Der Sputterdruck ist ein kritischer Parameter im Sputterprozess, der die Energieverteilung der Quellatome, die Bewegung der gesputterten Ionen und die Gesamtqualität der abgeschiedenen Schicht beeinflusst. Der Druck in der Sputterkammer bestimmt, ob sich die Ionen ballistisch oder diffusiv bewegen, was sich auf die Abscheidungsrate, die Gleichmäßigkeit der Schicht und die Haftung auswirkt. In der Regel wird das Sputtern unter niedrigen bis mittleren Vakuumbedingungen durchgeführt, wobei der Druck zwischen 1 und 100 mTorr (Millitorr) liegt. Höhere Drücke führen zu mehr Kollisionen zwischen Ionen und Gasatomen, was zu einer diffusiven Bewegung und Stößen mit geringerer Energie führt, während niedrigere Drücke ballistische Stöße mit hoher Energie ermöglichen. Die Wahl des Drucks hängt von den gewünschten Filmeigenschaften, dem Targetmaterial und der Sputtertechnik ab.
Die wichtigsten Punkte erklärt:
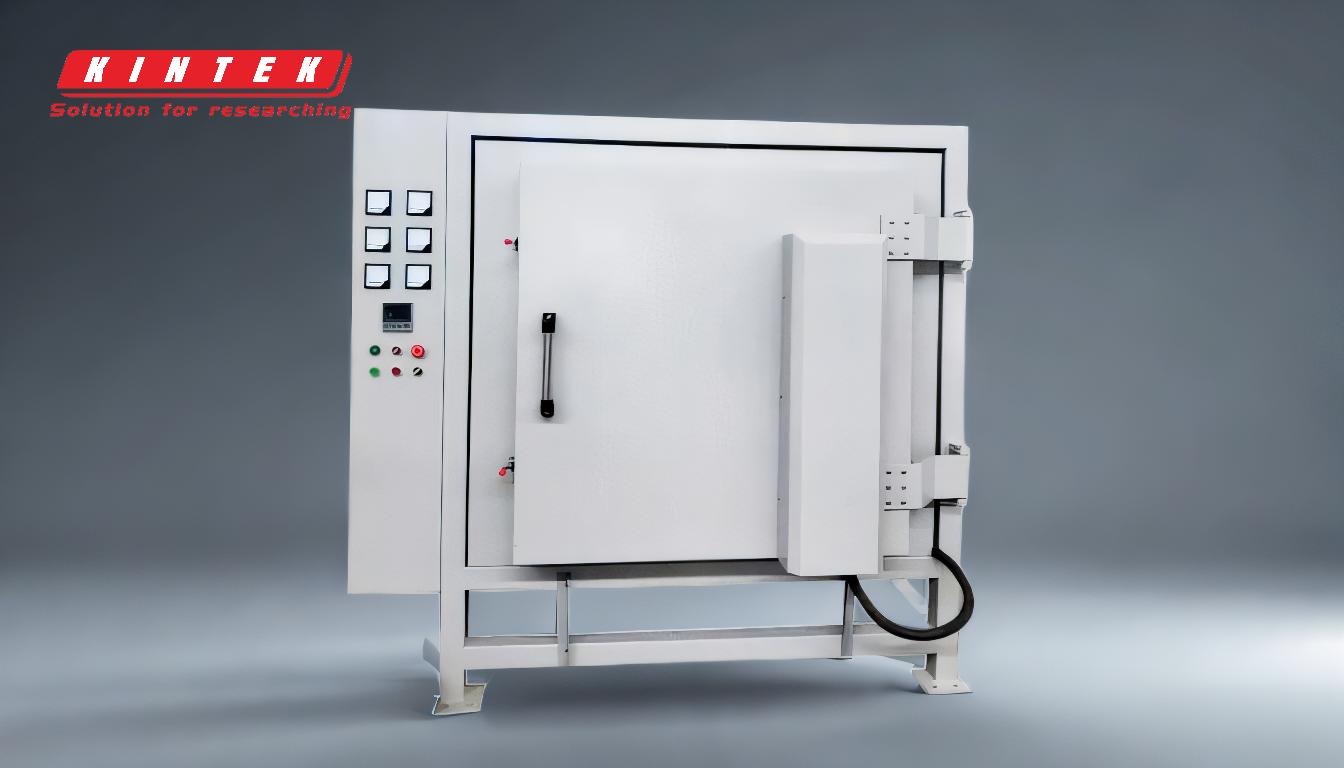
-
Definition des Sputterdrucks:
- Der Sputterdruck bezieht sich auf den Gasdruck in der Sputterkammer, der in der Regel auf niedrigem bis mittlerem Vakuumniveau gehalten wird (1 bis 100 mTorr).
