Die direkte Energieabscheidung (Direct Energy Deposition, DED) ist ein vielseitiges additives Fertigungsverfahren, bei dem durch den Einsatz fokussierter thermischer Energie, z. B. eines Lasers oder Elektronenstrahls, Materialien durch Schmelzen während des Abscheidens verschmolzen werden.Die beim DED verwendeten Werkstoffe liegen in der Regel in Form von Pulvern oder Drähten vor und werden je nach den gewünschten Eigenschaften des Endprodukts ausgewählt.Zu den gängigen Werkstoffen für die Senkerosion gehören Metalle, Legierungen und Verbundwerkstoffe, die aufgrund ihrer mechanischen, thermischen und elektrischen Eigenschaften ausgewählt werden.Das Verfahren ist in Branchen wie der Luft- und Raumfahrt, der Automobilindustrie und der Medizintechnik weit verbreitet, wo Hochleistungsmaterialien benötigt werden.
Die wichtigsten Punkte werden erklärt:
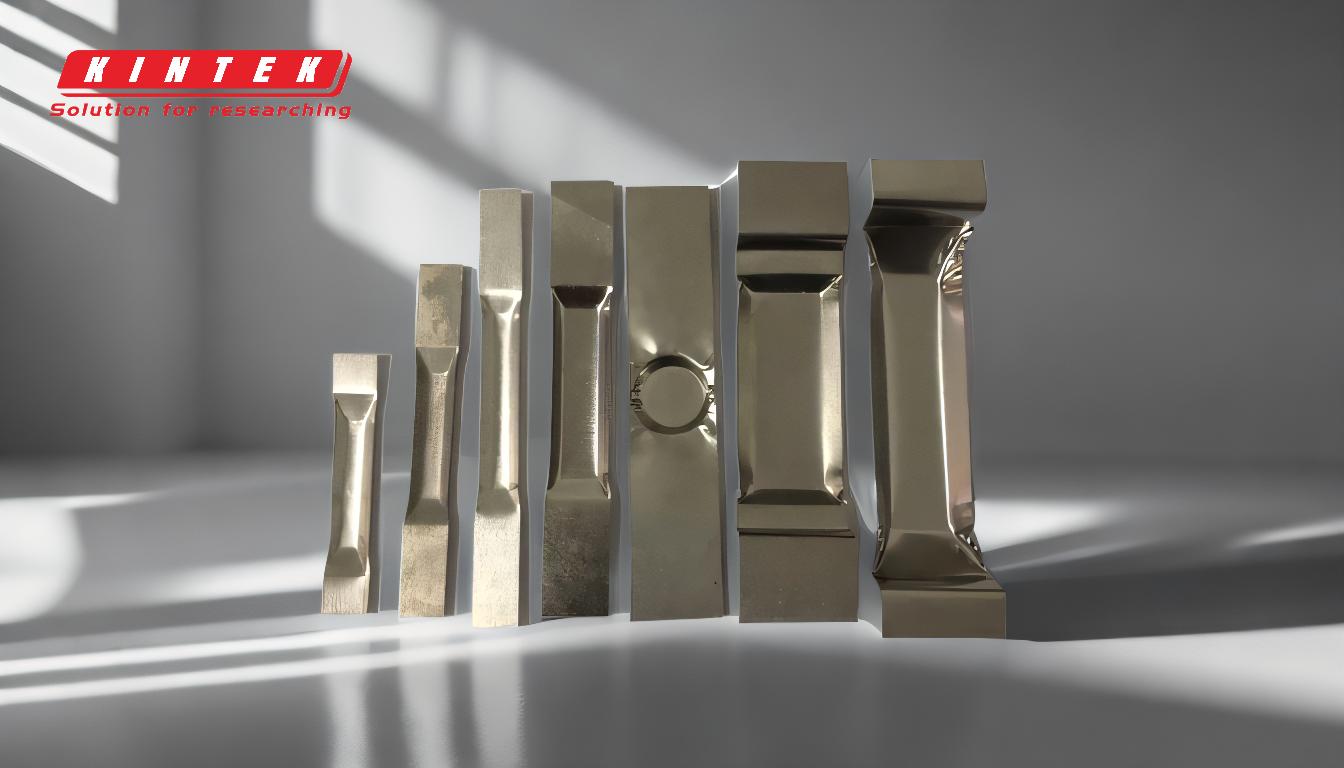
-
Materialien, die bei der direkten Energieabscheidung (DED) verwendet werden:
- Metalle und Legierungen: Bei DED werden in der Regel Metalle wie Titan, Aluminium, Nickel und Stahl sowie deren Legierungen verwendet.Diese Materialien werden aufgrund ihrer Festigkeit, Haltbarkeit und Korrosionsbeständigkeit ausgewählt und eignen sich daher ideal für hochbelastete Anwendungen.
- Verbundwerkstoffe: Verbundwerkstoffe, d. h. Materialien, die aus zwei oder mehr Bestandteilen mit unterschiedlichen physikalischen oder chemischen Eigenschaften bestehen, werden auch im DED eingesetzt.Diese Materialien können so konstruiert werden, dass sie bestimmte Eigenschaften aufweisen, wie z. B. ein besseres Verhältnis von Festigkeit zu Gewicht oder eine bessere Wärmeleitfähigkeit.
