Sowohl die Elektronenstrahlverdampfung als auch das Ionensputtern sind Verfahren zur physikalischen Abscheidung aus der Gasphase (PVD), die sich in ihren Mechanismen, Betriebsparametern und Anwendungen deutlich unterscheiden.Bei der Elektronenstrahlverdampfung wird ein fokussierter Elektronenstrahl zum Erhitzen und Verdampfen von Hochtemperaturmaterialien verwendet, was zu einer hohen Abscheidungsrate führt und sich für Anwendungen wie Solarzellen und Glas eignet.Beim Sputtern hingegen wird ein Zielmaterial mit energiereichen Ionen beschossen, um Atome auszustoßen, die sich dann auf einem Substrat ablagern.Das Sputtern arbeitet bei niedrigeren Temperaturen, bietet eine bessere Haftung und Schichthomogenität und ist ideal für komplexe Substrate und hochreine dünne Schichten.Jede Methode hat ihre eigenen Vorteile, die von den spezifischen Anforderungen des jeweiligen Projekts abhängen.
Die wichtigsten Punkte werden erklärt:
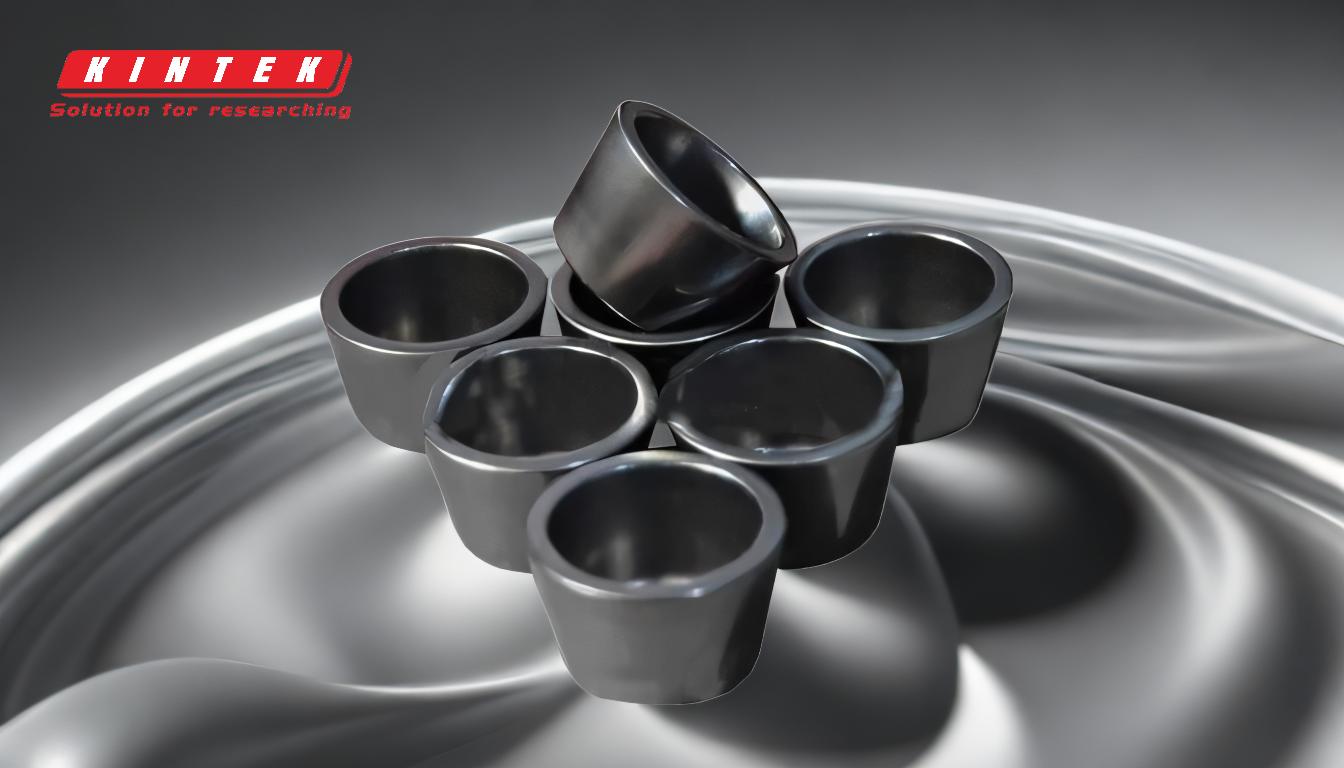
-
Mechanismus der Ablagerung:
- Elektronenstrahlverdampfung:Mit einem fokussierten Elektronenstrahl wird das Ausgangsmaterial erhitzt und verdampft.Das verdampfte Material kondensiert auf dem Substrat und bildet eine dünne Schicht.
- Ionen-Sputtern:Beschuss eines Zielmaterials mit energiereichen Ionen (in der Regel Argon) in einer Plasmaumgebung.Durch die Kollision werden Atome aus dem Target herausgeschleudert, die sich dann auf dem Substrat ablagern.
-
Betriebliche Umgebung:
- Elektronenstrahlverdampfung:Erfordert eine Hochvakuumumgebung, um Verunreinigungen zu minimieren und eine effiziente Verdampfung zu gewährleisten.
- Ionen-Sputtern:Arbeitet in einer Niedrigvakuum-Umgebung und oft in einem geschlossenen Magnetfeld, um die Ionisierung und die Abscheidungseffizienz zu verbessern.
