Verständnis des Vakuum-Schwebe-Induktionsschmelzofens
Lernen Sie die Komponenten eines Vakuumschwebe-Induktionsschmelzofens kennen, einschließlich des Ofenkörpers, der Mittelfrequenzleistung, des Vakuumsystems, des Kühlsystems und des elektrischen Steuerungssystems. Erfahren Sie, wie jedes Element zur Effizienz und Präzision von Metallschmelzprozessen beiträgt.
Vakuum-Induktionsschmelzöfen (VIM) haben sich von der spezialisierten Verarbeitung exotischer Legierungen zu einer weit verbreiteten Anwendung in verschiedenen Industriezweigen entwickelt, einschließlich der Herstellung von rostfreien Stählen und anderen Metallen. Diese Öfen arbeiten unter Vakuumbedingungen und bieten eine präzise Kontrolle über den Schmelzprozess.
Wie funktioniert ein Vakuum-Induktionsofen?
Das Material wird unter Vakuum in den Induktionsofen gegeben, wo es mit Strom versorgt wird, um den Schmelzvorgang einzuleiten. Um die gewünschte Schmelzleistung zu erreichen, werden weitere Chargen zugegeben. Das geschmolzene Metall wird unter Vakuumbedingungen verfeinert, wobei Anpassungen vorgenommen werden, um eine präzise Schmelzchemie zu erreichen.
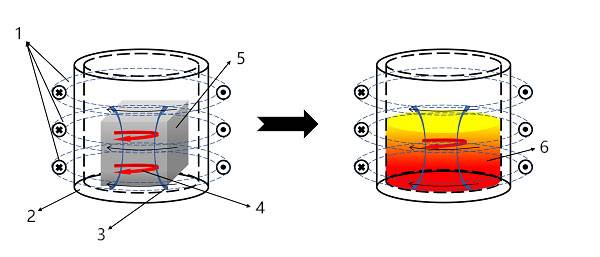
Hauptkomponenten und Funktionen
Neben dem Ofenkörper und dem Vakuumsystem ist ein Vakuum-Induktionsschmelzofen mit wichtigen Komponenten wie einer Mittelfrequenz-Stromversorgung, einem elektrischen Steuerungssystem und einem Kühlsystem ausgestattet. Diese Komponenten arbeiten zusammen, um die Energiezufuhr für das Schmelzen zu gewährleisten und gleichzeitig eine Überhitzung zu verhindern und die strukturelle Integrität sicherzustellen.
Hilfskomponenten wie Transportwagen, Ofentürmechanismen und Beobachtungsfenster können je nach den spezifischen Prozessanforderungen hinzugefügt werden. Bei Anwendungen mit hohen Verunreinigungsgraden ist ein Gasfiltersystem für die Aufrechterhaltung der Metallreinheit unerlässlich.
Vorteile von Vakuum-Induktionsschmelzöfen
Die kompakte Struktur von VIM-Öfen, bei denen nur der Schmelzteil in der Vakuumkammer eingeschlossen ist, ermöglicht eine bessere Kontrolle des Vakuumniveaus und schnellere Evakuierungszeiten. Merkmale wie das elektromagnetische Rühren sorgen für eine gleichmäßige Durchmischung der zugegebenen Elemente im gesamten Schmelzbad, wodurch eine konstante Temperatur aufrechterhalten wird.
Die Einbeziehung von Filterschikanen und anderen Maßnahmen verbessert die Metallreinheit, indem sie die Auswirkungen von Verunreinigungen abschwächt. Die Erkennung und Reparatur von Vakuumlecks wird durch das geringere Volumen des Ofens vereinfacht, was die Ausfallzeiten für die Wartung reduziert.
Präzision und Kontrolle
Vakuum-Induktionsschmelzöfen bieten eine präzise Temperaturregelung durch fortschrittliche elektrische Steuerungssysteme. Die Benutzer können den Schmelzprozess in Echtzeit überwachen und so Genauigkeit und Konsistenz gewährleisten. Das zentralisierte Kühlsystem regelt die Schmelztemperaturen und verbessert so die Prozesssteuerung und die Produktqualität.
Anwendungen und Flexibilität
VIM-Öfen sind in verschiedenen Größen erhältlich, von kleinen Geräten für Experimente im Gramm-Maßstab bis hin zu größeren Modellen für die industrielle Produktion. Dank dieser Vielseitigkeit können die Benutzer die Chargengrößen an ihre spezifischen Anforderungen anpassen.
