Aufkohlen ist ein Wärmebehandlungsverfahren, mit dem die Oberflächeneigenschaften von kohlenstoffarmen Stahllegierungen durch Einbringen von Kohlenstoff in die Oberflächenschicht verbessert werden. Dieser Prozess erhöht die Härte und Verschleißfestigkeit des Stahls und sorgt gleichzeitig für einen duktilen und zähen Kern. Die Aufkohlung erfolgt durch Erhitzen des Stahls unter seinen Schmelzpunkt in einer kohlenstoffreichen Umgebung, wodurch Kohlenstoffatome in die Oberfläche diffundieren können. Nach der Diffusion wird der Stahl in Öl abgeschreckt, um die mit Kohlenstoff angereicherte Oberfläche zu härten. Typische Härtetiefen reichen von 0,020″ bis 0,050″ und eignen sich daher ideal für Anwendungen, die eine harte, verschleißfeste Außenseite und einen elastischen Kern erfordern.
Wichtige Punkte erklärt:
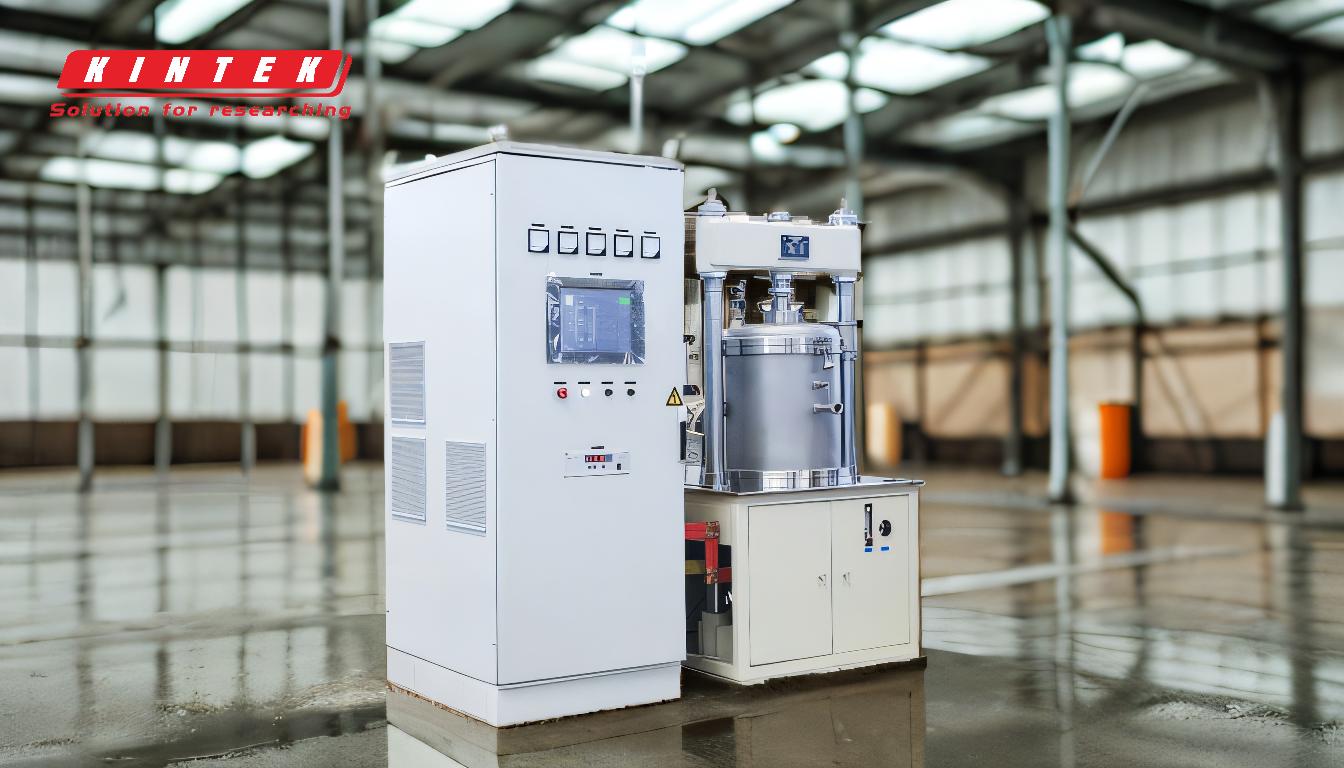
-
Definition und Zweck des Aufkohlens:
- Beim Aufkohlen handelt es sich um einen Oberflächenhärtungsprozess, der auf kohlenstoffarme Stahllegierungen angewendet wird.
- Der Hauptzweck besteht darin, die Oberfläche des Stahls mit Kohlenstoff anzureichern, wodurch seine Härte und Verschleißfestigkeit erhöht wird und gleichzeitig ein weicher, duktiler Kern erhalten bleibt.
- Dieses Verfahren ist besonders nützlich für Komponenten, die eine hohe Oberflächenbeständigkeit erfordern, wie z. B. Zahnräder, Wellen und Lager.
-
Prozessmechanismus:
- Der Stahl wird in einer kohlenstoffreichen Umgebung, beispielsweise einer endothermen Atmosphäre oder einem kohlenstoffhaltigen Medium, unter seinen Schmelzpunkt erhitzt.
