Spark Plasma Sintering (SPS) ist eine fortschrittliche Sintertechnologie, die zahlreiche Vorteile gegenüber herkömmlichen Sinterverfahren bietet.Es ist besonders effektiv bei der Herstellung von keramischen, metallischen und Verbundwerkstoffen mit hoher Dichte, feiner Korngröße und verbesserten mechanischen, elektrischen und thermischen Eigenschaften.Zu den wichtigsten Vorteilen von SPS gehören kürzere Verarbeitungszeiten, niedrigere Sintertemperaturen und eine präzise Steuerung der Sinterparameter.Darüber hinaus ermöglicht SPS eine Mehrfeldkopplung (elektrisch-mechanisch-thermisch), die die Verdichtung einer breiten Palette von Werkstoffen ermöglicht, von Metallen mit niedrigem Schmelzpunkt bis hin zu Ultrahochtemperaturkeramiken.Diese Vorteile machen SPS zu einer vielseitigen und effizienten Methode für die Materialherstellung.
Die wichtigsten Punkte erklärt:
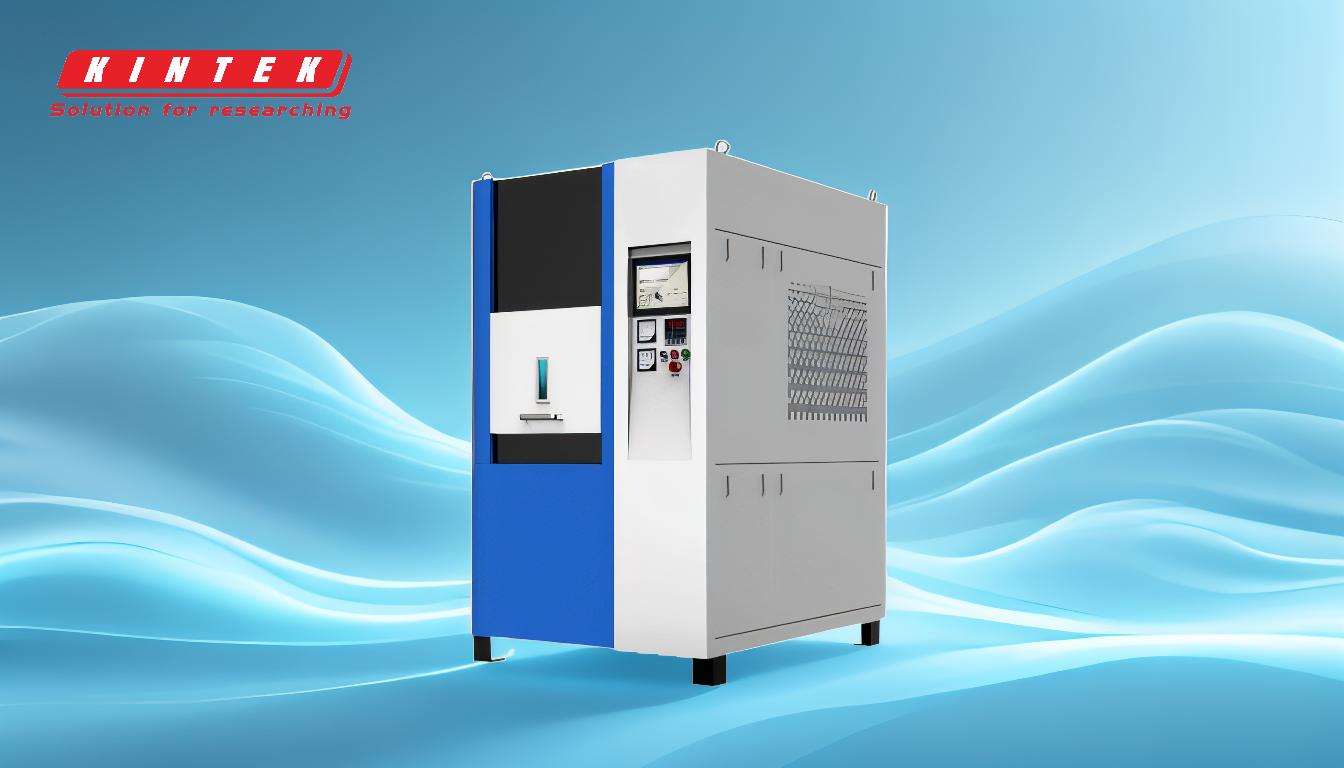
-
Hohe Heiz- und Kühlraten:
- SPS erreicht im Vergleich zu herkömmlichen Sinterverfahren deutlich höhere Heiz- und Kühlraten.Dies führt zu kürzeren Verarbeitungszeiten, wodurch die Zykluszeiten oft von Stunden oder Tagen auf nur Minuten reduziert werden.
- Die schnelle Erwärmung und Abkühlung trägt dazu bei, die feine Korngröße der Werkstoffe beizubehalten, was für die Verbesserung der mechanischen Eigenschaften wie Festigkeit und Zähigkeit entscheidend ist.
-
Niedrige Sintertemperaturen:
- SPS arbeitet mit niedrigeren Sintertemperaturen als herkömmliche Verfahren.Dies ist vorteilhaft für Materialien, die empfindlich auf hohe Temperaturen reagieren, da das Risiko einer thermischen Schädigung oder unerwünschter Phasenumwandlungen minimiert wird.
