Heißpressen ist ein Herstellungsverfahren, bei dem Wärme und Druck kombiniert werden, um Materialien, in der Regel Keramik oder Metalle, zu verdichten und in Strukturen mit nahezu theoretischer Dichte zu formen.Dabei wird pulverförmiges Material in eine Matrize gegeben, mit einachsigem Druck (10-30 MPa) beaufschlagt und gleichzeitig auf Sintertemperaturen erhitzt.Diese Methode beschleunigt die Verdichtung, verkürzt die Verarbeitungszeit und verbessert die Materialeigenschaften im Vergleich zum herkömmlichen Kaltpressen und Sintern.Das Verfahren umfasst Schritte wie das Einfüllen des Pulvers, das Absaugen von Verunreinigungen, das Erhitzen zum Schmelzen des Pulvers, das Ausüben von Druck zum Verschmelzen des Materials und das Abkühlen zum Verfestigen des Endprodukts.Das Heißpressen eignet sich besonders gut für die Herstellung von Materialien mit hoher Dichte, hoher Leistung und minimalen Fehlern.
Die wichtigsten Punkte werden erklärt:
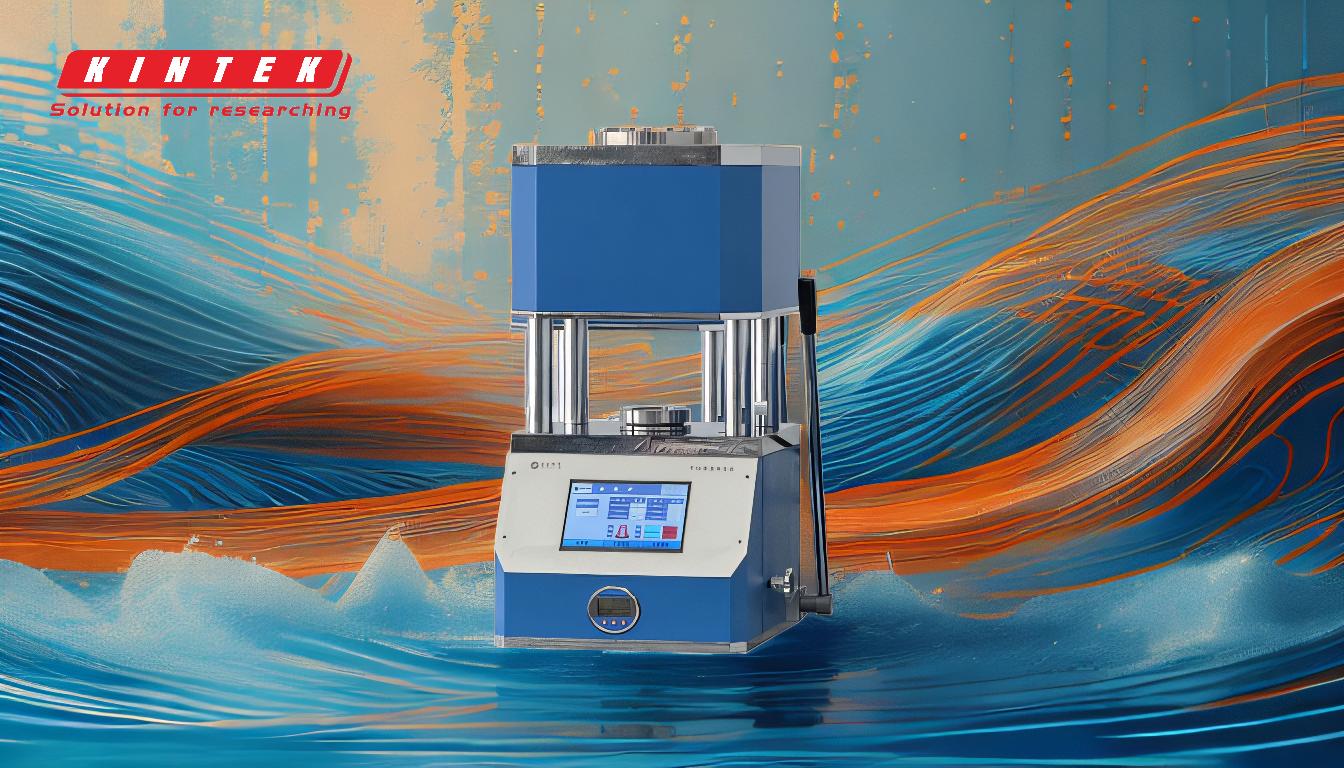
-
Gleichzeitige Anwendung von Wärme und Druck:
- Beim Heißpressen werden Hitze und Druck in einem einzigen Schritt kombiniert, im Gegensatz zu herkömmlichen Verfahren, bei denen Pressen und Sintern getrennt voneinander ablaufen.Durch diese gleichzeitige Anwendung wird die Zeit, die für Phasenwechsel und Legierungsbildung benötigt wird, erheblich verkürzt.
