Beim PVD-Beschichtungsverfahren (Physical Vapor Deposition) werden je nach den gewünschten Beschichtungseigenschaften und der spezifischen PVD-Technik verschiedene Gase verwendet.Argon ist das am häufigsten verwendete Inertgas, da es nicht reaktiv ist und die Reinheit des Beschichtungsmaterials während der Verdampfung gewährleistet.Reaktive Gase wie Sauerstoff, Stickstoff, Methan und Acetylen werden ebenfalls verwendet, um Verbundbeschichtungen wie Oxide, Nitride und Karbide zu bilden.Die Wahl des Gases hängt vom Beschichtungsmaterial, dem Substrat und dem Verwendungszweck des beschichteten Produkts ab.
Die wichtigsten Punkte erklärt:
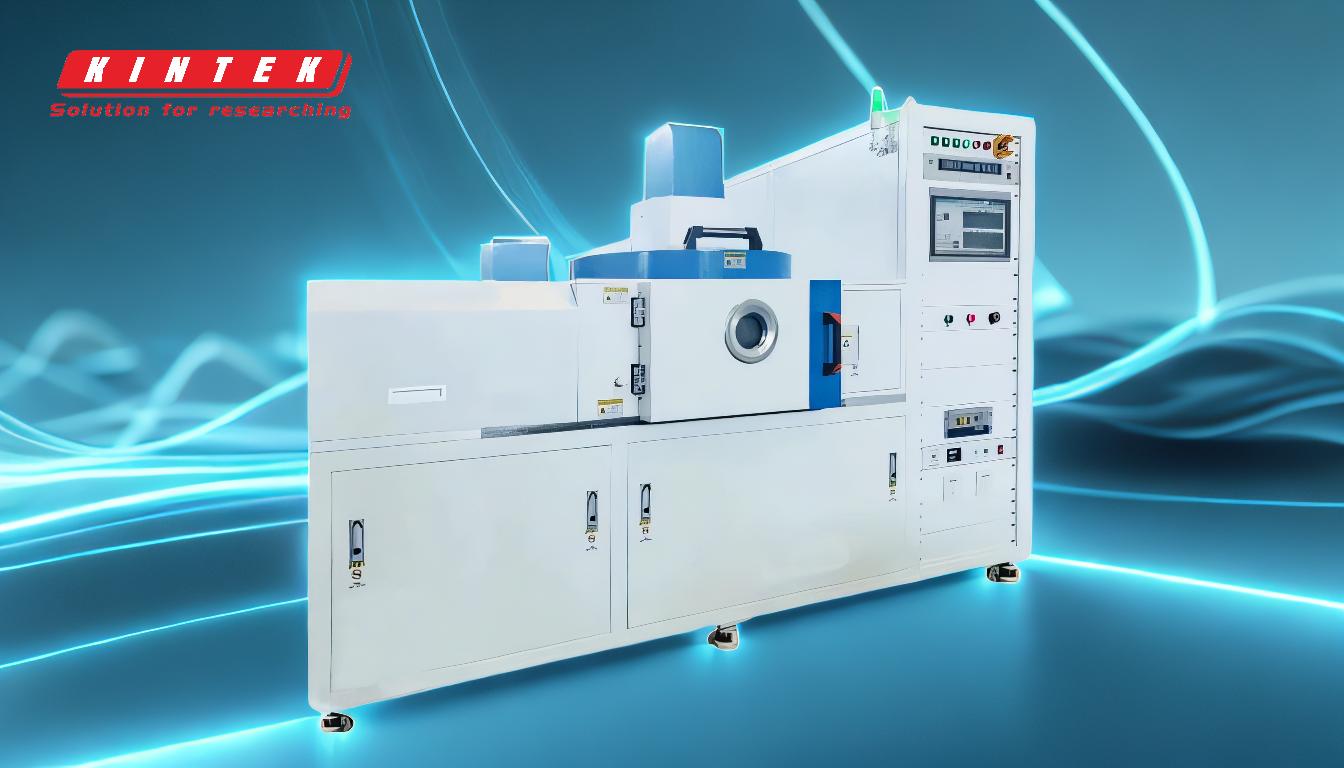
-
Argon als primäres Inertgas:
- Rolle:Argon wird bei der PVD-Beschichtung häufig verwendet, da es inert ist, d. h. es reagiert nicht mit dem Beschichtungsmaterial oder dem Substrat.Dadurch wird sichergestellt, dass das Beschichtungsmaterial während der Verdampfungs- und Abscheidungsphasen rein bleibt.
- Verfahren:Beim Magnetronsputtern oder kathodischen Lichtbogenverdampfen wird das Zielmaterial mit Argon-Ionen beschossen, wodurch es verdampft und ein Plasma entsteht.Das verdampfte Material lagert sich dann auf dem Substrat ab.
- Vorteile:Argon ist aufgrund seiner Inertheit ideal für die Herstellung reiner metallischer Beschichtungen ohne Verunreinigungen.
