Die Beschichtungsabscheidung ist ein hochentwickelter Prozess, bei dem dünne Materialschichten auf ein Substrat aufgetragen werden, um dessen Eigenschaften wie Haltbarkeit, Leitfähigkeit oder Aussehen zu verbessern. Der Prozess variiert je nach verwendeter Technik, beispielsweise Physical Vapour Deposition (PVD) oder Chemical Vapour Deposition (CVD). Im Allgemeinen geht es darum, das Substrat vorzubereiten, ein Vakuum oder eine kontrollierte Umgebung zu erzeugen, das Beschichtungsmaterial zu verdampfen und es auf das Substrat aufzutragen. Qualitätskontroll- und Endbearbeitungsschritte stellen sicher, dass die Beschichtung den gewünschten Spezifikationen entspricht. Jede Methode hat einzigartige Schritte und Überlegungen, aber die Kernprinzipien der Vorbereitung, Ablagerung und Validierung bleiben konsistent.
Wichtige Punkte erklärt:
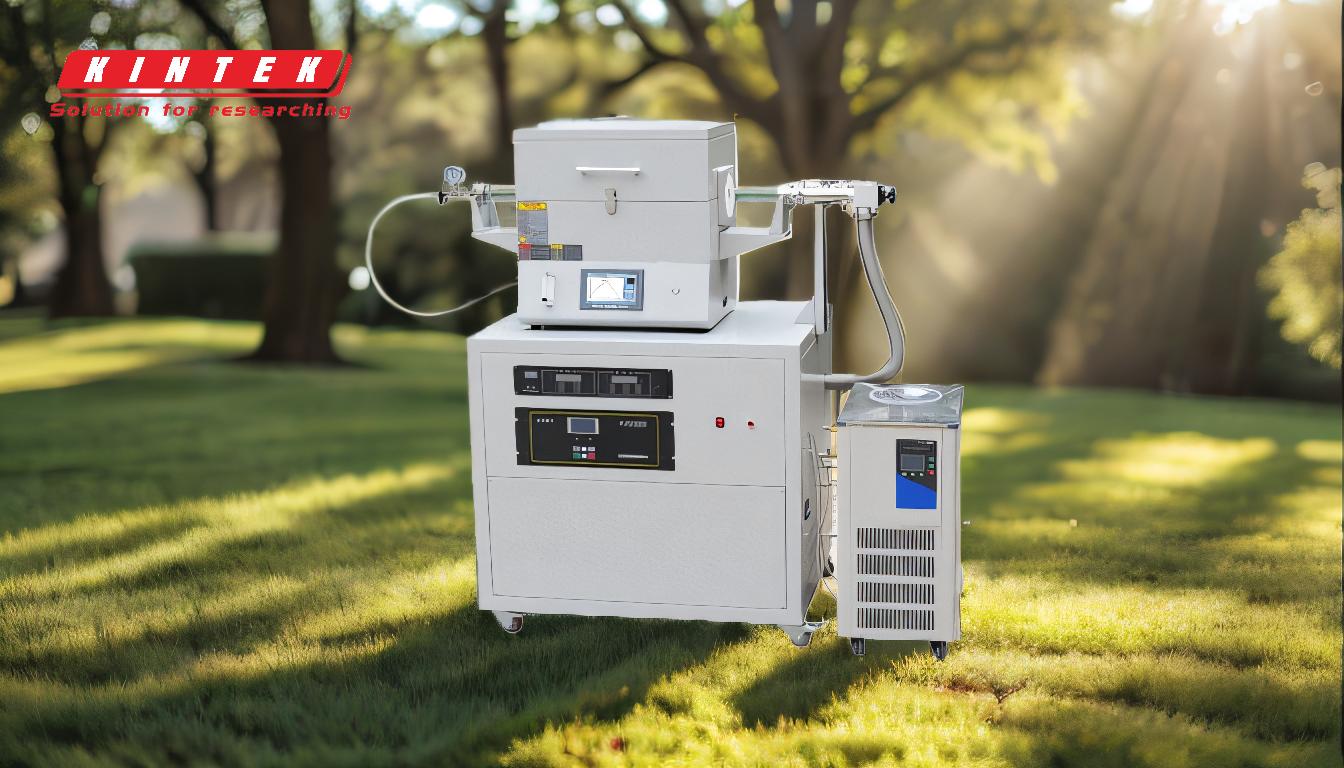
-
Vorbereitung des Untergrundes:
- Der Untergrund muss gründlich gereinigt werden, um Verunreinigungen wie Öle, Staub oder Oxide zu entfernen, die die Haftung beeinträchtigen könnten.
- Um den Verbund zwischen Beschichtung und Substrat zu verbessern, können Vorbehandlungsprozesse wie Ätzen oder das Aufbringen haftvermittelnder Schichten eingesetzt werden.
-
Erstellen einer kontrollierten Umgebung:
- Für PVD und CVD ist ein Vakuum oder eine kontrollierte Atmosphäre unerlässlich, um Kontaminationen zu verhindern und eine gleichmäßige Abscheidung sicherzustellen.