- Niedrigere Temperaturen verringern auch den Energieverbrauch und machen das Verfahren kostengünstiger und umweltfreundlicher.
-
Kurze Haltezeit:
- Die Haltezeit während des Sinterns wird bei SPS erheblich verkürzt.Dies beschleunigt nicht nur den Gesamtprozess, sondern trägt auch dazu bei, die Mikrostruktur des Werkstoffs zu erhalten, was zu besseren Endeigenschaften führt.
- Kurze Haltezeiten sind besonders vorteilhaft für Materialien, die bei längerer Einwirkung hoher Temperaturen zu Kornwachstum oder anderen Gefügeveränderungen neigen.
-
Einstellbarer Sinterdruck:
- SPS ermöglicht eine präzise Steuerung des Sinterdrucks, der je nach den spezifischen Anforderungen des zu verarbeitenden Materials eingestellt werden kann.
- Diese Flexibilität ermöglicht die Verdichtung eines breiten Spektrums von Materialien, einschließlich solcher, die mit herkömmlichen Methoden nur schwer zu sintern sind.
-
Mehrfeldkopplung (Elektrizität-Mechanik-Thermik):
- SPS nutzt eine Kombination aus elektrischen Feldern, mechanischem Druck und thermischer Energie, um eine Verdichtung zu erreichen.Diese Kopplung mehrerer Felder verbessert den Sinterprozess und führt zu verbesserten Materialeigenschaften.
- Die gleichzeitige Anwendung dieser Felder ermöglicht eine bessere Kontrolle des Sinterprozesses, was zu Materialien mit hervorragenden mechanischen, elektrischen und thermischen Eigenschaften führt.
-
Verbesserte Verdichtung in elektrisch leitfähigen Materialien:
- Der hohe gepulste Strom, der bei der SPS verwendet wird, ist besonders wirksam bei der Verdichtung von elektrisch leitfähigen Materialien.Dies führt zu Materialien mit höherer Dichte und besseren Gesamteigenschaften.
- Der gepulste Strom trägt auch zu einer gleichmäßigen Erwärmung bei, was für gleichbleibende Materialeigenschaften des gesamten Sinterprodukts entscheidend ist.
-
Vielseitigkeit in der Materialverarbeitung:
- SPS ist in der Lage, eine breite Palette von Materialien zu verarbeiten, von Metallen mit niedrigem Schmelzpunkt bis hin zu Ultrahochtemperaturkeramiken.Diese Vielseitigkeit macht sie zu einem wertvollen Werkzeug in verschiedenen Branchen, darunter Luft- und Raumfahrt, Automobilbau und Elektronik.
- Die Fähigkeit, eine so große Bandbreite an Materialien zu sintern, eröffnet neue Möglichkeiten für Materialdesign und -anwendung.
-
Hochpräzise Prozesskontrolle:
- SPS bietet eine hochpräzise Kontrolle über die Sinterparameter und ermöglicht fein abgestimmte Prozesse, die für bestimmte Materialien und gewünschte Ergebnisse optimiert werden können.
- Dieses Maß an Kontrolle stellt sicher, dass das Endprodukt die geforderten Spezifikationen erfüllt, was SPS zu einer zuverlässigen Methode für die Herstellung hochwertiger Materialien macht.
Zusammenfassend lässt sich sagen, dass das Spark-Plasma-Sintern (SPS) eine Reihe von Vorteilen bietet, die es zu einer hervorragenden Wahl für die Materialherstellung machen.Seine Fähigkeit, hohe Heiz- und Kühlraten zu erzielen, bei niedrigeren Temperaturen zu arbeiten und eine präzise Steuerung der Sinterparameter zu bieten, führt zu Materialien mit verbesserten Eigenschaften.Die Vielseitigkeit und Effizienz der SPS machen sie zu einer unschätzbaren Technologie auf dem Gebiet der Materialwissenschaft und -technik.
Zusammenfassende Tabelle:
Hauptvorteil | Beschreibung |
---|---|
Hohe Aufheiz- und Abkühlraten | Reduziert die Zykluszeiten auf Minuten, wobei die feine Korngröße für eine bessere Festigkeit erhalten bleibt. |
Niedrige Sintertemperaturen | Minimiert die thermische Schädigung und den Energieverbrauch, ideal für empfindliche Materialien. |
Kurze Haltezeit | Bewahrt das Mikrogefüge, verhindert Kornwachstum und verbessert die Endeigenschaften. |
Einstellbarer Sinterdruck | Ermöglicht die Verdichtung von anspruchsvollen Materialien mit präziser Druckregelung. |
Multi-Feld-Kopplung | Kombiniert Elektrizität, mechanischen Druck und thermische Energie für hervorragende Ergebnisse. |
Verbesserte Verdichtung in leitfähigen Materialien | Erzielt höhere Dichte und gleichmäßige Erwärmung für gleichbleibende Eigenschaften. |
Vielseitigkeit bei der Materialverarbeitung | Verarbeitet Metalle, Keramiken und Verbundwerkstoffe für verschiedene industrielle Anwendungen. |
Hochpräzise Prozesssteuerung | Sorgt für optimierte Sinterparameter für hochwertige, maßgeschneiderte Werkstoffe. |
Erschließen Sie das Potenzial des Spark Plasma Sintering für Ihre Werkstoffe. Kontaktieren Sie unsere Experten noch heute !