- Dieser Druck ist entscheidend für die Kontrolle der Bewegung und Energie der gesputterten Ionen und Atome.
-
Die Rolle des Drucks beim Sputtern:
- Energieverteilung: Der Druck beeinflusst die mittlere freie Weglänge der Ionen und Atome und bestimmt ihre Energieverteilung beim Aufprall auf das Substrat.
- Ionenbewegung: Bei höherem Druck stoßen die Ionen häufiger mit den Gasatomen zusammen, was zu einer diffusen Bewegung und Aufschlägen mit geringerer Energie führt. Bei niedrigerem Druck bewegen sich die Ionen ballistisch, was zu energiereichen Stößen führt.
- Filmqualität: Der Druck wirkt sich auf die Gleichmäßigkeit, Haftung und Dichte des abgeschiedenen Films aus. Ein optimaler Druck sorgt für ein Gleichgewicht zwischen energiereichen Stößen für eine starke Haftung und einer kontrollierten Bewegung für eine gleichmäßige Abdeckung.
-
Druckbereiche und ihre Auswirkungen:
- Niederdruck (1-10 mTorr): Ermöglicht ballistische Schläge mit hoher Energie, geeignet für dichte und gut haftende Filme. Er kann jedoch zu einer weniger gleichmäßigen Abdeckung führen.
- Moderater Druck (10-100 mTorr): Fördert die Diffusionsbewegung und verbessert die Gleichmäßigkeit und Deckkraft des Films, kann aber aufgrund der geringeren Aufprallenergie die Haftfestigkeit verringern.
-
Faktoren, die die Druckauswahl beeinflussen:
- Zielmaterial: Verschiedene Materialien erfordern spezifische Drücke, um eine optimale Sputterausbeute und Filmeigenschaften zu erzielen.
- Sputtertechnik: Techniken wie DC-Sputtern oder RF-Sputtern können je nach Stromquelle und Materialkompatibilität unterschiedliche Druckanforderungen haben.
- Gewünschte Filmeigenschaften: Die Wahl des Drucks hängt davon ab, ob der Schwerpunkt auf der Haftung, der Gleichmäßigkeit oder der Dichte liegt.
-
Wechselwirkung mit anderen Parametern:
- Abscheidetemperatur: Druck und Temperatur wirken sich gemeinsam auf die kinetische Energie und die Oberflächenmobilität der abgeschiedenen Atome aus.
- Gasart: Die Art des im Sputterprozess verwendeten Gases (z. B. Argon) wirkt sich auf die Kollisionsdynamik und folglich auf den optimalen Druckbereich aus.
-
Praktische Überlegungen:
- Vakuum-System: Eine zuverlässige Vakuumpumpe ist unerlässlich, um den gewünschten Druck während des gesamten Sputterprozesses aufrechtzuerhalten.
- Prozesskontrolle: Die Überwachung und Anpassung des Drucks in Echtzeit kann dazu beitragen, eine gleichbleibende Schichtqualität und Abscheidungsrate zu erreichen.
Durch die Kenntnis und Optimierung des Sputterdrucks können die Hersteller den Prozess an die spezifischen Anforderungen der Schichten anpassen und so hochwertige Beschichtungen für verschiedene Anwendungen gewährleisten.
Zusammenfassende Tabelle:
Aspekt | Beschreibung |
---|---|
Definition | Gasdruck in der Zerstäubungskammer (1-100 mTorr). |
Rolle beim Sputtern | Steuert die Ionenbewegung, die Energieverteilung und die Schichtqualität. |
Niedriger Druck (1-10 mTorr) | Ballistische Stöße mit hoher Energie; dichte Schichten, aber weniger gleichmäßige Abdeckung. |
Moderater Druck (10-100 mTorr) | Diffusionsbewegung; verbesserte Gleichmäßigkeit, aber geringere Haftfestigkeit. |
Schlüsselfaktoren | Zielmaterial, Sputtertechnik, gewünschte Schichteigenschaften. |
Wechselwirkung mit Parametern | Abscheidetemperatur und Gasart beeinflussen den optimalen Druckbereich. |
Praktische Erwägungen | Erfordert zuverlässige Vakuumsysteme und Drucküberwachung in Echtzeit. |
Optimieren Sie Ihren Sputtering-Prozess noch heute - Kontaktieren Sie unsere Experten für maßgeschneiderte Lösungen!