Bei der physikalischen Gasphasenabscheidung (PVD) ist eine Vakuumumgebung für das ordnungsgemäße Funktionieren des Abscheidungsverfahrens unerlässlich.Durch das Vakuum wird die Dichte der Atome in der Kammer verringert, so dass das verdampfte Material ungehindert auf das Substrat gelangen kann und hochwertige dünne Schichten bildet.Außerdem wird die Verunreinigung durch unerwünschte Gase minimiert, wodurch die Reinheit und Integrität des abgeschiedenen Materials gewährleistet wird.Darüber hinaus ermöglicht die Vakuumumgebung eine hohe thermische Verdampfungsrate und sorgt für einen kontrollierten, wiederholbaren Prozess, der für die Erzielung konsistenter und zuverlässiger Ergebnisse bei PVD-Anwendungen entscheidend ist.
Die wichtigsten Punkte erklärt:
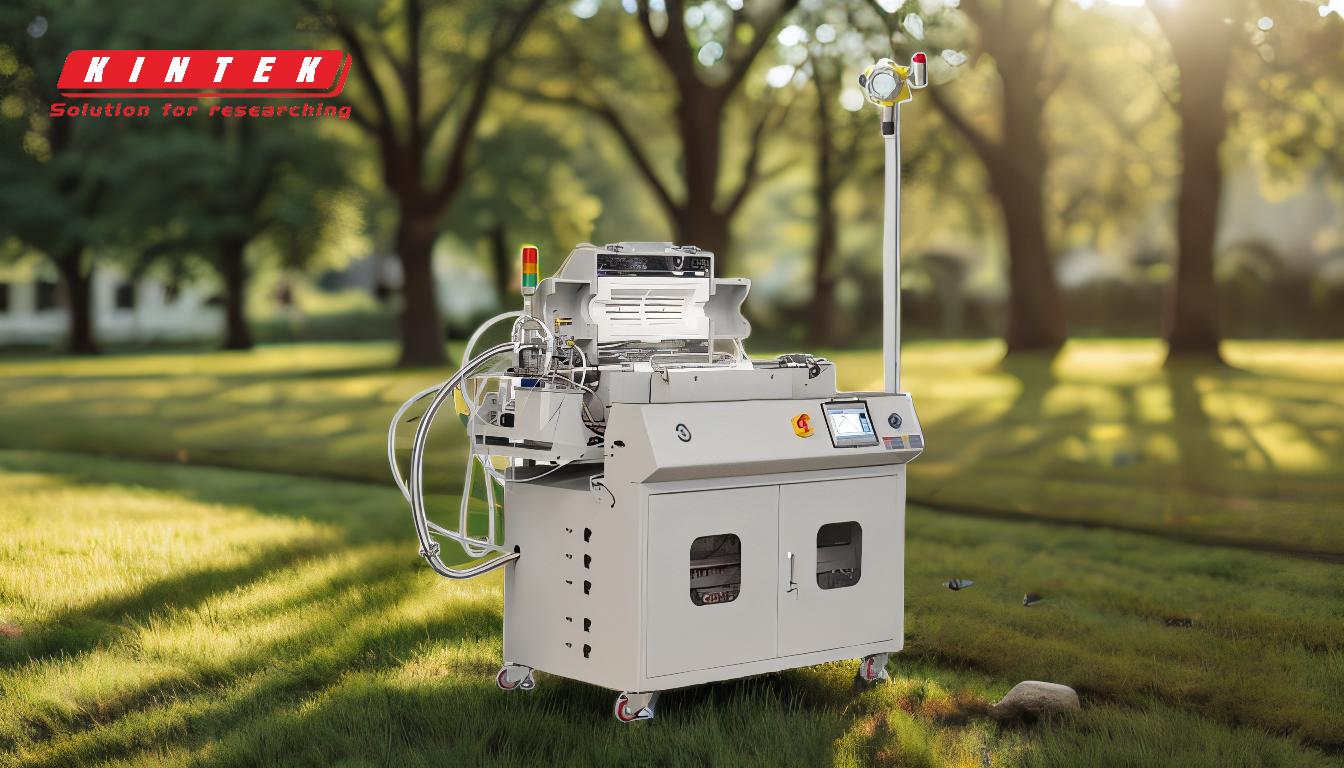
-
Die Verlängerung der mittleren freien Weglänge von Atomen:
- In einem Vakuum ist die Dichte der Atome in der Kammer deutlich geringer.Dadurch verringert sich die Wahrscheinlichkeit von Zusammenstößen zwischen verdampften Atomen und anderen Teilchen, so dass die Atome längere Strecken ohne Störungen zurücklegen können.Diese längere mittlere freie Weglänge gewährleistet, dass das verdampfte Material die Substratoberfläche effizient und gleichmäßig erreichen kann, was für die Bildung hochwertiger dünner Schichten entscheidend ist.
