Das Plasmasintern, insbesondere das Funkenplasmasintern (SPS), ist eine fortschrittliche Sintertechnik, die Plasmaaktivierung, Heißpressen und Widerstandserhitzung kombiniert, um eine schnelle Verdichtung von Werkstoffen zu erreichen.Bei diesem Verfahren wird ein gepulster Gleichstrom durch eine leitfähige Matrize und das Material geleitet, wodurch Joule-Wärme und Plasmaentladungen zwischen den Partikeln entstehen.Diese örtliche Erwärmung aktiviert und reinigt die Partikeloberflächen, was zu einer schnellen Bindung und Verdichtung bei niedrigeren Temperaturen im Vergleich zu herkömmlichen Sinterverfahren führt.Das Verfahren zeichnet sich dadurch aus, dass es in einem Bruchteil der Zeit, die herkömmliche Sinterverfahren benötigen, hochdichte Werkstoffe mit feinen Mikrostrukturen herstellen kann.
Die wichtigsten Punkte werden erklärt:
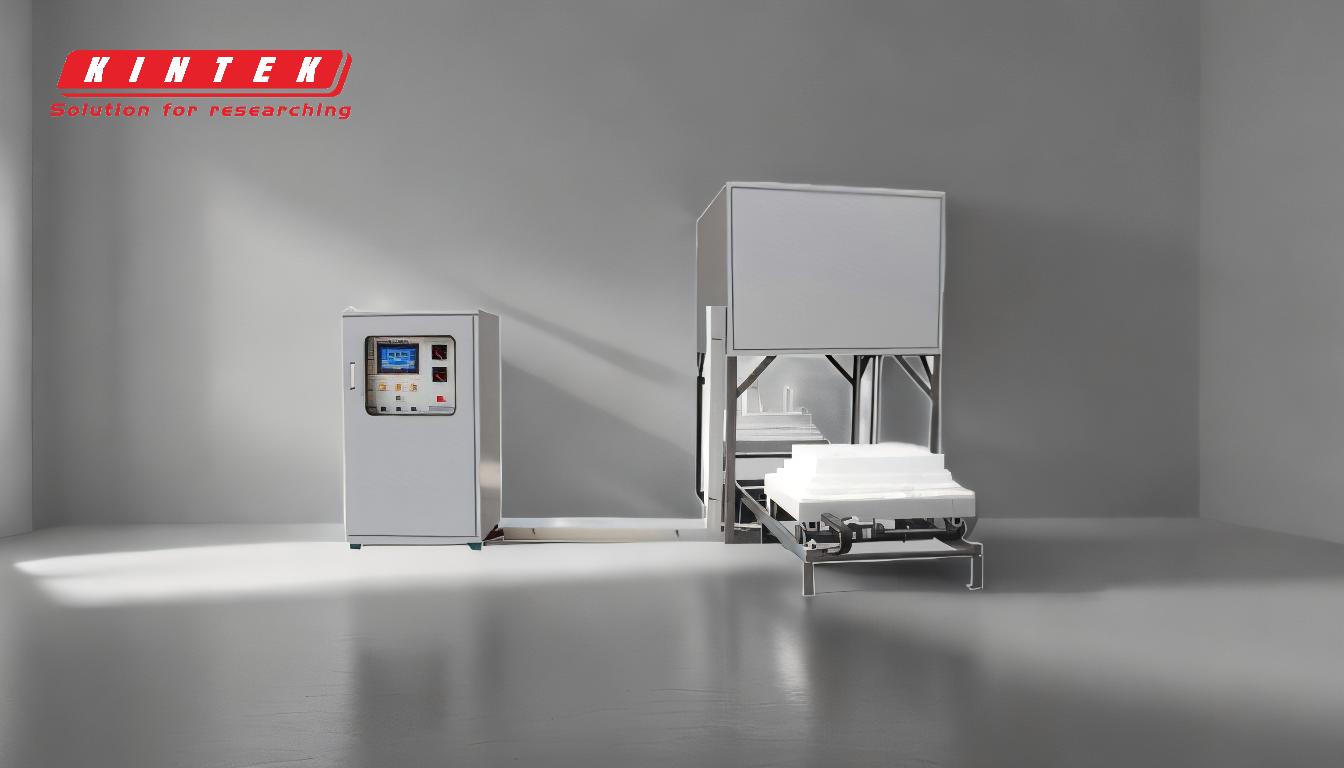
-
Integration von Plasma-Aktivierung, Heißpressen und Widerstandserwärmung:
- SPS kombiniert drei Schlüsselmechanismen: Plasmaaktivierung, Heißpressen und Widerstandserwärmung.Die Plasmaaktivierung erfolgt durch die Entladung zwischen den Pulverpartikeln, wodurch die Partikeloberflächen kurzzeitig auf mehrere tausend Grad Celsius erhitzt werden.Diese Erhitzung ist gleichmäßig verteilt und reinigt und aktiviert die Oberflächen durch Verdampfen von Verunreinigungen.
- Beim Heißpressen wird Druck auf den Pulverpressling ausgeübt, was zur Verdichtung durch plastische Verformung beiträgt.
- Die Widerstandserwärmung wird durch den Joule-Effekt erzeugt, bei dem der elektrische Strom, der durch das Material und die Matrize fließt, Wärme im Inneren und nach außen hin erzeugt.