Gaseliminierung und Oxidationsvermeidung
Einer der Hauptvorteile des Vakuum-Induktionsschmelzens ist die Entfernung von Gasen aus geschmolzenen Metallen. Dieser Prozess verhindert eine schnelle Oxidation und gewährleistet die Reinheit und Qualität des Endprodukts.
Zusammenfassend lässt sich sagen, dass Vakuum-Induktionsschmelzöfen in modernen Metallschmelzprozessen eine wichtige Rolle spielen, da sie eine präzise Steuerung, eine höhere Reinheit und eine größere Flexibilität in der Produktion bieten.
Effizienz und Flexibilität
Informieren Sie sich über das Angebot an Vakuumöfen, das von kleinen Einheiten, die für Chargen im Grammbereich geeignet sind, bis hin zu größeren Öfen für unterschiedliche Chargengrößen reicht. Verstehen Sie, wie diese Vielseitigkeit den Anwendern hilft, ihre Produktionsprozesse zu optimieren.
Fortschrittliche Automatisierung und Steuerung:
Unsere Vakuumöfen sind mit fortschrittlichen Automatisierungs- und Steuerungssystemen ausgestattet, die Ihnen ein präzises Prozessmanagement und Überwachungsmöglichkeiten bieten. Mit unserer benutzerfreundlichen Schnittstelle können Sie mühelos verschiedene Parameter programmieren und anpassen und so eine optimale Leistung und Effizienz sicherstellen. Mithilfe von Echtzeitdaten und -diagnosen können Sie fundierte Entscheidungen treffen, Anomalien erkennen und Ihre Produktionsprozesse für einen maximalen Output optimieren.
Energie-Effizienz und Nachhaltigkeit:
Vakuum-Designs
Vakuumöfen für die Niedertemperaturverarbeitung können chargenweise oder kontinuierlich betrieben werden, eigenständig, in kontinuierliche Vakuumofensysteme integriert oder als separates "Modul" in ein zelluläres System integriert sein. Die grundlegende Funktionsweise eines Batch-Vakuumofens ist zum Beispiel wie folgt:
- Mechanische Vakuumpumpen, optional mit Gebläsen ausgestattet, erzeugen ein Vakuum von bis zu 1,3 x 10-3 mbar (0,001 Torr), wobei 6,7 x 10-3 mbar (0,005 Torr) üblich sind. Dies wird normalerweise innerhalb von 10-30 Minuten nach Beginn des Zyklus erreicht, je nach Größe der Pumpsysteme und der Art der Verunreinigungen, die im Arbeitsbereich vorhanden sind.
- Anschließend wird die Einheit im Bereich von 66,7 x 101 mbar (500 Torr) Unterdruck bis 0,10 bar (1,5 psig) Überdruck mit einem Inertgas wie Stickstoff, Argon oder einem Stickstoff-Wasserstoff-Gemisch (maximal 3 %) aufgefüllt, und die Aufheizung beginnt.
- Doppelte Abpumpzyklen werden oft als vorteilhaft empfunden, um die Gesamtzykluszeit zu verkürzen. Nach dem Erreichen des Sollwerts und dem Eintauchen in die Temperatur wird der Kühlzyklus eingeleitet.
Merkmale des Vakuumofens
KinTek-Vakuumöfen bieten eine präzise Temperaturregelung, eine hervorragende Temperaturgleichmäßigkeit und eine breite Palette von Anwendungen für Labore, Universitäten und alle kleineren Produktionsanwendungen, die Industrieöfen verwenden.
Jeder Standard- und kundenspezifische Vakuumofen bietet die folgenden Merkmale und Vorteile:
- Ausgezeichnete Temperaturgenauigkeit und -gleichmäßigkeit
- Energieeffiziente Keramikfaserisolierung
- Sicherheitsfunktion mit automatischer Abschaltung
Kundenspezifische Vakuumöfen
Holen Sie sich einen Hochtemperatur-Vakuumofen, der speziell auf Ihre Anwendungsanforderungen zugeschnitten ist. Die erfahrenen und sachkundigen Vertreter von KinTek können Ihnen bei der Entwicklung oder dem Bau eines kundenspezifischen Ofens helfen, der Ihren genauen Spezifikationen oder Anwendungsanforderungen entspricht.
Diese umfassende Palette an Funktionen und Optionen gewährleistet, dass unsere Vakuumöfen die Effizienz und Flexibilität bieten, die für eine Vielzahl von Labor- und kleinen Produktionsanwendungen erforderlich sind.
