Bei der Regeneration von Aktivkohle wird das Material in der Regel auf etwa 538 °C (1000 °F) erhitzt, um 75-90 % der adsorbierten Verunreinigungen zu verflüchtigen.Anschließend wird Dampf eingeleitet, um die verbleibenden flüchtigen Bestandteile zu entfernen und die Kohle vollständig zu reaktivieren, so dass ihre Adsorptionskapazität für die Wiederverwendung wiederhergestellt wird.Dieses Verfahren stellt sicher, dass die Kohle nahezu vollständig wiederhergestellt wird, was es zu einer effizienten und nachhaltigen Methode für das Recycling von Aktivkohle in verschiedenen industriellen Anwendungen macht.
Die wichtigsten Punkte erklärt:
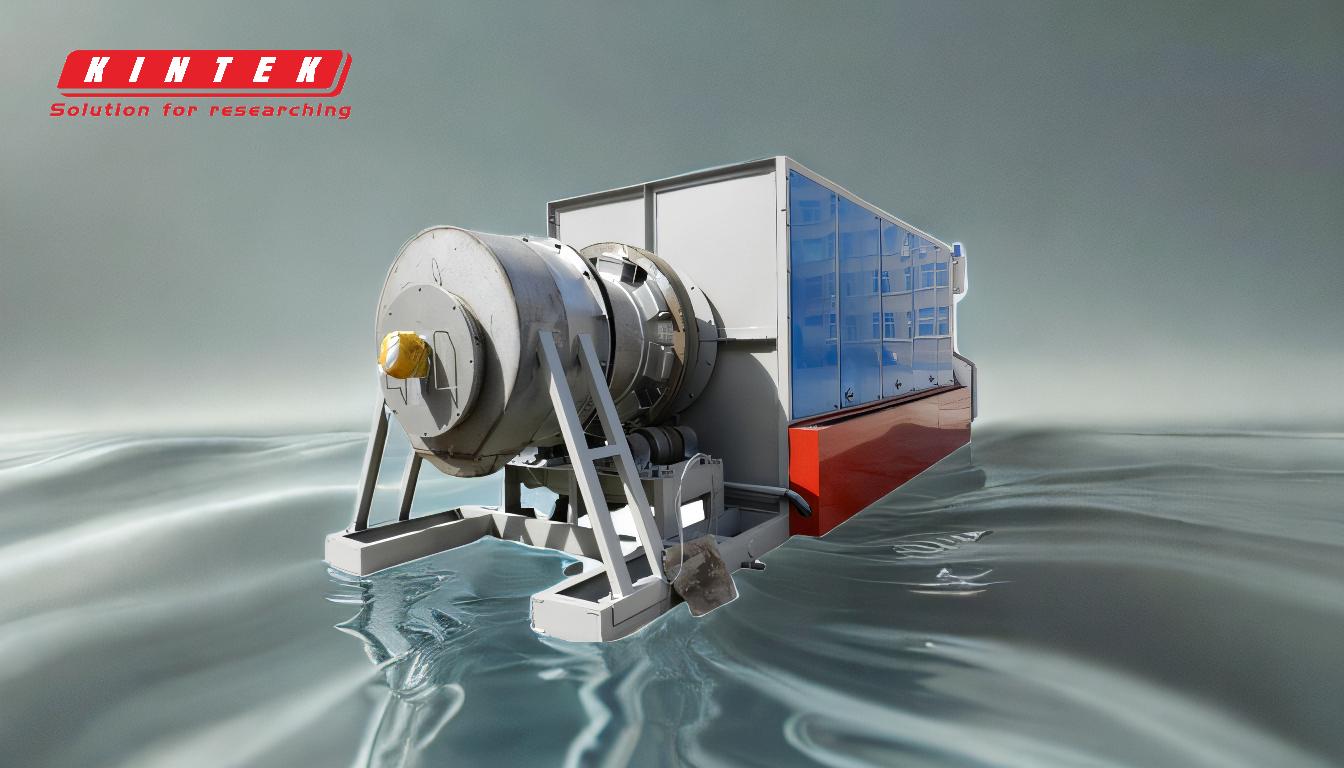
-
Regenerations-Temperatur:
- Der Regenerationsprozess für Aktivkohle beinhaltet das Erhitzen des Materials auf etwa 1000°F (538°C) .Diese hohe Temperatur ist notwendig, um den Großteil der adsorbierten Schadstoffe zu verflüchtigen, die in der Regel zwischen 75-90% der gesamten adsorbierten Stoffe.Bei dieser Temperatur zersetzen sich die auf der Kohlenstoffoberfläche adsorbierten organischen Verbindungen oder verdampfen, wodurch die Kohle für die weitere Behandlung vorbereitet wird.