-
Abscheidungsrate:
- Elektronenstrahlverdampfung:Bietet eine höhere Abscheidungsrate und eignet sich daher für Anwendungen, die eine schnelle Filmbildung erfordern.
- Ionen-Sputtern:Hat im Allgemeinen eine geringere Abscheidungsrate, insbesondere bei dielektrischen Materialien, bietet aber eine bessere Kontrolle der Filmeigenschaften.
-
Haftung und Filmqualität:
- Elektronenstrahlverdampfung:Erzeugt Schichten mit geringerer Haftung und weniger Homogenität, die möglicherweise Nachbehandlungen erfordern.
- Ionen-Sputtering:Bietet eine bessere Haftung, eine höhere Homogenität des Films und kleinere Korngrößen, was zu qualitativ hochwertigeren dünnen Filmen führt.
-
Temperatur-Anforderungen:
- Elektronenstrahlverdampfung:Erfordert hohe Temperaturen zum Verdampfen des Ausgangsmaterials, was die Verwendung bei temperaturempfindlichen Substraten einschränken kann.
- Ionen-Sputtern:Arbeitet bei niedrigeren Temperaturen und eignet sich daher für temperaturempfindliche Materialien und komplexe Substrate.
-
Skalierbarkeit und Automatisierung:
- Elektronenstrahlverdampfung:Weniger skalierbar und schwieriger zu automatisieren, da Hochvakuum und präzise Elektronenstrahlsteuerung erforderlich sind.
- Ionen-Sputtern:Größere Skalierbarkeit und einfachere Automatisierung, daher ideal für Großproduktionen und industrielle Anwendungen.
-
Anwendungen:
- Elektronenstrahlverdampfung:Wird aufgrund seiner hohen Abscheiderate häufig für Anwendungen wie Solarpaneele, Glasbeschichtungen und optische Filme verwendet.
- Ionen-Sputtern:Bevorzugt für die elektrische und optische Produktion, hochreine Dünnschichten und Beschichtungen auf komplexen Substraten aufgrund seiner hervorragenden Schichtqualität und Haftfestigkeit.
-
Energie der abgeschiedenen Spezies:
- Elektronenstrahlverdampfung:Erzeugt weniger energiereiche Dampfspezies, was zu weniger dichten Schichten führen kann.
- Ionen-Sputtern:Auswurf von Atomen mit höherer Energie, was zu dichteren und stärker haftenden Schichten führt.
-
Gas-Absorption:
- Elektronenstrahlverdampfung:Weniger anfällig für Gasabsorption aufgrund der Hochvakuumumgebung.
- Ionen-Sputtern:Es ist wahrscheinlicher, dass Gase absorbiert werden, was die Filmeigenschaften beeinträchtigen kann, aber auch reaktives Sputtern zur Erzeugung von Verbundschichten ermöglicht.
-
Ausrichtung der zerstäubten Partikel:
- Elektronenstrahlverdampfung:Erzeugt einen stärker dispergierten Dampfstrom, der zu einer weniger gerichteten Abscheidung führen kann.
- Ionen-Sputtern:Wirft die Partikel gerichteter aus und verbessert so die Abdeckung komplexer Geometrien.
Zusammenfassend lässt sich sagen, dass die Wahl zwischen Elektronenstrahlverdampfung und Ionensputtern von den spezifischen Anforderungen des Projekts abhängt, z. B. Abscheiderate, Schichtqualität, Komplexität des Substrats und Skalierbarkeit.Jede Methode hat ihre eigenen Vorteile und Grenzen, wodurch sie sich für unterschiedliche Anwendungen bei der Dünnschichtabscheidung eignen.
Zusammenfassende Tabelle:
Blickwinkel | Elektronenstrahlverdampfung | Ionen-Sputtern |
---|---|---|
Mechanismus | Ein fokussierter Elektronenstrahl erhitzt und verdampft Materialien. | Energetische Ionen beschießen das Zielmaterial und stoßen Atome aus. |
Betriebliche Umgebung | Hochvakuum erforderlich. | Niedrigeres Vakuum, oft mit einem Magnetfeld. |
Abscheiderate | Höhere Abscheidungsrate. | Geringere Abscheidungsrate, bessere Kontrolle der Filmeigenschaften. |
Haftung und Filmqualität | Geringere Adhäsion, weniger Homogenität. | Bessere Adhäsion, höhere Homogenität, kleinere Korngrößen. |
Temperatur | Hohe Temperaturen erforderlich, weniger geeignet für empfindliche Substrate. | Niedrigere Temperaturen, ideal für empfindliche Materialien und komplexe Substrate. |
Skalierbarkeit | Weniger skalierbar, schwieriger zu automatisieren. | Besser skalierbar, leichter zu automatisieren für die Großproduktion. |
Anwendungen | Sonnenkollektoren, Glasbeschichtungen, optische Filme. | Elektrische/optische Produktion, hochreine Schichten, komplexe Substrate. |
Energie der abgeschiedenen Atome | Niederenergetische Dampfspezies, weniger dichte Schichten. | Atome mit höherer Energie, dichtere und stärker haftende Filme. |
Gasabsorption | Weniger anfällig für Gasabsorption. | Neigt eher dazu, Gase zu absorbieren, was reaktives Sputtern ermöglicht. |
Richtungsabhängigkeit | Dispergierter Dampfstrom, weniger gerichtet. | Mehr gerichtet, bessere Abdeckung bei komplexen Geometrien. |
Benötigen Sie Hilfe bei der Auswahl des richtigen PVD-Verfahrens für Ihr Projekt? Kontaktieren Sie noch heute unsere Experten für eine persönliche Beratung!