Verdampfung und Sputtern sind zwei weit verbreitete Verfahren zur physikalischen Gasphasenabscheidung (PVD) zur Herstellung dünner Schichten auf Substraten.Beim Verdampfen wird ein Material im Vakuum erhitzt, bis es verdampft und der Dampf auf einem Substrat kondensiert.Beim Sputtern hingegen wird ein Zielmaterial mit hochenergetischen Ionen beschossen, die Atome ausstoßen, die sich dann auf dem Substrat ablagern.Beide Verfahren sind in Branchen wie der Halbleiter-, Optik- und Solarindustrie unverzichtbar, unterscheiden sich jedoch erheblich in ihren Mechanismen, Vorteilen und Anwendungen.
Die wichtigsten Punkte werden erklärt:
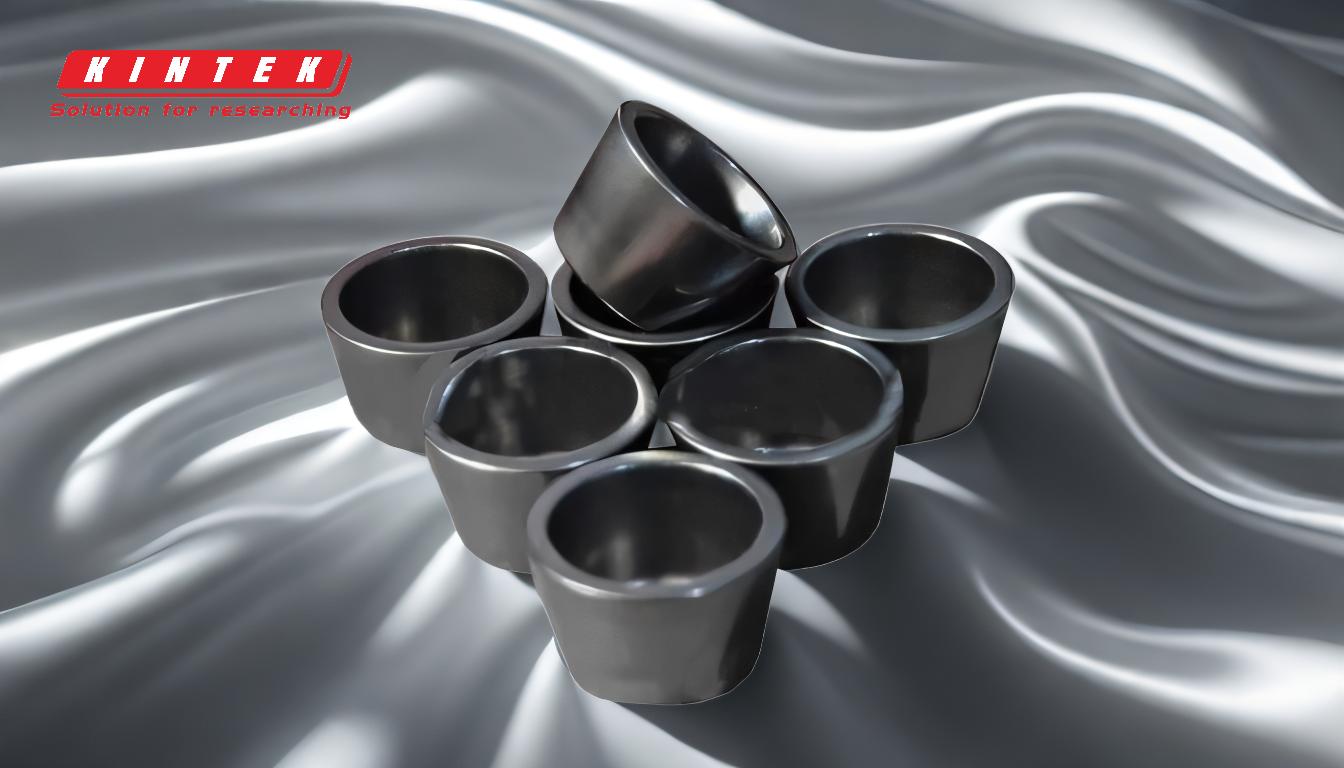
-
Mechanismus der Verdunstung:
- Bei der Verdampfung wird ein Material in einem Vakuum erhitzt, bis es seinen Verdampfungspunkt erreicht.
- Das verdampfte Material wandert durch das Vakuum, kondensiert auf dem Substrat und bildet einen dünnen Film.
- Dieses Verfahren wird in der Regel für Materialien mit niedrigem Schmelzpunkt eingesetzt und ist für seine hohen Abscheideraten bekannt.
-
Mechanismus des Sputterns:
- Beim Sputtern wird ein Targetmaterial mit hochenergetischen Ionen beschossen, die in der Regel aus einem Inertgas wie Argon stammen.
- Durch die Kollision zwischen den Ionen und dem Target werden Atome aus dem Target herausgeschleudert, die sich dann auf dem Substrat ablagern.
- Dieser Prozess findet in einer Vakuumkammer mit kontrollierter Atmosphäre statt, wobei häufig eine Plasmaentladung zum Einsatz kommt.
