Das Hochtemperatursintern ist ein Verfahren zur Verbesserung der Eigenschaften von Werkstoffen durch Erhitzen auf Temperaturen knapp unter dem Schmelzpunkt, wodurch sich die Partikel durch atomare Diffusion verbinden können.Dieses Verfahren verbessert die mechanischen Eigenschaften wie Zugfestigkeit, Biegewechselfestigkeit und Kerbschlagarbeit erheblich.Es erfordert jedoch spezielle Ausrüstungen wie Hochtemperaturöfen und eine sorgfältige Planung, um die potenzielle Schrumpfung und die Kosten in den Griff zu bekommen.Das Verfahren kann mit verschiedenen Techniken durchgeführt werden, darunter das Heißpresssintern, das Vorteile wie geringeren Verformungswiderstand, kürzere Sinterzeiten und die Möglichkeit zur Herstellung komplexer Formen mit hoher Präzision bietet.Kontinuierliche Hochtemperatursinteröfen gewährleisten gleichbleibende Bedingungen und verhindern Oxidation, was sie ideal für die Produktion mit hohem Durchsatz macht.Insgesamt ist das Hochtemperatursintern ein vielseitiges und effektives Verfahren zur Herstellung von Hochleistungswerkstoffen, das allerdings erhebliche Investitionen und Fachkenntnisse erfordert.
Die wichtigsten Punkte werden erklärt:
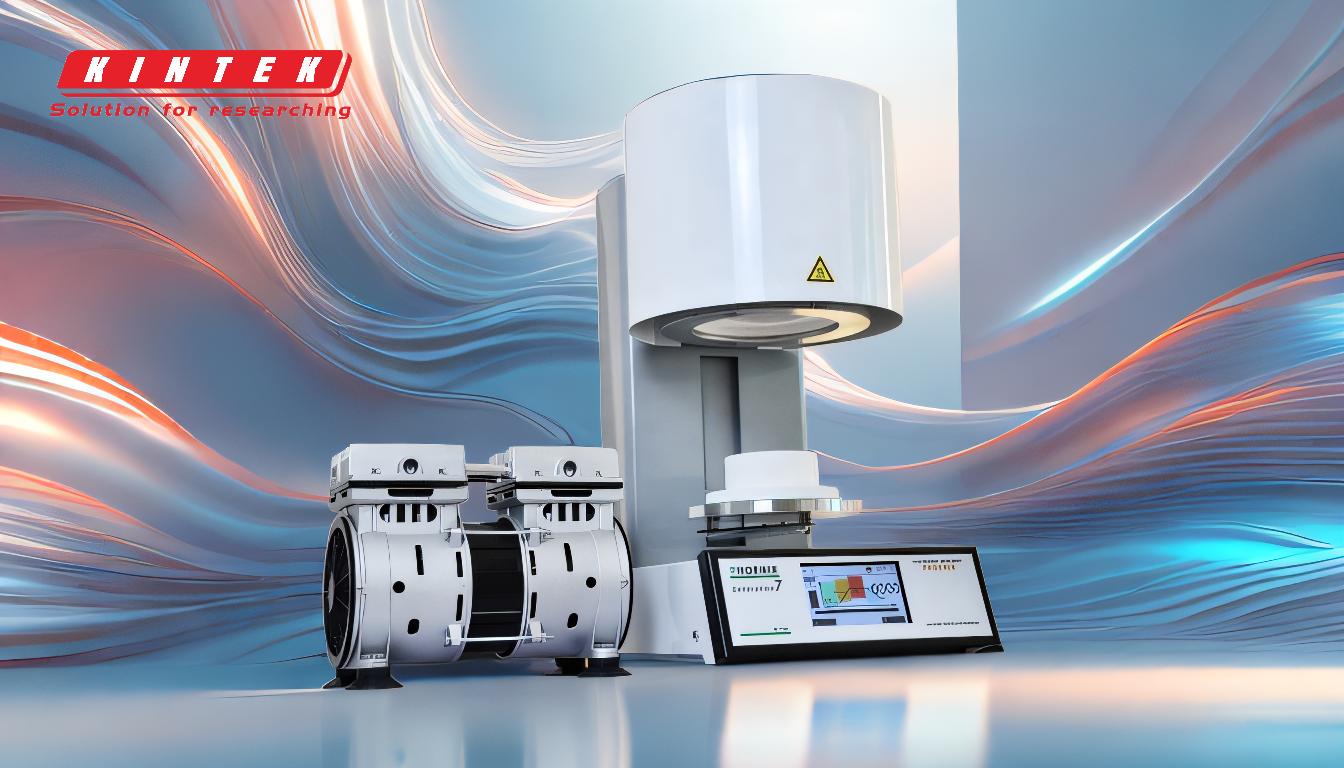
-
Definition und Zweck des Hochtemperatursinterns:
- Beim Hochtemperatursintern werden pulverförmige Werkstoffe bis knapp unter ihren Schmelzpunkt erhitzt, so dass sich die Partikel durch atomare Diffusion verbinden können.
- Das Hauptziel ist die Verbesserung der Materialeigenschaften, z. B. die Erhöhung der Zugfestigkeit um 30 %, der Biegewechselfestigkeit um 15 % und der Kerbschlagarbeit um 50 %.
-
Vorteile des Hochtemperatursinterns:
- Verbesserte mechanische Eigenschaften: Das Verfahren steigert die mechanische Festigkeit und Haltbarkeit von Materialien erheblich.
- Erhöhte Materialdichte: Durch Hochtemperatursintern entstehen Werkstoffe mit nahezu theoretischer Dichte, feinen Kornstrukturen und hervorragenden mechanischen und elektrischen Eigenschaften.
