Die Abscheidung von Dünnschichten erfolgt in der Regel im Vakuum, um hochwertige, reine und haftende Schichten zu gewährleisten. Eine Vakuumumgebung reduziert das Vorhandensein unerwünschter Substanzen wie Sauerstoff, Stickstoff und Feuchtigkeit, die den Film verunreinigen, seine Haftung schwächen oder den Abscheidungsprozess stören können. Außerdem verlängert das Vakuum die mittlere freie Weglänge der Partikel, so dass sich die Filmteilchen ungehindert von der Quelle zum Substrat bewegen können, was zu glatteren und gleichmäßigeren Schichten führt. Die kontrollierte Umgebung ermöglicht auch eine präzise Steuerung der Gaszusammensetzung, des Massenstroms und der Plasmabedingungen, die für wiederholbare und leistungsstarke Dünnschichtabscheidungsprozesse entscheidend sind.
Die wichtigsten Punkte werden erklärt:
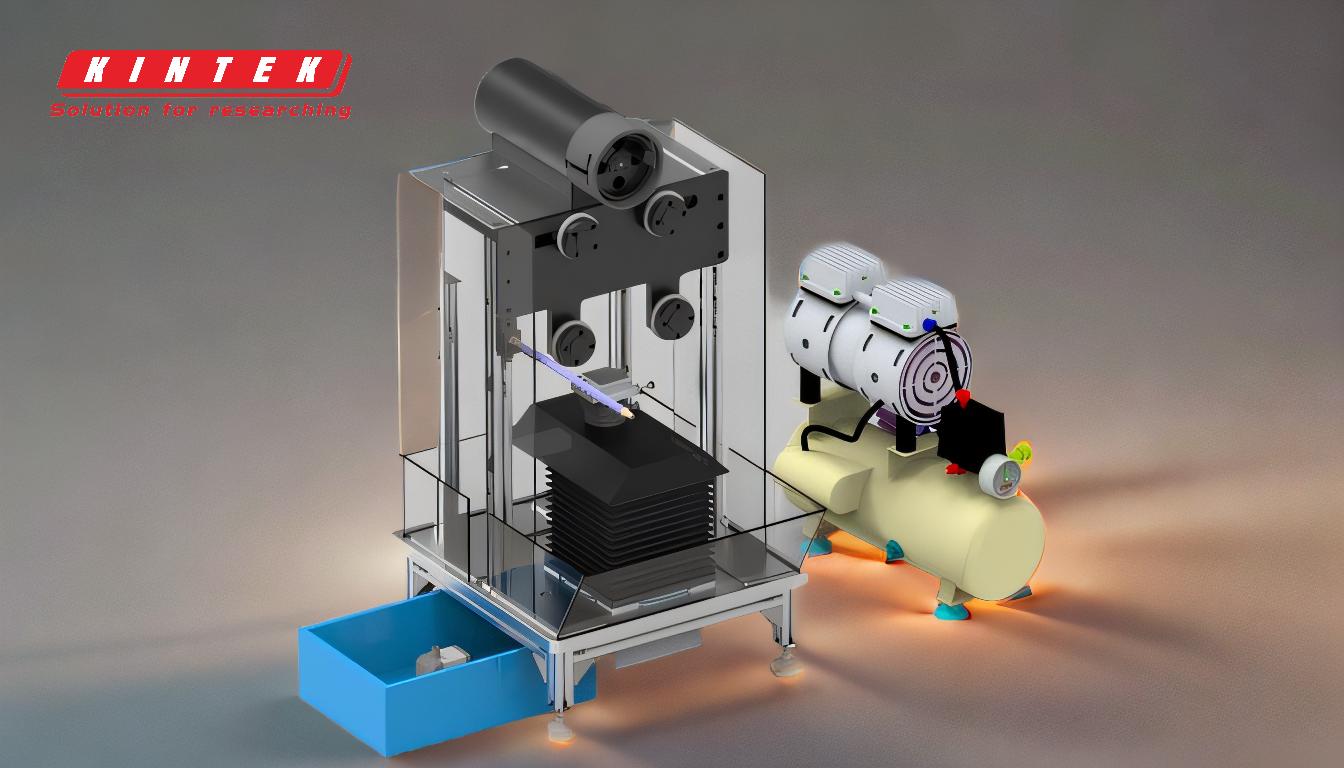
-
Reduktion von Schadstoffen:
- Die Dünnschichtabscheidung im Vakuum minimiert das Vorhandensein unerwünschter Gase und Moleküle wie Sauerstoff, Stickstoff und Feuchtigkeit, die die Schicht verunreinigen können.
- Verunreinigungen können mit dem Folienmaterial reagieren und zu Verunreinigungen oder Defekten führen, die die Qualität und Leistung der Folie beeinträchtigen.
- In organischen lichtemittierenden Bauelementen (OLEDs) oder in der organischen Photovoltaik können selbst Spuren von Sauerstoff oder Feuchtigkeit die für die Lichtemission oder -absorption verantwortlichen funktionellen Spezies auslöschen, was die Effizienz der Bauelemente erheblich verringert.
-
Verbesserte Adhäsion:
- Ein Vakuum sorgt dafür, dass die Filmteilchen das Substrat mit höherer Energie erreichen, was ihre Fähigkeit, sich fest mit dem Substrat zu verbinden, verbessert.
