Einführung in das Aufdampfen von Silizium-Kohlenstoff (VPD-SiC)
Vorteile von VPD-SiC
VPD-SiC weist in mehreren kritischen Bereichen erhebliche Verbesserungen gegenüber herkömmlichen Materialien auf, was es zu einer hervorragenden Wahl für fortschrittliche Batterieanwendungen macht. Erstens, dieWirkungsgrad der ersten Kurve von VPD-SiC deutlich höher, was sich in effektiveren ersten Lade-Entlade-Zyklen und geringeren Energieverlusten niederschlägt. Diese Verbesserung ist ausschlaggebend für den schnellen Einsatz von Hochleistungsbatterien in verschiedenen Branchen.
Darüber hinaus erhöht VPD-SiC deutlich dieEnergiedichte. Durch die Integration von Siliziumpartikeln in eine poröse Kohlenstoffmatrix kann das Material mehr Energie pro Volumen- oder Masseneinheit speichern, was längere Betriebszeiten und geringere Ladefrequenzen ermöglicht. Dies ist besonders vorteilhaft für tragbare Elektronik, Elektrofahrzeuge und Systeme zur Speicherung erneuerbarer Energien.
Die WebsiteZyklusleistung von VPD-SiC ist ebenfalls überragend und weist eine höhere Stabilität bei wiederholten Lade-/Entladezyklen auf. Diese Beständigkeit ist für die Langlebigkeit und Zuverlässigkeit von Batteriesystemen von entscheidender Bedeutung, da sie eine gleichbleibende Leistung über längere Zeiträume ohne Beeinträchtigung gewährleistet.
Darüber hinaus mindert VPD-SiC wirksam dieZellerweiterung Probleme, die bei herkömmlichen Anoden auf Siliziumbasis auftreten. Diese Verringerung der Volumenausdehnung während der Lade- und Entladevorgänge trägt dazu bei, die strukturelle Integrität der Batterie zu erhalten und damit ihre Lebensdauer und Sicherheit zu erhöhen.
Im Hinblick auf dieKostenreduzierungbietet VPD-SiC ein vielversprechendes Potenzial für die Industrialisierung. Der rationalisierte Syntheseprozess in Verbindung mit der effizienten Nutzung von Rohstoffen kann zu kostengünstigeren Produktionsmethoden führen. Dieser wirtschaftliche Vorteil ist entscheidend für die Ausweitung der Produktion und den Zugang zu Hochleistungsbatterien.
Insgesamt machen die umfassenden Vorteile von VPD-SiC in Bezug auf den Wirkungsgrad, die Energiedichte, die Zyklenleistung, die Zellerweiterung und die Kostenreduzierung es zu einem transformativen Material für die nächste Generation von Batterietechnologien.
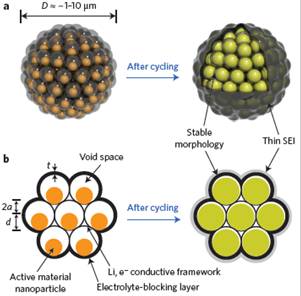
Die wichtigsten Schritte der VPD-SiC-Technologie
Das VPD-Verfahren (Vapor Phase Deposition) zur Herstellung von Silizium-Kohlenstoff (SiC)-Anodenmaterialien ist ein mehrstufiges Verfahren, das mehrere kritische Schritte umfasst, um leistungsstarke Energiespeicherlösungen zu erzielen. Die Technologie kann in drei Hauptphasen unterteilt werden: die Vorbereitung eines porösen Kohlenstoffskeletts, die Abscheidung von Siliziumpartikeln und das Aufbringen einer Kohlenstoffschicht.
-
Vorbereitung des porösen Kohlenstoffskeletts:
- Die Grundlage des VPD-SiC-Prozesses, das poröse Kohlenstoffskelett, wird sorgfältig hergestellt, um einen robusten Rahmen zu schaffen, der die Gesamtleistung des Materials verbessert. Dieser Schritt ist entscheidend für die Schaffung einer Struktur mit hoher spezifischer Oberfläche und hervorragender elektrischer Leitfähigkeit, die für die Verbesserung der Kapazität und der Zyklenstabilität der Anode unerlässlich sind.