-
Vakuum Anforderungen:
- Die Verdampfung erfordert ein hohes Vakuum, um Verunreinigungen zu minimieren und eine effiziente Dampfbewegung zu gewährleisten.
- Das Sputtern arbeitet mit einem niedrigeren Vakuum, was es für bestimmte Anwendungen vielseitiger macht.
-
Abscheiderate:
- Das Aufdampfen bietet im Allgemeinen höhere Abscheideraten und eignet sich daher für Anwendungen, die dicke Schichten erfordern.
- Das Sputtern hat eine geringere Abscheiderate, außer bei reinen Metallen, bietet aber eine bessere Kontrolle über die Schichtdicke.
-
Schichtqualität und Haftung:
- Beim Sputtern entstehen Schichten mit besserer Haftung und Homogenität aufgrund der hohen Energie der abgeschiedenen Atome.
- Verdampfungsschichten können eine geringere Haftung und weniger Homogenität aufweisen, sind aber oft glatter.
-
Energie der abgeschiedenen Spezies:
- Die gesputterten Atome haben eine höhere kinetische Energie, was zu dichteren Schichten und einer besseren Stufenbedeckung führt.
- Verdampfte Atome haben eine geringere Energie, was zu weniger dichten Schichten und einer schlechteren Stufenbedeckung führen kann.
-
Korngröße und Filmstruktur:
- Beim Sputtern entstehen in der Regel kleinere Körner, die die Eigenschaften der Schichten wie Härte und Verschleißfestigkeit verbessern können.
- Beim Aufdampfen entstehen in der Regel größere Korngrößen, was für bestimmte optische oder elektrische Anwendungen von Vorteil sein kann.
-
Anwendungen:
- Das Aufdampfen wird üblicherweise für optische Beschichtungen, dekorative Oberflächen und einige Halbleiteranwendungen verwendet.
- Das Sputtern wird für Anwendungen bevorzugt, die eine hohe Haftung, gleichmäßige Beschichtungen und eine präzise Steuerung erfordern, wie z. B. in der Mikroelektronik und bei Solarpanels.
-
Vorteile des Sputterns:
- Bessere Haftung und Gleichmäßigkeit des Films.
- Möglichkeit der Abscheidung einer breiten Palette von Materialien, einschließlich Legierungen und Verbindungen.
- Niedrigere Abscheidetemperaturen, wodurch die thermische Belastung der Substrate verringert wird.
-
Vorteile der Verdampfung:
- Hohe Abscheidungsraten für eine schnellere Verarbeitung.
- Einfachheit und Kosteneffizienz für bestimmte Materialien.
- Geeignet für Materialien mit niedrigem Schmelzpunkt.
-
Herausforderungen:
- Das Sputtern kann komplexer und teurer sein, da ein Plasma erzeugt werden muss und eine präzise Steuerung erforderlich ist.
- Bei der Verdampfung kann es bei komplexen Geometrien Probleme mit der Stufenabdeckung und der Haftung geben.
Wenn man diese Hauptunterschiede kennt, können Käufer von Geräten und Verbrauchsmaterialien fundierte Entscheidungen darüber treffen, welches Verfahren für ihre spezifischen Anwendungsanforderungen am besten geeignet ist.
Zusammenfassende Tabelle:
Blickwinkel | Verdampfung | Sputtern |
---|---|---|
Mechanismus | Erhitzen von Material im Vakuum, bis es verdampft und auf einem Substrat kondensiert. | Beschuss des Zielmaterials mit hochenergetischen Ionen, um Atome auszustoßen und abzuscheiden. |
Vakuumniveau | Hohes Vakuum erforderlich. | Niedrigere Vakuumniveaus, vielseitiger. |
Abscheiderate | Höhere Raten, geeignet für dicke Schichten. | Niedrigere Raten, außer für reine Metalle; bessere Kontrolle der Schichtdicke. |
Filmqualität | Glattere Filme, geringere Adhäsion und Homogenität. | Bessere Adhäsion, Homogenität und dichtere Filme. |
Energie der Atome | Niedrigere Energie, weniger dichte Filme, schlechtere Stufenabdeckung. | Höhere Energie, dichtere Filme, bessere Stufenabdeckung. |
Korngröße | Größere Körner, vorteilhaft für optische/elektrische Anwendungen. | Kleinere Körner, die die Härte und Verschleißfestigkeit erhöhen. |
Anwendungen | Optische Beschichtungen, dekorative Veredelungen, einige Halbleiter. | Mikroelektronik, Solarpaneele, Anwendungen, die eine präzise Kontrolle erfordern. |
Vorteile | Hohe Abscheidungsraten, kostengünstig, geeignet für Materialien mit niedrigem Schmelzpunkt. | Bessere Haftung, Gleichmäßigkeit, niedrigere Abscheidetemperaturen, vielseitige Materialverwendung. |
Herausforderungen | Schlechte Stufenabdeckung, geringere Haftung bei komplexen Geometrien. | Komplexe und teure Einrichtung, erfordert präzise Kontrolle. |
Benötigen Sie Hilfe bei der Entscheidung zwischen Verdampfen und Sputtern für Ihre Anwendung? Kontaktieren Sie unsere Experten noch heute!