Spark Plasma Sintering (SPS) ist eine fortschrittliche Sintertechnik, die gepulsten elektrischen Gleichstrom, einachsigen Druck und Plasmaaktivierung kombiniert, um eine schnelle und effiziente Verdichtung von Materialien zu erreichen.Im Gegensatz zu herkömmlichen Sinterverfahren nutzt SPS eine einzigartige Kombination aus Joule-Erwärmung, plastischer Verformung und örtlich begrenzter Plasmaentladung zwischen den Pulverpartikeln, um Oberflächen zu aktivieren, Verunreinigungen zu reinigen und die Partikelbindung zu fördern.Dies führt zu schnelleren Erhitzungsraten, kürzeren Sinterzeiten und niedrigeren Verarbeitungstemperaturen, während die Mikrostruktur erhalten bleibt und die mechanischen Eigenschaften des Endprodukts verbessert werden.SPS ist besonders vorteilhaft für die Herstellung hochdichter, feinkörniger Materialien mit verbesserter Leistung.
Die wichtigsten Punkte werden erklärt:
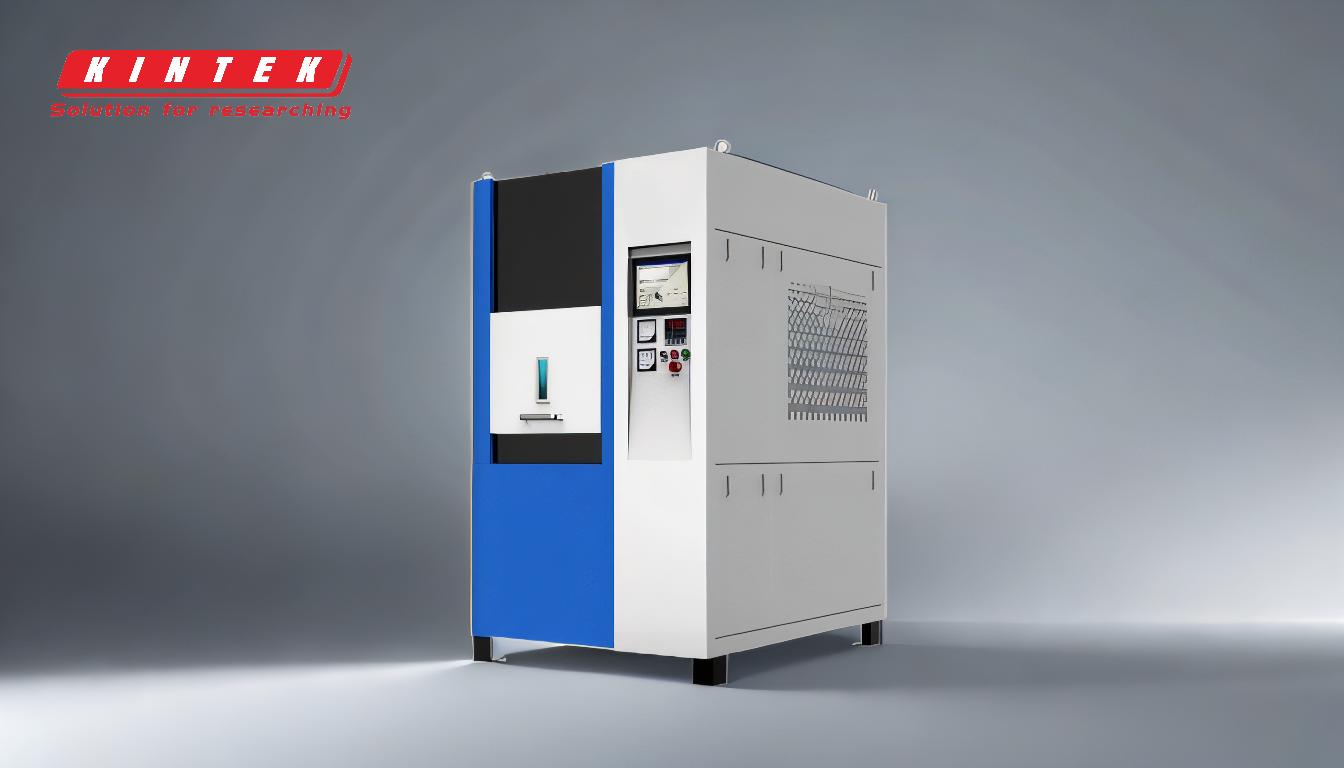
-
Grundlegende Prinzipien der SPS:
- Beim SPS-Verfahren wird gepulster elektrischer Gleichstrom durch eine leitfähige Graphitmatrize geleitet und mit einachsigem Druck kombiniert, um Materialien zu sintern.
- Das Verfahren umfasst drei Schlüsselmechanismen: Plasmaaktivierung, Heißpressen und Widerstandserwärmung.
- Die Joule-Erwärmung erzeugt Wärme im Material, während der Druck eine plastische Verformung bewirkt und die gepulste Spannung lokale Plasmaentladungen zwischen den Partikeln erzeugt.
