electrical Discharge Machining) hergestellt werden, das Toleranzen im Zentimeterbereich (0,01 mm) erreichen kann.
- Beispiele hierfür sind Bauteile mit inneren Kanälen, Hinterschneidungen oder komplexen Oberflächenstrukturen, die in Branchen wie der Automobilindustrie, der Luft- und Raumfahrt und der Medizintechnik von entscheidender Bedeutung sind.
-
Verbesserte Materialeigenschaften
- Durch das Sintern wird die Porosität des Endprodukts verringert, wodurch Eigenschaften wie Festigkeit, Haltbarkeit, elektrische Leitfähigkeit und Wärmeleitfähigkeit verbessert werden.
- Bei dem Verfahren entstehen Sinterhälse zwischen den Partikeln, die sich zu einer festen Struktur mit minimalen Hohlräumen verbinden.
- Dies ist besonders nützlich für Anwendungen, die eine hohe mechanische Leistung erfordern, wie z. B. Lager, Zahnräder und Strukturkomponenten.
-
Maßgeschneiderte Materialzusammensetzungen
- Das Sintern ermöglicht die Beimischung von Legierungselementen wie Nickel, Kupfer und Graphit in die Metallpulvermischung, wodurch maßgeschneiderte Materialeigenschaften erzielt werden können.
- Diese Flexibilität ist wertvoll, wenn es darum geht, spezifische Kundenanforderungen zu erfüllen, z. B. erhöhte Verschleißfestigkeit, verbesserte Wärmeleitfähigkeit oder kontrollierte Porosität für Filter und Katalysatoren.
-
Kosteneffizienz
- Sintern ist ein endkonturnahes Herstellungsverfahren, d. h. das Endprodukt muss nur minimal bearbeitet oder nachbearbeitet werden, was den Materialabfall und die Produktionskosten reduziert.
- Außerdem wird im Vergleich zum Schmelzen von Metallen weniger Energie verbraucht, was es zu einer umweltfreundlichen und wirtschaftlichen Option macht.
-
Vielseitigkeit bei der Materialauswahl
- Das Sintern ist besonders vorteilhaft für Werkstoffe mit hohen Schmelzpunkten, großen Unterschieden zwischen den Schmelzpunkten der einzelnen Bestandteile und schlechter Gießbarkeit.
- Beispiele hierfür sind Wolfram, Molybdän und Keramik, die mit herkömmlichen Methoden nur schwer zu verarbeiten sind.
-
Hohe Reproduzierbarkeit und Konsistenz
- Der Sinterprozess ist in hohem Maße wiederholbar und gewährleistet eine gleichbleibende Qualität bei großen Produktionsläufen.
- Diese Zuverlässigkeit ist entscheidend für Branchen, in denen Präzision und Gleichmäßigkeit von größter Bedeutung sind, wie z. B. in der Elektronik- und Medizintechnik.
-
Umweltfreundlichkeit und Energieeffizienz
- Das Sintern erfolgt bei niedrigeren Temperaturen als das Schmelzen, was den Energieverbrauch und die Treibhausgasemissionen reduziert.
- Der Wegfall von Schmiermitteln im verdichteten Pulver und die Verringerung des Oberflächensauerstoffs tragen ebenfalls zu seiner Umweltfreundlichkeit bei.
-
Branchenübergreifende Anwendungen
- Das Sintern wird zur Herstellung einer breiten Palette von Produkten verwendet, darunter Lager, Schmuck, Wärmerohre, Flintenschalen und Filter.
- Die Fähigkeit, Komponenten mit spezifischen Porositätsgraden herzustellen, macht es ideal für Anwendungen wie Katalysatoren und Filtersysteme.
Durch die Nutzung dieser Vorteile bietet das Sintern in der Pulvermetallurgie eine vielseitige, effiziente und nachhaltige Fertigungslösung für eine breite Palette von Branchen und Anwendungen.
Zusammenfassende Tabelle:
Vorteil | Beschreibung |
---|---|
Komplexe Formen mit hoher Präzision | Erzielen Sie komplizierte Geometrien mit Toleranzen im Zentimeterbereich (0,01 mm). |
Verbesserte Materialeigenschaften | Geringere Porosität erhöht die Festigkeit, Haltbarkeit und Leitfähigkeit. |
Maßgeschneiderte Materialzusammensetzungen | Anpassung der Eigenschaften durch Legierungselemente wie Nickel, Kupfer und Graphit. |
Kosteneffizienz | Das Near-Net-Shape-Verfahren reduziert den Materialabfall und den Energieverbrauch. |
Vielseitigkeit bei der Materialauswahl | Ideal für Metalle mit hohem Schmelzpunkt und anspruchsvolle Materialien wie Keramik. |
Hohe Reproduzierbarkeit und Konsistenz | Gewährleistet einheitliche Qualität bei großen Produktionsläufen. |
Umweltfreundlich und energieeffizient | Niedrigere Temperaturen und geringere Emissionen machen sie umweltfreundlich. |
Branchenübergreifende Anwendungen | Anwendungen in der Automobilindustrie, Luft- und Raumfahrt, Medizintechnik und mehr. |
Möchten Sie erfahren, wie das Sintern Ihren Fertigungsprozess verändern kann? Kontaktieren Sie uns noch heute um mehr zu erfahren!