Der Sputterdruck ist ein kritischer Parameter im Sputterprozess, der die Energieverteilung, die Richtung und die Abscheidungsqualität der gesputterten Partikel erheblich beeinflusst.Bei höherem Druck stoßen die gesputterten Ionen häufiger mit Gasatomen zusammen, was zu einer diffusiven Bewegung führt, die ihre Energie und Richtung mildert.Dies führt zu einem zufälligeren Abscheidungsmuster, was die Abdeckung verbessern kann, aber die kinetische Energie der Partikel verringern kann.Umgekehrt ermöglichen niedrigere Drücke mehr ballistische Stöße, bei denen die Teilchen eine höhere Energie und Richtwirkung behalten, was zu dichteren und gleichmäßigeren dünnen Schichten führt.Der Druck wirkt sich auch auf die Sputterrate aus, die von Faktoren wie der Sputterausbeute, der Ionenstromdichte und den Materialeigenschaften bestimmt wird.Das Verständnis und die Kontrolle des Sputterdrucks sind entscheidend für die Optimierung der Schichtqualität, der Abscheidungsrate und der Prozesseffizienz.
Die wichtigsten Punkte werden erklärt:
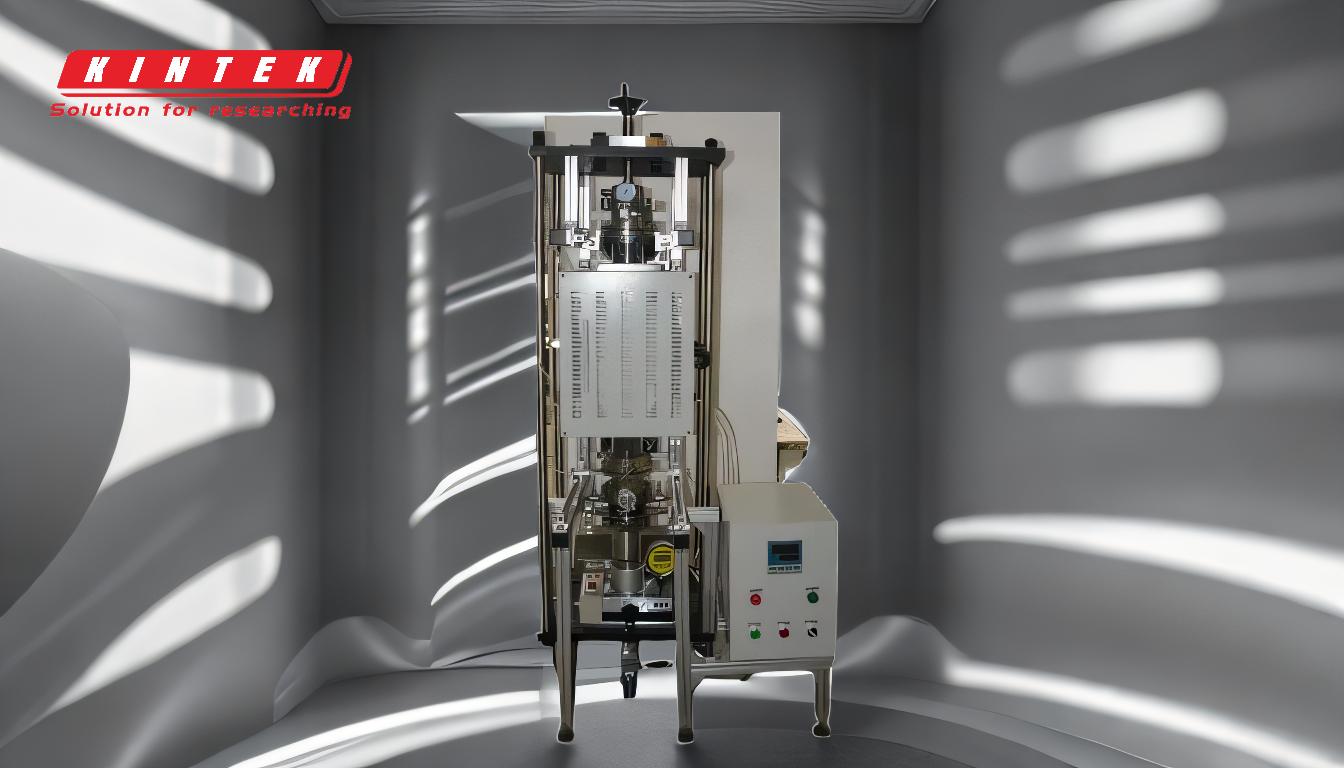
-
Auswirkungen auf Energie und Richtung der Partikel:
- Bei höherem Sputterdruck stoßen die gesputterten Ionen häufiger mit Gasatomen zusammen, was zu einer diffusen Bewegung führt.Dadurch wird ihre kinetische Energie gedämpft und ihre Richtung zufällig verändert, was zu einer gleichmäßigeren, aber weniger energiereichen Abscheidung führt.