-
Abscheidung von Siliziumpartikeln:
- Sobald das poröse Kohlenstoffgerüst aufgebaut ist, werden in einem nächsten Schritt Siliziumpartikel in den Poren abgeschieden. Dies wird in der Regel durch den Einsatz von Silangas erreicht, das eine entscheidende Rolle bei der Bildung von Silizium in der Kohlenstoffmatrix spielt. Der Abscheidungsprozess ist sehr empfindlich gegenüber Parametern wie Temperatur und Gasdurchsatz, die genau kontrolliert werden müssen, um eine gleichmäßige Partikelverteilung und optimale Materialeigenschaften zu gewährleisten.
-
Kohlenstoffschicht-Beschichtung:
- Der letzte Schritt der VPD-SiC-Technologie ist die Beschichtung des Silizium-Kohlenstoff-Verbunds mit einer Kohlenstoffschicht. Diese Schicht dient mehreren Zwecken: Sie schützt die Siliziumpartikel vor Abbau, verbessert die elektrische Leitfähigkeit des Materials und sorgt für zusätzliche mechanische Stabilität. Die Kohlenstoffbeschichtung wird in der Regel durch chemische Gasphasenabscheidung (CVD) oder ähnliche Verfahren aufgebracht, um eine gleichmäßige und kontinuierliche Schicht zu gewährleisten, die die Siliziumpartikel wirksam einkapselt.
Jeder dieser Schritte ist voneinander abhängig, und ihre erfolgreiche Integration ist entscheidend für die Herstellung hochwertiger Silizium-Kohlenstoff-Anodenmaterialien, die den strengen Anforderungen moderner Energiespeicheranwendungen genügen.
Synthese von porösen Kohlenstoffmaterialien
Die Bedeutung von porösem Kohlenstoff
Poröse Kohlenstoffmaterialien spielen eine zentrale Rolle bei der Optimierung von Silizium-Kohlenstoff-Anoden, da sie deren Gesamtleistung erheblich steigern. Diese Verbesserung ist in erster Linie auf mehrere Schlüsseleigenschaften zurückzuführen, die porösem Kohlenstoff eigen sind.
Erstens bietet die hohe spezifische Oberfläche von porösem Kohlenstoff eine große Plattform für die Ablagerung von Siliziumpartikeln. Diese große Oberfläche stellt sicher, dass die Siliziumpartikel gleichmäßig verteilt werden, was für die Aufrechterhaltung der strukturellen Integrität und Leistung der Anode entscheidend ist.
Zweitens erleichtert die ausgezeichnete elektrische Leitfähigkeit von porösem Kohlenstoff den effizienten Elektronentransfer innerhalb des Anodenmaterials. Diese Eigenschaft ist entscheidend für die Aufrechterhaltung einer hohen Energieeffizienz und die Verringerung des Innenwiderstands, was für die langfristige Leistung und Haltbarkeit der Anode von entscheidender Bedeutung ist.
Schließlich trägt die gute mechanische Stabilität von porösem Kohlenstoff zur strukturellen Widerstandsfähigkeit der Anode bei. Diese Stabilität ist besonders wichtig während der wiederholten Lade- und Entladezyklen, da sie dazu beiträgt, die Volumenänderungen der Siliziumpartikel abzuschwächen, wodurch eine Degradation verhindert und die Lebensdauer der Anode verlängert wird.
Zusammenfassend lässt sich sagen, dass die Kombination aus hoher spezifischer Oberfläche, hervorragender elektrischer Leitfähigkeit und guter mechanischer Stabilität poröse Kohlenstoffmaterialien für die Weiterentwicklung von Silizium-Kohlenstoff-Anoden in der Batterietechnologie unverzichtbar macht.
Überlegungen zur Synthese
Bei der Synthese von porösen Kohlenstoffmaterialien für Silizium-Kohlenstoff-Anoden müssen mehrere kritische Faktoren sorgfältig berücksichtigt werden, um eine optimale Leistung und Skalierbarkeit zu gewährleisten. Das Design der Porenstruktur ist von entscheidender Bedeutung, da es sich direkt auf die Fähigkeit des Materials auswirkt, Volumenänderungen während der Lithiierungs- und Delithiierungszyklen zu bewältigen. Eine gut durchdachte Porenstruktur kann die Zyklenstabilität und die Kapazitätserhaltung der Anode erheblich verbessern.
