Der Glühprozess ist eine Wärmebehandlungstechnik, mit der die physikalischen und manchmal chemischen Eigenschaften von Materialien, vor allem Metallen und Keramiken, verändert werden, um ihre mechanischen und thermischen Eigenschaften zu verbessern. Durch das Glühen werden Materialeigenschaften wie Dichte, Härte, Hitzebeständigkeit und Duktilität verbessert und gleichzeitig Qualitätsstabilität und Produktionseffizienz gewährleistet. Bei Metallen verringert das Glühen die Härte und erhöht die Duktilität, sodass sie sich leichter formen lassen, ohne dass Risse entstehen. Außerdem wird die Kristallstruktur verfeinert und die elektrische Leitfähigkeit verbessert. Bei Keramik verbessert das Glühen die Dichte und Hitzebeständigkeit. Darüber hinaus kann das Glühen interne Spannungen abbauen, die durch Herstellungsprozesse verursacht werden, wie dies beim Wasserstoffglühen der Fall ist. Der Prozess umfasst häufig kontrollierte Atmosphären, wie z. B. Stickstoffgasmischungen, um Oxidation und chemische Reaktionen zu verhindern.
Wichtige Punkte erklärt:
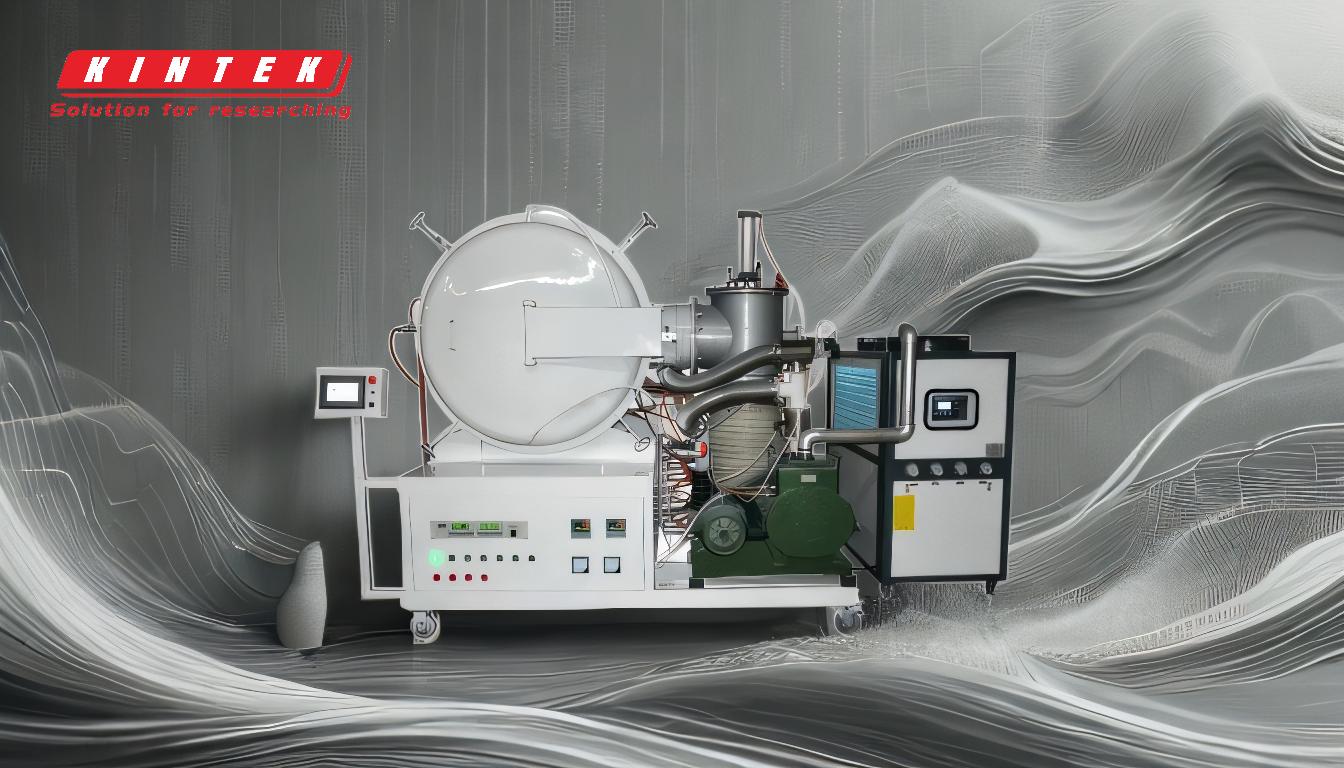
-
Verbesserung der Materialeigenschaften:
- Dichte und Härte: Das Glühen erhöht die Dichte und Härte keramischer Materialien und macht sie haltbarer und verschleißfester. Bei Metallen verringert das Glühen die Härte, wodurch sie duktiler und leichter zu bearbeiten sind.
