Das Glühverfahren ist in der Metallurgie und Werkstoffkunde zwar weit verbreitet, um die Eigenschaften von Metallen und Legierungen zu verbessern, hat jedoch einige Einschränkungen. Dazu gehören Einschränkungen im Zusammenhang mit der Temperaturregelung, dem Zeitbedarf, materialspezifischen Herausforderungen, dem Energieverbrauch und dem Potenzial für Oberflächenoxidation. Hinzu kommt, dass das Verfahren aufgrund komplexer Mikrostrukturen oder ungeeigneter Parameterwahl nicht immer die gewünschten Materialeigenschaften erzielt. Das Verständnis dieser Einschränkungen ist entscheidend für die Optimierung des Glühprozesses und die Gewährleistung der gewünschten Ergebnisse für bestimmte Anwendungen.
Die wichtigsten Punkte werden erklärt:
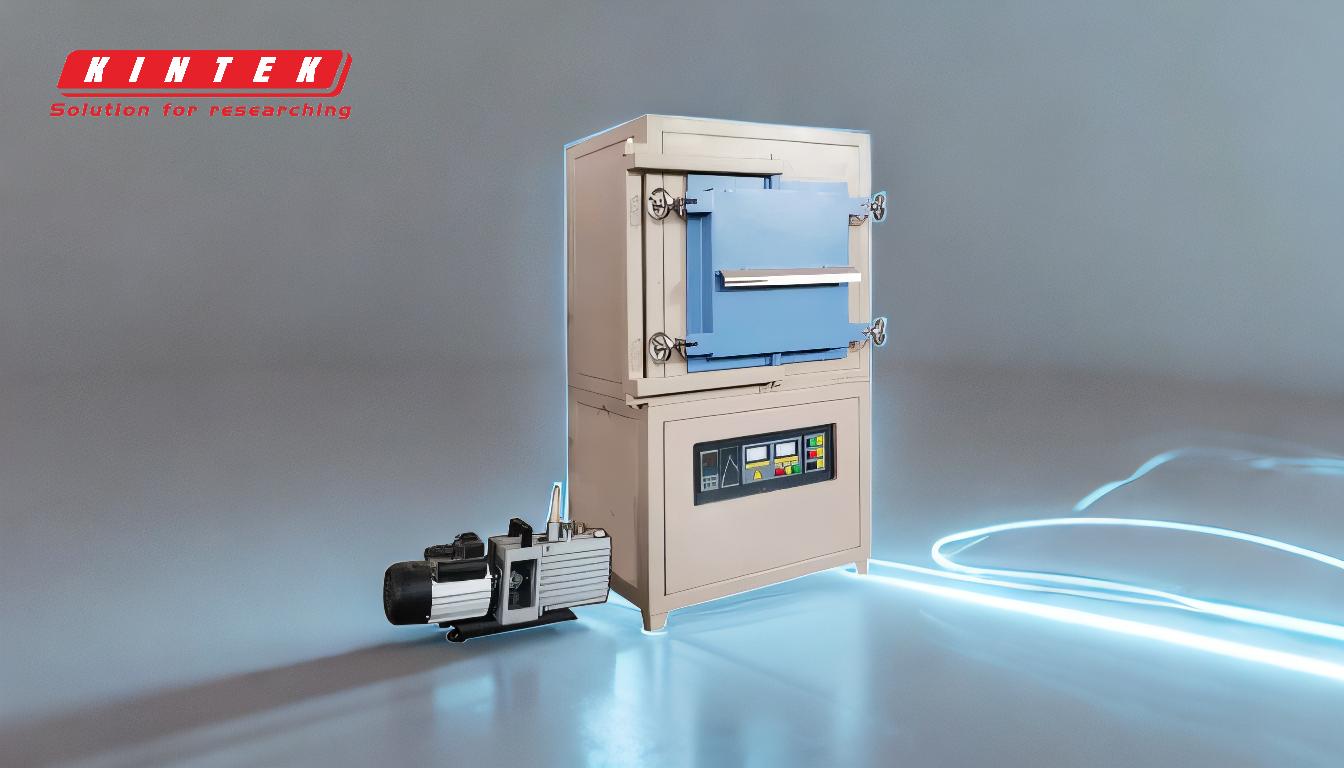
-
Herausforderungen bei der Temperaturkontrolle:
- Anforderungen an die Präzision: Das Glühen erfordert eine genaue Temperaturkontrolle, um die gewünschten Materialeigenschaften zu erreichen. Geringe Abweichungen können zu einer unvollständigen Rekristallisation oder zu Problemen beim Kornwachstum führen.
- Einschränkungen der Ausrüstung: Nicht alle Öfen können gleichmäßige Temperaturen bei großen oder komplexen Werkstücken aufrechterhalten, was zu uneinheitlichen Ergebnissen führt.
- Materielle Empfindlichkeit: Bei einigen Werkstoffen, wie z. B. kohlenstoffreichen Stählen oder bestimmten Legierungen, sind die Temperaturbereiche für ein effektives Glühen sehr eng, was den Prozess erschwert.
-
Zeitliche Beschränkungen:
- Lange Bearbeitungszeiten: Das Glühen erfordert oft lange Heiz- und Kühlzyklen, was bei der Produktion großer Mengen zeitaufwändig und ineffizient sein kann.
