Der Temperaturbereich für die Pyrolyse variiert je nach Art des durchgeführten Pyrolyseprozesses.Im Allgemeinen kann die Pyrolyse bei Temperaturen zwischen 350°C und 1200°C stattfinden, je nach spezifischer Anwendung und gewünschter Leistung.So findet die Hochtemperaturpyrolyse in der Regel bei 350-400°C statt, die Mitteltemperaturpyrolyse bei 600-700°C, und Prozesse, die flüssige und gasförmige Stoffe einbeziehen, können Temperaturen zwischen 700-1200°C erreichen.Diese Temperaturbereiche sind entscheidend für die Aufspaltung von Abfallstoffen in wertvolle Produkte wie Pyrolyseöl, Ruß und Synthesegas.
Die wichtigsten Punkte erklärt:
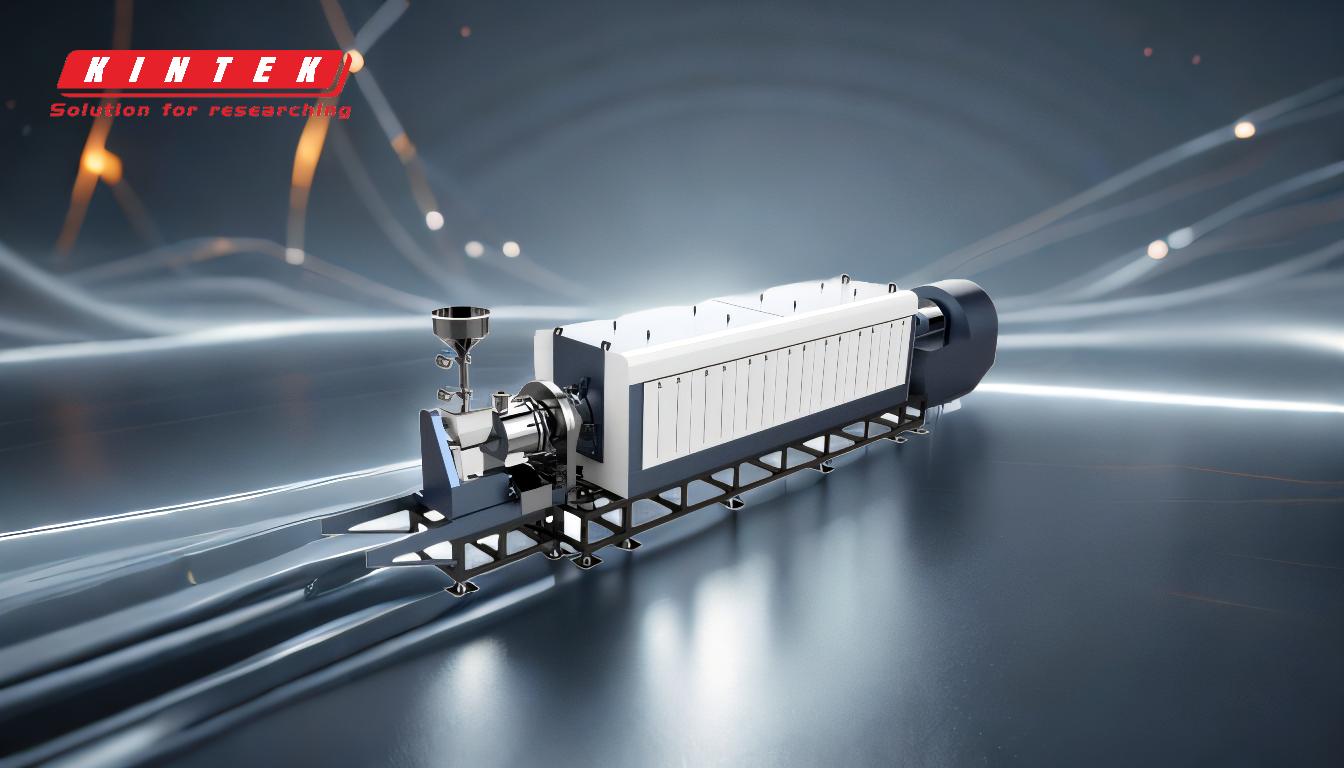
-
Hochtemperatur-Pyrolyse (350-400°C):
- Dieser Temperaturbereich ist für den Hochtemperatur-Pyrolyseprozess erforderlich.
- Er führt zur Aufspaltung von Abfallstoffen in wertvolle Produkte wie Pyrolyseöl, Ruß und Synthesegas.
- Dieser Bereich wird in der Regel verwendet, wenn das Ziel darin besteht, die Produktion von Gasen und Ölen zu maximieren.
