Thermische Behandlungsverfahren, wie sie in PECVD-Anlagen (Plasma-Enhanced Chemical Vapor Deposition) zum Einsatz kommen, unterscheiden sich erheblich je nach Art der Plasmaerzeugung und der Wechselwirkung zwischen dem Plasma und dem Substrat.Die drei wichtigsten Arten der Wärmebehandlung bei der PECVD sind die direkte PECVD, induktiv gekoppelte Plasmareaktoren und ferngesteuerte Plasmareaktoren.Jede Methode hat ihre eigenen Merkmale, z. B. wie das Plasma erzeugt wird, wie es mit dem Substrat interagiert und wie hoch das Kontaminationsrisiko ist.Das Verständnis dieser Unterschiede ist entscheidend für die Auswahl der geeigneten Anlage für bestimmte Anwendungen, wie z. B. Antireflexionsbeschichtungen auf Solarzellen.
Die wichtigsten Punkte erklärt:
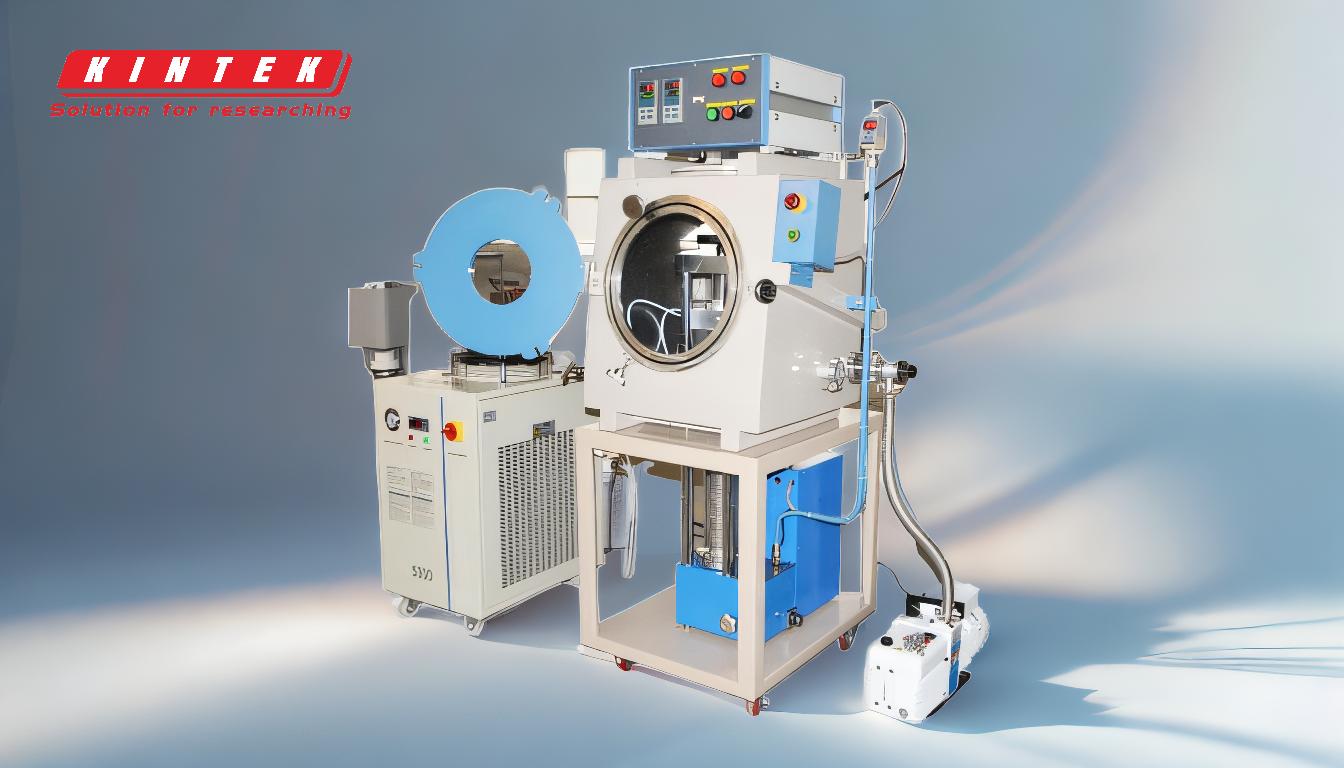
-
Direkte PECVD-Reaktoren:
- Plasmaerzeugung:Direkte PECVD-Reaktoren verwenden ein kapazitiv gekoppeltes Plasma, bei dem das Plasma in direktem Kontakt mit dem Substrat steht.
- Wechselwirkung mit dem Substrat:Der direkte Kontakt ermöglicht eine effiziente Energieübertragung und Abscheidung dünner Schichten.