Die Auswahl der Vorstufe ist ein weiterer entscheidender Aspekt. Die Wahl des Vorläufermaterials beeinflusst nicht nur die endgültigen Eigenschaften des porösen Kohlenstoffs, sondern auch die Einfachheit der Synthese und die Kosten des Materials. Vorstufen mit hoher Kohlenstoffausbeute und geringem Aschegehalt werden in der Regel bevorzugt, da sie die Bildung einer gleichmäßigen und leitfähigen Kohlenstoffmatrix erleichtern. Darüber hinaus sollte die Vorstufe mit skalierbaren Produktionstechniken kompatibel sein, um eine großtechnische Herstellung zu ermöglichen.
Die Skalierbarkeit für eine großtechnische Produktion ist ein nicht verhandelbarer Gesichtspunkt. Der Syntheseprozess muss an Reaktoren im industriellen Maßstab angepasst werden können, um eine gleichbleibende Qualität und Ausbeute zu gewährleisten. Dazu müssen die Reaktionsbedingungen wie Temperatur, Druck und Reaktantenkonzentrationen optimiert werden, um eine gleichmäßige Ablagerung der Siliziumpartikel im porösen Kohlenstoff zu erreichen. Darüber hinaus sollte das Verfahren den Energieverbrauch und die Abfallerzeugung minimieren, was einer nachhaltigen Herstellungspraxis entspricht.
Zusammenfassend lässt sich sagen, dass die Synthese poröser Kohlenstoffmaterialien für Silizium-Kohlenstoff-Anoden einen ganzheitlichen Ansatz erfordert, bei dem das Design der Porenstruktur, die Auswahl der Ausgangsstoffe und die Skalierbarkeit berücksichtigt werden müssen, um die Anforderungen an die Leistung und die industrielle Anwendung zu erfüllen.
Silan und Abscheidungsprozess
Die Rolle des Silangases
Silangas (SiH₄) spielt eine zentrale Rolle bei der Abscheidung von Siliziumpartikeln in der porösen Kohlenstoffstruktur, einem entscheidenden Schritt bei der Herstellung von Silizium-Kohlenstoff-Anodenmaterialien. Die Wirksamkeit dieses Prozesses hängt von der sorgfältigen Steuerung der Silaneigenschaften und der komplizierten Balance der Abscheidungsparameter ab.
Eine der größten Herausforderungen bei der Verwendung von Silan ist seine Empfindlichkeit gegenüber Umweltbedingungen. So kann beispielsweise das Einbringen von Sauerstoff in die Abscheidungskammer zur Bildung von SiOH führen, was die Qualität der Siliziumschicht beeinträchtigt. In Abwesenheit von Sauerstoff hingegen können amorphe Siliziumschichten erzeugt werden, die sowohl rein als auch für die Abscheidung geeignet sind. Dies unterstreicht die Notwendigkeit einer genauen Kontrolle der Abscheidungsumgebung, um unerwünschte chemische Reaktionen zu vermeiden.
Darüber hinaus sind die Kosten und die Verfügbarkeit von Silan wichtige Faktoren, die die Machbarkeit einer großtechnischen Produktion beeinflussen. Das Material muss aufgrund seiner reaktiven Natur vorsichtig gehandhabt werden, was eine spezielle Ausrüstung und Sicherheitsprotokolle zur Risikominderung erfordert. Darüber hinaus erfordert der Abscheidungsprozess ein empfindliches Gleichgewicht von Silan und anderen Gasen wie Sauerstoff und Xenon, um den gewünschten Silizium-Kohlenstoff-Verbundwerkstoff zu erhalten.
Um den Abscheidungsprozess zu optimieren, ist es wichtig, die Silaneinleitung in einem mittleren Bereich zu halten. Ein Überschuss an Silan kann zur Bildung von SIH führen, während ein Überschuss an Sauerstoff zu SiOH führen kann, was beides die Qualität des Endprodukts beeinträchtigt. Das richtige Gleichgewicht ist entscheidend, um Siliziumschichten zu erhalten, die sowohl amorph als auch hart sind, was die Leistungsmerkmale der Anode verbessert.
Zusammenfassend lässt sich sagen, dass die Rolle des Silangases im Abscheidungsprozess vielschichtig ist und ein tiefes Verständnis seiner chemischen Eigenschaften sowie eine sorgfältige Steuerung der Abscheidungsparameter erfordert, um die Herstellung hochwertiger Silizium-Kohlenstoff-Anodenmaterialien zu gewährleisten.
