Beim Härten handelt es sich um einen Prozess, der dazu dient, die Härte und Festigkeit von Materialien, typischerweise Metallen, durch Wärmebehandlung oder andere Methoden zu erhöhen. Es bietet zwar erhebliche Vorteile wie verbesserte Verschleißfestigkeit und Haltbarkeit, bringt aber auch mehrere Nachteile mit sich. Dazu gehören erhöhte Sprödigkeit, verringerte Duktilität, Rissgefahr und Einschränkungen bei der Materialauswahl. Darüber hinaus kann der Prozess kostspielig und zeitaufwändig sein und zu Eigenspannungen führen, die die Leistung des Materials beeinträchtigen. Das Verständnis dieser Nachteile ist entscheidend, um fundierte Entscheidungen bei der Materialauswahl und -anwendung treffen zu können.
Wichtige Punkte erklärt:
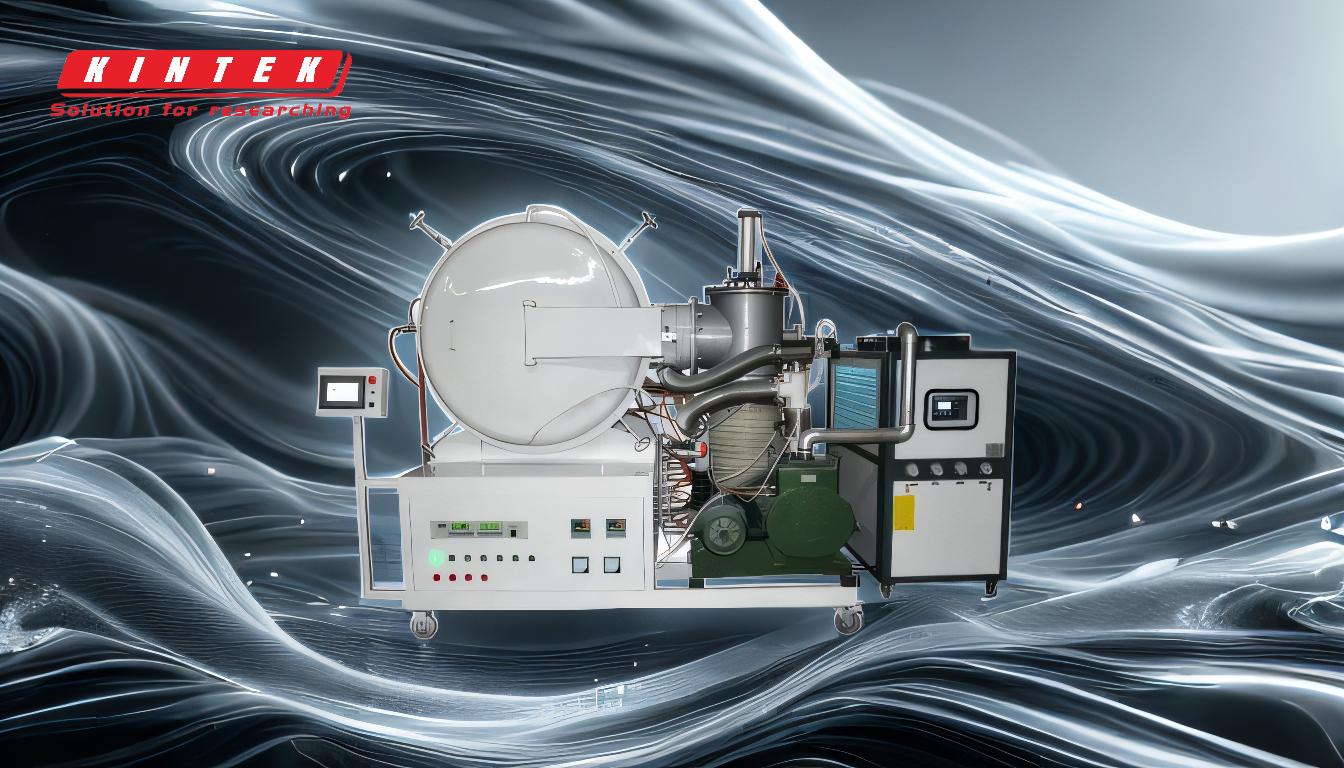
-
Erhöhte Sprödigkeit:
- Durch die Aushärtung nimmt die Sprödigkeit oft erheblich zu, wodurch das Material anfälliger für plötzliches Versagen unter Einwirkung von Stößen oder Belastungen wird.
- Dies ist besonders problematisch bei Anwendungen, bei denen das Material dynamischen Belastungen oder Stößen ausgesetzt ist.
-
Reduzierte Duktilität:
- Durch den Härtungsprozess verringert sich typischerweise die Duktilität des Materials, was bedeutet, dass es weniger in der Lage ist, sich plastisch zu verformen, ohne zu brechen.
