Kaltisostatisches Pressen (CIP) ist ein vielseitiges Herstellungsverfahren, mit dem eine breite Palette von Materialien und Komponenten mit gleichmäßiger Dichte und struktureller Integrität hergestellt werden. Dabei wird ein gleichmäßiger Druck auf Pulver oder Vorformen mithilfe eines flüssigen Mediums ausgeübt, typischerweise bei Raumtemperatur oder leicht erhöhten Temperaturen. Diese Methode ist besonders nützlich für Materialien, die mit herkömmlichen Techniken schwer zu pressen sind, wie z. B. Hartmetalle, Keramik und feuerfeste Materialien. CIP wird in Branchen wie der Luft- und Raumfahrt, der Automobilindustrie, der Elektronik und der chemischen Verarbeitung häufig eingesetzt und ermöglicht die Herstellung komplexer Formen, hochdichter Komponenten und fortschrittlicher Materialien wie Festkörperbatterien. Seine Fähigkeit, mechanische Eigenschaften wie Härte und Verschleißfestigkeit zu verbessern, macht es zu einer bevorzugten Wahl für die Herstellung von Hochleistungsmaterialien.
Wichtige Punkte erklärt:
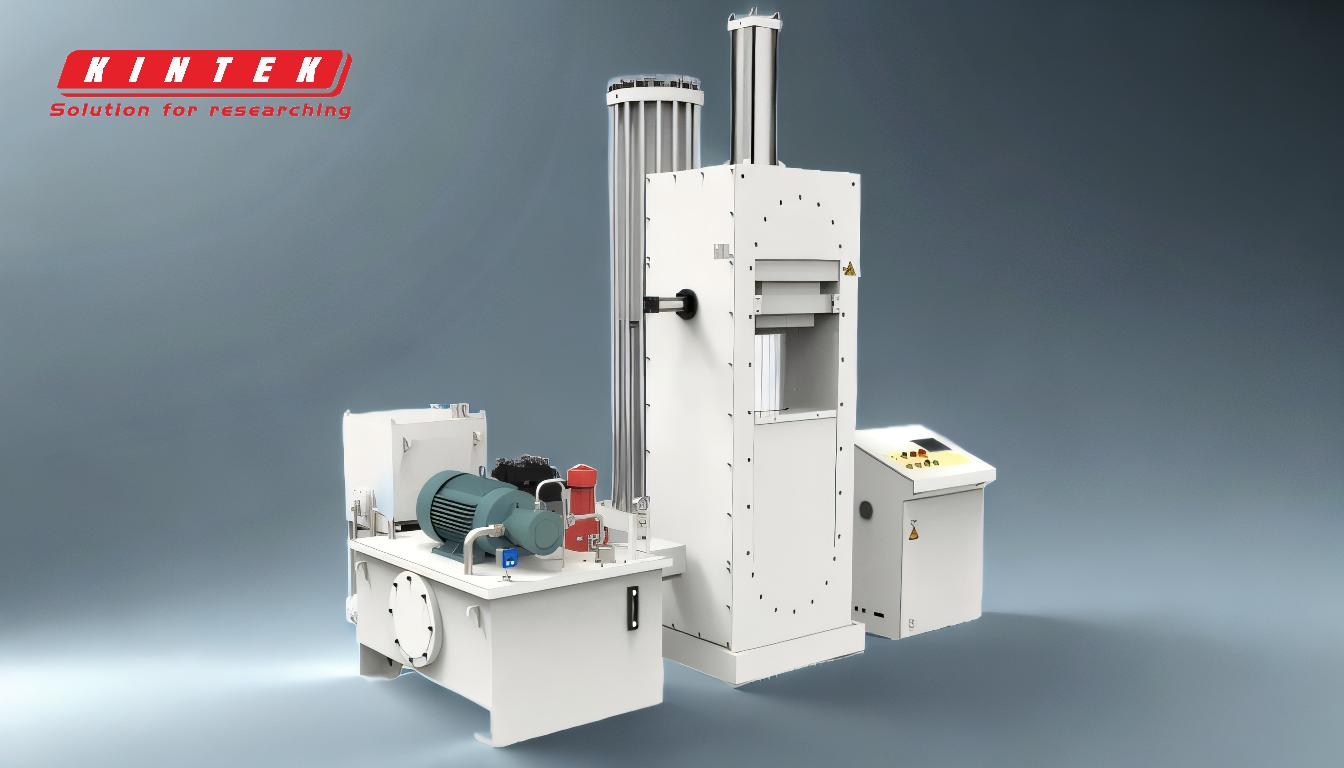
-
Gleichmäßige Dichte und strukturelle Integrität:
- Kaltisostatisches Pressen übt einen gleichmäßigen Druck in alle Richtungen aus und sorgt so für eine gleichmäßige Dichte im gesamten Material. Dies ist besonders vorteilhaft für Materialien wie isotroper Graphit und Keramik, wo Gleichmäßigkeit für die Leistung entscheidend ist.