- Kontaminationsrisiko:Höheres Kontaminationsrisiko aufgrund der direkten Wechselwirkung zwischen dem Plasma und dem Substrat.
- Anwendungen:Wird häufig bei Anwendungen eingesetzt, die eine präzise und effiziente Dünnschichtabscheidung erfordern, z. B. bei Antireflexionsbeschichtungen auf Solarzellen.
-
Induktiv gekoppelte Plasmareaktoren:
- Plasmaerzeugung:In induktiv gekoppelten Plasmareaktoren befinden sich die Elektroden außerhalb der Reaktionskammer und erzeugen das Plasma durch induktive Kopplung.
- Wechselwirkung mit dem Substrat:Das Plasma steht nicht in direktem Kontakt mit dem Substrat, was das Kontaminationsrisiko verringert.
- Kontaminationsrisiko:Geringeres Kontaminationsrisiko im Vergleich zu direkten PECVD-Reaktoren.
- Anwendungen:Geeignet für Anwendungen, bei denen die Kontaminationskontrolle von entscheidender Bedeutung ist, wie z. B. bei der Halbleiterherstellung.
-
Ferngesteuerte Plasma-Reaktoren:
- Plasmaerzeugung:Ferngesteuerte Plasmareaktoren erzeugen das Plasma in einer separaten Kammer und transportieren es dann in die Substratkammer.
- Wechselwirkung mit dem Substrat:Das Substrat ist dem Plasmaerzeugungsprozess nicht ausgesetzt, wodurch die Kontamination minimiert wird.
- Kontaminationsrisiko:Geringstes Kontaminationsrisiko unter den drei Typen.
- Anwendungen:Ideal für hochsensible Prozesse, bei denen Verunreinigungen minimiert werden müssen, wie z. B. in der modernen Mikroelektronik.
-
Prozessgase und Plasma-Interaktion:
- Verwendete Gase:Zu den üblichen Prozessgasen gehören Silan und Ammoniak, die im Reaktor zu Plasma ionisiert werden.
- Eigenschaften des Plasmas:Das Plasma ist chemisch reaktiv und erleichtert die Abscheidung von dünnen Schichten auf Substraten wie Siliziumchips.
- Rolle bei Anwendungen:Unverzichtbar für die Herstellung von Antireflexionsbeschichtungen auf Solarzellenchips, die deren Effizienz erhöhen.
-
Überlegungen zur Geräteauswahl:
- Kontaminationskontrolle:Wählen Sie induktiv gekoppelte oder ferngesteuerte Plasmareaktoren für Anwendungen, die eine geringe Kontamination erfordern.
- Effizienz und Präzision:Direkte PECVD-Reaktoren werden bevorzugt für Anwendungen eingesetzt, die eine hochpräzise und effiziente Abscheidung von Dünnschichten erfordern.
- Anwendungsspezifische Erfordernisse:Berücksichtigen Sie die spezifischen Anforderungen der Anwendung, z. B. die Notwendigkeit von Antireflexionsbeschichtungen oder fortschrittlichen Halbleitereigenschaften.
Das Verständnis dieser Unterschiede hilft bei der Auswahl der richtigen PECVD-Anlage für spezifische Anforderungen an die thermische Behandlung, um optimale Leistung und minimale Kontaminationsrisiken zu gewährleisten.
Zusammenfassende Tabelle:
Typ | Erzeugung von Plasma | Wechselwirkung mit dem Substrat | Kontaminationsrisiko | Anwendungen |
---|---|---|---|---|
Direkte PECVD-Reaktoren | Kapazitiv gekoppeltes Plasma in direktem Kontakt mit dem Substrat. | Effiziente Energieübertragung und Abscheidung von dünnen Schichten. | Höheres Kontaminationsrisiko durch direkte Wechselwirkung. | Antireflexionsbeschichtungen auf Solarzellen. |
Induktiv gekoppelte Plasmareaktoren | Elektroden außerhalb der Kammer erzeugen Plasma durch induktive Kopplung. | Kein direkter Kontakt des Plasmas mit dem Substrat, wodurch die Kontamination verringert wird. | Geringeres Kontaminationsrisiko im Vergleich zur direkten PECVD. | Halbleiterherstellung. |
Ferngesteuerte Plasmareaktoren | Das Plasma wird in einer separaten Kammer erzeugt und zur Substratkammer transportiert. | Das Substrat ist der Plasmabildung nicht ausgesetzt, was die Kontamination minimiert. | Geringstes Kontaminationsrisiko unter den drei Typen. | Fortschrittliche Mikroelektronik. |
Benötigen Sie Hilfe bei der Auswahl der richtigen PECVD-Anlage für Ihre Anforderungen? Kontaktieren Sie unsere Experten noch heute!