Glühen ist ein Wärmebehandlungsprozess, mit dem die physikalischen und manchmal chemischen Eigenschaften eines Materials verändert werden, typischerweise um seine Duktilität zu erhöhen und seine Härte zu verringern, wodurch es besser bearbeitbar wird. Der Prozess besteht darin, das Material auf eine bestimmte Temperatur zu erhitzen, es über einen bestimmten Zeitraum auf dieser Temperatur zu halten und es dann mit kontrollierter Geschwindigkeit abzukühlen. Die beiden Hauptprozesse des Glühens sind Wasserstoffglühen Und konventionelles Glühen , jeweils mit unterschiedlichen Eigenschaften und Anwendungen.
Wichtige Punkte erklärt:
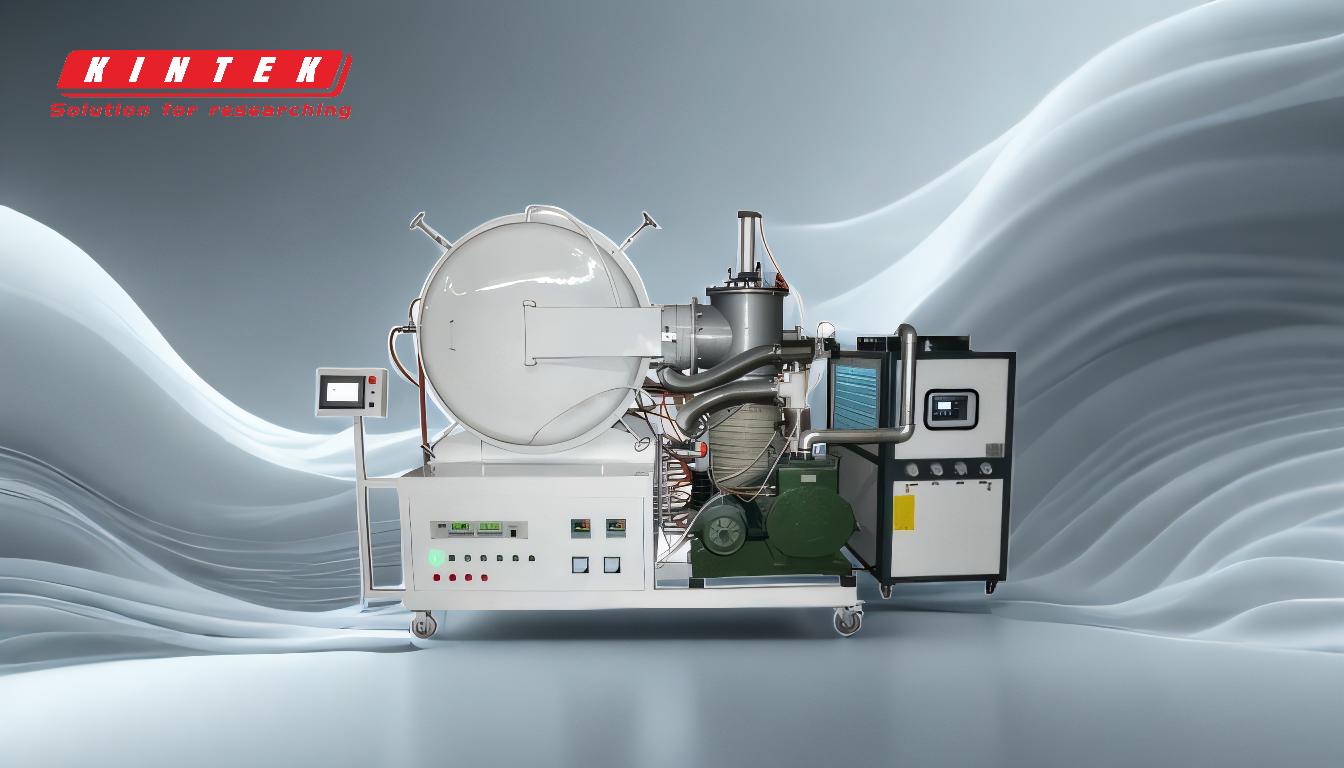
-
Wasserstoffglühen:
- Prozessübersicht: Beim Wasserstoffglühen wird das Material in einer kontrollierten Atmosphäre aus 100 % Wasserstoff erhitzt. Diese Umgebung verhindert Oxidation und Verfärbung des Produkts.
- Oberflächenreinigung: Wasserstoff wirkt als reduzierendes Gas, das bei der Reinigung der Oberfläche oxidierter Teile hilft, indem es die auf dem Material vorhandenen Oxide reduziert.
- Blankglühen: Dieser Prozess wird oft als „Blankglühen“ bezeichnet, da er zu einer sauberen, hellen Oberflächenbeschaffenheit führt.
- Entkohlungsrisiko: Einer der Nachteile des Wasserstoffglühens ist die Möglichkeit einer Entkohlung von Stahlteilen, die das Material schwächen kann. Es müssen Vorkehrungen getroffen werden, um dieses Risiko zu mindern.