- Bei PVD wird eine Vakuumkammer zur Entfernung von Luft und Gasen verwendet, während CVD auf einer präzisen Steuerung von Gasfluss und -druck beruht.
-
Verdampfung des Beschichtungsmaterials:
- Beim PVD wird das Beschichtungsmaterial durch Methoden wie Sputtern (mit Ionen, um Atome von einem Target abzustoßen) oder Verdampfen (Erhitzen des Materials, bis es in Dampf übergeht) verdampft.
- Bei der CVD werden gasförmige Reaktanten in die Kammer eingeleitet, wo sie auf der Substratoberfläche unter Bildung der Beschichtung reagieren.
-
Ablagerung auf dem Substrat:
- Das verdampfte Material wird zum Substrat transportiert, wo es kondensiert und einen dünnen Film bildet.
- Gleichmäßigkeit ist entscheidend und Techniken wie das Drehen des Substrats oder die Verwendung von Überwachungsinstrumenten (z. B. Quarzkristall-Mikrowaage) sorgen für eine gleichmäßige Verteilung.
-
Reaktion und Filmbildung:
- Beim CVD entsteht durch die Reaktion zwischen Gasen und dem Substrat die gewünschte Beschichtung, häufig unter Einbeziehung eines Metallkatalysators, um den Prozess zu erleichtern.
- Bei PVD werden die Eigenschaften der Beschichtung, wie zum Beispiel Härte oder Farbe, während der Reaktionsphase bestimmt.
-
Kühlen und Belüften:
- Nach der Abscheidung wird das System abgekühlt, um die Beschichtung zu stabilisieren.
- Die Kammer wird entlüftet, um den atmosphärischen Druck wiederherzustellen, sodass das beschichtete Substrat entfernt werden kann.
-
Qualitätskontrolle und Prüfung:
- Jede Charge beschichteter Komponenten wird auf Konsistenz in Zusammensetzung, Dicke und Leistung getestet.
- Zur Überprüfung der Spezifikationen werden Werkzeuge wie Röntgenfluoreszenzgeräte (RFA) und Spektralfotometer eingesetzt.
-
Endbearbeitung und Nachbehandlung:
- Um die Eigenschaften oder das Erscheinungsbild der Beschichtung zu verbessern, können zusätzliche Schritte wie Glühen oder Polieren durchgeführt werden.
- Diese Schritte stellen sicher, dass das Endprodukt die erforderlichen Standards für die beabsichtigte Anwendung erfüllt.
-
Anwendungen und Variationen:
- PVD wird häufig für dekorative Beschichtungen, verschleißfeste Schichten und elektronische Komponenten verwendet.
- CVD ist ideal für die Herstellung hochreiner Filme wie Graphen oder Halbleitermaterialien.
- Beide Methoden können durch Anpassung von Parametern wie Temperatur, Druck und Materialauswahl an spezifische Anforderungen angepasst werden.
Durch das Verständnis dieser Schritte können Käufer von Geräten und Verbrauchsmaterialien die Eignung verschiedener Beschichtungsmethoden für ihre spezifischen Anwendungen besser beurteilen.
Übersichtstabelle:
Schritt | Beschreibung |
---|---|
1. Untergrundvorbereitung | Reinigen und vorbehandeln Sie den Untergrund, um Verunreinigungen zu entfernen und die Haftung zu verbessern. |
2. Kontrollierte Umgebung | Erstellen Sie ein Vakuum oder eine kontrollierte Atmosphäre, um eine gleichmäßige Abscheidung zu gewährleisten und Kontaminationen zu verhindern. |
3. Verdampfung | Verdampfen Sie das Beschichtungsmaterial mittels PVD (Sputtern/Verdampfen) oder CVD (Gasreaktionen). |
4. Hinterlegung | Transportieren und kondensieren Sie das verdampfte Material auf dem Substrat, um eine gleichmäßige Dünnfilmbildung zu erreichen. |
5. Reaktion und Filmbildung | Erleichtern Sie Reaktionen (CVD) oder bestimmen Sie Beschichtungseigenschaften (PVD) während des Prozesses. |
6. Kühlung und Belüftung | Kühlen Sie das System ab und entlüften Sie die Kammer, um die Beschichtung zu stabilisieren und das Substrat zu entfernen. |
7. Qualitätskontrolle | Testen Sie mithilfe fortschrittlicher Tools die Konsistenz in Zusammensetzung, Dicke und Leistung. |
8. Fertigstellung | Führen Sie Nachbehandlungen wie Glühen oder Polieren durch, um die Eigenschaften und das Erscheinungsbild zu verbessern. |
9. Bewerbungen | Maßgeschneiderte Verfahren (PVD/CVD) für dekorative, verschleißfeste oder hochreine Beschichtungen. |
Sind Sie bereit, Ihre Materialien mit fortschrittlicher Beschichtungsabscheidung zu verbessern? Kontaktieren Sie uns noch heute um die perfekte Lösung für Ihre Bedürfnisse zu finden!