Die Sintertemperatur ist ein kritischer Parameter im Sinterprozess, und die Bestimmung, was „zu hoch“ ist, hängt vom zu sinternden Material, den gewünschten Eigenschaften des Endprodukts und der spezifischen verwendeten Sintertechnik ab. Zu hohe Sintertemperaturen können zu Problemen wie erhöhten Kosten, übermäßiger Schrumpfung, Materialfehlern und Schwierigkeiten bei der Prozesssteuerung führen. Die optimale Temperatur muss ein Gleichgewicht zwischen der Erzielung der gewünschten Dichte und mechanischen Eigenschaften und der Vermeidung dieser Nachteile haben. Zu den Schlüsselfaktoren, die das Sintern beeinflussen, gehören Materialzusammensetzung, Partikelgröße, Heizrate und atmosphärische Bedingungen. Hohe Temperaturen können Eigenschaften wie Zugfestigkeit und Schlagenergie verbessern, müssen jedoch sorgfältig gehandhabt werden, um negative Folgen zu vermeiden.
Wichtige Punkte erklärt:
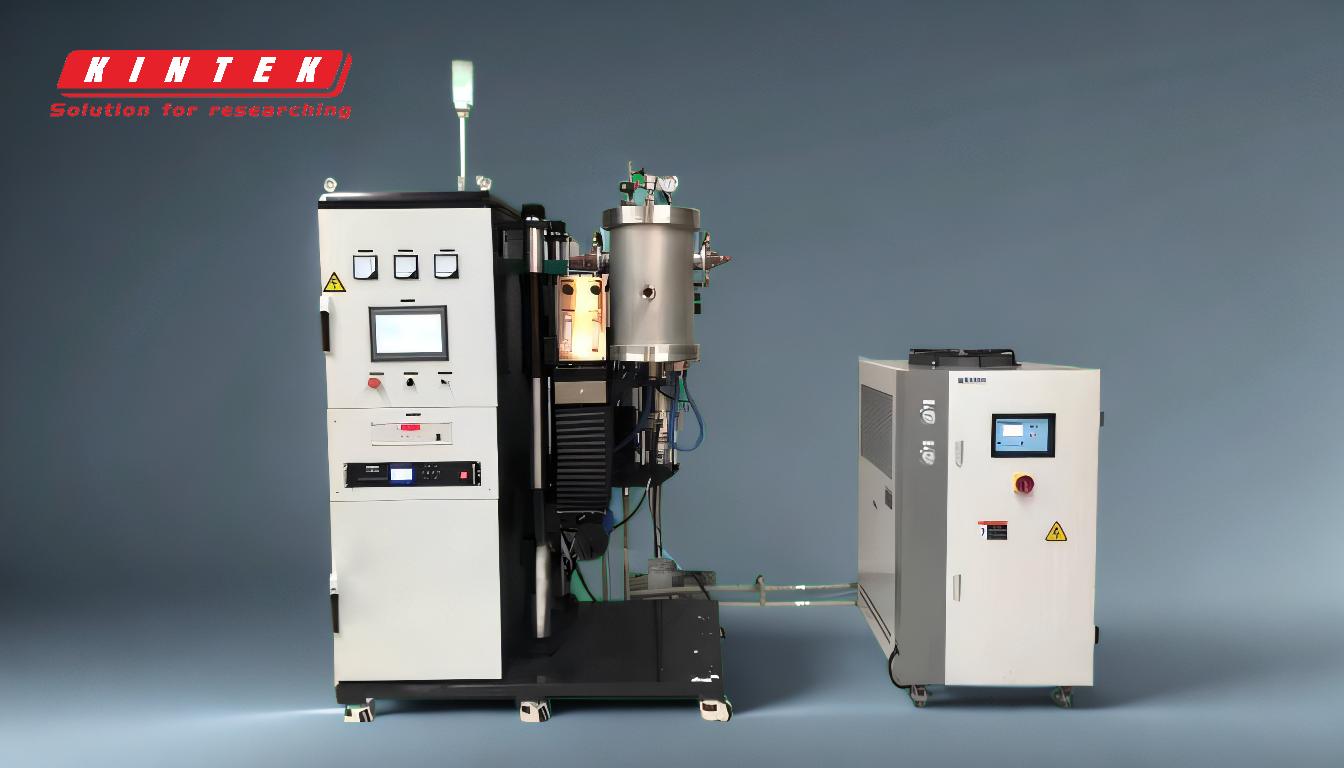
-
Materialspezifische Sintertemperaturen:
- Die Sintertemperatur muss auf das zu verarbeitende Material abgestimmt sein. Beispielsweise haben Metalle, Keramik und Polymere jeweils unterschiedliche Temperaturbereiche für ein effektives Sintern.
- Das Überschreiten der materialspezifischen optimalen Temperatur kann zu unerwünschten Ergebnissen wie übermäßigem Kornwachstum, Schmelzen oder Phasenumwandlungen führen, die die strukturelle Integrität des Endprodukts beeinträchtigen.