Präzise Temperaturregelung
Entdecken Sie, wie das elektrische Regelsystem von Vakuum-Induktionsschmelzöfen eine präzise Temperaturregelung während des gesamten Schmelzprozesses gewährleistet. Informieren Sie sich über die Rolle des Kühlsystems bei der Aufrechterhaltung optimaler Schmelztemperaturen und der Vermeidung von Oxidation.
Induktionserwärmung ist ein Verfahren, bei dem induzierte Wirbelströme leitfähige Materialien erhitzen. Diese Erwärmung kann zum Schmelzen von Metallen und zur Herstellung von Legierungen verwendet werden. Das Vakuum-Induktionsschmelzen bietet eine attraktive Kombination aus einer kontrollierten Atmosphäre (Vakuum oder Inertgas) und einer präzisen Kontrolle des Schmelzprozesses.
Beschreibung des Vakuum-Sinterofens
Ein Vakuumsinterofen ist ein Ofentyp, in dem erhitzte Gegenstände in einer Vakuumumgebung gesintert werden. Dieser Ofen ist in verschiedenen industriellen Prozessen, insbesondere in der Pulvermetallurgie, von entscheidender Bedeutung.
Der Sinterprozess ist sehr empfindlich gegenüber Temperaturschwankungen. Eine Abweichung von nur wenigen Grad Celsius kann sich erheblich auf die Qualität des Endprodukts auswirken. Daher ist eine strenge Kontrolle der Sintertemperatur unabdingbar, wobei die Abweichungen in der Regel einen festgelegten Bereich von ±3℃ bis ±5℃ nicht überschreiten.
Vorteile von Vakuum-Induktionsanlagen
Im Vergleich zu herkömmlichen Schmelzverfahren bieten Vakuum-Induktionsanlagen erhebliche Vorteile bei der Prozesssteuerung. Dank des Fortschritts in der Computertechnologie verfügen moderne Vakuuminduktionsöfen über intelligente Steuersysteme, die den Betrieb rationalisieren, die Arbeitskosten senken und die Präzision erhöhen.
Zukünftige Entwicklungen bei intelligenten Steuerungssystemen werden die Möglichkeiten von Vakuuminduktionsanlagen weiter verbessern. Diese Systeme werden eine präzise Steuerung der Schmelztemperaturen ermöglichen, die automatische Zugabe von Legierungen in vorgegebenen Intervallen erleichtern und den gesamten Schmelzprozess rationalisieren. Darüber hinaus wird die Integration einer umfassenden Datenerfassung und Echtzeitanalyse die Bediener in die Lage versetzen, fundierte Entscheidungen zu treffen und die Prozessparameter während des Schmelzens zu optimieren.
Komponenten des Vakuum-Induktionsschmelzofens
Der Vakuum-Induktionsschmelzofen besteht aus mehreren wesentlichen Komponenten, darunter:
- Vakuum-Ofenkörper: Er bildet die Kammer, in der das Schmelzen unter Vakuum oder kontrollierter Atmosphäre stattfindet.
- Mittelfrequenz-Leistung: Liefert die für die Induktionserwärmung erforderliche Energie.
- Vakuum-System: Hält das gewünschte Vakuumniveau in der Ofenkammer aufrecht.
- Kühlsystem: Verhindert Überhitzung und sorgt für optimale Schmelztemperaturen.
- Elektrisches Kontrollsystem: Ermöglicht eine präzise Temperaturregelung und den Gesamtbetrieb des Ofens.
Hauptmerkmale und Vorteile
- Präzise Temperaturregelung: Das elektrische Regelsystem sorgt für eine präzise Regulierung der Schmelztemperaturen, wodurch die Qualität und Konsistenz des Endprodukts verbessert wird.
- Gasentnahme: Durch die Vakuumumgebung werden Gase aus den geschmolzenen Metallen entfernt, wodurch eine schnelle Oxidation verhindert und die Integrität der Legierung bewahrt wird.
- Flexible Chargengrößen: Die Vakuumöfen sind in verschiedenen Größen erhältlich und eignen sich für eine Reihe von Chargengrößen, von kleinen bis hin zu größeren industriellen Anwendungen.
- Zentrales Kühlsystem: Das Kühlsystem leitet die Wärme effizient ab, hält die Betriebstemperaturen stabil und verlängert die Lebensdauer der Anlage.
Zusammenfassend lässt sich sagen, dass Vakuum-Induktionsschmelzöfen unvergleichliche Präzision und Kontrolle bei Metallschmelzprozessen bieten. Durch den Einsatz fortschrittlicher Technologien und intelligenter Steuerungssysteme ermöglichen diese Öfen eine effiziente Produktion, gewährleisten die Produktqualität und ebnen den Weg für künftige Fortschritte in der metallurgischen Verarbeitung.
