Beim Hartlöten handelt es sich um einen Prozess, bei dem zwei oder mehr Metallteile mit einem Füllmetall verbunden werden, dessen Schmelzpunkt über 450 °C, aber unter dem Schmelzpunkt der Grundmetalle liegt. Bestimmte Faktoren können jedoch das Löten einer Verbindung unmöglich machen oder zu einer minderwertigen Verbindung führen. Zu diesen Faktoren gehören die falsche Materialauswahl, unzureichende Oberflächenvorbereitung, unzureichende Erwärmung, schlechte Verbindungsgestaltung und Verschmutzung. Das Verständnis dieser Herausforderungen ist entscheidend für das Erreichen einer erfolgreichen Lötverbindung.
Wichtige Punkte erklärt:
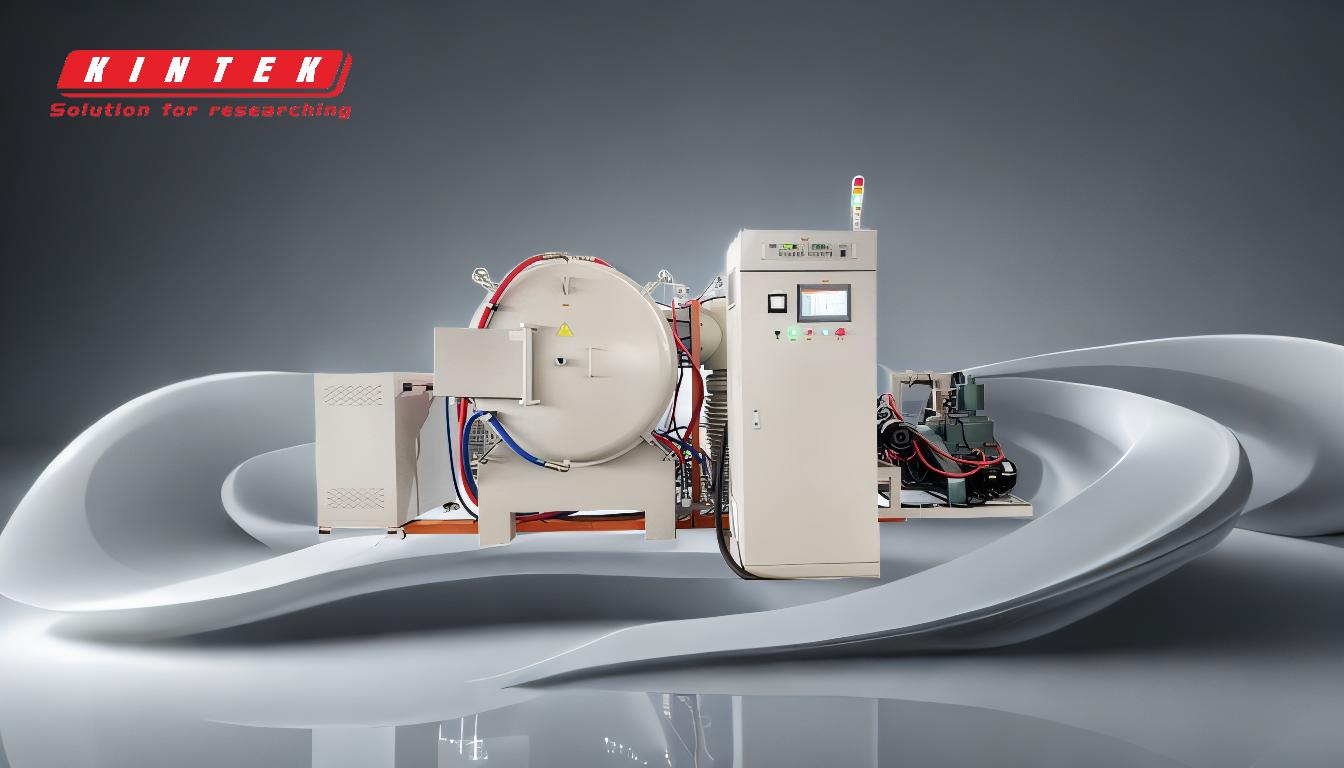
-
Falsche Materialauswahl:
- Nicht übereinstimmende Metalle: Wenn die Grundmetalle und das Füllmetall inkompatible Eigenschaften haben, wie z. B. unterschiedliche Schmelzpunkte oder Wärmeausdehnungsraten, kann das Löten fehlschlagen. Beispielsweise kann der Versuch, Aluminium mit Stahl ohne geeigneten Zusatzwerkstoff zu verlöten, zum Versagen der Verbindung führen.
- Ungeeigneter Zusatzwerkstoff: Das Füllmetall muss den richtigen Schmelzpunkt und die richtigen Benetzungseigenschaften haben, um richtig zu fließen und sich mit den Grundmetallen zu verbinden. Die Verwendung eines Füllmetalls, das die Oberflächen nicht benetzt oder dessen Schmelzpunkt zu nahe am Grundmetall liegt, kann das Löten unmöglich machen.
-
Unzureichende Oberflächenvorbereitung:
- Oxidschichten: Metalle bilden auf ihren Oberflächen häufig Oxidschichten, die die Verbindung des Zusatzmetalls verhindern können. Eine ordnungsgemäße Reinigung und Entfernung von Oxiden durch mechanische oder chemische Mittel ist unerlässlich.
