Während des Sinterns von keramischen Pulvern treten mehrere physikalische Veränderungen auf, die das Pulver in ein dichtes, festes Material verwandeln.Zu diesen Veränderungen gehören die Entfernung von Wasser, organischen Stoffen und adsorbierten Gasen sowie der Abbau von Spannungen und die Reduzierung von Oberflächenoxiden.Mit steigender Temperatur kommt es zu Materialwanderung, Rekristallisation und Kornwachstum, was zu einer Verringerung der Oberflächenenergie und zum Schließen der Poren führt.Dies führt zu einem dichteren Material mit verbesserten mechanischen Eigenschaften, wie z. B. einer höheren Festigkeit und Haltbarkeit.Das Mikrogefüge des Werkstoffs, einschließlich Korngröße, Porengröße und Korngrenzenverteilung, wird durch den Sinterprozess erheblich beeinflusst.
Die wichtigsten Punkte werden erklärt:
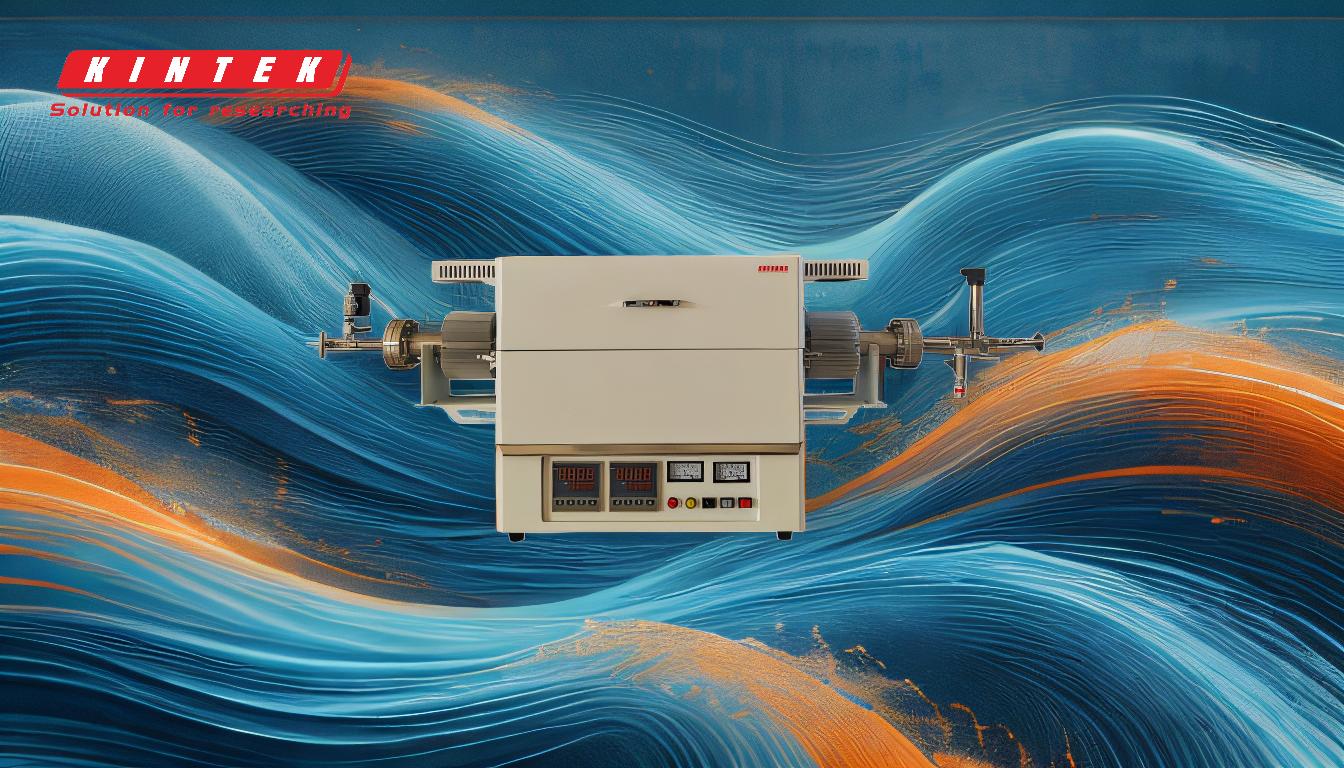
-
Entfernung von Wasser und organischen Stoffen:
- In der Anfangsphase des Sinterns wird das im Keramikpulver enthaltene Wasser oder organische Material verdampft oder entfernt.Dies ist von entscheidender Bedeutung, da das Vorhandensein dieser Stoffe zu Mängeln im Endprodukt, wie Rissen oder Hohlräumen, führen kann.Die Entfernung erfolgt in der Regel bei niedrigeren Temperaturen, bevor die eigentliche Sinterphase beginnt.
