Vakuumaufkohlung, auch Niederdruckaufkohlung (LPC) genannt, ist ein Wärmebehandlungsprozess, der die Oberflächenhärte von Stahl- oder Legierungskomponenten erhöht, indem Kohlenstoff in ihre Oberflächenschichten eingebracht wird. Dieser Prozess wird in einem Vakuumofen durchgeführt, in dem das Metall auf hohe Temperaturen erhitzt wird (typischerweise zwischen 1.600 und 1.950 °F oder 870 und 1.070 °C). Ein kohlenstoffreiches Gas wie Propan oder Acetylen wird in den Ofen eingeleitet, wo es durch die Hitze in Kohlenstoff und Wasserstoff zerfällt. Der Kohlenstoff diffundiert dann in die Metalloberfläche und erhöht so dessen Härte. Der Prozess umfasst abwechselnde Zyklen der Gaseinleitung und -diffusion, gefolgt von einem Abschrecken in Öl oder Hochdruckgas (HPGQ), um die gewünschte Härte und Härtetiefe zu erreichen. Diese Methode ist streng kontrolliert und gewährleistet eine gleichmäßige Kohlenstoffdurchdringung ohne Oberflächenverunreinigung.
Wichtige Punkte erklärt:
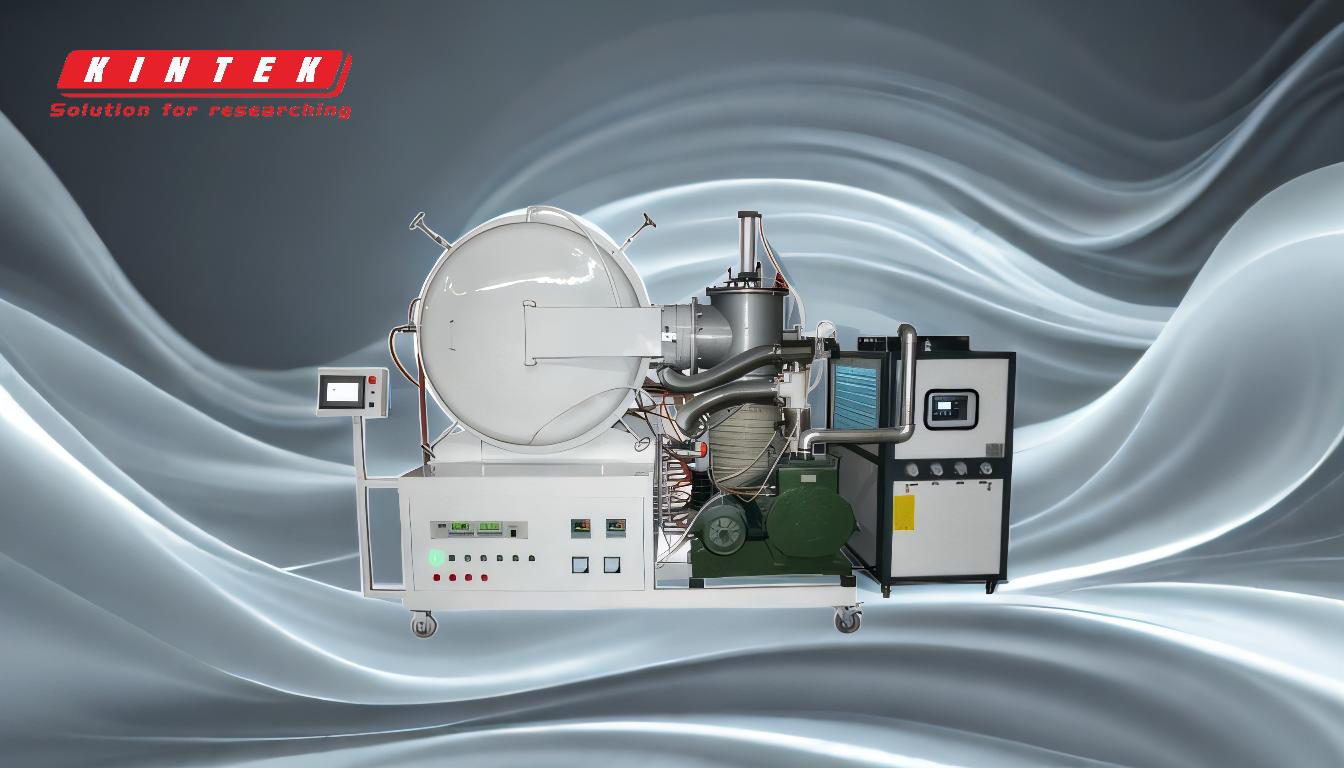
-
Einführung in das Vakuumaufkohlen
- Vakuumaufkohlen ist ein Wärmebehandlungsverfahren, mit dem die Oberflächenhärte von Stahl- oder Legierungskomponenten durch Einbringen von Kohlenstoff in ihre Oberflächenschichten erhöht wird.