- Diese Verringerung der Duktilität kann die Fähigkeit des Materials zur Energieabsorption einschränken und es für Anwendungen, die Flexibilität erfordern, ungeeignet machen.
-
Potenzial für Risse:
- Während des Härteprozesses, insbesondere bei schnellen Abkühlungsverfahren wie dem Abschrecken, besteht ein hohes Risiko der Rissbildung aufgrund thermischer Spannungen.
- Risse können die strukturelle Integrität des Materials beeinträchtigen und zu einem vorzeitigen Versagen führen.
-
Eigenspannungen:
- Durch das Härten können Eigenspannungen im Material entstehen, die zu Verformungen oder Verwerfungen führen können.
- Diese Spannungen können auch die Ermüdungslebensdauer des Materials verringern und es anfälliger für Ausfälle bei zyklischer Belastung machen.
-
Materialbeschränkungen:
- Nicht alle Materialien sind zum Härten geeignet. Einige Legierungen und Metalle reagieren möglicherweise nicht gut auf den Prozess, was die Auswahl an Materialien einschränkt, die effektiv gehärtet werden können.
- Dies kann die Gestaltungsmöglichkeiten einschränken und den Einsatz alternativer Materialien oder Behandlungen erforderlich machen.
-
Kosten- und Zeitüberlegungen:
- Der Härteprozess kann teuer sein und erfordert spezielle Ausrüstung und kontrollierte Umgebungen.
- Außerdem ist es zeitaufwändig, was die Produktionsvorlaufzeiten und die Gesamtkosten erhöhen kann.
-
Oberflächenhärte vs. Kerneigenschaften:
- Durch das Härten entsteht oft eine Oberfläche, die viel härter ist als der Kern des Materials. Diese Diskrepanz kann unter bestimmten Bedingungen zu Problemen wie Delamination oder Abplatzungen führen.
- Der Ausgleich der Oberflächenhärte mit den Kerneigenschaften ist ein entscheidender Gesichtspunkt bei der Konstruktion und Anwendung gehärteter Materialien.
-
Umwelt- und Sicherheitsbedenken:
- Der Härtungsprozess, insbesondere wenn er hohe Temperaturen und chemische Behandlungen erfordert, kann Umwelt- und Sicherheitsrisiken bergen.
- Um diese Risiken zu mindern, sind die ordnungsgemäße Handhabung und Entsorgung von Chemikalien sowie die Einhaltung von Sicherheitsprotokollen unerlässlich.
Zusammenfassend lässt sich sagen, dass das Härten zwar erhebliche Vorteile hinsichtlich Materialfestigkeit und Verschleißfestigkeit bietet, seine Nachteile jedoch sorgfältig abgewogen werden müssen. Dazu gehören erhöhte Sprödigkeit, verringerte Duktilität, Rissgefahr, Eigenspannungen, Materialbeschränkungen, Kosten- und Zeiterwägungen, Unterschiede zwischen Oberflächen- und Kerneigenschaften sowie Umwelt- und Sicherheitsbedenken. Das Verständnis dieser Nachteile ermöglicht eine bessere Entscheidungsfindung bei der Materialauswahl und -anwendung und stellt sicher, dass die Vorteile der Härtung maximiert und gleichzeitig ihre negativen Auswirkungen minimiert werden.
Übersichtstabelle:
Nachteil | Beschreibung |
---|---|
Erhöhte Sprödigkeit | Höheres Risiko eines plötzlichen Ausfalls unter Belastung oder Stößen. |
Reduzierte Duktilität | Verringerte Fähigkeit, sich zu verformen, ohne zu brechen, was die Flexibilität einschränkt. |
Potenzial für Risse | Hohe Rissgefahr durch thermische Spannungen beim schnellen Abkühlen. |
Eigenspannungen | Führt zu inneren Spannungen, die zu Verformungen oder einer verkürzten Ermüdungslebensdauer führen. |
Materialbeschränkungen | Nicht alle Materialien können gehärtet werden, was die Gestaltungsmöglichkeiten einschränkt. |
Kosten- und Zeitüberlegungen | Teures und zeitaufwändiges Verfahren, das spezielle Ausrüstung erfordert. |
Diskrepanz zwischen Oberfläche und Kern | Härtere Oberfläche im Vergleich zum Kern, wodurch die Gefahr einer Delaminierung oder Abplatzung besteht. |
Umwelt- und Sicherheitsrisiken | Hohe Temperaturen und Chemikalien werfen Sicherheits- und Umweltprobleme auf. |
Benötigen Sie Hilfe bei der Auswahl des richtigen Materials oder Prozesses? Kontaktieren Sie noch heute unsere Experten für maßgeschneiderte Lösungen!