- Keramiken: Obwohl weniger verbreitet, können auch Keramiken für DED verwendet werden.Diese Materialien werden in der Regel für Anwendungen verwendet, die eine hohe thermische und chemische Beständigkeit erfordern.
-
Form der Materialien im DED:
- Pulver: Die häufigste Form des Materials, das beim DED verwendet wird, ist Pulver.Das Pulver wird dem Beschichtungsbereich zugeführt, wo es durch die Energiequelle geschmolzen wird und dann zum Endprodukt erstarrt.
- Draht: In einigen Fällen wird Draht anstelle von Pulver verwendet.Der Draht wird in den Beschichtungsbereich geführt, wo er geschmolzen und dann Schicht für Schicht zum Aufbau des Endprodukts abgeschieden wird.
-
Anwendungen von DED-Materialien:
- Luft- und Raumfahrt: In der Luft- und Raumfahrtindustrie wird DED zur Herstellung komplexer Bauteile wie Turbinenschaufeln, Triebwerksteile und Strukturkomponenten verwendet.Materialien wie Titan und Superlegierungen auf Nickelbasis werden aufgrund ihrer hohen Festigkeit und Beständigkeit gegen extreme Temperaturen häufig verwendet.
- Automobilindustrie: In der Automobilindustrie wird DED zur Herstellung leichter Komponenten verwendet, die die Kraftstoffeffizienz und die Leistung verbessern.In diesem Sektor werden häufig Aluminium- und Stahllegierungen verwendet.
- Medizinische Geräte: DED wird auch im medizinischen Bereich zur Herstellung von maßgeschneiderten Implantaten und Prothesen eingesetzt.Materialien wie Titan und Kobalt-Chrom-Legierungen werden aufgrund ihrer Biokompatibilität und Festigkeit bevorzugt.
-
Vorteile der Verwendung von DED-Materialien:
- Maßarbeit: DED ermöglicht die Herstellung hochgradig kundenspezifischer Teile mit komplexen Geometrien, die mit herkömmlichen Fertigungsmethoden nur schwer oder gar nicht zu realisieren wären.
- Materialeffizienz: Das Verfahren ist äußerst effizient im Hinblick auf den Materialverbrauch, da nur dort Material eingesetzt wird, wo es benötigt wird, und somit weniger Abfall anfällt.
- Schnelles Prototyping: DED ist ideal für Rapid Prototyping, da es eine schnelle Iteration und Prüfung neuer Designs ermöglicht.
-
Herausforderungen und Überlegungen:
- Materialeigenschaften: Die Eigenschaften der im DED verwendeten Materialien müssen sorgfältig geprüft werden, da sie die Leistung des Endprodukts beeinflussen können.Faktoren wie Schmelzpunkt, Wärmeleitfähigkeit und mechanische Festigkeit sind entscheidend.
- Prozesskontrolle: Um mit DED gleichbleibende Ergebnisse zu erzielen, ist eine präzise Steuerung des Abscheidungsprozesses erforderlich, einschließlich der Energiequelle, der Materialzufuhr und der Kühlrate.
Zusammenfassend lässt sich sagen, dass die direkte Energieabscheidung (Direct Energy Deposition, DED) eine leistungsstarke additive Fertigungstechnik ist, bei der eine Vielzahl von Materialien, darunter Metalle, Legierungen, Verbundwerkstoffe und Keramik, in Form von Pulver oder Draht verwendet werden.Diese Materialien werden nach den spezifischen Anforderungen der Anwendung ausgewählt, z. B. Festigkeit, Haltbarkeit und Beständigkeit gegen extreme Bedingungen.DED ist in Branchen wie der Luft- und Raumfahrt, der Automobilindustrie und der Medizintechnik weit verbreitet und bietet Vorteile wie individuelle Anpassung, Materialeffizienz und schnelles Prototyping.Eine sorgfältige Berücksichtigung der Materialeigenschaften und der Prozesssteuerung ist jedoch unerlässlich, um die gewünschten Ergebnisse zu erzielen.
Zusammenfassende Tabelle:
Materialtyp | Beispiele | Wichtige Eigenschaften | Allgemeine Anwendungen |
---|---|---|---|
Metalle und Legierungen | Titan, Aluminium | Festigkeit, Langlebigkeit, Korrosionsbeständigkeit | Luft- und Raumfahrt, Automobilindustrie |
Verbundwerkstoffe | Kohlenstofffaser-Verbundwerkstoffe | Verbessertes Verhältnis von Festigkeit zu Gewicht | Luft- und Raumfahrt, Automotive |
Keramiken | Zirkoniumdioxid, Tonerde | Hohe thermische und chemische Beständigkeit | Medizinische Geräte, High-Tech |
Pulver/Drahtform | Pulver, Draht | Materialeffizienz, Individualisierung | Rapid Prototyping, Komplexe Teile |
Sind Sie bereit, DED für Ihr nächstes Projekt zu nutzen? Kontaktieren Sie noch heute unsere Experten für maßgeschneiderte Lösungen!