-
Einfluss hoher Temperaturen auf die Kosten:
- Höhere Sintertemperaturen erfordern häufig fortschrittlichere und teurere Öfen, die extremer Hitze standhalten und präzise atmosphärische Bedingungen aufrechterhalten können.
- Diese erhöhten Kosten werden in der Regel an den Kunden weitergegeben, wodurch das Hochtemperatursintern für einige Anwendungen weniger wirtschaftlich ist.
-
Schrumpfung und Dimensionskontrolle:
- Hohe Sintertemperaturen können zu einer stärkeren Schrumpfung des Endprodukts führen und erfordern sorgfältige Designanpassungen, um dies während der Produktion zu berücksichtigen.
- Eine übermäßige Schrumpfung kann zu Maßungenauigkeiten führen, die eine zusätzliche Bearbeitung nach dem Sintern erfordern oder das Teil unbrauchbar machen.
-
Kontrolle der flüssigen Phase und Verdichtung:
- Während feinere Pulver und höhere Temperaturen die Verdichtung und Verdichtung verbessern können, muss die Menge der flüssigen Phase sorgfältig kontrolliert werden.
- Zu viel flüssige Phase kann zu ungleichmäßiger Verdichtung, Verformung oder anderen Mängeln im Endprodukt führen.
-
Atmosphärische und ökologische Überlegungen:
- Die Sinteratmosphäre (z. B. Luft, Vakuum oder Inertgase wie Argon oder Stickstoff) spielt eine entscheidende Rolle bei der Bestimmung der optimalen Temperatur.
- Hohe Temperaturen in reaktiven Atmosphären können zu Oxidation oder anderen chemischen Reaktionen führen, die das Material zersetzen.
-
Mechanische Eigenschaften und Kompromisse:
- Durch Hochtemperatursintern können mechanische Eigenschaften wie Zugfestigkeit, Biegewechselfestigkeit und Schlagenergie verbessert werden.
- Diese Vorteile müssen jedoch gegen die Risiken einer Materialverschlechterung, erhöhter Kosten und Prozesskomplexität abgewogen werden.
-
Prozesskontrolle und Risiken:
- Um konsistente Sinterergebnisse bei hohen Temperaturen aufrechtzuerhalten, ist eine präzise Steuerung von Parametern wie Heizrate, Abkühlrate und Schichtdicke erforderlich.
- Zu den Risiken gehören Materialfehler, inkonsistente Sinterergebnisse und Schwierigkeiten beim Erreichen des gewünschten Endpunkts.
-
Alternative Techniken und Parameter:
- Verschiedene Sintertechniken (z. B. druckunterstütztes Sintern, Funkenplasmasintern) können unterschiedliche Temperaturgrenzen und Anforderungen haben.
- Faktoren wie Partikelgröße, Zusammensetzung und angewandter Druck können die optimale Sintertemperatur beeinflussen und die Notwendigkeit übermäßig hoher Temperaturen verringern.
Zusammenfassend lässt sich sagen, dass die Frage, ob die Sintertemperatur „zu hoch“ ist, von einem Gleichgewicht zwischen der Erzielung gewünschter Materialeigenschaften und der Vermeidung negativer Folgen wie erhöhter Kosten, übermäßiger Schrumpfung und Herausforderungen bei der Prozesskontrolle abhängt. Um den optimalen Temperaturbereich für eine bestimmte Anwendung zu bestimmen, ist eine sorgfältige Berücksichtigung der Materialeigenschaften, der Sintertechnik und der Prozessparameter unerlässlich.
Übersichtstabelle:
Schlüsselfaktor | Einfluss hoher Sintertemperaturen |
---|---|
Materialspezifische Temperaturen | Übermäßiges Kornwachstum, Schmelzen oder Phasenumwandlungen können die strukturelle Integrität beeinträchtigen. |
Kosten | Fortschrittliche Öfen und eine präzise Atmosphärenkontrolle erhöhen die Kosten. |
Schwindung | Eine stärkere Schrumpfung führt zu Maßungenauigkeiten, die nach dem Sintern Anpassungen erforderlich machen. |
Flüssigphasenkontrolle | Wenn die flüssige Phase nicht ordnungsgemäß verwaltet wird, kommt es zu ungleichmäßiger Verdichtung und Verformung. |
Atmosphärische Bedingungen | Hohe Temperaturen in reaktiven Atmosphären können zu Oxidation oder chemischem Abbau führen. |
Mechanische Eigenschaften | Verbessert die Zugfestigkeit und Schlagenergie, birgt jedoch das Risiko einer Materialverschlechterung und Prozesskomplexität. |
Prozesskontrolle | Um Defekte zu vermeiden, ist eine genaue Steuerung der Heiz-/Kühlraten und der Schichtdicke unerlässlich. |
Alternative Techniken | Techniken wie das druckunterstützte Sintern können den Bedarf an übermäßig hohen Temperaturen reduzieren. |
Benötigen Sie Hilfe bei der Bestimmung der optimalen Sintertemperatur für Ihre Materialien? Kontaktieren Sie noch heute unsere Experten für maßgeschneiderte Lösungen!