- Bei diesem Verfahren wird pulverförmiges Material in eine Graphitmatrize gegeben und gleichzeitig mit Hitze und Druck beaufschlagt.Dadurch wird sichergestellt, dass sich das Material gleichmäßig verdichtet und nahezu die theoretische Dichte erreicht.
-
Uniaxialer Druck:
- Ein einachsiger Druck von 10-30 MPa wird durch eine einfach geformte Matrize ausgeübt.Dieser Druck trägt dazu bei, das Pulver zu verdichten und die Verdichtungsrate zu erhöhen.
- Der ausgeübte Druck trägt dazu bei, die Porosität zu verringern und die mechanischen Eigenschaften des Endprodukts zu verbessern, so dass es dichter und fester wird.
-
Schritte beim Heißpressen:
- Aufladen:Das Keramik- oder Metallpulver wird in den Ofen oder die Matrize gefüllt.
- Vakuumieren:Der Ofen wird evakuiert, um ein Vakuum zu erzeugen, das Gase und Verunreinigungen entfernt, die andernfalls zu Mängeln im Endprodukt führen könnten.
- Heizung:Die Temperatur wird auf die Sintertemperatur angehoben, wodurch die Pulverteilchen schmelzen und sich verbinden können.
- Druckbeaufschlagung:Durch Druck werden die Pulverpartikel zu einer dichten, festen Struktur verschmolzen.
- Abkühlung:Das Material wird allmählich auf Raumtemperatur abgekühlt, um die Struktur zu verfestigen und thermische Spannungen zu vermeiden.
-
Vorteile gegenüber traditionellen Methoden:
- Reduzierte Bearbeitungszeit:Durch die Kombination von Pressen und Sintern verkürzt das Heißpressen die Gesamtbearbeitungszeit im Vergleich zum herkömmlichen Kaltpressen und Sintern erheblich.
- Verbesserte Materialeigenschaften:Die gleichzeitige Anwendung von Hitze und Druck führt zu Materialien mit höherer Dichte, besseren mechanischen Eigenschaften und weniger Fehlern.
- Nahezu theoretische Dichte:Durch das Heißpressen kann das Material eine Dichte nahe dem theoretischen Maximum erreichen, was mit anderen Verfahren nur schwer möglich ist.
-
Anwendungen:
- Das Heißpressen ist bei der Herstellung von Hochleistungskeramik, modernen Verbundwerkstoffen und Spezialmetallen weit verbreitet.Es ist besonders nützlich in Branchen, in denen Materialien mit hoher Festigkeit, Verschleißfestigkeit und thermischer Stabilität erforderlich sind.
- Zu den üblichen Anwendungen gehören Komponenten für die Luft- und Raumfahrt, Schneidwerkzeuge und elektronische Substrate.
-
Umweltbedingungen:
- Das Heißpressen kann im Vakuum oder unter einem Überdruck von Inertgas durchgeführt werden.Diese Umgebung verhindert Oxidation und andere chemische Reaktionen, die die Qualität des Materials beeinträchtigen könnten.
- Die Verwendung eines Vakuums oder Inertgases hilft auch dabei, Restgase oder Verunreinigungen aus dem Pulver zu entfernen, was die Qualität des Endprodukts weiter verbessert.
-
Überlegungen zum Material:
- Die Wahl des Materials für die Matrize (in der Regel Graphit) ist entscheidend, da es hohen Temperaturen und Drücken standhalten muss, ohne sich zu verformen oder mit dem Pulver zu reagieren.
- Das verwendete Pulver muss eine gleichmäßige Partikelgrößenverteilung aufweisen, um eine gleichmäßige Verdichtung zu gewährleisten und Fehler im Endprodukt zu vermeiden.
Wenn man diese Schlüsselpunkte versteht, kann man die Effizienz und Effektivität des Heißpressens bei der Herstellung hochwertiger, dichter Materialien mit hervorragenden Eigenschaften schätzen.Diese Methode ist besonders vorteilhaft für Industrien, die Materialien mit außergewöhnlichen mechanischen und thermischen Eigenschaften benötigen.
Zusammenfassende Tabelle:
Hauptaspekt | Einzelheiten |
---|---|
Prozess | Kombiniert Hitze und Druck, um Keramik oder Metalle zu verdichten. |
Druck | Uniaxialer Druck von 10-30 MPa. |
Schritte | Aufladen, Vakuumieren, Erhitzen, Unterdrucksetzen, Abkühlen. |
Vorteile | Geringere Verarbeitungszeit, verbesserte Materialeigenschaften, nahezu theoretische Dichte. |
Anwendungen | Bauteile für die Luft- und Raumfahrt, Schneidwerkzeuge, elektronische Substrate. |
Umgebung | Wird im Vakuum oder unter Inertgas durchgeführt, um Oxidation zu verhindern. |
Überlegungen zum Material | Graphitstempel, gleichmäßige Partikelgrößenverteilung für Pulver. |
Entdecken Sie, wie Heißpressen Ihre Materialproduktion verbessern kann. Kontaktieren Sie uns noch heute für fachkundige Beratung!