-
Entfernung von adsorbierten Gasen:
- Adsorbierte Gase an der Oberfläche der Pulverteilchen werden beim Sintern ebenfalls ausgetrieben.Diese Gase können die Bindung zwischen den Partikeln beeinträchtigen, weshalb ihre Entfernung für die Erzielung einer dichten und gleichmäßigen Mikrostruktur von entscheidender Bedeutung ist.
-
Spannungsabbau:
- Das Sintern trägt dazu bei, innere Spannungen abzubauen, die während des Pulververdichtungsprozesses entstanden sein können.Dieser Spannungsabbau ist wichtig, um eine Verformung oder Rissbildung des Materials während oder nach dem Sintern zu verhindern.
-
Reduktion von Oberflächenoxiden:
- Die Oberflächenoxide auf den Pulverpartikeln werden während des Sinterns reduziert.Dieser Abbau ist notwendig, weil Oxide als Diffusionsbarrieren wirken können, was ein Schlüsselmechanismus im Sinterprozess ist.Die Reduktion der Oxide erleichtert eine bessere Bindung zwischen den Partikeln.
-
Materialwanderung:
- Bei hohen Temperaturen kommt es durch verschiedene Mechanismen wie Diffusion, viskoses Fließen und Gleiten an den Korngrenzen zu einer Materialwanderung.Diese Migration führt zur Füllung von Hohlräumen und zur Verringerung der Porosität, was zu einem dichteren Material führt.
-
Rekristallisation:
- Bei der Rekristallisation werden aus den vorhandenen Pulverpartikeln neue, spannungsfreie Körner gebildet.Dieser Prozess trägt zur Beseitigung von Defekten und zur Verbesserung des gesamten Mikrogefüges des Materials bei.
-
Kornwachstum:
- Unter Kornwachstum versteht man die Größenzunahme der einzelnen Körner innerhalb des Materials.Dies geschieht durch das Zusammenwachsen kleinerer Körner zu größeren Körnern, was durch die Verringerung der Oberflächenenergie bedingt ist.Das Kornwachstum kann sich auf die mechanischen Eigenschaften des Werkstoffs auswirken, z. B. auf seine Festigkeit und Zähigkeit.
-
Verringerung der Oberflächenenergie:
- Der Sinterprozess verringert die Oberflächenenergie der Pulverpartikel, indem die Dampf-Festkörper-Grenzfläche verkleinert wird.Diese Verringerung der Oberflächenenergie ist eine treibende Kraft für die Verdichtung des Materials.
-
Schließen der Poren:
- Mit fortschreitender Sinterung verkleinern sich die im Material vorhandenen Poren oder schließen sich vollständig.Dieser Porenschluss ist eine wesentliche Voraussetzung für das Erreichen eines Materials mit hoher Dichte und verbesserten mechanischen Eigenschaften.
