Eine Vakuumbeschichtungsanlage ist ein Spezialgerät, mit dem dünne Filme oder Beschichtungen in einer Vakuumumgebung auf verschiedene Substrate wie Glas, Metall oder Kunststoff aufgetragen werden.Dieses Verfahren ist in Branchen wie der Luft- und Raumfahrt, der Automobilindustrie, der Medizintechnik und der industriellen Fertigung weit verbreitet, um Eigenschaften wie Verschleißfestigkeit, Härte, Korrosionsschutz und Ästhetik zu verbessern.Bei Vakuumbeschichtungsverfahren wie der physikalischen Gasphasenabscheidung (PVD) wird ein Zielmaterial verdampft und auf ein Substrat aufgebracht, wodurch dünne, gleichmäßige Schichten entstehen.Diese Beschichtungen sind von entscheidender Bedeutung für Anwendungen, die von reflektierenden Oberflächen und optischen Filmen bis hin zu energieeffizientem Glas und langlebigen Automobilkomponenten reichen.Die Vakuumumgebung gewährleistet einen sauberen, kontrollierten Prozess, der frei von Verunreinigungen ist, was für die Erzielung hochwertiger, gleichmäßiger Ergebnisse unerlässlich ist.
Die wichtigsten Punkte erklärt:
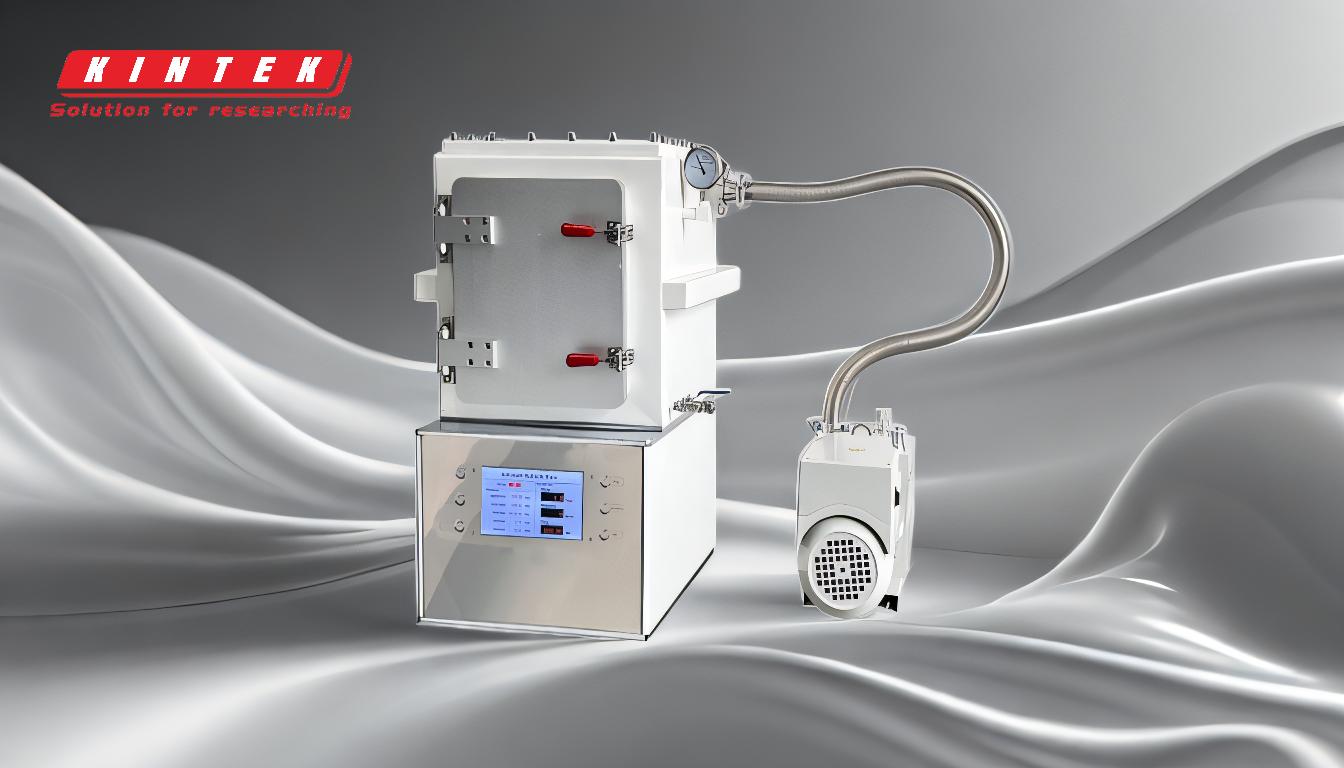
-
Definition und Zweck von Vakuum-Beschichtungsmaschinen:
- Eine Vakuumbeschichtungsanlage dient dazu, dünne Filme oder Beschichtungen auf Substrate in einer Vakuumumgebung aufzubringen.Dieses Verfahren wird eingesetzt, um die Eigenschaften von Werkstoffen zu verbessern, z. B. die Verschleißfestigkeit zu erhöhen, die Härte zu steigern und den Korrosionsschutz zu verbessern.Die Vakuumumgebung gewährleistet, dass der Beschichtungsprozess frei von Verunreinigungen ist, was zu hochwertigen, gleichmäßigen Beschichtungen führt.