-
Minimierung der Kontamination:
- Eine Vakuumumgebung reduziert das Vorhandensein von unerwünschten Gasen und Partikeln, die das abgeschiedene Material verunreinigen könnten.Verunreinigungen können die Eigenschaften der Dünnschicht beeinträchtigen, z. B. ihre elektrische Leitfähigkeit, optische Transparenz oder mechanische Festigkeit.Durch die Aufrechterhaltung einer Niederdruckumgebung (in der Regel weniger als 10^-5 Torr) wird bei PVD-Verfahren sichergestellt, dass die abgeschiedenen Schichten rein und frei von Verunreinigungen sind.
-
Hohe thermische Verdampfungsrate:
- Die Vakuumumgebung ermöglicht eine hohe thermische Verdampfungsrate, die für die Verdampfung des Zielmaterials erforderlich ist.In Abwesenheit von Luft oder anderen Gasen kann das Material auf die erforderlichen Temperaturen erhitzt werden, ohne dass es zu Oxidation oder anderen chemischen Reaktionen kommt, die in einer Nicht-Vakuum-Umgebung auftreten könnten.Dies ermöglicht eine effiziente und kontrollierte Verdampfung des Zielmaterials.
-
Ungehinderter Materialtransfer:
- Im Vakuum können sich die verdampften Atome frei auf das Substrat zubewegen, ohne durch Luft oder andere Flüssigkeiten gebremst zu werden.Diese ungehinderte Übertragung stellt sicher, dass das Material das Substrat mit genügend Energie erreicht, um fest zu haften, was zu starken und dauerhaften Beschichtungen führt.Das Fehlen von Störungen durch externe Gase ermöglicht außerdem eine präzise Steuerung des Abscheidungsprozesses.
-
Kontrollierter und wiederholbarer Prozess:
- Eine Vakuumumgebung bietet eine stabile und kontrollierte Atmosphäre für den PVD-Prozess.Diese Stabilität ist entscheidend für gleichbleibende und wiederholbare Ergebnisse, die für industrielle Anwendungen unerlässlich sind.Durch die Minimierung von Druck- und Verschmutzungsschwankungen stellt das Vakuum sicher, dass bei jedem Abscheidungszyklus hochwertige dünne Schichten mit den gewünschten Eigenschaften entstehen.
-
Verhinderung von Keimbildung im Dampf:
- Die Vakuumumgebung verhindert, dass verdampfte Atome Keime bilden und Ruß oder andere unerwünschte Partikel in der Dampfphase entstehen.Durch die Aufrechterhaltung eines niedrigen Gasdrucks bleiben die Atome in ihrem Dampfzustand, bis sie das Substrat erreichen, wo sie kondensieren und einen gleichmäßigen dünnen Film bilden können.Dies ist besonders wichtig, um glatte und fehlerfreie Beschichtungen zu erzielen.
-
Verbesserung von Haftung und Filmqualität:
- Das Vakuum sorgt dafür, dass das verdampfte Material das Substrat mit genügend Energie erreicht, um fest zu haften.Diese starke Haftung ist entscheidend für die Haltbarkeit und Leistung der abgeschiedenen Schicht.Außerdem ermöglicht die kontrollierte Umgebung die Bildung von Schichten mit präziser Dicke, Zusammensetzung und Mikrostruktur, die für die Erfüllung spezifischer Anwendungsanforderungen unerlässlich sind.
Durch die Berücksichtigung dieser Schlüsselpunkte spielt die Vakuumumgebung bei PVD-Prozessen eine entscheidende Rolle bei der Gewährleistung der Effizienz, Qualität und Konsistenz der abgeschiedenen dünnen Schichten oder Beschichtungen.
Zusammenfassende Tabelle:
Hauptvorteile von Vakuum bei PVD | Erläuterung |
---|---|
Verlängerung des Mittleren Freien Weges | Reduziert Atomkollisionen und gewährleistet einen effizienten Materialtransfer. |
Minimierung der Kontamination | Die Niederdruckumgebung verhindert Verunreinigungen und gewährleistet die Reinheit des Films. |
Hohe thermische Verdampfungsrate | Ermöglicht effiziente Verdampfung ohne Oxidation oder Reaktionen. |
Ungehinderter Materialtransfer | Ermöglicht es den verdampften Atomen, das Substrat mit hoher Energie zu erreichen. |
Kontrollierter und wiederholbarer Prozess | Gewährleistet gleichbleibende und zuverlässige Abscheidungsergebnisse. |
Verhinderung von Keimbildung im Dampf | Bewahrt den Dampfzustand für glatte, fehlerfreie Beschichtungen. |
Verbessert Haftung und Filmqualität | Verbessert die Haltbarkeit und Präzision der abgeschiedenen Schichten. |
Optimieren Sie Ihren PVD-Prozess mit einer Vakuumumgebung - Kontaktieren Sie noch heute unsere Experten für maßgeschneiderte Lösungen!