Bei der PVD-Beschichtung (Physical Vapor Deposition) handelt es sich um ein hochentwickeltes Verfahren, mit dem dünne Materialschichten auf ein Substrat aufgebracht werden, um dessen Eigenschaften wie Verschleißfestigkeit, Härte und ästhetisches Aussehen zu verbessern.Bei diesem Verfahren wird ein Zielmaterial erhitzt, bis es verdampft, und dann wird der Dampf auf der Substratoberfläche abgeschieden.Zu den gängigen Materialien für PVD-Beschichtungen gehören Metalle wie Titan, Chrom, Wolfram und Aluminium, die oft mit reaktiven Gasen wie Stickstoff oder Kohlenwasserstoffen kombiniert werden, um Beschichtungen wie Nitride und Carbonitride zu bilden.Das PVD-Verfahren ist vielseitig und kann eine breite Palette anorganischer und einiger organischer Materialien einbeziehen, so dass es sich für verschiedene Anwendungen eignet, von dauerhaften dekorativen Beschichtungen bis hin zu Hochleistungskomponenten für die Luft- und Raumfahrt.
Die wichtigsten Punkte erklärt:
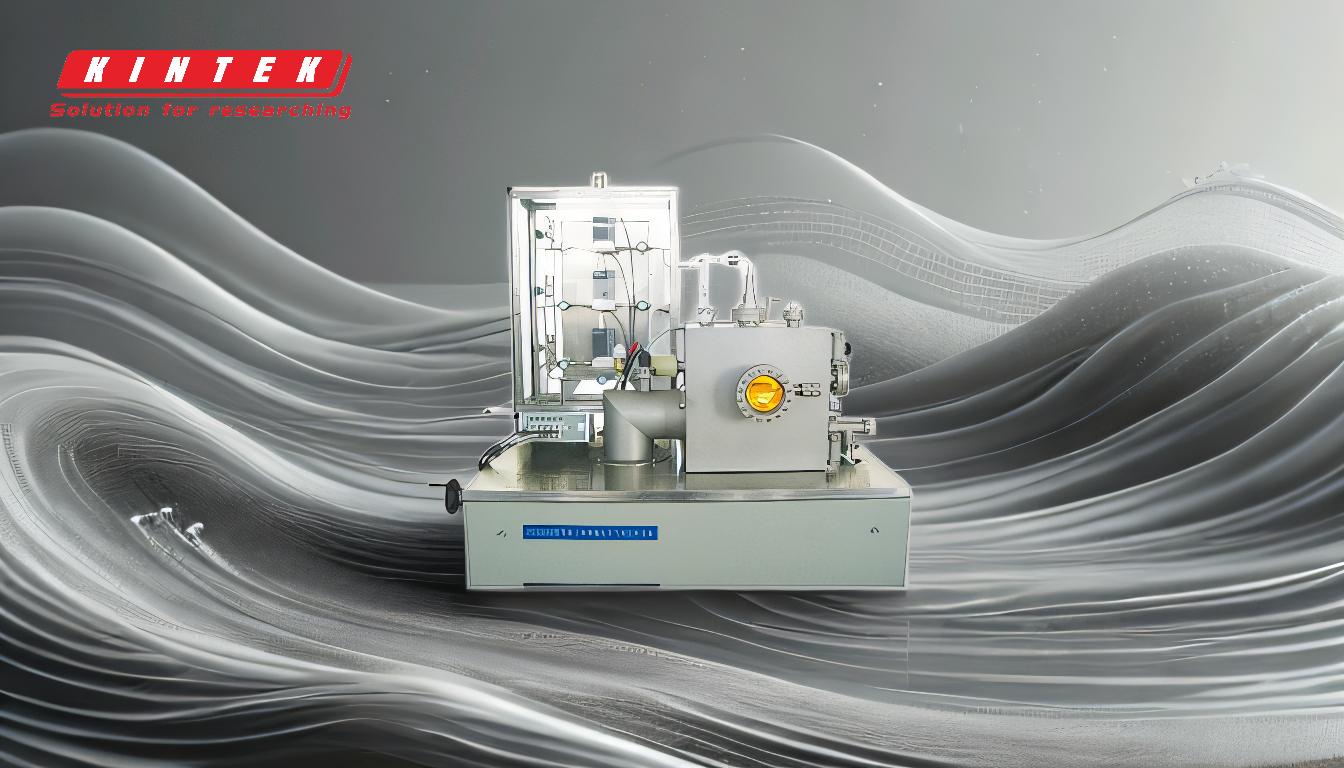
-
Zielmaterialien in der PVD-Beschichtung:
- Metalle und Legierungen:Zu den gängigen Metallen, die für PVD-Beschichtungen verwendet werden, gehören Titan, Chrom, Wolfram und Aluminium.Diese Metalle werden aufgrund ihrer spezifischen Eigenschaften ausgewählt, wie z. B. Härte, Verschleißfestigkeit und der Fähigkeit, starke Bindungen mit reaktiven Gasen einzugehen.