-
Anwendungen der Vakuumbeschichtung:
-
Die Vakuumbeschichtung ist in Branchen wie der Luft- und Raumfahrt, der Automobilindustrie, der Medizintechnik und der industriellen Fertigung weit verbreitet.Zu den spezifischen Anwendungen gehören:
- Luft- und Raumfahrt:Schutzbeschichtungen für Komponenten, die extremen Bedingungen ausgesetzt sind.
- Automobilindustrie:Harte Beschichtungen für Motorkomponenten und dekorative Oberflächenbehandlungen.
- Medizinische:Biokompatible Beschichtungen für Implantate und chirurgische Instrumente.
- Industriell:Korrosionsbeständige Beschichtungen für Maschinen und Werkzeuge.
-
Die Vakuumbeschichtung ist in Branchen wie der Luft- und Raumfahrt, der Automobilindustrie, der Medizintechnik und der industriellen Fertigung weit verbreitet.Zu den spezifischen Anwendungen gehören:
-
Physikalische Gasphasenabscheidung (PVD):
- PVD ist eine gängige Vakuumbeschichtungstechnik, bei der ein Zielmaterial erhitzt wird, bis es verdampft, und der Dampf dann auf ein Substrat aufgebracht wird.Bei diesem Verfahren entstehen dünne Schichten, die nur wenige Nanometer bis Mikrometer dick sind, aber erhebliche Vorteile bieten, wie z. B. verbesserte Verschleißfestigkeit, erhöhte Härte und verbessertes ästhetisches Erscheinungsbild.
-
Vorteile der Vakuumbeschichtung:
- Dauerhaftigkeit:Beschichtungen verbessern die Verschleißfestigkeit und Härte von Werkstoffen.
- Korrosionsschutz:Beschichtungen schützen Substrate vor Umweltschäden.
- Ästhetische Aufwertung:Beschichtungen können für dekorative Oberflächen sorgen und das Aussehen von Produkten verbessern.
- Energie-Effizienz:Beschichtungen wie Glas mit niedrigem Emissionsgrad tragen zur Energieeinsparung bei.
-
Arten von Beschichtungen und ihre Verwendung:
- Glas mit niedriger Lichtdurchlässigkeit:Wird in energieeffizienten Fenstern verwendet, um die Wärmeübertragung zu verringern.
- Harte Beschichtungen:Wird auf Motorkomponenten aufgetragen, um die Haltbarkeit zu erhöhen.
- Ophthalmische Beschichtungen:Wird auf Linsen verwendet, um die Kratzfestigkeit und die optischen Eigenschaften zu verbessern.
- Reflektierende Beschichtungen:Wird in Spiegeln und optischen Filmen zur Verbesserung des Reflexionsvermögens verwendet.
-
Vakuumumgebung Vorteile:
- Die Vakuumumgebung in Beschichtungsanlagen verhindert die Verunreinigung durch Gase und Partikel und gewährleistet einen sauberen und kontrollierten Prozess.Dies ist entscheidend für gleichbleibend hochwertige Beschichtungen, insbesondere in Branchen, in denen Präzision und Zuverlässigkeit von größter Bedeutung sind.
-
Vergleich mit anderen Vakuum-Verfahren:
- Während sich die Vakuumbeschichtung auf das Aufbringen dünner Schichten konzentriert, dienen andere Vakuumverfahren wie die Vakuumtrocknung und das Vakuumlöten anderen Zwecken.Bei der Vakuumtrocknung wird beispielsweise unter niedrigem Druck Feuchtigkeit aus Stoffen entfernt, während beim Vakuumlöten Metalle mit einem Zusatzwerkstoff in einem Vakuumofen verbunden werden.Jedes Verfahren nutzt die Vorteile einer Vakuumumgebung, jedoch für unterschiedliche Anwendungen.
-
Industrieller Maßstab und Vielseitigkeit:
- Die Vakuumbeschichtung wird in industriellem Maßstab zur Herstellung von Folien aus anorganischen Materialien eingesetzt.Sie ist vielseitig und kann auf verschiedene Substrate wie Glas, Metall und Kunststoffe aufgebracht werden, wodurch sie sich für eine Vielzahl von Produkten und Branchen eignet.
Wenn ein Käufer diese Schlüsselpunkte versteht, kann er die Eignung einer Vakuumbeschichtungsanlage für seine spezifischen Bedürfnisse besser beurteilen und sicherstellen, dass er die richtige Anlage auswählt, um die gewünschten Ergebnisse für seine Anwendungen zu erzielen.
Zusammenfassende Tabelle:
Aspekt | Einzelheiten |
---|---|
Definition | Aufbringen dünner Filme/Beschichtungen in einer Vakuumumgebung zur Verbesserung der Eigenschaften. |
Anwendungen | Luft- und Raumfahrt, Automobilindustrie, Medizintechnik, industrielle Fertigung. |
Techniken | Physikalische Gasphasenabscheidung (PVD). |
Vorteile | Langlebigkeit, Korrosionsschutz, ästhetische Aufwertung, Energieeffizienz. |
Arten von Beschichtungen | Glas mit niedrigem Emissionsgrad, harte Beschichtungen, augenoptische Beschichtungen, reflektierende Folien. |
Vakuum Vorteile | Sauberer, kontrollierter Prozess frei von Verunreinigungen. |
Industrielle Vielseitigkeit | Geeignet für Glas, Metall, Kunststoff und mehr. |
Entdecken Sie, wie eine Vakuumbeschichtungsanlage Ihre Materialien verändern kann. Kontaktieren Sie uns noch heute für fachkundige Beratung!