Parameter des Abscheidungsprozesses
Die Parameter des Abscheidungsprozesses spielen eine entscheidende Rolle bei der Bestimmung der Qualität und Leistung von Silizium-Kohlenstoff (Si-C)-Anodenmaterialien. Zu den Schlüsselparametern gehören die Abscheidungstemperatur, die Reaktionsbedingungen und strenge Sicherheitsmaßnahmen, von denen jeder einzelne die Eigenschaften des Endprodukts erheblich beeinflusst.
Einfluss der Temperatur
Die Abscheidungstemperatur ist ein entscheidender Faktor, der sich direkt auf die Gleichmäßigkeit und Dichte der Siliziumpartikel innerhalb der porösen Kohlenstoffmatrix auswirkt. Höhere Temperaturen können die Diffusion von Silangas in die Kohlenstoffporen verbessern, was zu einer gleichmäßigeren Abscheidung führt. Zu hohe Temperaturen können jedoch auch zu einer thermischen Zersetzung der Kohlenstoffstruktur führen, wodurch die mechanische Stabilität und die spezifische Oberfläche verringert werden. Daher ist die Optimierung der Abscheidungstemperatur von entscheidender Bedeutung, um diese konkurrierenden Effekte auszugleichen.
Reaktionsbedingungen
Die Reaktionsbedingungen, wie Gasdurchsatz und Druck, sind ebenso wichtig. Diese Bedingungen bestimmen die Verweilzeit der Reaktanten in der Abscheidekammer und die Geschwindigkeit der Siliziumpartikelbildung. So kann ein höherer Gasdurchsatz zu kürzeren Verweilzeiten führen, wodurch die Gleichmäßigkeit der Siliziumabscheidung möglicherweise verringert wird. Umgekehrt können niedrigere Durchflussraten den Abscheidungsprozess verbessern, aber auch das Risiko einer Verstopfung oder anderer betrieblicher Probleme erhöhen. Daher ist eine genaue Kontrolle dieser Bedingungen erforderlich, um optimale Silizium-Kohlenstoff-Materialeigenschaften zu erzielen.
Sicherheitsmaßnahmen
Angesichts der Gefährlichkeit von Silangas sind strenge Sicherheitsmaßnahmen während des Abscheidungsprozesses unerlässlich. Dazu gehören moderne Gasdetektionssysteme, Notabschaltprotokolle und robuste Belüftungssysteme, um die Gefahr von Lecks oder Explosionen zu verringern. Die Gewährleistung einer sicheren Arbeitsumgebung schützt nicht nur das Personal, sondern gewährleistet auch die Zuverlässigkeit und Beständigkeit des Abscheidungsprozesses, was für die industrielle Produktion entscheidend ist.
Zusammenfassend lässt sich sagen, dass die Parameter des Abscheidungsprozesses - Temperatur, Reaktionsbedingungen und Sicherheitsmaßnahmen - eng mit der Leistung und Qualität von Silizium-Kohlenstoff-Anodenmaterialien verbunden sind. Die Optimierung dieser Parameter ist unerlässlich, um die elektrochemischen Eigenschaften des Materials zu verbessern und seine Eignung für großtechnische Anwendungen zu gewährleisten.
Abscheidungsausrüstung
Arten von Abscheidungsanlagen
Für die Abscheidung von Silizium-Kohlenstoff-Anodenmaterialien werden in erster Linie Drehrohröfen und Wirbelschichtanlagen eingesetzt. Jeder Anlagentyp bietet unterschiedliche Vorteile und Herausforderungen, die für das Erreichen optimaler Materialeigenschaften und die Skalierbarkeit entscheidend sind.
Drehrohröfen
- Betriebliche Einfachheit: Drehrohröfen sind relativ einfach zu bedienen und werden daher bevorzugt für erste Versuche und die Produktion in kleinem Maßstab eingesetzt.
- Kostengünstig: Sie sind in der Regel kostengünstiger, sowohl was die Investitions- als auch die Betriebskosten betrifft, was für Pilotprojekte von Vorteil sein kann.
- Flexibel: Drehrohröfen bieten Flexibilität bei der Handhabung verschiedener Ausgangsmaterialien und können an unterschiedliche Ablagerungsbedingungen angepasst werden.
Wirbelschichtöfen
- Gleichmäßigkeit und Effizienz: Wirbelschichten sind bekannt für ihre überragende Gleichmäßigkeit in der Partikelverteilung und eine höhere Silangasausnutzung. Dies führt zu gleichmäßigeren Materialeigenschaften und einer verbesserten Gesamtleistung.