- Kohlenstoffatome diffundieren in die Stahloberfläche und bilden eine mit Kohlenstoff angereicherte Schicht.
- Nach der Diffusion wird der Stahl schnell in Öl oder einem anderen Kühlmedium abgeschreckt, um die Oberfläche zu härten.
-
Vorteile des Aufkohlens:
- Oberflächenhärte: Die mit Kohlenstoff angereicherte Oberfläche wird deutlich härter und verbessert so die Verschleißfestigkeit.
- Duktiler Kern: Der Kern bleibt weich und formbar und bietet Zähigkeit und Schlagfestigkeit.
- Gehäusetiefenkontrolle: Die Tiefe der gehärteten Schicht (typischerweise 0,020″ bis 0,050″) kann gesteuert werden, um spezifische Anwendungsanforderungen zu erfüllen.
-
Anwendungen von aufgekohltem Stahl:
- Aufgekohlter Stahl wird häufig in Branchen verwendet, die Komponenten mit hoher Oberflächenhaltbarkeit und Ermüdungsbeständigkeit erfordern.
- Zu den häufigsten Anwendungen gehören Automobilteile (Zahnräder, Nockenwellen), Industriemaschinen (Lager, Rollen) und Werkzeuge.
-
Vergleich mit anderen Wärmebehandlungsverfahren:
- Im Gegensatz zum Durchhärten, bei dem das gesamte Bauteil gehärtet wird, wird beim Aufkohlen selektiv nur die Oberfläche gehärtet.
- Dies ermöglicht eine Kombination aus Oberflächenhärte und Kernzähigkeit, die mit anderen Verfahren wie Abschrecken und Anlassen nicht erreichbar ist.
-
Endotherme Atmosphäre beim Aufkohlen:
- Beim Aufkohlen wird häufig eine endotherme Atmosphäre verwendet, um eine kontrollierte kohlenstoffreiche Umgebung zu schaffen.
- Diese Atmosphäre sorgt für eine gleichmäßige Kohlenstoffdiffusion und verhindert eine Oxidation der Stahloberfläche.
-
Bedeutung des Abschreckens:
- Das Abschrecken ist ein entscheidender Schritt im Aufkohlungsprozess, da es die Kohlenstoffatome einschließt und die Oberfläche in eine harte martensitische Struktur umwandelt.
- Die Wahl des Abschreckmediums (z. B. Öl, Wasser oder Polymer) beeinflusst die Endhärte und den Verzug des Bauteils.
-
Materielle Überlegungen:
- Das Aufkohlen ist bei Stählen mit niedrigem Kohlenstoffgehalt am effektivsten, da diese eine höhere Fähigkeit zur Kohlenstoffaufnahme haben.
- Stähle mit hohem Kohlenstoffgehalt eignen sich grundsätzlich nicht zum Aufkohlen, da sie bereits ausreichend Kohlenstoff zum Härten enthalten.
-
Qualitätskontrolle und Prüfung:
- Die Wirksamkeit der Aufkohlung wird häufig durch Härteprüfungen (z. B. Rockwell- oder Vickers-Härteprüfungen) und Mikrostrukturanalyse überprüft.
- Die Gehäusetiefe wird gemessen, um sicherzustellen, dass sie den Designspezifikationen entspricht.
-
Umwelt- und Sicherheitsaspekte:
- Aufgrund der Verwendung von kohlenstoffreichen Gasen und Abschreckölen müssen Aufkohlungsprozesse in gut belüfteten Bereichen durchgeführt werden.
- Der ordnungsgemäße Umgang mit Abschreckmedien und die Entsorgung von Abfallstoffen sind für die Minimierung der Umweltbelastung von entscheidender Bedeutung.
Durch das Verständnis dieser Schlüsselpunkte kann ein Käufer von Geräten oder Verbrauchsmaterialien fundierte Entscheidungen über die Eignung der Aufkohlung für seine spezifischen Anwendungen treffen. Dieses Verfahren bietet ein ausgewogenes Verhältnis von Oberflächenhärte und Kernzähigkeit und ist somit eine vielseitige und weit verbreitete Wärmebehandlungsmethode in verschiedenen Branchen.
Übersichtstabelle:
Aspekt | Einzelheiten |
---|---|
Zweck | Oberflächenhärtung für kohlenstoffarme Stahllegierungen. |
Verfahren | Erhitzen in einer kohlenstoffreichen Umgebung, gefolgt von Abschrecken. |
Vorteile | Erhöhte Oberflächenhärte, Verschleißfestigkeit und kontrollierte Einsatztiefe. |
Anwendungen | Zahnräder, Wellen, Lager, Automobilteile und Industriemaschinen. |
Materialeignung | Am effektivsten bei Stählen mit niedrigem Kohlenstoffgehalt; Nicht geeignet für Stähle mit hohem Kohlenstoffgehalt. |
Schlüsselschritt | Abschrecken, um Kohlenstoff einzuschließen und die Oberfläche zu härten. |
Testen | Härteprüfungen (Rockwell/Vickers) und Mikrostrukturanalyse. |
Entdecken Sie, wie Aufkohlen Ihre Stahlkomponenten verbessern kann – Kontaktieren Sie uns noch heute für kompetente Beratung!