- Es wird auch als Niederdruckaufkohlung (LPC) bezeichnet und in einem Vakuumofen durchgeführt, um äußere Verunreinigungen zu entfernen und eine reine Aufkohlungsumgebung sicherzustellen.
-
Prozessübersicht
- Bei diesem Verfahren wird das Metall in einen Vakuumofen gegeben, auf eine bestimmte Temperatur erhitzt, ein kohlenstoffreiches Gas eingeleitet und der Kohlenstoff in die Metalloberfläche diffundiert.
-
Die Schritte umfassen:
- Laden des Metalls in den Vakuumofen.
- Erhitzen des Metalls auf die erforderliche Temperatur (normalerweise 1.600–1.950 °F oder 870–1.070 °C).
- Einleiten eines kohlenstoffreichen Gases (z. B. Propan oder Acetylen) in den Ofen.
- Aufgrund der hohen Temperatur zerfällt das Gas in Kohlenstoff und Wasserstoff.
- Dadurch kann der Kohlenstoff in die Metalloberfläche diffundieren.
- Abschrecken des Metalls, um die gewünschte Härte zu erreichen.
-
Kohlenstoffquelle und Gasaufschlüsselung
- Das kohlenstoffreiche Gas (z. B. Propan oder Acetylen) wird als Partialdruck in den Ofen eingeleitet.
- Bei hohen Temperaturen zerfällt das Gas in seine Bestandteile: Kohlenstoff und Wasserstoff.
- Die Kohlenstoffatome diffundieren in die Metalloberfläche, während der Wasserstoff aus dem Ofen evakuiert wird.
-
Diffusion und Einsatzhärtung
- Der Kohlenstoffdiffusionsprozess wird in Zyklen mit unterschiedlicher Dauer der Gaszufuhr und Diffusionszeit wiederholt, um die gewünschte Einsatztiefe und Härte zu erreichen.
- Der Prozess gewährleistet eine gleichmäßige Kohlenstoffdurchdringung, was zu einer gehärteten Oberflächenschicht (Hülle) führt und gleichzeitig die Kerneigenschaften des Metalls beibehält.
-
Abschrecken
- Nach dem Aufkohlungsprozess wird das Metall abgeschreckt, um die Härte zu fixieren.
- Das Abschrecken kann mit Öl oder Hochdruckgas (HPGQ) erfolgen, wobei für schnellere Abkühlraten üblicherweise Stickstoff oder Helium verwendet werden.
- Die Abschreckmethode hängt vom Material und den gewünschten mechanischen Eigenschaften ab.
-
Vorteile des Vakuumaufkohlens
- Reinheit: Die Vakuumumgebung beseitigt Oberflächenverunreinigungen und sorgt für einen sauberen, kontrollierten Prozess.
- Gleichmäßigkeit: Der Prozess sorgt für eine gleichmäßige Kohlenstoffdurchdringung und Härtetiefe.
- Effizienz: Der Einsatz von Hochdruck-Gasabschreckung verkürzt die Zykluszeiten und verbessert die Produktivität.
- Vorteile für die Umwelt: Das Verfahren erzeugt im Vergleich zu herkömmlichen Gasaufkohlungsmethoden weniger Emissionen.
-
Anwendungen
- Die Vakuumaufkohlung wird häufig in Branchen eingesetzt, die Hochleistungskomponenten erfordern, beispielsweise in der Automobil-, Luft- und Raumfahrtindustrie sowie im Werkzeugbau.
- Zu den üblichen Anwendungen gehören Zahnräder, Wellen, Lager und andere Teile, die eine hohe Oberflächenhärte und Verschleißfestigkeit erfordern.
Durch die Befolgung dieses strukturierten Prozesses gewährleistet das Vakuumaufkohlen eine präzise Kontrolle über die Härtung von Metallkomponenten und macht es zu einer bevorzugten Methode zur Herstellung hochwertiger, langlebiger Teile.
Übersichtstabelle:
Aspekt | Einzelheiten |
---|---|
Prozessname | Vakuumaufkohlung (Niederdruckaufkohlung) |
Temperaturbereich | 870–1.070 °C (1.600–1.950 °F) |
Kohlenstoffquelle | Propan oder Acetylen |
Wichtige Schritte | Erhitzen, Gaseinleitung, Kohlenstoffdiffusion, Abschrecken |
Abschreckmethoden | Öl oder Hochdruckgas (HPGQ) |
Vorteile | Reinheit, Einheitlichkeit, Effizienz, Vorteile für die Umwelt |
Anwendungen | Automobil, Luft- und Raumfahrt, Werkzeugbau (Zahnräder, Wellen, Lager usw.) |
Entdecken Sie, wie Vakuumaufkohlung Ihre Metallkomponenten verbessern kann – Kontaktieren Sie uns noch heute für kompetente Beratung!