- Verunreinigungen: Öle, Fette oder andere Verunreinigungen auf den Metalloberflächen können den Lötvorgang beeinträchtigen. Um eine starke Verbindung zu gewährleisten, ist eine gründliche Reinigung erforderlich.
-
Unzureichende Heizung:
- Ungleichmäßige Erwärmung: Wenn die Verbindung nicht gleichmäßig erhitzt wird, fließt das Zusatzmetall möglicherweise nicht richtig, was zu einer unvollständigen Verbindung führt. Dies kann auf eine falsche Brennertechnik oder unzureichende Ofeneinstellungen zurückzuführen sein.
- Unzureichende Temperatur: Die Löttemperatur muss hoch genug sein, um das Zusatzmetall zu schmelzen, darf aber nicht so hoch sein, dass die Grundmetalle beschädigt werden. Wenn die Temperatur zu niedrig ist, fließt das Füllmetall nicht, und wenn sie zu hoch ist, können sich die Grundmetalle verziehen oder schmelzen.
-
Schlechtes Gelenkdesign:
- Unzureichender Abstand: Der Spalt zwischen den beiden zu lötenden Metallteilen muss präzise sein. Wenn der Spalt zu klein ist, fließt das Zusatzmetall möglicherweise nicht in die Verbindung. Wenn es zu groß ist, bildet das Zusatzmetall möglicherweise keine starke Verbindung.
- Komplexe Geometrie: Verbindungen mit komplexen Formen oder engen Ecken können schwierig zu löten sein, da das Zusatzmetall möglicherweise nicht gleichmäßig in alle Bereiche fließt.
-
Kontamination beim Löten:
- Luftverschmutzung: Die Einwirkung von Sauerstoff oder anderen reaktiven Gasen beim Löten kann zu Oxidation führen, die die Verbindung des Zusatzmetalls verhindert. Die Verwendung einer kontrollierten Atmosphäre oder eines Flussmittels kann dieses Problem mildern.
- Flussmittelrückstände: Während Flussmittel zur Entfernung von Oxiden und zur Verbesserung der Benetzung verwendet werden, kann eine übermäßige oder unsachgemäße Anwendung von Flussmittel Rückstände hinterlassen, die die Verbindung schwächen.
-
Nichtübereinstimmung der Wärmeausdehnung:
- Differenzielle Expansion: Wenn die Grundmetalle deutlich unterschiedliche Wärmeausdehnungsraten aufweisen, kann es beim Erhitzen und Abkühlen zu Spannungen in der Verbindung kommen, die zu Rissen oder Ausfällen führen können. Dies ist insbesondere bei ungleichen Metallverbindungen problematisch.
-
Falsche Kühlrate:
- Schnelle Abkühlung: Zu schnelles Abkühlen der Verbindung kann zu thermischen Spannungen führen, die zu Rissen oder einer schwachen Verbindung führen können. Eine kontrollierte Kühlung ist unerlässlich, um eine starke, dauerhafte Verbindung zu gewährleisten.
-
Bedienerfehler:
- Falsche Technik: Eine unsachgemäße Handhabung des Lötbrenners, eine falsche Anwendung des Flussmittels oder eine Fehlausrichtung der Verbindung können zum Versagen des Lötvorgangs führen. Eine angemessene Schulung und die Einhaltung bewährter Verfahren sind von entscheidender Bedeutung.
Durch die Berücksichtigung dieser Faktoren ist es möglich, die Herausforderungen zu meistern, die das Hartlöten einer Verbindung unmöglich machen, und eine starke, zuverlässige Verbindung zu erreichen. Die richtige Materialauswahl, Oberflächenvorbereitung, Erwärmung, Verbindungsgestaltung und Kontaminationskontrolle sind entscheidend für den Erfolg des Lötprozesses.
Übersichtstabelle:
Herausforderung | Beschreibung |
---|---|
Falsche Materialauswahl | Nicht übereinstimmende Metalle oder ungeeignetes Zusatzmetall können die Verbindung verhindern. |
Unzureichende Oberflächenvorbereitung | Oxidschichten oder Verunreinigungen behindern den Fluss des Zusatzwerkstoffes. |
Unzureichende Heizung | Ungleichmäßige oder falsche Temperaturen führen zu einem schlechten Fluss des Zusatzmetalls. |
Schlechtes Gelenkdesign | Unzureichender Abstand oder komplexe Geometrie beeinträchtigen die Verteilung des Zusatzwerkstoffs. |
Kontamination | Witterungseinflüsse oder Flussmittelrückstände schwächen die Verbindung. |
Nichtübereinstimmung der Wärmeausdehnung | Unterschiedliche Ausdehnungsgeschwindigkeiten führen zu Spannungen und Rissen. |
Falsche Kühlrate | Durch schnelles Abkühlen entstehen thermische Spannungen, die die Bindung schwächen. |
Bedienerfehler | Eine unsachgemäße Technik oder eine falsche Ausrichtung führen zu Lötfehlern. |
Benötigen Sie Hilfe beim Erreichen einer stabilen Lötverbindung? Kontaktieren Sie noch heute unsere Experten für maßgeschneiderte Lösungen!