Arbeitsprinzip und historische Bedeutung
Entdecken Sie die historischen Wurzeln der Vakuum-Induktionsschmelztechnologie und verfolgen Sie ihre Ursprünge in der Luft- und Raumfahrt sowie in der Metallurgie. Erfahren Sie, wie sich diese Technologie zu einem Eckpfeiler bei der Herstellung von Hochleistungslegierungen für verschiedene Anwendungen entwickelt hat.
Vakuum-Induktionsschmelzen: Ein Weg zu fortschrittlichen Materialien
Das Vakuum-Induktionsschmelzen (VIM) ist eine Schlüsseltechnologie im Bereich der Metallurgie, insbesondere bei der Herstellung von speziellen und exotischen Legierungen. Ursprünglich für die Verarbeitung von Superlegierungen entwickelt, hat sich das Anwendungsspektrum auf nichtrostende Stähle und verschiedene andere Metalle erweitert. Diese Ausweitung ist vor allem auf die steigende Nachfrage nach modernen Werkstoffen in verschiedenen Branchen zurückzuführen.
Das Vakuum-Induktions-Schmelzverfahren
Im Mittelpunkt des VIM steht das Prinzip des Schmelzens von Metallen unter Vakuumbedingungen, wobei die elektromagnetische Induktion als primäre Energiequelle dient. Der Prozess beinhaltet die Erzeugung elektrischer Wirbelströme im Metall, die durch eine Induktionsspule mit Wechselstrom unterstützt werden. Diese Ströme wiederum bewirken eine Erwärmung, die letztlich zum Schmelzen der Metallladung führt.
Die rasche Entwicklung der VIM-Technologie hat ihre Wurzeln in der Suche der Luft- und Raumfahrtindustrie nach Hochtemperaturlegierungen. Diese für die Luft- und Raumfahrt, für Raketen und Atomenergieanlagen unverzichtbaren Werkstoffe erforderten Innovationen bei den Schmelzverfahren. VIM-Öfen boten sich als Lösung an, da sie das Schmelzen von Legierungen auf Nickel-, Eisen- und Kobaltbasis unter Vakuumbedingungen ermöglichen. Diese Umgebung reduziert effektiv das Vorhandensein von Lückenelementen wie O2, N2 und H2 und gewährleistet die Entfernung von nichtmetallischen Einschlüssen und schädlichen Verunreinigungen wie Pb, Bi, Sb, Cu, Sn und Te.
Anwendungen des Vakuum-Induktionsschmelzens
Die Vielseitigkeit des VIM erstreckt sich auf verschiedene Anwendungen in der Metallurgie:
- Raffinieren von hochreinen Metallen und Legierungen.
- Herstellung von Elektroden für Umschmelzprozesse.
- Herstellung von Vorlegierungsstäben, die bei Verfahren wie dem Feinguss unerlässlich sind.
- Gießen von kritischen Komponenten für Flugzeugtriebwerke.
Historische Entwicklung
Die Anfänge des Vakuum-Induktionsschmelzens gehen auf das Jahr 1920 zurück, als der erste Prototyp entwickelt wurde. Im Wesentlichen nutzt das VIM die elektromagnetische Induktion, um Wirbelströme in Leitern zu induzieren und dadurch das Metall zu erwärmen und zu schmelzen. Im Laufe der Jahrzehnte hat diese Technologie sowohl in der Luft- und Raumfahrt als auch in der Nuklearindustrie unentbehrliche Dienste geleistet und die Fortschritte in der Materialwissenschaft und -technik vorangetrieben.
Zusammenfassend lässt sich sagen, dass das Vakuum-Induktionsschmelzen ein Beweis für den menschlichen Erfindungsreichtum ist und die Herstellung von Materialien ermöglicht, die moderne technische Wunderwerke antreiben. Von seinen bescheidenen Anfängen bis zu seinem heutigen Status als Eckpfeiler der metallurgischen Innovation prägt das VIM weiterhin die Landschaft der modernen Werkstoffherstellung.
Branchenübergreifende Anwendungen
Entdecken Sie die vielfältigen Anwendungen der Vakuum-Induktionsschmelztechnologie in der Luft- und Raumfahrt, der Elektronik, der Energiewirtschaft und vielen anderen Bereichen. Erfahren Sie, wie diese Technologie die Eigenschaften und die Qualität von Werkstoffen verbessert, die für die moderne Technik und Fertigung unerlässlich sind.