- Empfindlichkeit der Abkühlungsrate: Langsame Abkühlungsgeschwindigkeiten sind bei einigen Materialien erforderlich, um innere Spannungen zu vermeiden, was jedoch die Bearbeitungszeiten weiter verlängern kann.
-
Materialspezifische Beschränkungen:
- Uneinheitliche Mikrostrukturen: Materialien mit heterogener Zusammensetzung oder früherer Verarbeitung reagieren möglicherweise nicht gleichmäßig auf das Glühen.
- Fragen des Getreidewachstums: Übermäßiges Glühen kann zu übermäßigem Kornwachstum führen und die Festigkeit und Zähigkeit des Materials verringern.
- Eingeschränkte Anwendbarkeit: Einige Materialien, wie nichtmetallische Verbundwerkstoffe oder Keramik, profitieren nicht wesentlich vom Glühen.
-
Energieverbrauch:
- Hoher Energiebedarf: Die Aufrechterhaltung hoher Temperaturen über längere Zeiträume verbraucht viel Energie, was das Verfahren kostspielig und weniger umweltfreundlich macht.
- Ineffizienz bei der Stapelverarbeitung: Das Chargenglühen ist zwar üblich, aber im Vergleich zu kontinuierlichen Glühverfahren weniger energieeffizient.
-
Oberflächenoxydation und Entkohlung:
- Oxidationsgefahren: Hohe Temperaturen in Gegenwart von Sauerstoff können zur Oxidation der Oberfläche führen und die Qualität des Materials beeinträchtigen.
- Entkohlung: Bei Stählen kann längeres Erhitzen zu Kohlenstoffverlusten an der Oberfläche führen, was die Härte und Verschleißfestigkeit verringert.
-
Prozesskomplexität und Qualifikationsanforderungen:
- Optimierung der Parameter: Die Wahl der richtigen Glühtemperatur, -zeit und Abkühlgeschwindigkeit erfordert Fachwissen und Experimentierfreude.
- Behandlungen nach dem Glühen: Um die gewünschten Eigenschaften zu erreichen, können zusätzliche Verfahren wie Abschrecken oder Anlassen erforderlich sein, was die Komplexität erhöht.
-
Wirtschaftliche und praktische Zwänge:
- Kosten der Ausrüstung: Hochwertige Glühöfen und Temperaturregelungssysteme können in der Anschaffung und Wartung teuer sein.
- Platzbedarf: Großflächige Glühvorgänge erfordern viel Platz, der für kleinere Anlagen möglicherweise nicht zur Verfügung steht.
-
Inkonsistente Ergebnisse:
- Variabilität in der Materialantwort: Selbst bei kontrollierten Parametern können Schwankungen in der Materialzusammensetzung oder der vorherigen Verarbeitung zu uneinheitlichen Ergebnissen führen.
- Menschliches Versagen: Die manuelle Steuerung von Glühprozessen erhöht das Risiko von Fehlern, wie z. B. falsche Temperatureinstellungen oder Zeitvorgaben.
-
Begrenzte Verbesserung für bestimmte Immobilien:
- Kompromisse zwischen Härte und Festigkeit: Durch das Glühen werden oft Härte und Festigkeit verringert, um die Duktilität zu verbessern, was nicht für alle Anwendungen wünschenswert ist.
- Begrenzte Auswirkungen auf Defekte: Das Glühen kann zwar die inneren Spannungen reduzieren, aber nicht alle Defekte, wie Hohlräume oder Einschlüsse, beseitigen.
-
Umwelt- und Sicherheitsaspekte:
- Wärme und Emissionen: Bei Hochtemperaturprozessen entstehen Wärme und Emissionen, die eine angemessene Belüftung und Sicherheitsmaßnahmen erfordern.
- Sicherheit der Arbeitnehmer: Der Umgang mit heißen Materialien und der Betrieb von Hochtemperaturgeräten stellen ein Sicherheitsrisiko dar.
Wenn Hersteller und Ingenieure diese Einschränkungen verstehen, können sie Glühprozesse besser gestalten, geeignete Materialien auswählen und ergänzende Behandlungen durchführen, um optimale Ergebnisse zu erzielen.
Zusammenfassende Tabelle:
Einschränkung Kategorie | Zentrale Herausforderungen |
---|---|
Temperaturkontrolle | Präzisionsanforderungen, Ausrüstungsgrenzen, Materialempfindlichkeit |
Zeitliche Beschränkungen | Lange Bearbeitungszeiten, Empfindlichkeit der Abkühlgeschwindigkeit |
Materialspezifische Fragen | Uneinheitliche Mikrostrukturen, Kornwachstum, begrenzte Anwendbarkeit |
Energieverbrauch | Hoher Energiebedarf, Ineffizienz bei Stapelverarbeitung |
Oxidation der Oberfläche | Oxidationsrisiken, Entkohlung bei Stählen |
Komplexität der Prozesse | Parameteroptimierung, Nachglühbehandlungen |
Wirtschaftliche Zwänge | Kosten der Ausrüstung, Platzbedarf |
Inkonsistente Ergebnisse | Variabilität in der Reaktion des Materials, menschliches Versagen |
Begrenzte Eigentumsverbesserung | Kompromisse zwischen Härte und Festigkeit, begrenzte Fehlerbeseitigung |
Umweltaspekte | Hitze und Emissionen, Risiken für die Arbeitssicherheit |
Benötigen Sie Hilfe bei der Optimierung Ihres Glühprozesses? Kontaktieren Sie unsere Experten noch heute für maßgeschneiderte Lösungen!