- Bei niedrigerem Druck kommt es zu weniger Zusammenstößen zwischen den Partikeln, wodurch eine höhere kinetische Energie und eine stärkere gerichtete Bewegung erhalten bleiben, was zu dichteren und gleichmäßigeren dünnen Schichten führen kann.
-
Auswirkungen auf die Abscheidequalität:
- Höhere Drücke verbessern die Abdeckung, indem sie die Abscheidung gleichmäßiger über das Substrat verteilen, aber die geringere kinetische Energie der Partikel kann zu weniger dichten Schichten führen.
- Niedrigere Drücke begünstigen hochenergetische ballistische Stöße, die die Schichtdichte und Gleichmäßigkeit verbessern, aber die Bedeckung verringern können, wenn sie nicht richtig kontrolliert werden.
-
Einfluss auf die Sputtering-Rate:
- Die Sputterrate, definiert als die Anzahl der vom Target gesputterten Monoschichten pro Sekunde, wird durch den Druck beeinflusst, da er sich auf die Ionenstromdichte und die mittlere freie Weglänge der Teilchen auswirkt.
- Höhere Drücke können die Sputtering-Rate aufgrund erhöhter Kollisionen und Energieverluste verringern, während niedrigere Drücke die Rate erhöhen können, da sie direktere und energiereichere Stöße ermöglichen.
-
Rolle bei der Prozesskontrolle:
- Der Druck ist neben der Abscheidungstemperatur ein entscheidender Prozessparameter, der sorgfältig gesteuert werden muss, um die gewünschten Schichteigenschaften zu erzielen.
- Durch die Anpassung des Hintergrundgasdrucks kann der Prozess von hochenergetischen ballistischen Stößen bis hin zu niederenergetischen thermischen Bewegungen reichen, was eine flexible Anpassung der Filmeigenschaften ermöglicht.
-
Interaktion mit anderen Faktoren:
- Die Sputterausbeute, die von der Energie der einfallenden Ionen, der Masse der Ionen und der Zielatome sowie der Bindungsenergie der Atome im Festkörper abhängt, wird indirekt durch den Druck beeinflusst, da dieser sich auf die Ionenenergie und die Kollisionsfrequenz auswirkt.
- Die Art der Stromquelle (Gleichstrom oder Hochfrequenz) und die Materialeigenschaften stehen ebenfalls in Wechselwirkung mit dem Druck und bestimmen die Gesamteffizienz des Sputterprozesses und die Schichtqualität.
Wenn die Käufer von Anlagen und Verbrauchsmaterialien diese Schlüsselpunkte verstehen, können sie fundierte Entscheidungen über die Optimierung des Sputterdrucks treffen, um bestimmte Filmeigenschaften und Prozessziele zu erreichen.
Zusammenfassende Tabelle:
Aspekt | Hoher Druck | Niederdruck |
---|---|---|
Energie und Richtung der Teilchen | Mehr Zusammenstöße mit Gasatomen, geringere kinetische Energie, zufälliges Abscheidungsmuster. | Weniger Kollisionen, höhere kinetische Energie, gerichtete Bewegung für dichtere Schichten. |
Qualität der Abscheidung | Verbesserte Bedeckung, aber weniger dichte Schichten aufgrund der geringeren Partikelenergie. | Erhöhte Schichtdichte und Gleichmäßigkeit, aber die Bedeckung kann abnehmen. |
Sputtering-Rate | Reduzierte Rate aufgrund erhöhter Kollisionen und Energieverluste. | Erhöhte Rate bei direkteren und energiereicheren Stößen. |
Prozess-Steuerung | Einstellbar, um eine thermische Bewegung mit niedriger Energie für spezifische Filmeigenschaften zu erreichen. | Einstellbar zur Erzielung hochenergetischer ballistischer Stöße für maßgeschneiderte Eigenschaften. |
Benötigen Sie Hilfe bei der Optimierung des Sputterdrucks für Ihren Prozess? Kontaktieren Sie noch heute unsere Experten !