-
Mikrostrukturelle Veränderungen:
- Der Sinterprozess wirkt sich direkt auf die Korngröße, die Porengröße und die Form und Verteilung der Korngrenzen im Mikrogefüge des Materials aus.Diese Veränderungen wirken sich wiederum auf die Eigenschaften des Materials aus, z. B. auf seine Festigkeit, Haltbarkeit und Wärmeleitfähigkeit.
-
Temperatur und Zeit:
- Die Sinterung erfolgt in der Regel bei hohen Temperaturen, in der Regel unterhalb des Schmelzpunkts des Werkstoffs.Der Prozess erfordert oft eine umfangreiche Diffusion und relativ hohe Temperaturen (>~0,6Tm, wobei Tm der Schmelzpunkt ist).Auch die Dauer des Sinterns spielt eine entscheidende Rolle bei der Bestimmung der endgültigen Eigenschaften des Materials.
-
Mechanische Eigenschaften:
- Die physikalischen Veränderungen, die während des Sinterns auftreten, wie Verdichtung, Kornwachstum und Porenschluss, führen zu einer Verbesserung der mechanischen Eigenschaften des Materials.Zu diesen Eigenschaften gehören erhöhte Festigkeit, Härte und Haltbarkeit, wodurch sich die gesinterte Keramik für verschiedene industrielle Anwendungen eignet.
Zusammenfassend lässt sich sagen, dass das Sintern von Keramikpulvern eine Reihe komplexer physikalischer Veränderungen beinhaltet, die das Pulver in ein dichtes, festes Material verwandeln.Diese Veränderungen werden durch hohe Temperaturen angetrieben und führen zu einem Material mit verbesserten mechanischen Eigenschaften und einem verfeinerten Gefüge.Das Verständnis dieser Prozesse ist entscheidend für die Optimierung der Sinterbedingungen, um die gewünschten Materialeigenschaften zu erreichen.
Zusammenfassende Tabelle:
Stufe | Beschreibung |
---|---|
Entfernung von Wasser/organischen Stoffen | Verdampfen von Rückständen bei niedrigeren Temperaturen, um Defekte wie Risse oder Hohlräume zu vermeiden. |
Entfernung von adsorbierten Gasen | Gase auf den Partikeloberflächen werden ausgetrieben, um eine gleichmäßige Bindung und Mikrostruktur zu gewährleisten. |
Spannungsabbau | Innere Spannungen, die durch die Verdichtung entstehen, werden abgebaut, um Verformungen oder Risse zu verhindern. |
Reduktion von Oberflächenoxiden | Oxide werden reduziert, um die Diffusion und Bindung zwischen den Partikeln zu verbessern. |
Materialwanderung | Die Hochtemperaturmigration füllt Hohlräume, verringert die Porosität und erhöht die Dichte. |
Rekristallisation | Die Bildung neuer, defektfreier Körner verbessert das Mikrogefüge. |
Kornwachstum | Kleinere Körner verschmelzen zu größeren, was sich auf die Festigkeit und Zähigkeit auswirkt. |
Verringerung der Oberflächenenergie | Die Oberflächenenergie nimmt ab, was zu Verdichtung und Porenverschluss führt. |
Porenschluss | Die Poren verkleinern oder schließen sich, wodurch sich die Materialdichte und die mechanischen Eigenschaften verbessern. |
Mikrostrukturelle Veränderungen | Korngröße, Porengröße und Korngrenzen werden verfeinert, wodurch sich Festigkeit und Haltbarkeit verbessern. |
Temperatur und Zeit | Hohe Temperaturen (>0,6 Tm) und die Dauer sind entscheidend für das Erreichen der gewünschten Eigenschaften. |
Mechanische Eigenschaften | Verbesserte Festigkeit, Härte und Haltbarkeit machen Sinterkeramik ideal für den industriellen Einsatz. |
Optimieren Sie Ihren keramischen Sinterprozess für hervorragende Ergebnisse - Kontaktieren Sie unsere Experten noch heute !