-
Reaktive Gase für Verbundbeschichtungen:
- Sauerstoff (O2):Zur Herstellung von Metalloxidbeschichtungen (z. B. Titandioxid, Aluminiumoxid).Diese Beschichtungen werden häufig wegen ihrer Härte, Verschleißfestigkeit und optischen Eigenschaften verwendet.
- Stickstoff (N2):Reagiert mit Metallatomen und bildet Nitride (z. B. Titannitrid, Chromnitrid), die für ihre Härte, Korrosionsbeständigkeit und ihr dekoratives goldähnliches Aussehen bekannt sind.
- Methan (CH4) und Acetylen (C2H2):Zur Herstellung von Karbidschichten (z. B. Titankarbid, Siliziumkarbid), die extrem hart und verschleißfest sind.Acetylen wird insbesondere für diamantähnliche Kohlenstoffschichten (DLC) verwendet.
- Hexa-Methyl-Disiloxan (HMDSO):Wird bei der plasmaunterstützten chemischen Gasphasenabscheidung (PACVD) verwendet, um siliziumhaltige Beschichtungen zu erzeugen, die häufig wegen ihrer optischen und Barriereeigenschaften eingesetzt werden.
-
Gasauswahl auf Basis der PVD-Technik:
- Magnetron-Sputtern:Argon ist das primäre Sputtergas, aber reaktive Gase wie Stickstoff oder Sauerstoff können zur Bildung von Verbundschichten zugeführt werden.
- Kathodische Lichtbogenverdampfung:Als Primärgas wird Argon verwendet, aber es können auch reaktive Gase hinzugefügt werden, um die Eigenschaften der Beschichtung zu verändern.
- Thermische oder Elektronenstrahl-Verdampfung:In der Regel wird Argon verwendet, es können aber auch reaktive Gase zur Bildung von Verbundbeschichtungen eingesetzt werden.
-
Prozessgas-Eingabesystem:
- Gasversorgung:Die Gase werden aus Zylindern zugeführt und über Ventile und Messgeräte gesteuert, um präzise Durchflussraten zu gewährleisten.
- Vakuumkammer:Die Gase werden in die Vakuumkammer eingeleitet, wo sie mit dem verdampften Beschichtungsmaterial interagieren und die gewünschte Beschichtung bilden.
-
Anwendungen der verschiedenen Gase:
- Dekorative Beschichtungen:Stickstoff wird häufig verwendet, um goldähnliche Beschichtungen zu dekorativen Zwecken herzustellen.
- Funktionelle Beschichtungen:Sauerstoff und Methan werden zur Herstellung harter, verschleißfester Beschichtungen für industrielle Anwendungen verwendet.
- Optische Beschichtungen:HMDSO wird zur Herstellung von Beschichtungen mit besonderen optischen Eigenschaften verwendet.
-
Die Bedeutung der Gasreinheit:
- Hochreine Gase sind unerlässlich, um Verunreinigungen zu vermeiden und eine gleichbleibende Beschichtungsqualität zu gewährleisten.Verunreinigungen im Gas können zu Defekten in der Beschichtung führen und deren Leistung und Haltbarkeit verringern.
Durch die sorgfältige Auswahl des geeigneten Gases oder Gasgemischs können die Hersteller die Eigenschaften der PVD-Beschichtung auf die spezifischen Anwendungsanforderungen abstimmen, sei es für dekorative, funktionale oder optische Zwecke.
Zusammenfassende Tabelle:
Gasart | Rolle bei der PVD-Beschichtung | Allgemeine Anwendungen |
---|---|---|
Argon (Ar) | Inertes Gas für reine metallische Beschichtungen, das bei Sputtering- und Verdampfungsprozessen verwendet wird. | Reine metallische Beschichtungen, die keine Verunreinigungen aufweisen. |
Sauerstoff (O2) | Bildet Metalloxidschichten (z. B. TiO2, Al2O3) für Härte und Verschleißfestigkeit. | Harte, verschleißfeste Beschichtungen für industrielle Anwendungen. |
Stickstoff (N2) | Erzeugt Nitride (z. B. TiN, CrN) für Härte, Korrosionsbeständigkeit und Dekoration. | Dekorative goldähnliche Beschichtungen und funktionelle verschleißfeste Schichten. |
Methan (CH4) | Bildet Karbidschichten (z. B. TiC, SiC) für extreme Härte und Verschleißfestigkeit. | Industrielle Anwendungen, die eine hohe Haltbarkeit erfordern. |
Acetylen (C2H2) | Wird für diamantähnliche Kohlenstoffbeschichtungen (DLC) verwendet. | Hochleistungsbeschichtungen für Werkzeuge und Maschinen. |
HMDSO | Erzeugt siliziumhaltige Beschichtungen für optische und Barriereeigenschaften. | Optische Beschichtungen und schützende Barriereschichten. |
Benötigen Sie Hilfe bei der Auswahl der richtigen Gase für Ihr PVD-Beschichtungsverfahren? Kontaktieren Sie noch heute unsere Experten für maßgeschneiderte Lösungen!