-
Plasmaaktivierung und Partikelbindung:
- Während der Plasmaerwärmung bewirken elektrische Entladungen zwischen den Pulverpartikeln eine örtliche Oberflächenerwärmung, die Temperaturen von mehreren tausend Grad Celsius erreicht.
- Diese Erhitzung reinigt die Partikeloberflächen durch Verdampfen von Verunreinigungen und aktiviert die Oberflächen, wodurch die Bildung von "Nasen" zwischen den Partikeln gefördert wird.
- Die gleichmäßige Verteilung von Wärme und Plasmaaktivierung gewährleistet eine effiziente Bindung und Verdichtung.
-
Vorteile von SPS:
- Schnelles Erhitzen und Sintern:SPS erreicht schnelle Aufheizraten und kurze Sinterzeiten, was die Verarbeitungszeit im Vergleich zu herkömmlichen Verfahren erheblich verkürzt.
- Niedrige Sintertemperatur:Das Verfahren arbeitet bei Temperaturen unterhalb des Schmelzpunkts des Materials, wodurch das Gefüge erhalten bleibt und das Kornwachstum minimiert wird.
- Energie-Effizienz:Die Kombination aus direkter Erwärmung und Plasmaaktivierung führt zu einem geringeren Energieverbrauch.
- Verbesserte Materialeigenschaften:SPS erzeugt Materialien mit hoher Dichte, feinkörnigen Strukturen und verbesserten mechanischen Eigenschaften.
-
Anwendungen und Vorteile:
- SPS ist ideal für die Konsolidierung von gemahlenen Pulvern, insbesondere von solchen mit verfeinerten Mikrostrukturen, die durch Verfahren wie das kryogene Mahlen erreicht werden.
- Es wird häufig bei der Herstellung von Hochleistungskeramik, Verbundwerkstoffen und nanostrukturierten Materialien eingesetzt, bei denen die Beibehaltung feiner Korngrößen und hoher Dichten entscheidend ist.
- Durch die Fähigkeit, bei niedrigeren Temperaturen und kürzeren Zeiten zu sintern, eignet sich SPS für Materialien, die empfindlich auf eine Zersetzung bei hohen Temperaturen reagieren.
-
Einzigartige Merkmale von SPS:
- Einheitliche Heizung:Das Verfahren gewährleistet eine gleichmäßige Wärmeverteilung in der Probe, wodurch Wärmegradienten reduziert und Defekte minimiert werden.
- Oberflächen-Aktivierung:Die Plasmaentladung reinigt und aktiviert die Partikeloberflächen und verbessert die Bindung und Verdichtung.
- Mikrostruktur Konservierung:SPS hemmt das Kornwachstum, wodurch die ursprüngliche Mikrostruktur der Partikel erhalten bleibt und die Leistung des Endprodukts verbessert wird.
-
Vergleich mit dem traditionellen Sintern:
- Das herkömmliche Sintern beruht auf externen Heizquellen und längeren Bearbeitungszeiten, was häufig zu Kornwachstum und verminderten Materialeigenschaften führt.
- SPS bietet mit seiner direkten Beheizung und Plasmaaktivierung einen effizienteren und kontrollierten Sinterprozess, der zu besseren Materialeigenschaften führt.
Zusammenfassend lässt sich sagen, dass das Spark-Plasma-Sintern ein hochmodernes Verfahren ist, das die Synergieeffekte von gepulstem elektrischem Strom, Druck und Plasmaaktivierung nutzt, um Hochleistungswerkstoffe mit außergewöhnlicher Dichte und Mikrostruktur herzustellen.Seine Vorteile in Bezug auf Geschwindigkeit, Effizienz und Materialqualität machen es zu einer bevorzugten Wahl für die moderne Materialverarbeitung.
Zusammenfassende Tabelle:
Hauptaspekt | Beschreibung |
---|---|
Grundlegende Prinzipien | Kombiniert gepulsten elektrischen Strom, einachsigen Druck und Plasmaaktivierung. |
Plasma-Aktivierung | Die lokale Oberflächenerwärmung reinigt und aktiviert die Partikel für eine effiziente Bindung. |
Vorteile | Schnelle Aufheizung, niedrige Sintertemperaturen, Energieeffizienz und verbesserte Eigenschaften. |
Anwendungen | Hochleistungskeramik, Verbundwerkstoffe, nanostrukturierte Materialien und empfindliche Materialien. |
Einzigartige Merkmale | Gleichmäßige Erwärmung, Oberflächenaktivierung und Erhaltung des Mikrogefüges. |
Vergleich mit herkömmlichen Verfahren | Schneller, effizienter und mit besseren Materialeigenschaften im Vergleich zum herkömmlichen Sintern. |
Nutzen Sie das Potenzial des Spark-Plasma-Sinterns für Ihre Werkstoffe. Kontaktieren Sie unsere Experten noch heute !