Diamantähnliche Beschichtungen (DLC) werden mit Hilfe fortschrittlicher Abscheidetechniken aufgebracht, vor allem durch physikalische Gasphasenabscheidung (PVD) und chemische Gasphasenabscheidung (CVD).Bei diesen Verfahren wird eine dünne, dauerhafte Schicht aus diamantartigem Kohlenstoff (DLC) auf der Oberfläche von Werkzeugen oder Bauteilen erzeugt.Bei der PVD-Beschichtung wird ein Ausgangsmaterial verdampft und auf dem Werkzeug kondensiert, so dass eine Monoschicht aus DLC entsteht, die in der Regel 0,5 bis 2,5 Mikrometer dick ist.Beim CVD-Verfahren hingegen werden Wasserstoff- und Methangase in einer Kammer verwendet, in der Wolframdrähte, die auf über 2.300 °C erhitzt werden, die Gase aufspalten, so dass sich die Kohlenstoffatome rekombinieren und eine reine Diamantschicht auf der Werkzeugoberfläche bilden können.Beide Methoden erfordern eine präzise Steuerung von Temperatur, Druck und Gaszusammensetzung, um optimale Ergebnisse zu erzielen.
Die wichtigsten Punkte werden erklärt:
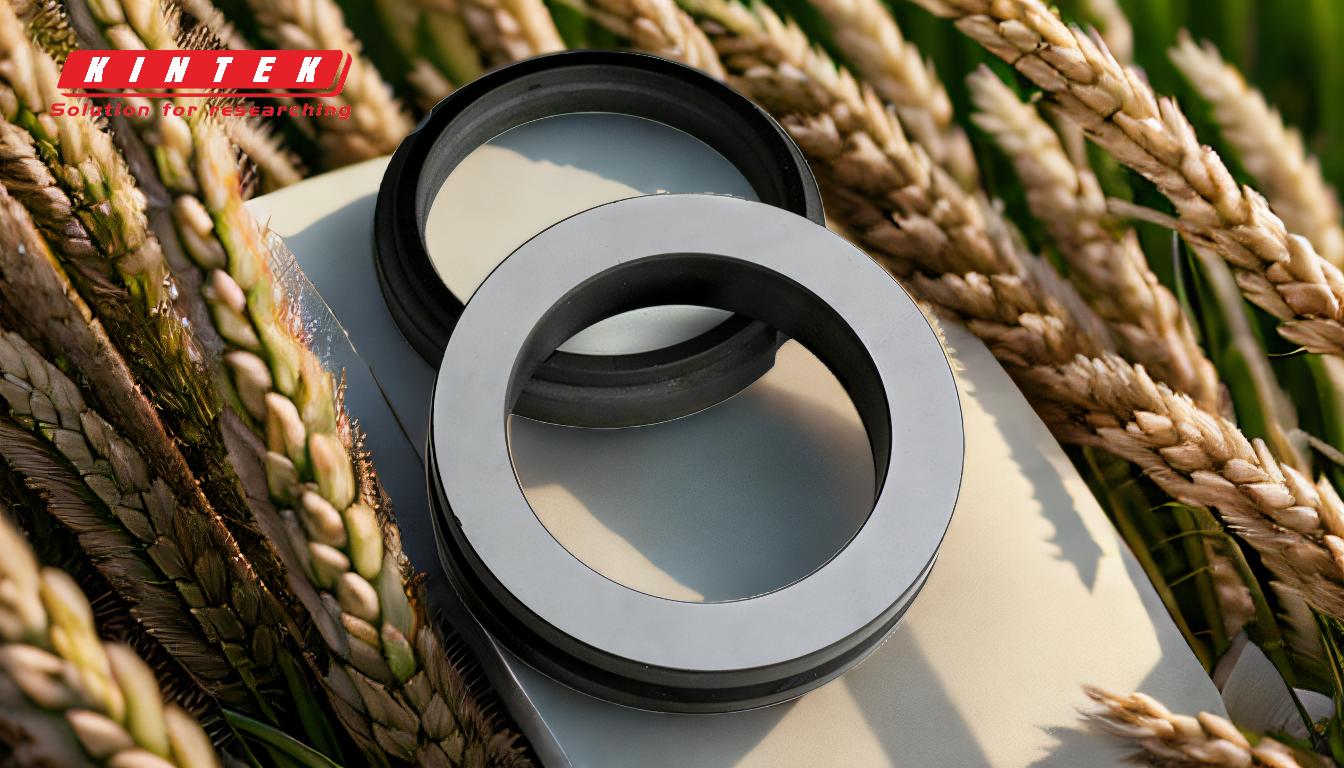
-
Überblick über diamantähnliche Beschichtungen (DLC):
- DLC-Beschichtungen sind dünne, harte und verschleißfeste Schichten, die auf Werkzeuge oder Bauteile aufgetragen werden, um deren Leistung und Langlebigkeit zu verbessern.