- Keramische Werkstoffe und Verbindungen:Mit PVD können auch Keramiken und Verbindungen wie Karbide, Nitride, Silizide und Boride abgeschieden werden.Diese Werkstoffe werden häufig für Spezialanwendungen verwendet, die eine hohe Leistung erfordern, z. B. in der Luft- und Raumfahrt und in der Automobilindustrie.
- Periodensystem der Elemente:Bei diesem Verfahren kann eine breite Palette von Elementen aus dem Periodensystem verwendet werden, was die Herstellung einzigartiger, auf spezifische Bedürfnisse zugeschnittener Beschichtungen ermöglicht.
-
Reaktive Gase:
- Stickstoff:Wird häufig zur Herstellung von Nitridschichten verwendet, die für ihre Härte und Verschleißfestigkeit bekannt sind.Titannitrid (TiN) ist zum Beispiel eine gängige PVD-Beschichtung für Schneidwerkzeuge.
- Gase auf Kohlenwasserstoffbasis:Diese Gase werden zur Herstellung von Karbonitridbeschichtungen verwendet, die die Eigenschaften von Karbiden und Nitriden kombinieren.Sie sind besonders nützlich für Anwendungen, die sowohl Härte als auch geringe Reibung erfordern.
-
Substrate Materialien:
- Grundstoffe:Das Substrat oder Basismaterial kann aus verschiedenen Materialien wie Metallen, Kunststoffen und Keramik bestehen.Die Wahl des Substrats hängt von der geplanten Anwendung und den gewünschten Eigenschaften des Endprodukts ab.
- Vorbereitung der Oberfläche:Vor dem PVD-Verfahren wird das Substrat häufig einer Oberflächenvorbereitung wie Reinigen und Polieren unterzogen, um eine gute Haftung der Beschichtung zu gewährleisten.
-
PVD-Beschichtungsprozess:
- Verdampfung:Das Zielmaterial wird erhitzt, bis es verdampft.Dies kann durch Methoden wie Sputtern oder Verdampfen erreicht werden.
- Abscheidung:Das verdampfte Material wird dann auf der Substratoberfläche abgeschieden und bildet einen dünnen Film.Die Dicke des Films kann von einigen Nanometern bis zu einigen Mikrometern reichen.
- Gleichmäßigkeit:Das PVD-Verfahren ist für die Herstellung gleichmäßiger Beschichtungen bekannt, die für eine gleichmäßige Leistung und ein einheitliches Erscheinungsbild unerlässlich sind.
-
Anwendungen von PVD-Beschichtungen:
- Dauerhaft-dekorative Beschichtungen:Wird für Produkte verwendet, bei denen sowohl Haltbarkeit als auch Ästhetik wichtig sind, z. B. Uhren, Schmuck und Unterhaltungselektronik.
- Leistungsfähige Beschichtungen:Angewandt auf Komponenten, die verbesserte mechanische Eigenschaften erfordern, wie z. B. Schneidwerkzeuge, Formen und Motorenteile.
- Diamantähnliche Kohlenstoffbeschichtungen (DLC):Diese Beschichtungen zeichnen sich durch hohe Härte und geringe Reibung aus und sind daher ideal für Anwendungen in der Automobil- und Luftfahrtindustrie.
- PVD-Chrom-Alternativen:Wird als umweltfreundliche Alternative zur herkömmlichen Verchromung verwendet und bietet ähnliche ästhetische und schützende Eigenschaften.
-
Vorteile der PVD-Beschichtung:
- Verbesserte Eigenschaften:PVD-Beschichtungen verbessern die Verschleißfestigkeit, die Härte und die Korrosionsbeständigkeit des Substrats.
- Ästhetisches Erscheinungsbild:Mit diesem Verfahren können Beschichtungen mit einer Vielzahl von Farben und Oberflächen hergestellt werden, was die optische Attraktivität des Produkts erhöht.
- Umweltverträglichkeit:PVD gilt als umweltfreundliches Verfahren, da es im Vergleich zu herkömmlichen Beschichtungsmethoden nur wenig Abfall produziert und weniger Energie verbraucht.
Wenn man diese Schlüsselkomponenten und -prozesse versteht, kann man die Vielseitigkeit und Effektivität von PVD-Beschichtungen in verschiedenen industriellen Anwendungen schätzen.
Zusammenfassende Tabelle:
Komponente | Beschreibung |
---|---|
Ziel-Materialien | Metalle (z. B. Titan, Chrom), Keramiken und Elemente des Periodensystems. |
Reaktive Gase | Stickstoff, Kohlenwasserstoffe (z. B. für Nitrid- und Carbonitridbeschichtungen). |
Substrate | Metalle, Kunststoffe, Keramiken; erfordert Oberflächenvorbereitung für die Haftung. |
Verfahren | Verdampfungs- und Abscheidungsmethoden (z. B. Sputtern, Verdampfen). |
Anwendungen | Dauerhaft-dekorative Beschichtungen, Hochleistungsbeschichtungen, DLC, PVD-Chrom-Alternativen. |
Vorteile | Verbesserte Verschleißfestigkeit, Härte, Korrosionsbeständigkeit und ästhetisches Erscheinungsbild. |
Erschließen Sie das Potenzial von PVD-Beschichtungen für Ihre Anwendungen. Kontaktieren Sie unsere Experten noch heute !