-
Pyrolyse bei mittlerer Temperatur (600-700°C):
- Die Pyrolyse bei mittleren Temperaturen findet im Allgemeinen zwischen 600 und 700 °C statt.
- Dieser Bereich wird häufig für Verfahren verwendet, die ein Gleichgewicht zwischen gasförmigen, flüssigen und festen Produkten erfordern.
- Er eignet sich für Anwendungen, bei denen eine moderate Temperatur ausreicht, um das Ausgangsmaterial ohne übermäßigen Energieverbrauch aufzuspalten.
-
Hochtemperatur-Pyrolyse für flüssige und gasförmige Stoffe (700-1200°C):
- Pyrolyseprozesse, an denen flüssige und gasförmige Stoffe beteiligt sind, werden in der Regel bei Temperaturen zwischen 700 und 1200 °C durchgeführt.
- Diese hohen Temperaturen sind für die vollständige Zerlegung komplexer Moleküle in einfachere gasförmige und flüssige Produkte erforderlich.
- Das Verfahren wird häufig in extern beheizten Reaktorrohren durchgeführt, die aus feuerfesten Legierungen bestehen, um den hohen Temperaturen standzuhalten.
-
Langsame Pyrolyse:
- Die langsame Pyrolyse wird in einer sauerstoffarmen oder sauerstofffreien Umgebung durchgeführt.
- Typische Heizraten liegen zwischen 1 und 30 °C min-1.
- Das Verfahren wird in der Regel bei Atmosphärendruck durchgeführt, und die Prozesswärme wird in der Regel von einer externen Energiequelle zugeführt, z. B. durch die Verbrennung der erzeugten Gase oder die teilweise Verbrennung des Biomasse-Rohstoffs.
- Diese Methode wird häufig eingesetzt, um die Produktion von Biokohle, einem festen, kohlenstoffreichen Rückstand, zu maximieren.
-
Überlegungen zum Druck:
- Pyrolyseprozesse, an denen flüssige und gasförmige Stoffe beteiligt sind, werden in der Regel bei Drücken zwischen 1-30 bar durchgeführt.
- Der Druck kann die Ausbeute und die Zusammensetzung der Pyrolyseprodukte beeinflussen.
- Höhere Drücke können zu einer verstärkten Produktion von flüssigen Produkten führen, während niedrigere Drücke die Bildung von Gasen begünstigen.
-
Konstruktion des Reaktors:
- Die Konstruktion des Pyrolysereaktors ist entscheidend für die Einhaltung der gewünschten Temperatur- und Druckbedingungen.
- Reaktoren werden häufig aus feuerfesten Legierungen hergestellt, um hohen Temperaturen und korrosiven Umgebungen zu widerstehen.
- Die Länge und der Durchmesser der Reaktorrohre (20-30 Meter lang und 1-2 Zoll im Durchmesser) werden optimiert, um eine effiziente Wärmeübertragung und Produktausbeute zu gewährleisten.
Die Kenntnis dieser Temperaturbereiche und ihrer Auswirkungen ist für die Auswahl des geeigneten Pyrolyseverfahrens auf der Grundlage der gewünschten Produkte und der Eigenschaften des Ausgangsmaterials unerlässlich.
Zusammenfassende Tabelle:
Pyrolyse-Typ | Temperaturbereich | Wichtige Produkte | Anwendungen |
---|---|---|---|
Hochtemperatur-Pyrolyse | 350-400°C | Pyrolyseöl, Ruß, Syn-Gas | Maximiert die Gas- und Ölproduktion |
Pyrolyse bei mittlerer Temperatur | 600-700°C | Ausgewogene gasförmige, flüssige und feste Produkte | Moderate Temperatur für effiziente Aufspaltung von Rohstoffen |
Hochtemperatur für Gase/Flüssigkeiten | 700-1200°C | Gasförmige und flüssige Produkte | Vollständiger Abbau komplexer Moleküle |
Langsame Pyrolyse | 1-30°C/min Heizung | Biokohle | Maximiert die Biokohleproduktion in sauerstoffarmen Umgebungen |
Überlegungen zum Druck | 1-30 bar | Beeinflusst die Produktausbeute | Höherer Druck begünstigt Flüssigkeiten; niedrigerer Druck begünstigt Gase |
Konstruktion des Reaktors | 20-30m lang, 1-2in Durchmesser | Optimierte Wärmeübertragung | Gewährleistet eine effiziente Produktausbeute und widersteht hohen Temperaturen und Korrosion |
Sind Sie bereit, Ihren Pyrolyseprozess zu optimieren? Kontaktieren Sie unsere Experten noch heute für maßgeschneiderte Lösungen!