Die Technologie des Vakuum-Induktionsschmelzens (VIM) hat sich erheblich weiterentwickelt. Ursprünglich für die Verarbeitung spezieller und exotischer Legierungen entwickelt, wird sie heute immer häufiger eingesetzt, da fortschrittliche Materialien eine breitere Anwendung finden. Ursprünglich für Werkstoffe wie Superlegierungen eingesetzt, hat VIM seinen Nutzen auf rostfreie Stähle und verschiedene andere Metalle erweitert.
Die rasche Entwicklung der VIM-Technologie steht in engem Zusammenhang mit der Nachfrage nach Hochtemperaturlegierungen in Branchen wie Luft- und Raumfahrt, Raketen und Atomenergieanlagen. Superlegierungen, die für diese Anwendungen entscheidend sind, profitieren in hohem Maße von den Möglichkeiten der VIM-Öfen.
Wie Vakuum-Induktionsöfen funktionieren
In einem Vakuum-Induktionsofen wird das Material unter Vakuum chargiert, und es wird Energie zugeführt, um die Charge zu schmelzen. Um die gewünschte Schmelzkapazität zu erreichen, werden weitere Chargen zugeführt, und das geschmolzene Metall wird unter Vakuumbedingungen veredelt. Dieses Verfahren ermöglicht eine präzise Einstellung der Schmelzchemie, bis die gewünschte Zusammensetzung erreicht ist.
Vorteile des Vakuum-Induktionsschmelzens
-
Hohe Reinheit und Qualität: VIM zeichnet sich durch die Herstellung hochreiner und hochwertiger Materialien aus. Durch die Vakuumumgebung wird das Risiko einer Verunreinigung durch Sauerstoff, Stickstoff und andere in der Atmosphäre vorhandene Gase ausgeschlossen. Das Ergebnis ist eine sauberere, homogenere Schmelze ohne schädliche Einschlüsse und Verunreinigungen, die die mechanischen Eigenschaften beeinträchtigen könnten.
-
Kontrollierte Atmosphäre: In der Vakuumkammer wird die Atmosphäre streng kontrolliert, wobei nur bestimmte Gase bei präzisen Drücken zugeführt werden. Dieses Maß an Kontrolle ermöglicht eine genaue Steuerung der chemischen Zusammensetzung des geschmolzenen Materials und verhindert unerwünschte Oxidation oder Reaktionen mit Umgebungsgasen.
Vakuum-Induktionsschmelzöfen sind von zentraler Bedeutung im Bereich der Vakuum-Metallurgie und spielen eine wichtige Rolle bei der Herstellung von Legierungen und Spezialstählen, die für die Luft- und Raumfahrt, Raketen, Atomenergieanlagen und die Elektronikindustrie von entscheidender Bedeutung sind. Ein beträchtlicher Teil der Produkte in diesen Sektoren wird mit der VIM-Technologie hergestellt.
Verschiedene Werkstoffe, darunter Edelstahl, hitzebeständiger Stahl, ultrahochfester Stahl, Werkzeugstahl, Lagerstahl, magnetische Werkstoffe, elastische Legierungen und Ausdehnungslegierungen, werden in Vakuum-Induktionsschmelzöfen geschmolzen, um optimale Leistung und Qualität zu gewährleisten. Diese Öfen verbessern die Warmumformbarkeit und die mechanischen Eigenschaften von Superlegierungen auf Nickel-, Kobalt- und Eisenbasis, was sie für fortschrittliche Konstruktions- und Fertigungsprozesse unverzichtbar macht.
Vorteile gegenüber herkömmlichen Verfahren
Die Vakuum-Induktionsschmelztechnologie zeichnet sich aufgrund ihrer zahlreichen Vorteile gegenüber herkömmlichen Verfahren als erstklassige Methode zum Schmelzen von Metallen aus. Vergleicht man ihre Effizienz, Nachhaltigkeit und Materialreinheit mit konventionellen Verfahren, so wird deutlich, warum das Vakuum-Induktionsschmelzen in verschiedenen Branchen immer beliebter wird.
Energieeffizienz und Umweltverträglichkeit
Die Technologie des Vakuum-Induktionsschmelzens (VIM) stellt im Vergleich zu herkömmlichen Schmelzverfahren einen bedeutenden Fortschritt in Bezug auf Energieeffizienz und Umweltverträglichkeit dar. Im Gegensatz zu konventionellen Verfahren arbeitet VIM in einer Vakuumumgebung, was Wärmeverluste minimiert und den Energieverbrauch senkt. Diese effiziente Energienutzung senkt nicht nur die Produktionskosten, sondern trägt auch zu einem umweltfreundlicheren Herstellungsprozess bei, indem Kohlenstoffemissionen und Energieverschwendung reduziert werden.