- Herstellung komplexer Formen: Es ermöglicht die Herstellung komplexer Formen und genauer Größen, die mit anderen Methoden nur schwer zu erreichen sind.
-
Herausforderungen und Überlegungen:
- Kosten: Das Verfahren ist teurer, da spezielle Öfen und Geräte benötigt werden.
- Schrumpfung: Teile können stärker schrumpfen als erwartet, was eine sorgfältige Planung und Designanpassung durch den Hersteller erfordert.
- Fachwissen erforderlich: Das Hochtemperatursintern erfordert ein hohes Maß an Fachwissen, um den Prozess effektiv zu steuern und Fehler zu vermeiden.
-
Arten von Sinterverfahren:
- Heißpresssintern: Kombiniert Erhitzung und Druckbeaufschlagung, um den Verformungswiderstand zu verringern, die Sintertemperaturen zu senken und die Sinterzeiten zu verkürzen.Es entstehen Materialien mit hoher Dichte und hervorragenden Eigenschaften.
- Kontinuierliches Hochtemperatursintern: Sorgt für gleichbleibende Bedingungen bei jedem Teil, verhindert Oxidation und garantiert Wiederholbarkeit und Durchsatz.
- Andere Methoden: Dazu gehören Wasserstoffschutz, Vakuumsintern, heißisostatisches Pressen und andere, die je nach Material und gewünschtem Ergebnis spezifische Vorteile aufweisen.
-
Vorteile spezifischer Sintertechniken:
- Heißpressen und Sintern: Bietet einen geringeren Verformungswiderstand, gleichzeitige Erhitzung und Druckbeaufschlagung sowie die Möglichkeit, komplexe Formen mit hoher Präzision herzustellen.
- Kontinuierliches Hochtemperatursintern: Bietet garantierten Durchsatz, Wiederholbarkeit und Schutz vor Oxidation und ist damit ideal für die Großserienproduktion.
- Isostatisches Heißpressen: Durch die Anwendung von hohem Druck und hoher Temperatur werden Pulverpartikel geformt und verschmolzen, wodurch Materialien mit hoher Dichte und mechanischen Eigenschaften entstehen.
-
Anwendungen und Materialtypen:
- Keramiken: Das Hochtemperatursintern eignet sich besonders gut für die Herstellung von keramischen Werkstoffen mit komplexer und poröser Struktur, wodurch ihre Festigkeit und Leistung verbessert wird.
- Metalle und Legierungen: Das Verfahren wird auch bei Metallen und Legierungen eingesetzt, um deren mechanische Eigenschaften und Haltbarkeit zu verbessern.
- Moderne Werkstoffe: Das Hochtemperatursintern ist entscheidend für die Herstellung fortschrittlicher Werkstoffe, die in der Luft- und Raumfahrt-, Automobil- und Elektronikindustrie verwendet werden.
-
Technologischer Fortschritt:
- IT-Integration: Bei modernen Sinterverfahren wird häufig IT-Technologie eingesetzt, um den Verdichtungsprozess und die Materialqualität besser zu steuern.
- Energie-Effizienz: Fortschritte in der Sintertechnologie haben zu einer verbesserten Gleichmäßigkeit des Temperaturfeldes und einem geringeren Energieverbrauch geführt.
- Großserienproduktion: Das Hochtemperatursintern kann jetzt zur Herstellung von Werkstoffen mit großem Durchmesser eingesetzt werden, was seine Anwendbarkeit in verschiedenen Industriezweigen erweitert.
-
Vergleich mit anderen Sinterverfahren:
- Festkörpersintern: Erhitzen eines pulverförmigen Materials unter seinen Schmelzpunkt, um die Partikel durch atomare Diffusion zu verbinden.
- Flüssigphasensintern: Verwendet ein flüssiges Lösungsmittel, um eine geringe Porosität und Bindung zu erzeugen, die dann durch Erhitzen ausgetrieben wird.
- Reaktives Sintern: Es handelt sich um eine chemische Reaktion der Pulverteilchen während der Erhitzung.
- Mikrowellen-Sintern: Nutzt Mikrowellen für eine schnellere Integration in Keramiken.
- Spark-Plasma-Sintern: Verwendet elektrischen Strom und physikalische Kompression, um eine schnelle Sinterung zu erreichen.
Zusammenfassend lässt sich sagen, dass das Hochtemperatursintern eine leistungsstarke Methode zur Verbesserung der Materialeigenschaften ist, die erhebliche Vorteile in Bezug auf Festigkeit, Dichte und die Herstellung komplexer Formen bietet.Es erfordert jedoch ein sorgfältiges Management von Kosten, Schrumpfung und Fachwissen, um optimale Ergebnisse zu erzielen.Das Verfahren ist vielseitig und es stehen verschiedene Techniken für unterschiedliche Materialien und Anwendungen zur Verfügung, was es zu einem Eckpfeiler der modernen Materialwissenschaft und Fertigung macht.
Zusammenfassende Tabelle:
Hauptaspekt | Einzelheiten |
---|---|
Zweck | Verbessert die Materialeigenschaften durch atomare Diffusion bei hohen Temperaturen. |
Vorteile | - Erhöhte Zugfestigkeit (30%) |
- Erhöhte Biegewechselfestigkeit (15%)
- Verbesserte Schlagenergie (50%) | | Herausforderungen
- | - Hohe Kosten
- Potenzieller Schwund Erfordert Fachwissen und spezielle Ausrüstung. |
- Sinterverfahren
- | - Heißpresssintern Kontinuierliches Hochtemperatursintern Heißisostatisches Pressen |
| Anwendungen | Keramik, Metalle, Legierungen, Luft- und Raumfahrt, Automobil- und Elektronikindustrie |