- Der Prozess minimiert Defekte wie Hohlräume oder Risse, die bei herkömmlichen Pressverfahren häufig auftreten, was zu einer überlegenen strukturellen Integrität führt.
-
Vielseitigkeit in der Materialbearbeitung:
- CIP eignet sich für eine Vielzahl von Materialien, darunter Hartmetalle, Keramik, feuerfeste Materialien und Hartmetalle. Dies macht es ideal für die Herstellung von Bauteilen wie feuerfeste Düsen , Tiegel und Keramikisolatoren.
- Es wird auch zur Herstellung von Metallfiltern, Vorformlingen und Kunststoffrohren verwendet und zeigt damit seine branchenübergreifende Anpassungsfähigkeit.
-
Komplexe und komplizierte Formen:
- Im Gegensatz zu herkömmlichen Pressverfahren können mit CIP komplexe und komplizierte Formen mit hoher Präzision hergestellt werden. Dies ist besonders nützlich für die Herstellung von Komponenten wie Rohren für chemische Anwendungen oder Ferriten für die Elektronik.
- Das Verfahren ermöglicht die Erzeugung dünner, dichter Schichten, beispielsweise Festelektrolytschichten in Festkörperbatterien, die mit anderen Techniken nur schwer zu erreichen sind.
-
Verbesserte mechanische Eigenschaften:
- Durch CIP hergestellte Komponenten weisen verbesserte mechanische Eigenschaften auf, einschließlich Härte, Verschleißfestigkeit und thermische Stabilität. Dies ist für Anwendungen in Umgebungen mit hoher Belastung, beispielsweise in der Luft- und Raumfahrt- und Automobilindustrie, von entscheidender Bedeutung.
- Der Prozess ermöglicht auch die Integration mehrerer Schichten, wie Kathoden-, Festelektrolyt- und Anodenschichten, in dichte Dreischichtsysteme für fortgeschrittene Anwendungen.
-
Verarbeitung bei Raumtemperatur:
- CIP arbeitet bei Raumtemperatur oder leicht erhöhten Temperaturen (<93 °C) und ist daher im Vergleich zum heißisostatischen Pressen (HIP) energieeffizienter. Dies ist bei hochtemperaturempfindlichen Materialien von Vorteil.
- Die Verwendung eines flüssigen Mediums, beispielsweise Wasser mit Korrosionsinhibitor, sorgt für eine gleichmäßige Druckverteilung und minimiert die Kontamination.
-
Anwendungen in fortgeschrittenen Technologien:
- CIP spielt eine entscheidende Rolle bei der Entwicklung von Festkörperbatterien (SSBs), indem es die Herstellung dichter, dünner Elektrolytschichten und integrierter Mehrschichtsysteme ermöglicht.
- Es wird auch bei der Herstellung von isotropem Graphit verwendet, der für Anwendungen in Hochtemperaturumgebungen unerlässlich ist, z Muffelöfen .
-
Wirtschaftliche und ökologische Vorteile:
- Die Fähigkeit, Hochleistungsmaterialien mit hoher Dichte und minimalem Abfall herzustellen, macht CIP zu einem umweltfreundlichen Herstellungsverfahren.
- Seine Effizienz bei der Handhabung schwer zu pressender Pulver senkt die Materialkosten und verbessert die Produktionsausbeute, wodurch es sich für die Herstellung in großem Maßstab wirtschaftlich lohnt.
Zusammenfassend lässt sich sagen, dass kaltisostatisches Pressen ein äußerst effektives und vielseitiges Herstellungsverfahren ist, das zahlreiche Vorteile bietet, darunter eine gleichmäßige Dichte, verbesserte mechanische Eigenschaften und die Möglichkeit, komplexe Formen herzustellen. Seine Anwendungen erstrecken sich über verschiedene Branchen, von der Luft- und Raumfahrt über die Elektronik bis hin zur chemischen Verarbeitung und fortschrittlichen Energiespeicherung, was es zu einem unverzichtbaren Werkzeug in der modernen Fertigung macht.
Übersichtstabelle:
Hauptanwendungsbereiche | Vorteile |
---|---|
Luft- und Raumfahrt & Automobil | Verbesserte mechanische Eigenschaften, Komponenten mit hoher Dichte |
Elektronik | Produktion von Ferriten und Festkörperbatterien |
Chemische Verarbeitung | Komplexe Formen wie Rohre und Düsen |
Fortschrittliche Energiespeicherung | Dichte Elektrolytschichten für Festkörperbatterien |
Hochtemperaturumgebungen | Herstellung von isotropem Graphit |
Umwelt und Wirtschaft | Minimaler Abfall, kosteneffiziente Produktion |
Entdecken Sie, wie kaltisostatisches Pressen Ihren Herstellungsprozess verändern kann – Kontaktieren Sie uns noch heute für fachkundige Beratung!