Obwohl das Induktionslöten effizient und präzise ist, weist es mehrere Nachteile auf, die seine Eignung für bestimmte Anwendungen beeinträchtigen können. Dazu gehören Herausforderungen im Zusammenhang mit Materialeigenschaften, wie z. B. die Notwendigkeit einer präzisen Temperaturkontrolle aufgrund der engen Schmelzbereiche von Grund- und Zusatzmetallen sowie die Möglichkeit einer verringerten Materialhärte nach dem Hartlöten. Darüber hinaus kann der Prozess technisch anspruchsvoll sein und qualifiziertes Personal und spezielle Ausrüstung erfordern, was zu einem höheren Energieverbrauch und längeren Verarbeitungszeiten führen kann. Auch Umwelt- und Reinigungskosten vor dem Schweißen erhöhen den Gesamtaufwand. Diese Faktoren müssen bei der Auswahl des Induktionslötens für ein Projekt sorgfältig berücksichtigt werden.
Wichtige Punkte erklärt:
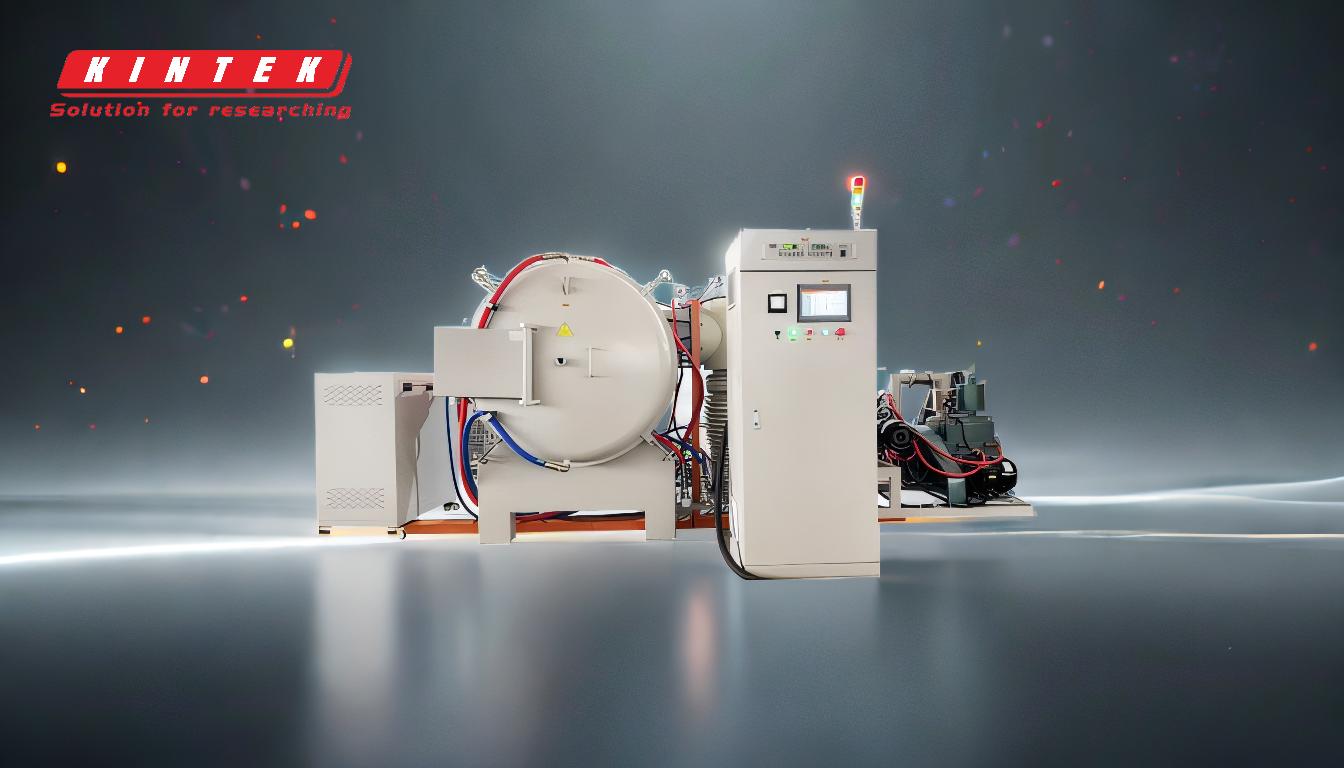
-
Präzise Temperaturkontrolle und homogene Wärmeverteilung:
- Beim Induktionslöten ist eine präzise Temperaturkontrolle erforderlich, da die Schmelzbereiche der Grund- und Zusatzmetalle oft sehr nahe beieinander liegen. Diese Präzision ist entscheidend, um eine Überhitzung oder Unterhitzung zu verhindern, die die Verbindungsqualität beeinträchtigen kann. Auch das Erreichen einer homogenen Wärmeverteilung ist insbesondere bei komplexen Geometrien eine Herausforderung, da eine ungleichmäßige Erwärmung zu schwachen Verbindungen oder Materialschäden führen kann.