- Bei Verfahren wie der physikalischen Gasphasenabscheidung (PVD) verhindert das Fehlen von Luft oder anderen Flüssigkeiten die Verlangsamung der Partikel, so dass sie sich mit größerer Kraft und Haftung abscheiden können.
- Eine starke Haftung ist entscheidend für die Haltbarkeit und Leistung der Dünnschicht in Anwendungen wie Beschichtungen, Elektronik und Optik.
-
Längerer mittlerer freier Weg:
- Im Vakuum ist die mittlere freie Weglänge von Teilchen (die durchschnittliche Entfernung, die ein Teilchen zurücklegt, bevor es mit einem anderen zusammenstößt) erheblich größer.
- Dadurch können die gesputterten Atome oder verdampften Materialien direkt von der Quelle (z. B. dem Sputtertarget oder dem Verdampfungsmaterial) zum Substrat gelangen, ohne dass es zu Interferenzen kommt, was zu einer gleichmäßigeren und glatteren Abscheidung führt.
- Beim DC-Sputtern beispielsweise sorgt eine längere mittlere freie Weglänge dafür, dass sich die Atome gleichmäßig auf dem Substrat ablagern, was Defekte reduziert und die Schichtqualität verbessert.
-
Kontrollierte und wiederholbare Prozesse:
- Eine Vakuumumgebung ermöglicht eine präzise Steuerung der Gaszusammensetzung, des Drucks und des Massenstroms, die für wiederholbare und hochwertige Abscheidungsprozesse unerlässlich sind.
- Diese Kontrolle ist besonders wichtig bei Anwendungen, die konstante Filmeigenschaften erfordern, wie z. B. bei der Halbleiterherstellung oder bei optischen Beschichtungen.
- Die Fähigkeit, eine Niederdruck-Plasmaumgebung aufrechtzuerhalten, erhöht die Präzision und Zuverlässigkeit des Abscheidungsprozesses weiter.
-
Erhöhte Filmreinheit:
- Hochvakuumumgebungen reduzieren den Partialdruck von Hintergrundgasen wie Sauerstoff und Feuchtigkeit auf extrem niedrige Werte (z. B. unter 10^-6 Torr).
- Dadurch wird die Reinheit der abgeschiedenen Schicht erheblich verbessert, was für Anwendungen wie die Mikroelektronik von entscheidender Bedeutung ist, wo selbst geringfügige Verunreinigungen die Leistung der Geräte beeinträchtigen können.
- Hochreine Schichten sind auch für fortschrittliche Technologien wie Quantencomputer und hocheffiziente Solarzellen unerlässlich.
-
Optimierte Plasma-Umgebung:
- Ein Vakuum ermöglicht die Schaffung einer Niederdruck-Plasmaumgebung, die für viele Beschichtungsverfahren wie Sputtern und plasmaunterstützte chemische Gasphasenabscheidung (PECVD) unerlässlich ist.
- Die Plasmaumgebung erleichtert die Ionisierung von Gasen und die Aktivierung von Abscheidungsprozessen, was die Effizienz und Qualität der Filmbildung verbessert.
- Dies ist besonders vorteilhaft für die Abscheidung komplexer Materialien oder mehrschichtiger Strukturen mit präziser Kontrolle über Dicke und Zusammensetzung.
-
Überlegungen zur Materialqualität:
- Die Qualität der Dünnschicht wird auch von der Reinheit, der Korngröße und der Oberflächenbeschaffenheit der verwendeten Sputtertargets oder Aufdampfmaterialien beeinflusst.
- Hochreine Materialien mit kleinen Korngrößen und glatten Oberflächen werden bevorzugt, um Defekte zu minimieren und eine gleichmäßige Abscheidung zu gewährleisten.
- Bei der Herstellung von Halbleitern beispielsweise ist die Verwendung hochwertiger Targets entscheidend, um die gewünschten elektrischen und optischen Eigenschaften der Dünnschicht zu erreichen.
Durch die Abscheidung von Dünnschichten im Vakuum können die Hersteller Schichten mit hoher Reinheit, starker Haftung, gleichmäßiger Dicke und gleichbleibenden Eigenschaften erzielen, was eine wesentliche Voraussetzung für eine breite Palette moderner Anwendungen ist.
Zusammenfassende Tabelle:
Hauptvorteil | Erläuterung |
---|---|
Reduktion von Schadstoffen | Minimiert unerwünschte Gase wie Sauerstoff und Feuchtigkeit und verhindert so eine Verunreinigung des Films. |
Verbesserte Adhäsion | Sorgt dafür, dass sich die Partikel fest mit dem Untergrund verbinden, was die Haltbarkeit erhöht. |
Längerer mittlerer freier Weg | Lässt die Partikel ungehindert wandern, was zu glatteren, gleichmäßigeren Filmen führt. |
Kontrollierte Prozesse | Ermöglicht die präzise Steuerung von Gaszusammensetzung, Druck und Plasmabedingungen. |
Erhöhte Filmreinheit | Reduziert Verunreinigungen, die für die Mikroelektronik und fortschrittliche Technologien von entscheidender Bedeutung sind. |
Optimierte Plasma-Umgebung | Ermöglicht effiziente Abscheidungstechniken wie Sputtern und PECVD. |
Qualität der Materialien | Hochreine Targets gewährleisten eine gleichmäßige Abscheidung und hervorragende Schichteigenschaften. |
Erzielen Sie hervorragende Ergebnisse bei der Dünnschichtabscheidung kontaktieren Sie unsere Experten noch heute für maßgeschneiderte Lösungen!