Sputtern ist ein weit verbreitetes Verfahren zur Abscheidung von Dünnschichten, bei dem Atome aus einem festen Zielmaterial durch Beschuss mit hochenergetischen Ionen, in der Regel aus einem Inertgas wie Argon, herausgeschleudert werden.Diese ausgestoßenen Atome lagern sich dann auf einem Substrat ab und bilden einen dünnen Film.Das Verfahren findet in einer Vakuumkammer statt, in der durch Anlegen einer Hochspannung ein Plasma erzeugt wird, das die Gasatome ionisiert und auf das Target beschleunigt.Durch den Zusammenstoß dieser Ionen mit dem Target werden Atome freigesetzt, die dann auf das Substrat wandern und dort haften bleiben, wodurch eine gleichmäßige und dauerhafte Beschichtung entsteht.Das Sputtern ist vielseitig, kann auf verschiedene Materialien angewendet werden und wird in verschiedenen Branchen eingesetzt, von der Elektronik bis zur Automobilindustrie.
Die wichtigsten Punkte werden erklärt:
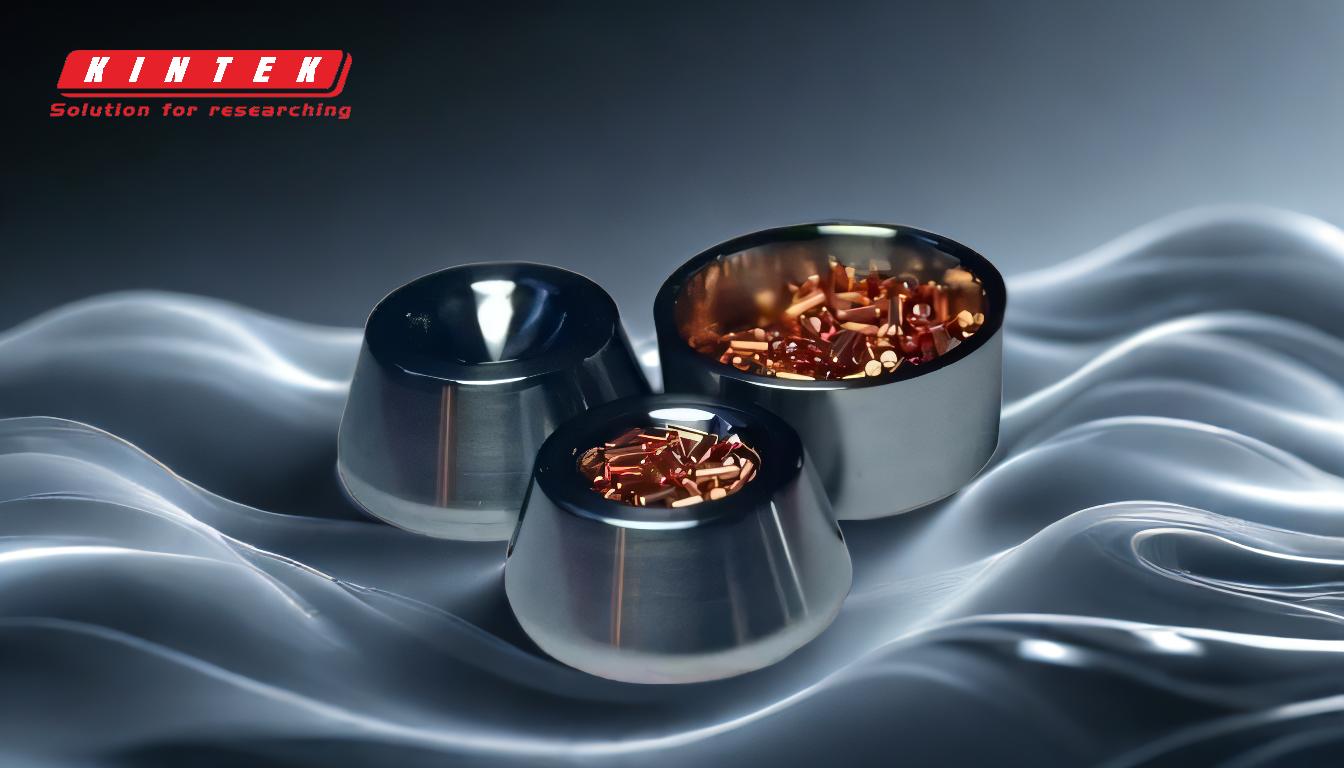
-
Grundprinzip des Sputterns:
- Beim Sputtern wird ein Zielmaterial in einer Vakuumkammer mit hochenergetischen Ionen beschossen, die in der Regel aus einem Inertgas wie Argon stammen.Diese Ionen lösen Atome aus dem Target, die sich dann auf einem Substrat ablagern und einen dünnen Film bilden.
- Das Verfahren beruht auf der Impulsübertragung zwischen den Ionen und den Targetatomen, wodurch ein effizienter Ausstoß und eine effiziente Abscheidung gewährleistet werden.
-
Komponenten des Sputtering-Systems:
- Vakuumkammer:Bietet eine kontrollierte Umgebung, um die Kontamination zu minimieren und eine effiziente Plasmaerzeugung zu gewährleisten.
- Ziel-Material:Die Quelle der abzuscheidenden Atome, in der Regel ein Metall oder eine Verbindung.
- Substrat:Die Oberfläche, auf der die dünne Schicht abgeschieden wird.