- Kostenüberlegungen: Wasserstoff ist die teuerste Atmosphäre zum Glühen. Kostengünstigere Alternativen wie Stickstoff-Wasserstoff-Mischungen können jedoch effektiv genutzt werden, um die Kosten zu senken und gleichzeitig einige der Vorteile des Wasserstoffglühens zu nutzen.
-
Konventionelles Glühen:
- Prozessübersicht: Beim herkömmlichen Glühen wird das Material typischerweise in einem Ofen ohne den Einsatz einer speziellen Atmosphäre wie Wasserstoff erhitzt. Der Prozess folgt den drei Hauptphasen des Glühens: Erholung, Rekristallisation und Kornwachstum.
- Erholungsphase: In dieser Anfangsphase wird das Material erhitzt, um innere Spannungen abzubauen. Dieser Schritt bringt keine wesentliche Veränderung der Mikrostruktur mit sich, trägt aber zur Reduzierung der inneren Energie des Materials bei.
- Rekristallisationsstufe: Das Material wird über seine Rekristallisationstemperatur, aber unter seinen Schmelzpunkt erhitzt. In dieser Phase können sich neue, spannungsfreie Körner bilden, die die deformierten Körner ersetzen.
- Getreidewachstumsphase: Wenn das Material abkühlt, wachsen weiterhin neue Körner, was zu einer gleichmäßigeren und geschmeidigeren Mikrostruktur führt. Dieser Schritt ist entscheidend für das Erreichen der gewünschten mechanischen Eigenschaften, wie z. B. erhöhte Duktilität und verringerte Härte.
-
Vergleich von Wasserstoff und konventionellem Glühen:
- Atmosphäre: Wasserstoffglühen erfordert eine kontrollierte Wasserstoffatmosphäre, wohingegen herkömmliches Glühen in einer Standardofenatmosphäre durchgeführt werden kann.
- Oberflächenbeschaffenheit: Wasserstoffglühen sorgt aufgrund der reduzierenden Wirkung von Wasserstoff für eine hervorragende Oberflächengüte, die mit herkömmlichem Glühen normalerweise nicht erreicht wird.
- Kosten: Wasserstoffglühen ist aufgrund der Kosten für Wasserstoffgas und der Notwendigkeit spezieller Ausrüstung teurer. Konventionelles Glühen ist im Allgemeinen kostengünstiger.
- Materialeignung: Das Wasserstoffglühen eignet sich besonders für Materialien, die zur Oxidation neigen oder eine hochwertige Oberflächenbeschaffenheit erfordern. Konventionelles Glühen eignet sich für ein breiteres Spektrum an Materialien und Anwendungen.
-
Anwendungen des Glühens:
- Wasserstoffglühen: Dieses Verfahren wird häufig in Branchen eingesetzt, in denen eine hochwertige Oberflächenbeschaffenheit von entscheidender Bedeutung ist, beispielsweise bei der Herstellung von Edelstahlkomponenten, Drähten und anderen Präzisionsteilen.
- Konventionelles Glühen: Dieses Verfahren wird häufig bei der Herstellung verschiedener Metallprodukte eingesetzt, darunter Stahl, Aluminium und Kupfer, wobei das Hauptziel darin besteht, die Duktilität zu verbessern und die Härte zu verringern.
Zusammenfassend lässt sich sagen, dass die beiden Hauptprozesse des Glühens – Wasserstoffglühen und konventionelles Glühen – unterschiedlichen Zwecken dienen und auf der Grundlage der spezifischen Anforderungen des Materials und des gewünschten Ergebnisses ausgewählt werden. Das Wasserstoffglühen bietet eine bessere Oberflächenqualität, allerdings zu höheren Kosten, während das konventionelle Glühen vielseitiger und kostengünstiger für eine Vielzahl von Anwendungen ist.
Übersichtstabelle:
Aspekt | Wasserstoffglühen | Konventionelles Glühen |
---|---|---|
Atmosphäre | Kontrollierte Wasserstoffatmosphäre (100 % H₂ oder N₂-H₂-Mischungen) | Standard-Ofenatmosphäre |
Oberflächenbeschaffenheit | Hervorragende, saubere und glänzende Oberfläche (Blankglühen) | Standardausführung, keine spezielle Oberflächenbehandlung |
Kosten | Höher aufgrund von Wasserstoffgas und Spezialausrüstung | Kostengünstiger |
Materialeignung | Ideal für Materialien, die zu Oxidation neigen oder eine hochwertige Oberflächenveredelung erfordern | Geeignet für eine Vielzahl von Materialien und Anwendungen |
Anwendungen | Edelstahlkomponenten, Draht, Präzisionsteile | Stahl-, Aluminium-, Kupfer- und andere Metallprodukte |
Benötigen Sie Hilfe bei der Auswahl des richtigen Glühverfahrens für Ihre Materialien? Kontaktieren Sie noch heute unsere Experten für persönliche Beratung!