Das Sputtering-Verfahren ist eine weit verbreitete Methode zur Abscheidung dünner Schichten auf Substraten, die häufig in Branchen wie der Halbleiterherstellung, der Präzisionsoptik und der Oberflächenbearbeitung eingesetzt wird. Dabei wird durch die Ionisierung eines Inertgases, in der Regel Argon, in einer Vakuumkammer ein Plasma erzeugt. Positiv geladene Ionen aus dem Plasma werden auf ein negativ geladenes Zielmaterial beschleunigt, wodurch Atome oder Moleküle von der Oberfläche des Ziels ausgestoßen werden. Diese ausgestoßenen Teilchen wandern dann durch die Kammer und lagern sich auf einem Substrat ab, wobei sie einen dünnen, gleichmäßigen und haftenden Film bilden. Das Verfahren erfordert eine genaue Kontrolle der Vakuumbedingungen, des Gasdrucks und der Energieübertragung, um hochwertige Beschichtungen zu gewährleisten.
Die wichtigsten Punkte erklärt:
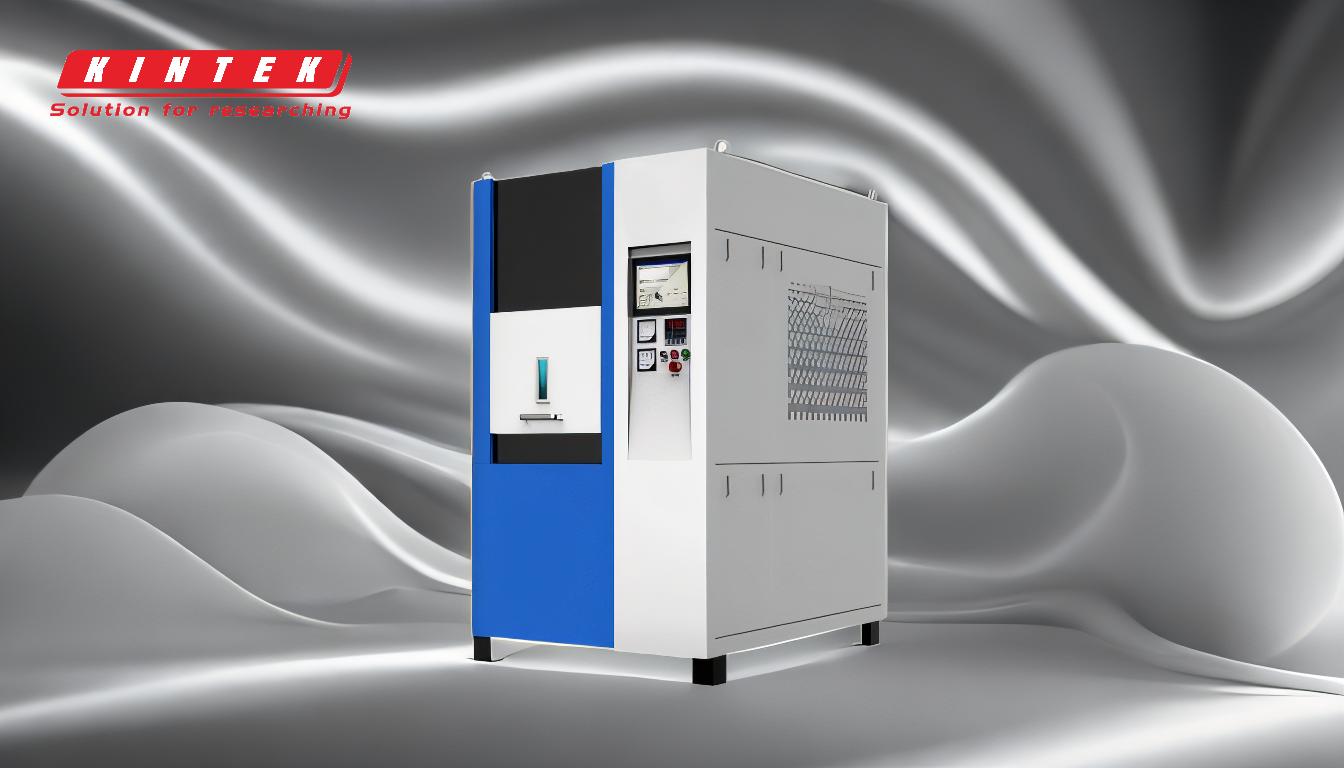
-
Inertgas-Ionisierung:
- Das Sputtering-Verfahren beginnt mit der Einleitung eines Inertgases, z. B. Argon, in eine Vakuumkammer. Das Gas wird mit Hilfe einer Hochspannung oder einer elektromagnetischen Anregung ionisiert, wodurch ein Plasma aus positiv geladenen Ionen (z. B. Ar+) entsteht.