- Verbesserte Sicherheitsmaßnahmen: Der Einsatz von Wirbelschichten erfordert aufgrund der hohen Reaktivität von Silangas strenge Sicherheitsprotokolle. Hochentwickelte Sicherheitssysteme und eine kontinuierliche Überwachung sind unerlässlich, um die Risiken im Zusammenhang mit Gaslecks und anderen Gefahren zu mindern.
- Komplexität und Verlässlichkeit: Trotz ihrer Vorteile sind Wirbelschichten komplexer und erfordern eine hohe Zuverlässigkeit, um einen kontinuierlichen und stabilen Betrieb zu gewährleisten. Diese Komplexität kann eine Herausforderung bei der Vergrößerung der Produktion im industriellen Maßstab darstellen.
Zusammenfassend lässt sich sagen, dass Drehrohröfen eine einfachere und kostengünstigere Lösung darstellen, während Wirbelschichten eine höhere Gleichmäßigkeit und Effizienz bieten, wenn auch mit erhöhter Komplexität und Sicherheitsanforderungen. Die Wahl der Anlage hängt von den spezifischen Anforderungen und dem Umfang des Produktionsprozesses ab.
Herausforderungen bei der Industrialisierung
Die großtechnische Herstellung von Silizium-Kohlenstoff-Anodenmaterialien mit Hilfe von Wirbelschichten birgt einige erhebliche Herausforderungen. Diese Herausforderungen betreffen vor allem die Gewährleistung eines kontinuierlichen Betriebs, die Aufrechterhaltung der Gleichmäßigkeit des Abscheidungsprozesses und die Erzielung einer hohen Silangasausnutzung.
Eines der Haupthindernisse ist die Notwendigkeit derAnlagen- und Prozessoptimierung. Wirbelschichten bieten zwar eine hervorragende Gleichmäßigkeit und Silanausnutzung, erfordern aber eine genaue Kontrolle verschiedener Parameter wie Temperatur, Gasdurchsatz und Partikelgrößenverteilung. Jede Abweichung von diesen optimalen Bedingungen kann zu uneinheitlichen Materialeigenschaften führen, die sich nachteilig auf die Gesamtleistung der Anode auswirken.
Außerdem ist dieZuverlässigkeit und Sicherheit des Wirbelschichtsystems von entscheidender Bedeutung. Die Verwendung von Silangas, das hochreaktiv und explosionsgefährdet ist, erfordert robuste Sicherheitsmaßnahmen und eine kontinuierliche Überwachung. Dadurch wird der Industrialisierungsprozess noch komplexer und erfordert fortschrittliche Automatisierungs- und Kontrollsysteme, um einen sicheren und effizienten Betrieb zu gewährleisten.
Außerdem ist dieSkalierbarkeit des Wirbelschichtverfahrens ein großes Problem dar. Der Übergang von Experimenten im Labormaßstab zur industriellen Produktion in vollem Umfang erfordert sorgfältige Überlegungen, wie das gleiche Maß an Kontrolle und Gleichmäßigkeit über größere Mengen aufrechterhalten werden kann. Dies ist oft mit erheblichen Investitionen in die Aufrüstung der Anlagen und die Verbesserung des Verfahrens verbunden.
Zusammenfassend lässt sich sagen, dass Wirbelschichten zwar vielversprechende Vorteile für die Herstellung von Silizium-Kohlenstoff-Anoden bieten, ihre industrielle Nutzung jedoch die Bewältigung erheblicher technischer und betrieblicher Herausforderungen erfordert. Dazu gehören die Optimierung von Anlagen und Prozessen, die Gewährleistung von Zuverlässigkeit und Sicherheit sowie die Lösung von Fragen der Skalierbarkeit, um eine großtechnische, kontinuierliche Produktion zu erreichen.
Kontaktieren Sie uns für eine kostenlose Beratung
Die Produkte und Dienstleistungen von KINTEK LAB SOLUTION werden von Kunden auf der ganzen Welt anerkannt. Unsere Mitarbeiter helfen Ihnen gerne bei allen Fragen weiter. Kontaktieren Sie uns für eine kostenlose Beratung und sprechen Sie mit einem Produktspezialisten, um die am besten geeignete Lösung für Ihre Anwendungsanforderungen zu finden!