Die Auswirkung der Dauer des Kugelmahlens auf die Partikelgröße ist signifikant, da sie die Verringerung der Partikelgröße durch mechanisches Mahlen direkt beeinflusst.In den ersten Stunden des Mahlens (1-5 Stunden) findet die stärkste Verringerung der Partikelgröße statt, wobei die durchschnittliche Partikelgröße von 160 μm auf 25 μm sinkt.Nach diesem Zeitraum verlangsamt sich die Größenverringerung, aber durch fortgesetztes Mahlen können immer noch feinere Partikel erzielt werden, wobei die Größe nach 10 Stunden Mahldauer unter 10 μm fällt.Längere Mahlzeiten und kleinere Mahlkugeln sind im Allgemeinen erforderlich, um kleinere Partikel zu erzeugen, da sie die Häufigkeit der Kollisionen und die Effizienz des Partikelabbaus erhöhen.Außerdem tragen wiederholte Mahlzyklen zur Erosion größerer Partikel bei, was zu einem höheren Anteil kleinerer, nanoskaliger Fragmente führt.
Die wichtigsten Punkte werden erklärt:
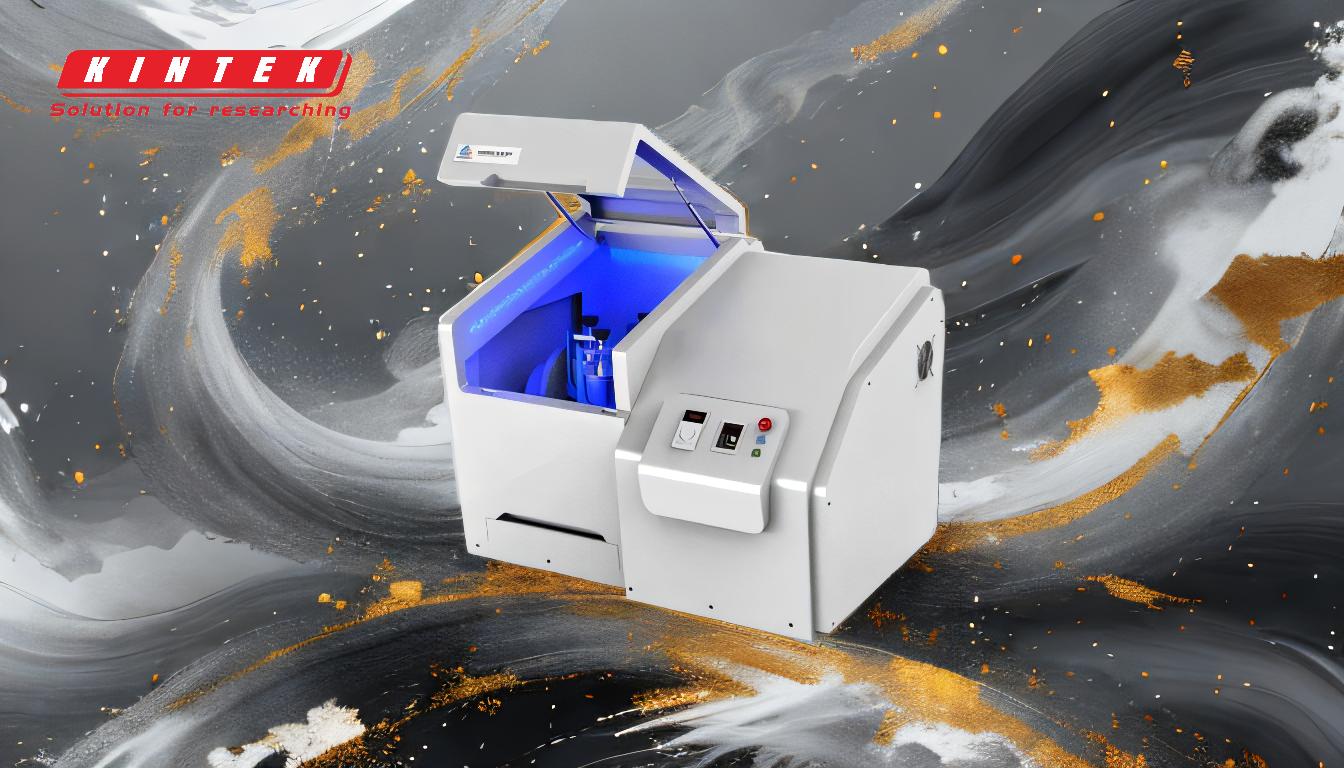
-
Erste schnelle Partikelgrößenreduzierung (1-5 Stunden):
- Die stärkste Verringerung der Partikelgröße tritt während der ersten 1-5 Stunden des Kugelmahlens auf.