- Hitzebeständigkeit: Der Prozess erhöht die Hitzebeständigkeit von Keramik und stellt sicher, dass sie hohen Temperaturen standhalten, ohne sich zu verschlechtern.
- Duktilität: Bei Metallen erhöht das Glühen die Duktilität, sodass das Material geformt werden kann, ohne dass es unter Druck reißt.
-
Verfeinerung der Kristallstruktur:
- Durch das Glühen wird die Kristallstruktur von Metallen verfeinert, wodurch Defekte reduziert und die elektrische Leitfähigkeit verbessert werden. Dies ist besonders vorteilhaft für Materialien, die in elektrischen Anwendungen verwendet werden.
-
Stressabbau:
- Wasserstoffglühen: Diese spezielle Art des Glühens baut mechanische Spannungen ab, die durch die Verarbeitung und Herstellung entstehen, und verhindert so Materialversagen während des Gebrauchs.
- Interner Stressabbau: Durch die Reduzierung innerer Spannungen sorgt das Glühen dafür, dass das Material stabil bleibt und weniger anfällig für Verformungen oder Risse unter Belastung ist.
-
Kontrollierte Atmosphäre:
- Inerte Atmosphäre: Beim Glühen werden üblicherweise Stickstoffgasmischungen verwendet, um eine inerte Atmosphäre zu schaffen und Oxidation und unerwünschte chemische Reaktionen zu verhindern. Dadurch wird sichergestellt, dass das Material seine gewünschten Eigenschaften behält.
-
Einfluss auf mechanische Eigenschaften:
- Streckgrenze und Dehnung: Bei Materialien wie X80-Pipelinestahl kann das Glühen bei niedrigem Wasserstoffgehalt die Streckgrenze um etwa 10 % erhöhen und gleichzeitig die Dehnung um etwa 20 % verringern. Dies ist darauf zurückzuführen, dass Kohlenstoffatome in interstitielle Versetzungsstellen diffundieren und eine Cottrell-Atmosphäre bilden, die Versetzungen an Ort und Stelle fixiert.
- Änderungen der Spannungs-Dehnungs-Kurve: Durch Glühen kann sich die Spannungs-Dehnungs-Kurve von Materialien verändern, was sich im Auftreten von Fließerscheinungen nach dem Glühen zeigt.
-
Produktionseffizienz und Qualitätsstabilität:
- Das Glühen gewährleistet eine gleichbleibende Materialqualität, was für industrielle Anwendungen von entscheidender Bedeutung ist. Es verbessert auch die Produktionseffizienz, indem es die Materialverarbeitbarkeit erleichtert und die Wahrscheinlichkeit von Fehlern verringert.
Durch das Verständnis dieser Schlüsselpunkte können Käufer von Geräten und Verbrauchsmaterialien fundierte Entscheidungen über den Glühprozess treffen und sicherstellen, dass sie die richtigen Materialien und Methoden für ihre spezifischen Anwendungen auswählen.
Übersichtstabelle:
Wirkung | Auswirkungen |
---|---|
Verbesserte Dichte und Härte | Erhöht die Haltbarkeit von Keramik; verringert die Härte, erhöht die Duktilität in Metallen. |
Verbesserte Hitzebeständigkeit | Stellt sicher, dass Keramik hohen Temperaturen standhält, ohne sich zu verschlechtern. |
Raffinierte Kristallstruktur | Reduziert Defekte, verbessert die elektrische Leitfähigkeit in Metallen. |
Stressabbau | Entlastet innere Spannungen und verhindert Materialversagen (z. B. Wasserstoffglühen). |
Kontrollierte Atmosphäre | Verwendet Stickstoffgas, um Oxidation zu verhindern und die Materialintegrität sicherzustellen. |
Änderungen der mechanischen Eigenschaften | Erhöht die Streckgrenze, verringert die Dehnung und verändert Spannungs-Dehnungs-Kurven. |
Produktionseffizienz | Verbessert die Qualitätsstabilität und die Verarbeitungsfreundlichkeit und reduziert Fehler. |
Optimieren Sie Ihre Materialeigenschaften durch Glühen – Kontaktieren Sie noch heute unsere Experten um mehr zu erfahren!