- Diese Beschichtungen sind amorph, d. h. sie haben keine kristalline Struktur, aber sie weisen ähnliche Eigenschaften wie Diamant auf, z. B. hohe Härte und geringe Reibung.
-
Primäre Beschichtungsmethoden:
-
Physikalische Gasphasenabscheidung (PVD):
- PVD ist eine weit verbreitete Methode zum Aufbringen von DLC-Beschichtungen.
- Bei diesem Verfahren wird ein Ausgangsmaterial (häufig auf Kohlenstoffbasis) in einer Vakuumkammer verdampft.
- Das verdampfte Material kondensiert dann auf der Oberfläche des Werkzeugs und bildet eine dünne, gleichmäßige Schicht aus DLC.
- Die Schichtdicke beträgt in der Regel zwischen 0,5 und 2,5 Mikrometer.
- PVD ist bekannt für seine Fähigkeit, qualitativ hochwertige, haftende Beschichtungen mit hervorragender Verschleißfestigkeit zu erzeugen.
-
Chemische Gasphasenabscheidung (CVD):
- CVD ist eine weitere gängige Methode zum Aufbringen von DLC-Schichten.
- Bei diesem Verfahren wird das Werkzeug in eine mit Wasserstoff und Methangas gefüllte Kammer gestellt.
- Wolframdrähte, die auf über 2.300 °C erhitzt werden, liefern die nötige Energie, um die Gasmoleküle aufzuspalten.
- Die aktivierten Kohlenstoffatome rekombinieren dann auf der Oberfläche des Werkzeugs und bilden eine reine Diamantschicht.
- CVD ist besonders effektiv für die Herstellung dickerer, haltbarerer Schichten.
-
Physikalische Gasphasenabscheidung (PVD):
-
Verfahrensschritte für das Aufbringen von DLC-Beschichtungen:
-
Vorbereitung:
- Das zu beschichtende Werkzeug oder Bauteil muss gründlich gereinigt und vorbereitet werden, damit die Beschichtung gut haftet.
- Dies beinhaltet häufig die Entfernung von Oberflächenverunreinigungen wie Ölen oder Oxiden durch chemische oder mechanische Mittel.
-
Einlegen in die Kammer:
- Die vorbereiteten Werkzeuge werden in die Beschichtungskammer geladen.
- Bei der PVD-Beschichtung wird die Kammer evakuiert, um ein Vakuum zu erzeugen, während bei der CVD-Beschichtung die Kammer mit den entsprechenden Gasen gefüllt wird.
-
Abscheidung:
- Bei der PVD wird das Ausgangsmaterial verdampft, und der Dampf kondensiert auf der Oberfläche des Werkzeugs.
- Beim CVD-Verfahren werden die Gase aktiviert, und die Kohlenstoffatome lagern sich auf dem Werkzeug ab.
-
Abkühlung und Endbearbeitung:
- Nach der Beschichtung lassen wir die beschichteten Werkzeuge langsam abkühlen, um thermische Spannungen zu vermeiden.
- Die fertige Beschichtung wird auf Qualität, Dicke und Haftung geprüft.