-
Die Rolle von Dampf bei der Regeneration:
-
Nach dem Erhitzen,
wird Dampf in das
in das System eingespeist.Der Dampf dient in erster Linie zwei Zwecken:
- Er hilft die restlichen flüchtigen Bestandteile zu entfernen die während der Erhitzungsphase nicht vollständig entfernt wurden.
- Es reaktiviert die Kohle indem sie ihre Poren öffnet und ihre Adsorptionsfähigkeit wiederherstellt.Durch diesen Schritt wird sichergestellt, dass die Kohle nahezu vollständig in ihren ursprünglichen Zustand zurückversetzt wird und wiederverwendet werden kann.
-
Nach dem Erhitzen,
wird Dampf in das
in das System eingespeist.Der Dampf dient in erster Linie zwei Zwecken:
-
Effizienz des Prozesses:
- Die Kombination aus Hochtemperaturerwärmung und Dampfbehandlung führt zu einer nahezu vollständigen Wiederherstellung der Aktivkohle.Dies macht den Regenerationsprozess äußerst effizient und kostengünstig, da die Kohle ohne nennenswerten Leistungsverlust mehrfach wiederverwendet werden kann.
-
Nachhaltigkeit und Kosteneffizienz:
- Die Regenerierung von Aktivkohle ist eine nachhaltige Praxis die den Abfall reduziert und die Notwendigkeit des häufigen Austauschs von frischer Kohle minimiert.Dies senkt nicht nur die Betriebskosten, sondern trägt auch zu den Umweltzielen bei, indem es den mit der Herstellung und Entsorgung von Aktivkohle verbundenen Kohlenstoff-Fußabdruck verringert.
-
Anwendungen von Regeneratkohle:
-
Regenerierte Aktivkohle kann in einer Vielzahl von Anwendungen wiederverwendet werden, z. B:
- Wasseraufbereitung
- Luftfiltration
- Behandlung von Industriegasen
- Chemische Rückgewinnungsverfahren
- Ihre wiederhergestellte Adsorptionskapazität gewährleistet, dass sie diese Aufgaben effektiv erfüllt, was sie zu einem vielseitigen und wertvollen Material in zahlreichen Branchen macht.
-
Regenerierte Aktivkohle kann in einer Vielzahl von Anwendungen wiederverwendet werden, z. B:
Durch diesen strukturierten Regenerationsprozess kann Aktivkohle effizient recycelt werden, was sowohl wirtschaftliche als auch ökologische Vorteile mit sich bringt.
Zusammenfassende Tabelle:
Hauptaspekt | Einzelheiten |
---|---|
Regenerations-Temperatur | 1000°F (538°C), um 75-90% der Verunreinigungen zu verflüchtigen |
Die Rolle von Dampf | Entfernt verbleibende flüchtige Bestandteile und reaktiviert die Kohlenstoffporen |
Wirkungsgrad | Nahezu vollständige Wiederherstellung, die mehrere Wiederverwendungszyklen ermöglicht |
Nachhaltigkeit | Reduziert Abfall, senkt Kosten und minimiert die Umweltbelastung |
Anwendungen | Wasseraufbereitung, Luftfiltration, industrielle Gasbehandlung und mehr |
Entdecken Sie, wie die Regeneration von Aktivkohle Ihren Betrieb unterstützen kann. Kontaktieren Sie unsere Experten noch heute !