- Die durchschnittliche Partikelgröße nimmt in diesem Zeitraum drastisch ab, von 160 μm auf 25 μm.
- Diese Phase ist gekennzeichnet durch den Zerfall größerer Partikel in kleinere Fragmente aufgrund starker mechanischer Kräfte.
-
Langsamere Reduktion nach 5 Stunden:
- Nach den ersten 5 Stunden verlangsamt sich die Geschwindigkeit der Partikelgrößenverringerung.
- Wird das Mahlen über diesen Zeitraum hinaus fortgesetzt, verringert sich die Partikelgröße immer noch, allerdings mit abnehmender Geschwindigkeit.
- Beispielsweise kann die Partikelgröße nach 10 Stunden Mahlen unter 10 μm fallen.
-
Die Bedeutung von Mahldauer und Kugelgröße:
- Um feinere Partikel zu erhalten, sind im Allgemeinen längere Mahlzeiten erforderlich.
- Kleinere Mahlkugeln sind bei der Herstellung kleinerer Partikel effektiver, da sie die Häufigkeit der Zusammenstöße und die Effizienz der Partikelzerkleinerung erhöhen.
- Die Kombination aus längeren Mahlzeiten und kleineren Kugeln verbessert den Mahlprozess.
-
Auswirkung von wiederholten Mahlzyklen:
- Die Erhöhung der Anzahl der Mahlzyklen führt zu einem höheren Anteil an kleineren Partikeln.
- Wiederholte Zyklen bewirken die Erosion größerer Partikel, was zur Bildung von Fragmenten in Nanogröße führt.
- Dieser Prozess ist besonders beim Kryomahlen zu beobachten, bei dem mit der Zeit kleinere Fragmente von größeren Partikeln abfallen.
-
Praktische Auswirkungen für Einkäufer von Geräten und Verbrauchsmaterialien:
- Für Käufer, die eine bestimmte Partikelgröße anstreben, ist das Verständnis des Verhältnisses zwischen Mahldauer und Partikelgröße entscheidend.
- Durch die Auswahl geeigneter Mahlgeräte mit einstellbaren Zeiteinstellungen und geeigneten Kugelgrößen kann der Mahlprozess optimiert werden.
- Längere Mahlzeiten und kleinere Kugeln können notwendig sein, um feinere Partikel zu erhalten, aber dies muss gegen den Energieverbrauch und die Betriebskosten abgewogen werden.
Durch sorgfältige Abwägung dieser Faktoren können Käufer fundierte Entscheidungen über die Ausrüstung und die Verbrauchsmaterialien treffen, die sie benötigen, um die gewünschte Partikelgröße zu erreichen.
Zusammenfassende Tabelle:
Mahldauer | Reduktion der Partikelgröße | Wichtige Einblicke |
---|---|---|
1-5 Stunden | 160 μm → 25 μm | Deutlichste Verringerung aufgrund starker mechanischer Kräfte. |
Mehr als 5 Stunden | Langsamere Reduktion | Die Partikelgröße fällt nach 10 Stunden unter 10 μm. |
Längeres Mahlen | Feinere Partikel | Kleinere Mahlkugeln erhöhen die Effizienz. |
Wiederholte Zyklen | Nanoskalige Fragmente | Die Erosion größerer Partikel führt zu einer Zunahme kleinerer Fragmente. |
Benötigen Sie Hilfe bei der Optimierung Ihres Kugelmahlprozesses? Kontaktieren Sie noch heute unsere Experten um Ihre gewünschte Partikelgröße zu erreichen!