Materialreinheit und Qualität
Einer der wichtigsten Vorteile von VIM ist die Fähigkeit, Materialien von außergewöhnlicher Reinheit und Qualität herzustellen. Die Vakuumumgebung schließt die Anwesenheit von Sauerstoff, Stickstoff und anderen Gasen aus, die das geschmolzene Metall verunreinigen könnten. Infolgedessen erzeugt VIM sauberere und homogenere Schmelzen, die frei von schädlichen Verunreinigungen und Einschlüssen sind. Diese Reinheit verbessert die mechanischen Eigenschaften und die Gesamtleistung der entstehenden Werkstoffe und macht sie für verschiedene Anwendungen sehr begehrt.
Kontrollierte Atmosphäre
In der Vakuumkammer der VIM-Anlagen wird die Atmosphäre genauestens kontrolliert, so dass Gaszusammensetzung und Druck präzise geregelt werden können. Indem nur bestimmte Gase bei exaktem Druck eingeleitet werden, gewährleistet VIM eine strenge Kontrolle über die chemische Zusammensetzung des geschmolzenen Materials und minimiert das Risiko unerwünschter Oxidation oder Reaktionen mit Umgebungsgasen. Dieses Maß an Kontrolle ist entscheidend für die Herstellung von Legierungen mit gleichbleibenden Eigenschaften und die Minimierung von Materialverlusten.
Prozesseffizienz und -flexibilität
Neben den Vorteilen für Umwelt und Qualität bietet VIM eine unübertroffene Prozesseffizienz und -flexibilität. Die schnellen Erwärmungszyklen und die gleichmäßige Erwärmung der Metallchargen erhöhen die Produktionsraten erheblich und reduzieren gleichzeitig die Fehlerquote. Darüber hinaus ermöglicht die Vielseitigkeit des VIM das mühelose Schmelzen verschiedener Metalle und Legierungen, was einen schnellen Wechsel zwischen verschiedenen Materialien und bei Bedarf eine sofortige Abschaltung ermöglicht. Diese Flexibilität in der Produktion steigert die betriebliche Effizienz und die Anpassungsfähigkeit an sich ändernde Produktionsanforderungen.
Anwendung und Zukunftsaussichten
Die weit verbreitete Anwendung der Vakuum-Induktionsschmelztechnologie in allen Industriezweigen unterstreicht ihr immenses Potenzial und ihre Vielseitigkeit. Von der experimentellen Forschung im kleinen Maßstab bis hin zur industriellen Großproduktion hat VIM seine Effektivität und Zuverlässigkeit unter Beweis gestellt. Der einfache Betrieb und die schnellen Schmelztemperaturen machen es zu einer bevorzugten Wahl für Hersteller, die Präzision und Beständigkeit in ihren Produktionsprozessen suchen. Im Zuge des technologischen Fortschritts ist zu erwarten, dass sich die Anwendung von VIM weiter ausbreiten und die Innovation und Effizienz von Metallschmelz- und Raffinationsprozessen vorantreiben wird.
Vakuum-Sintern: Steigerung von Effizienz und Qualität
Neben dem Vakuum-Induktionsschmelzen erweist sich das Vakuumsintern als ein weiteres wichtiges Verfahren zur Steigerung der Effizienz und Produktqualität bei der Metallherstellung. Durch das Sintern von Metallpulvern bei Temperaturen unterhalb des Schmelzpunktes in einer Vakuumumgebung bietet das Vakuumsintern mehrere Vorteile. Es schließt Reaktionen zwischen Metallen und Gasen aus, verbessert die Verdichtung und senkt die Sintertemperaturen, wodurch Energie gespart und die Lebensdauer der Sinteröfen verlängert wird. Das Ergebnis ist die Herstellung hochwertiger Metallprodukte mit verbesserten mechanischen Eigenschaften und geringerem Energieverbrauch.
Zusammenfassend lässt sich sagen, dass das Vakuuminduktionsschmelzen und das Vakuumsintern hochmoderne Technologien sind, die zahlreiche Vorteile gegenüber herkömmlichen Schmelzverfahren bieten. Von Energieeffizienz und Materialreinheit bis hin zu Prozessflexibilität und Umweltverträglichkeit treiben diese fortschrittlichen Verfahren Innovationen voran und verändern die Landschaft der Metallherstellung. Da die Industrie weiterhin auf Nachhaltigkeit und Qualität Wert legt, wird die Einführung vakuumbasierter Verfahren wie VIM und Vakuumsintern beschleunigt und eine neue Ära der Effizienz und Exzellenz in der Metallproduktion eingeläutet.