-
Etappen des SPS-Prozesses:
- Zubereitung des Pulvers Compact:Das Material wird in Form eines Pulverpresslings vorbereitet, der durch Kaltschweißen, 3D-Druck oder Presswerkzeuge hergestellt werden kann.Der Pressling wird in einer kontrollierten Atmosphäre gelagert, um Gleichmäßigkeit zu gewährleisten.
- Erwärmung und Verfestigung:Das Material wird im Funkenplasmasinterofen bis knapp unter seinen Schmelzpunkt erhitzt. Funkenplasma-Sinterofen .In diesem Stadium werden die martensitischen kristallinen Gefüge aktiviert und die Partikelbindung eingeleitet.
- Partikelverschmelzung:Unter der kombinierten Wirkung von Hitze und Druck verdichten sich die Partikel und verschmelzen.Dieser Prozess kann durch Flüssigphasensintern (LPS) beschleunigt werden, bei dem sich an den Korngrenzen eine flüssige Phase bildet, die den Materialfluss und die Verdichtung fördert.
- Erstarrung:Nachdem die gewünschte Dichte erreicht ist, wird das Material abgekühlt und erstarrt zu einer einzigen, einheitlichen Masse mit feinkörnigem Gefüge.
-
Vorteile von SPS:
- Schnelles Heizen und Kühlen Tarife:SPS ermöglicht ein sehr schnelles Aufheizen und Abkühlen, wodurch die Gesamtverarbeitungszeit erheblich verkürzt wird.
- Niedrigere Sintertemperaturen:Bei diesem Verfahren erfolgt die Verdichtung bei Temperaturen, die mehrere hundert Grad niedriger sind als beim herkömmlichen Sintern, wobei die Mikrostruktur und die Eigenschaften des Materials erhalten bleiben.
- Verbesserte Materialeigenschaften:Der schnelle Sinterprozess führt zu Materialien mit hoher Dichte, feiner Korngröße und verbesserten mechanischen Eigenschaften.
-
Anwendungen von SPS:
- SPS ist bei der Herstellung von Hochleistungskeramiken, Metallen und Verbundwerkstoffen weit verbreitet.Es ist besonders vorteilhaft für Werkstoffe, die mit herkömmlichen Methoden nur schwer zu sintern sind, wie z. B. nanostrukturierte Werkstoffe, funktional abgestufte Werkstoffe und Werkstoffe mit hohen Schmelzpunkten.
-
Vergleich mit anderen Sintertechniken:
- Im Gegensatz zu herkömmlichen Sinterverfahren, die ausschließlich auf thermischer Energie beruhen, wird bei SPS die Verdichtung durch elektrische Entladung und Druck erreicht.Dies führt zu einem effizienteren Prozess mit besserer Kontrolle über die Mikrostruktur des Materials.
- Im Vergleich zum Heißpressen bietet SPS schnellere Heizraten und niedrigere Sintertemperaturen, was es zu einem energie- und kosteneffizienteren Verfahren macht.
-
Mechanismen von SPS:
- Entladungsplasma:Das bei der SPS erzeugte Plasma ist ein stark ionisiertes Gas mit Temperaturen zwischen 4000 und 10999°C.Dieses Plasma ist hochgradig aktiviert und fördert schnelle Oberflächenreaktionen und Bindungen zwischen Partikeln.
- Joule-Erwärmung:Der elektrische Strom, der durch das Material und die Matrize fließt, erzeugt im Inneren Wärme und sorgt für eine gleichmäßige Erwärmung der gesamten Probe.
- Druck Anwendung:Der angewandte Druck unterstützt die Umlagerung der Partikel und die plastische Verformung, was die Verdichtung fördert.
Zusammenfassend lässt sich sagen, dass das Funkenplasmasintern ein hocheffizientes und vielseitiges Sinterverfahren ist, das die Plasmaaktivierung, die Widerstandserhitzung und den Druck nutzt, um eine schnelle Verdichtung von Materialien zu erreichen.Seine Fähigkeit, bei niedrigeren Temperaturen und kürzeren Verarbeitungszeiten zu arbeiten, macht es zu einer attraktiven Option für die Herstellung moderner Werkstoffe mit hervorragenden Eigenschaften.
Zusammenfassende Tabelle:
Aspekt | Einzelheiten |
---|---|
Schlüsselmechanismen | Plasmaaktivierung, Heißpressen und Widerstandserwärmung |
Prozess-Stufen | Aufbereitung, Erwärmung und Verfestigung, Partikelverschmelzung, Erstarrung |
Vorteile | Schnelle Erwärmung/Abkühlung, niedrigere Sintertemperaturen, verbesserte Eigenschaften |
Anwendungen | Hochleistungskeramiken, Metalle, Verbundwerkstoffe, nanostrukturierte Materialien |
Vergleich | Effizienter als traditionelles Sintern, schneller als Heißpressen |
Mechanismen | Entladungsplasma, Joule-Erwärmung, Druckanwendung |
Sind Sie bereit, die Vorteile des Spark-Plasma-Sinterns für Ihre Materialien zu erkunden? Kontaktieren Sie uns noch heute um mehr zu erfahren!