- Die Wahl des Gases hängt vom Zielmaterial ab. Für leichte Elemente wird Neon bevorzugt, während für schwerere Targets schwerere Elemente wie Krypton oder Xenon verwendet werden, um einen effizienten Impulstransfer zu gewährleisten.
-
Vakuumumgebung:
- Das Verfahren wird unter Vakuumbedingungen durchgeführt, um Verunreinigungen zu beseitigen und eine saubere Abscheidungsumgebung zu gewährleisten. Der Druck in der Kammer wird in der Regel auf etwa 1 Pa (0,0000145 psi) reduziert, bevor das Sputtergas eingeleitet wird.
- Anfänglich werden niedrigere Drücke aufrechterhalten, um Feuchtigkeit und Verunreinigungen zu entfernen, und anschließend höhere Drücke (10^-1 bis 10^-3 mbar) für den eigentlichen Sputterprozess.
-
Energieübertragung und Ausstoß von Target-Atomen:
- Positiv geladene Ionen aus dem Plasma werden durch eine angelegte Hochspannung (3-5 kV) auf das negativ geladene Targetmaterial (Kathode) beschleunigt.
- Beim Aufprall übertragen die Ionen ihre kinetische Energie auf die Zielatome, so dass diese von der Oberfläche abgestoßen werden. Bei den ausgestoßenen Teilchen handelt es sich um neutrale Atome, Cluster oder Moleküle.
-
Abscheidung von Dünnschichten:
- Die ausgestoßenen Zielatome bewegen sich in geraden Linien durch die Vakuumkammer und lagern sich auf dem Substrat ab, wobei sie einen dünnen Film bilden.
- Der resultierende Film zeichnet sich durch hervorragende Gleichmäßigkeit, Dichte und Haftung aus und eignet sich daher für verschiedene Anwendungen.
-
Magnetischer Feldeinschluss:
- Ein Magnetfeld wird häufig eingesetzt, um das Plasma um das Target herum einzuschließen und so die Effizienz des Ionenbeschusses zu erhöhen und einen kontrollierteren Abscheidungsprozess zu gewährleisten.
- Dieses Magnetfeld wird durch die Platzierung eines Elektromagneten in der Nähe des Targets erzeugt, was ebenfalls zur Aufrechterhaltung eines stabilen Plasmas beiträgt.
-
Temperaturkontrolle:
- Die Kammer kann auf Temperaturen von 150°C bis 750°C (302°F bis 1382°F) aufgeheizt werden, je nach dem abzuscheidenden Material. Dieser Heizschritt verbessert die Qualität und die Haftung der dünnen Schicht.
-
Anwendungen des Sputterns:
- Sputtern ist in Branchen wie der Halbleiterindustrie, der Präzisionsoptik und der Oberflächenveredelung weit verbreitet, da es die Herstellung hochwertiger Dünnschichten mit präziser Kontrolle über Dicke und Zusammensetzung ermöglicht.
Durch die Befolgung dieser Schritte erreicht das Sputtern eine hochgradig kontrollierte und effiziente Methode für die Abscheidung dünner Schichten, was es in der modernen Fertigung und Materialwissenschaft unentbehrlich macht.
Zusammenfassende Tabelle:
Hauptaspekt | Einzelheiten |
---|---|
Inertgas-Ionisierung | Argon oder andere Inertgase werden ionisiert, um ein Plasma für das Sputtern zu erzeugen. |
Vakuum-Umgebung | Der Kammerdruck wird auf ~1 Pa reduziert, um eine saubere, verunreinigungsfreie Abscheidung zu gewährleisten. |
Energieübertragung | Ionen werden auf 3-5 kV beschleunigt, um Zielatome für die Dünnschichtbildung auszustoßen. |
Magnetische Feldeinschränkung | Verbessert die Plasmakontrolle und die Effizienz des Ionenbeschusses. |
Temperaturkontrolle | Die Kammer wird auf 150°C bis 750°C beheizt, um die Schichtqualität und die Haftung zu verbessern. |
Anwendungen | Einsatz in der Halbleiter-, Präzisionsoptik- und Oberflächenbearbeitungsindustrie. |
Entdecken Sie, wie Sputtern Ihren Fertigungsprozess verbessern kann. Kontaktieren Sie unsere Experten noch heute !