Hauptmerkmale von Vakuum-Induktionsschmelzöfen
Vakuum-Induktionsschmelzöfen sind in metallurgischen Prozessen von zentraler Bedeutung und bieten ein Spektrum an Funktionen, die auf eine präzise Steuerung und verbesserte Produktivität zugeschnitten sind. Im Folgenden finden Sie eine umfassende Übersicht über ihre wichtigsten Komponenten und Fortschritte:
Strukturelle Komponenten
Der Ofen besteht aus einem luftdichten, wassergekühlten Stahlmantel, der so konstruiert ist, dass die erforderlichen Vakuumbedingungen während der Verarbeitung aufrechterhalten werden. Innerhalb dieses Gehäuses wird das Metall in einem Tiegel geschmolzen, der sich in einer wassergekühlten Induktionsspule befindet. Außerdem ist das Innere des Ofens in der Regel mit feuerfesten Materialien ausgekleidet, die extremen Temperaturen standhalten.
Prozessverbesserungen
1. Kontrolle der Umgebung
- Das Gießen von Metallschmelzen kann unter Vakuum oder Inertgas durchgeführt werden, wodurch optimale Bedingungen für die Legierungsbildung und die Aufrechterhaltung der Reinheit gewährleistet werden.
2. Zusätzliche Merkmale
- Die Öfen können Kipp- und Gießmechanismen, Gießkammern und Probenentnahmeöffnungen enthalten, um unterschiedliche Produktionsanforderungen zu erfüllen.
- Formenhandhabungseinrichtungen ermöglichen eine automatische oder halbautomatische Verarbeitung, manchmal mit Vakuumverriegelungssystemen für einen nahtlosen Betrieb.
Zukünftige Entwicklungstrends
Die Entwicklung von Vakuum-Induktionsschmelzanlagen spiegelt den Übergang zu multifunktionalen Strukturen wider, die sich für verschiedene technologische Prozesse eignen. Es ist absehbar, dass modulare Konfigurationen dominieren werden, die maßgeschneiderte Kombinationen von Komponenten ermöglichen, um spezifische Prozessanforderungen effizient zu erfüllen.
Präzisionssteuerung und Automatisierung
Die Integration fortschrittlicher Technologien wie Computersysteme und intelligente Signalerfassung ermöglicht eine präzise Prozesssteuerung. Freundliche Mensch-Maschine-Schnittstellen rationalisieren den Betrieb, reduzieren die Arbeitskosten und erhöhen die betriebliche Einfachheit.
Zusatzsysteme
Neben den Kernkomponenten spielen auch Hilfssysteme wie Stromversorgungen, Steuereinheiten und Kühlsysteme eine wichtige Rolle. Diese Systeme stellen die Energiezufuhr für das Schmelzen sicher und verhindern die Überhitzung kritischer Komponenten.
Strukturelle Überlegungen
Um eine Vakuumentladung zu verhindern, ist eine sorgfältige Bauweise von größter Bedeutung. Die Isolierung aller geladenen Körper innerhalb des Ofenmantels und die Beseitigung scharfer Kanten in der Induktorenkonstruktion sind entscheidend, um einen unterbrechungsfreien Betrieb zu gewährleisten.
Die wichtigsten Vorteile
- Schmelzen von bestimmten Titanlegierungen: Die Vakuumbedingungen ermöglichen das Schmelzen von Titanlegierungen und erweitern damit die Einsatzmöglichkeiten des Ofens.
- Vermeidung von chemischen Reaktionen: Die Vakuumumgebung schützt geschmolzene Metalle und Legierungen vor unerwünschten chemischen Reaktionen mit nichtmetallischen Einschlüssen.
- Beseitigung von schädlichen Gasen: Der Vakuumzustand erleichtert die Beseitigung von schädlichen gelösten Gasen und Schadstoffen aus der flüssigen Metallschmelze und gewährleistet so die Reinheit des Materials.
Zusammenfassend lässt sich sagen, dass Vakuum-Induktionsschmelzöfen Vielseitigkeit und Präzision verkörpern und durch innovatives Design und technologische Integration den Fortschritt in metallurgischen Prozessen vorantreiben.
Vorteile für Umwelt und Leistung
Das Vakuum-Induktionsschmelzen (VIM) bietet signifikante Umwelt- und Leistungsvorteile, die es zu einer bevorzugten Methode für die Herstellung hochreiner Materialien mit hervorragenden Eigenschaften machen.