- Inertes Gas (z. B. Argon):Ionisiert zur Erzeugung des Plasmas, das das Ziel beschießt.
- Kathode und Anode:Elektroden, die zur Erzeugung des Plasmas und zur Beschleunigung der Ionen auf das Ziel verwendet werden.
-
Plasmaerzeugung und Ionenbeschleunigung:
- Zwischen der Kathode (Target) und der Anode wird eine Hochspannung angelegt, wodurch in Gegenwart von Inertgas ein Plasma entsteht.
- Die Gasatome werden zu positiv geladenen Ionen und werden auf das negativ geladene Target beschleunigt.
- Beim Aufprall übertragen die Ionen ihre Energie auf die Zielatome und schleudern sie in die Gasphase.
-
Abscheidungsprozess:
- Die ausgestoßenen Zielatome wandern durch die Vakuumkammer und lagern sich auf dem Substrat ab.
- Die abgeschiedenen Atome bilden einen dünnen, gleichmäßigen Film, der sicher auf dem Substrat haftet.
- Der Prozess kann wiederholt werden, um mehrere Schichten des gewünschten Materials zu erzeugen.
-
Arten des Sputterns:
- DC-Sputtern:Verwendet Gleichstrom zur Erzeugung des Plasmas, geeignet für leitende Materialien.
- RF-Sputtern:Nutzt Hochfrequenz für nichtleitende Materialien und verhindert so den Aufbau von Ladungen auf dem Target.
- Magnetron-Sputtern:Erhöht die Effizienz, indem die Elektronen durch Magnetfelder in der Nähe des Targets eingeschlossen werden, wodurch die Ionisierung verstärkt wird.
- Reaktives Sputtern:Einleiten reaktiver Gase (z. B. Sauerstoff oder Stickstoff) zur Bildung von Verbundschichten (z. B. Oxide oder Nitride).
-
Vorteile des Sputterns:
- Einheitlichkeit:Erzeugt sehr gleichmäßige und dichte Filme.
- Vielseitigkeit:Kann eine breite Palette von Materialien abscheiden, darunter Metalle, Legierungen und Verbindungen.
- Adhäsion:Bietet eine hervorragende Haftung zwischen Folie und Substrat.
- Skalierbarkeit:Geeignet für großtechnische Anwendungen.
-
Anwendungen des Sputterns:
- Elektronik:Wird bei der Halbleiterherstellung, bei Dünnschichttransistoren und integrierten Schaltungen verwendet.
- Optik:Abscheidung von Antireflexions- und Reflexionsschichten für Linsen und Spiegel.
- Automobilindustrie:Verbessert die Haltbarkeit und das Aussehen von Bauteilen durch Beschichtungen.
- Dekorative Beschichtungen:Bietet ästhetische Oberflächen für Konsumgüter.
- Energie:Wird in Solarzellen und Batterietechnologien verwendet.
-
Historischer Kontext:
- Das Sputtern wurde erstmals 1904 von Thomas Edison kommerziell genutzt, um dünne Metallschichten auf Wachsphonographenaufnahmen aufzubringen.
- Im Laufe der Zeit hat sich die Technik weiterentwickelt, wobei Fortschritte wie das Magnetronsputtern die Effizienz verbessert und die Anwendungsmöglichkeiten erweitert haben.
-
Herausforderungen und Überlegungen:
- Kosten:Erfordert teure Geräte und Hochvakuumbedingungen.
- Ratenkontrolle:Die Abscheidungsraten können im Vergleich zu anderen Techniken langsamer sein.
- Grenzen des Materials:Einige Materialien können aufgrund ihrer geringen Sputterausbeute oder Reaktivität schwer zu sputtern sein.
-
Zukünftige Trends:
- Entwicklung des Hochleistungsimpuls-Magnetronsputterns (HiPIMS) zur Verbesserung von Schichtqualität und Haftung.
- Integration mit anderen Abscheidetechniken für hybride Verfahren.
- Erforschung neuer Materialien und Anwendungen im Bereich der Nanotechnologie und der erneuerbaren Energien.
Wenn ein Käufer diese Schlüsselpunkte versteht, kann er die Eignung des Sputterns für seine spezifischen Bedürfnisse beurteilen und dabei Faktoren wie Materialkompatibilität, gewünschte Filmeigenschaften und Kosteneffizienz berücksichtigen.
Zusammenfassende Tabelle:
Aspekt | Einzelheiten |
---|---|
Grundprinzip | Beschuss des Zielmaterials mit hochenergetischen Ionen in einer Vakuumkammer. |
Wichtige Komponenten | Vakuumkammer, Targetmaterial, Substrat, Inertgas, Kathode und Anode. |
Arten des Sputterns | DC-, RF-, Magnetron- und reaktives Sputtern. |
Vorteile | Gleichmäßigkeit, Vielseitigkeit, hervorragende Haftung und Skalierbarkeit. |
Anwendungen | Elektronik, Optik, Automobilindustrie, dekorative Beschichtungen und Energiesektor. |
Herausforderungen | Hohe Kosten, langsamere Abscheidungsraten und Materialbeschränkungen. |
Zukünftige Trends | HiPIMS, Hybridverfahren und neue Materialien für Nanotechnologie und Energie. |
Sind Sie an Sputtering für Ihre Anwendungen interessiert? Kontaktieren Sie noch heute unsere Experten um mehr zu erfahren!