-
Vorbereitung:
-
Wichtige Parameter und Überlegungen:
-
Temperatur:
- Sowohl PVD- als auch CVD-Verfahren erfordern hohe Temperaturen, die je nach Verfahren zwischen 750°C und über 2.300°C liegen.
- Eine ordnungsgemäße Temperaturkontrolle ist entscheidend für die Qualität und Haftung der Beschichtung.
-
Gaszusammensetzung:
- Bei der CVD muss die Zusammensetzung der Wasserstoff- und Methangase sorgfältig kontrolliert werden, um die gewünschte Kohlenstoffabscheidung zu erreichen.
-
Dicke der Beschichtung:
- Die Dicke der DLC-Beschichtung ist ein entscheidender Faktor bei der Bestimmung ihrer Leistungsfähigkeit.
- Dickere Beschichtungen bieten zwar eine bessere Verschleißfestigkeit, können aber auch anfälliger für Risse oder Delaminationen sein.
-
Adhäsion:
- Die Gewährleistung einer starken Haftung zwischen der Beschichtung und dem Substrat ist für die Haltbarkeit der Beschichtung entscheidend.
- Dies erfordert häufig eine Vorbehandlung des Substrats oder die Verwendung von Zwischenschichten.
-
Temperatur:
-
Anwendungen von DLC-Beschichtungen:
- DLC-Beschichtungen werden in einer Vielzahl von Branchen eingesetzt, u. a. in der Automobilindustrie, der Luft- und Raumfahrt, in medizinischen Geräten und Schneidwerkzeugen.
- Sie werden besonders wegen ihrer Fähigkeit geschätzt, die Reibung zu verringern, dem Verschleiß zu widerstehen und die Lebensdauer von Komponenten zu verlängern, die rauen Bedingungen ausgesetzt sind.
-
Vorteile und Beschränkungen:
-
Vorteile:
- Hohe Härte und Verschleißfestigkeit.
- Niedriger Reibungskoeffizient, der den Energieverbrauch reduziert und die Effizienz verbessert.
- Ausgezeichnete Korrosionsbeständigkeit.
- Fähigkeit, komplexe Geometrien zu beschichten.
-
Beschränkungen:
- Hohe Kosten für Ausrüstung und Verfahren.
- Begrenzte Dicke aufgrund der Gefahr von Eigenspannungen und Rissen.
- Erfordert eine genaue Kontrolle der Prozessparameter.
-
Vorteile:
-
Zukünftige Trends:
- Die laufende Forschung konzentriert sich auf die Verbesserung der Haftung, Dicke und Einheitlichkeit von DLC-Beschichtungen.
- Es wird erwartet, dass Fortschritte in der Nanotechnologie und hybride Beschichtungsmethoden die Leistung und Anwendbarkeit von DLC-Beschichtungen in verschiedenen Branchen weiter verbessern werden.
Wenn die Käufer von Geräten und Verbrauchsmaterialien diese Schlüsselpunkte verstehen, können sie fundierte Entscheidungen über die Anwendung von diamantähnlichen Beschichtungen treffen und sicherstellen, dass sie die für ihre spezifischen Bedürfnisse am besten geeignete Methode und Parameter auswählen.
Zusammenfassende Tabelle:
Aspekt | Einzelheiten |
---|---|
Primäre Methoden | PVD (Physikalische Gasphasenabscheidung), CVD (Chemische Gasphasenabscheidung) |
Dicke der Beschichtung | 0,5 bis 2,5 Mikrometer (PVD), dicker für CVD |
Wichtige Parameter | Temperatur (750°C bis 2.300°C), Gaszusammensetzung, Adhäsion, Schichtdicke |
Anwendungen | Automobilindustrie, Luft- und Raumfahrt, medizinische Geräte, Schneidwerkzeuge |
Vorteile | Hohe Härte, geringe Reibung, Korrosionsbeständigkeit, komplexe Geometrien |
Beschränkungen | Hohe Kosten, begrenzte Schichtdicke, präzise Parametersteuerung erforderlich |
Optimieren Sie Ihre Werkzeuge mit modernen DLC-Beschichtungen - Kontaktieren Sie noch heute unsere Experten für maßgeschneiderte Lösungen!