-
Reduzierung der Materialhärte:
- Hochtemperaturprozesse wie Induktionslöten können die Härte bestimmter Materialien verringern, insbesondere von Metallen, die bei erhöhten Temperaturen geglüht oder erweicht werden. Diese Verringerung der Härte kann sich auf die mechanischen Eigenschaften des Endprodukts auswirken und es für Anwendungen, die eine hohe Festigkeit oder Verschleißfestigkeit erfordern, weniger geeignet machen.
-
Technischer Schwierigkeitsgrad und qualifizierte Arbeitskräfte:
- Induktionslöten ist ein technisch anspruchsvoller Prozess, der erfahrene Bediener erfordert, um die Ausrüstung zu verwalten und eine ordnungsgemäße Verbindungsbildung sicherzustellen. Die Komplexität der Einrichtung und Wartung der Induktionsspulen sowie die Notwendigkeit einer präzisen Kontrolle der Heizparameter machen es für unerfahrene Benutzer weniger zugänglich.
-
Hoher Energieverbrauch:
- Der Prozess kann energieintensiv sein, insbesondere bei großtechnischen oder kontinuierlichen Betrieben. Die Induktionsspulen benötigen erhebliche elektrische Energie, um die notwendigen elektromagnetischen Felder zum Erhitzen zu erzeugen, was im Vergleich zu einigen alternativen Lötmethoden zu höheren Betriebskosten führt.
-
Lange Bearbeitungszeiten:
- Während das Induktionslöten im Allgemeinen schneller ist als das Ofenlöten, kann es im Vergleich zu anderen Methoden wie dem Brennerlöten dennoch längere Bearbeitungszeiten erfordern. Dies gilt insbesondere für komplexe Baugruppen oder wenn mehrere Verbindungen nacheinander gelötet werden müssen, was die Produktionsgeschwindigkeit verlangsamen kann.
-
Hohe Reinigungs- und Umweltkosten:
- Vor dem Induktionslöten müssen Komponenten häufig gründlich gereinigt werden, um Oxide, Öle und andere Verunreinigungen zu entfernen, die den Lötprozess beeinträchtigen können. Dieser Reinigungsprozess kann kostspielig und zeitaufwändig sein. Darüber hinaus müssen die Auswirkungen der Verwendung von Flussmitteln oder Reinigungsmitteln auf die Umwelt berücksichtigt werden, da diese möglicherweise spezielle Entsorgungsmethoden erfordern oder zur Umweltverschmutzung beitragen.
-
Designbeschränkungen:
- Beim Induktionslöten sind enge Passungen zwischen den Komponenten erforderlich, um die Kapillarwirkung zu erleichtern, die für den ordnungsgemäßen Fluss des Schweißzusatzmetalls unerlässlich ist. Diese Anforderung kann Designbeschränkungen mit sich bringen, da Teile mit sehr engen Toleranzen hergestellt werden müssen. Darüber hinaus muss die Position des Lötmaterials während der Entwurfsphase sorgfältig geplant werden, was den Prozess komplexer macht.
Wenn Einkäufer und Ingenieure diese Nachteile verstehen, können sie fundierte Entscheidungen darüber treffen, ob Induktionslöten für ihre spezifische Anwendung die richtige Wahl ist, und die Vor- und Nachteile gegenüber anderen Lötmethoden abwägen.
Übersichtstabelle:
Nachteil | Beschreibung |
---|---|
Präzise Temperaturregelung | Erfordert eine genaue Überwachung, um eine Überhitzung oder Unterhitzung zu verhindern. |
Reduzierung der Materialhärte | Hohe Temperaturen können Metalle erweichen und so die Festigkeit und Verschleißfestigkeit verringern. |
Technischer Schwierigkeitsgrad und qualifizierte Arbeitskräfte | Erfordert qualifizierte Bediener und Spezialausrüstung. |
Hoher Energieverbrauch | Energieintensiver Prozess, der zu höheren Betriebskosten führt. |
Lange Bearbeitungszeiten | Langsamer als einige Alternativen, insbesondere bei komplexen Baugruppen. |
Hohe Reinigungs- und Umweltkosten | Erfordert eine gründliche Reinigung und kann umweltschädliche Flussmittel enthalten. |
Designbeschränkungen | Teile müssen enge Toleranzen aufweisen, was Design und Fertigung komplexer macht. |
Benötigen Sie Hilfe bei der Entscheidung, ob Induktionslöten für Ihr Projekt geeignet ist? Kontaktieren Sie noch heute unsere Experten für persönliche Beratung!