Hohe Reinheit und Qualität
VIM zeichnet sich durch die Herstellung von Materialien von außergewöhnlicher Reinheit und Qualität aus. Durch den Betrieb in einer Vakuumumgebung eliminiert VIM das Risiko einer Verunreinigung durch atmosphärische Gase wie Sauerstoff und Stickstoff. Dies gewährleistet eine sauberere und homogenere Schmelze ohne schädliche Einschlüsse und Verunreinigungen, die die mechanische Integrität des Materials beeinträchtigen könnten. Folglich weisen die entstehenden Legierungen verbesserte mechanische Eigenschaften und Leistungsmerkmale auf.
Kontrollierte Atmosphäre
In der Vakuumkammer wird die Atmosphäre genauestens kontrolliert, so dass Gaszusammensetzung und Druck präzise geregelt werden können. Diese Kontrolle ist von entscheidender Bedeutung, um die gewünschte chemische Zusammensetzung des geschmolzenen Materials zu erreichen und gleichzeitig unerwünschte Oxidation oder Reaktionen mit Umgebungsgasen zu verhindern. Dadurch ermöglicht VIM die Herstellung von Materialien mit gleichbleibenden chemischen Eigenschaften und minimaler Reaktivität, was eine hervorragende Leistung in verschiedenen Anwendungen gewährleistet.
Vorteile im Überblick
Die Vorteile des Einsatzes eines Vakuum-Induktionsschmelzofens sind vielfältig:
-
Eliminierung von Gasen: VIM arbeitet unter extrem niedrigem Druck, typischerweise bei 0,000001 Atmosphäre. Diese Umgebung erleichtert die Beseitigung unerwünschter Gase und flüchtiger Elemente aus den Rohstoffen während des Schmelzprozesses und gewährleistet die Herstellung hochreiner Legierungen.
-
Präzise chemische Analyse: Das Fehlen einer Atmosphäre in der Vakuumkammer ermöglicht eine außergewöhnliche und reproduzierbare Kontrolle der chemischen Zusammensetzung der geschmolzenen Materialien. Diese Präzision ermöglicht die Herstellung von Legierungen mit maßgeschneiderten Zusammensetzungen und gewünschten Eigenschaften, was die Effizienz des Gesamtprozesses und die Produktqualität verbessert.
-
Überlegene Prozesskontrolle: VIM bietet eine unabhängige Steuerung von Druck, Temperatur und induktivem Rühren und damit eine unvergleichliche Prozesskontrolle. Diese Flexibilität ermöglicht die Entwicklung optimierter Schmelzverfahren, die auf die jeweilige Legierungszusammensetzung abgestimmt sind und die Leistung und Konsistenz der hergestellten Materialien weiter verbessern.
Zusätzlich zu den Vorteilen für die Umwelt erstrecken sich die Vorteile eines Vakuum-Induktionsofens auch auf die Verarbeitung verschiedener Metalle und Legierungen:
- Reinheitsverbesserung: Das Fehlen von Luft- und Schlackenverschmutzung in Vakuum-Induktionsöfen trägt zur Herstellung relativ reiner Legierungen mit hohem Leistungsniveau bei.
- Gasentfernung: Der Betrieb unter Vakuumbedingungen ermöglicht die Reduzierung des Gasgehalts im geschmolzenen Stahl und in den Legierungen, was zu Materialien mit niedrigeren Gaskonzentrationen und verbesserten Eigenschaften führt.
- Verhinderung von Oxidation: Die Verarbeitung von Metallen in einer Vakuumumgebung mindert das Oxidationsrisiko und bewahrt die Integrität des verarbeiteten Materials.
- Verdampfung von Verunreinigungen: Verunreinigungen wie Blei (Pb) und Wismut (Bi) können in einem Vakuum leichter verdampfen, was die Reinigung des Materials während des Schmelzprozesses erleichtert.
Zusammengefasst,Vakuum-Induktionsschmelzöfen eine umfassende Lösung für die Herstellung hochreiner Werkstoffe mit hervorragenden Leistungsmerkmalen, die gleichzeitig die Umweltverschmutzung eindämmen und die Effizienz des Prozesses gewährleisten.
Kontaktieren Sie uns für eine kostenlose Beratung
Die Produkte und Dienstleistungen von KINTEK LAB SOLUTION werden von Kunden auf der ganzen Welt anerkannt. Unsere Mitarbeiter helfen Ihnen gerne bei allen Fragen weiter. Kontaktieren Sie uns für eine kostenlose Beratung und sprechen Sie mit einem Produktspezialisten, um die am besten geeignete Lösung für Ihre Anwendungsanforderungen zu finden!