Die Temperatur spielt im Schmiedeprozess eine entscheidende Rolle und beeinflusst die Bearbeitbarkeit, die Mikrostruktur und die endgültigen mechanischen Eigenschaften des Materials. Beim Schmieden wird Metall mithilfe von Druckkräften geformt. Die Temperatur, bei der dies geschieht, bestimmt die Leichtigkeit der Verformung, die Bildung von Fehlern und die Qualität des Schmiedeteils. Höhere Temperaturen machen Metalle im Allgemeinen formbarer und verringern die zum Formen erforderliche Kraft. Übermäßige Hitze kann jedoch zu Kornwachstum, Oxidation oder sogar zum Schmelzen führen. Umgekehrt kann das Schmieden bei niedrigeren Temperaturen zu einer höheren Festigkeit führen, aber auch zu Rissen oder unvollständiger Formgebung führen. Um das gewünschte Gleichgewicht zwischen Formbarkeit und mechanischen Eigenschaften zu erreichen, ist es wichtig, den optimalen Schmiedetemperaturbereich für bestimmte Materialien zu kennen.
Wichtige Punkte erklärt:
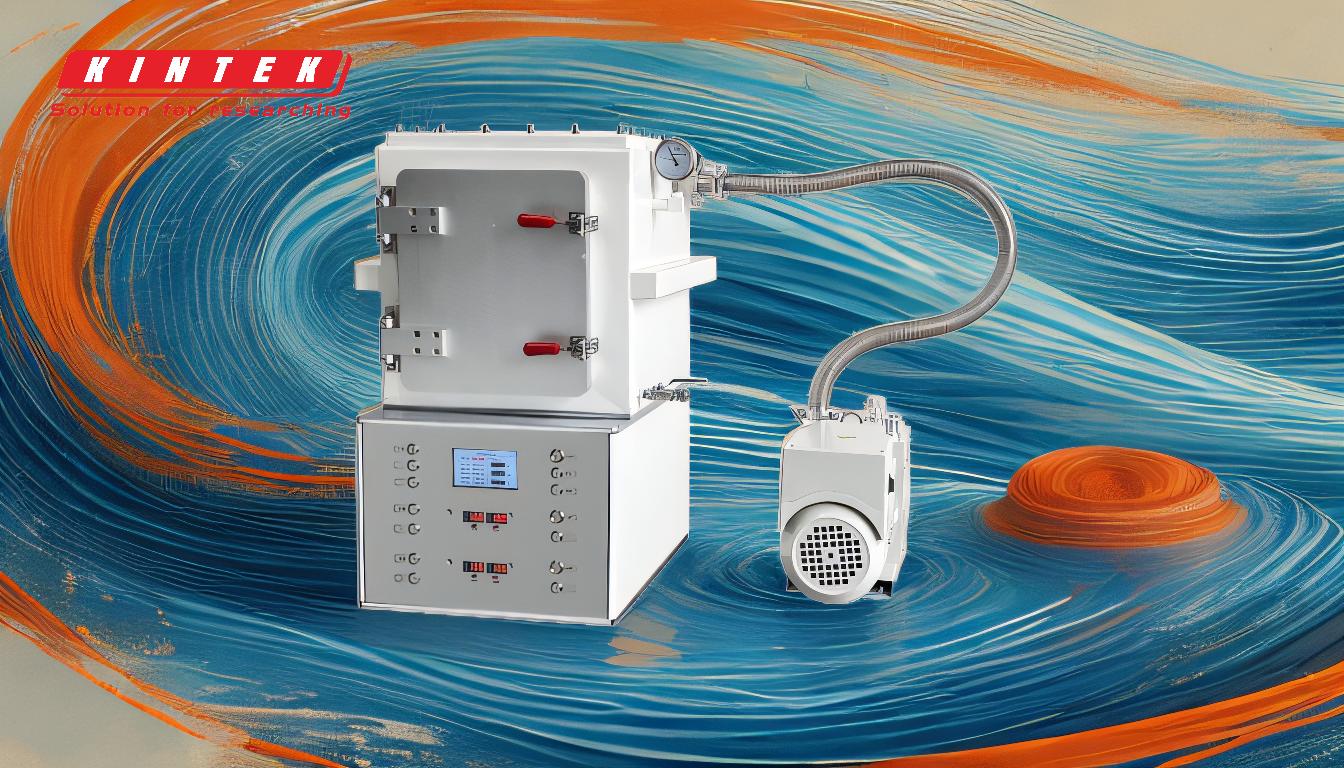
-
Temperatur- und Materialverarbeitbarkeit:
- Mit zunehmender Temperatur werden Metalle duktiler und lassen sich leichter formen. Dies liegt daran, dass höhere Temperaturen die Streckgrenze des Materials verringern, sodass es sich unter Druckkräften leichter verformen kann.
- Das Schmieden bei erhöhten Temperaturen (Warmschmieden) ist bei Materialien wie Stahl, Aluminium und Titan üblich, da es das Risiko von Rissen minimiert und eine gleichmäßige Verformung gewährleistet.
- Kaltschmieden, das bei oder nahe Raumtemperatur durchgeführt wird, wird für Materialien verwendet, die ohne Erhitzen eine ausreichende Duktilität aufweisen, wie z. B. bestimmte Aluminiumlegierungen. Allerdings erfordert das Kaltschmieden höhere Kräfte und kann zu einer Kaltverfestigung führen.
-
Mikrostrukturelle Veränderungen:
- Die Temperatur beeinflusst die Mikrostruktur des Metalls beim Schmieden erheblich. Warmschmieden fördert die dynamische Rekristallisation, bei der sich neue, spannungsfreie Körner bilden, wodurch die Zähigkeit und Duktilität des Materials verbessert wird.
- Bei zu hohen Temperaturen kann es zu übermäßigem Kornwachstum und damit zu einer Schwächung des Materials kommen. Umgekehrt kann das Schmieden bei einer zu niedrigen Temperatur zu einer unvollständigen Rekristallisation führen, was zu Eigenspannungen und verringerten mechanischen Eigenschaften führt.
-
Oxidation und Oberflächenqualität:
- Hohe Temperaturen beim Schmieden können zu Oxidation führen und eine Zunderschicht auf der Metalloberfläche bilden. Dieser Zunder muss entfernt werden, um ein sauberes Finish zu gewährleisten, kann aber auch zu Materialverlust und Maßungenauigkeiten führen.
- Eine ordnungsgemäße Temperaturkontrolle und Schutzatmosphären können die Oxidation minimieren und so die Oberflächenqualität und Maßgenauigkeit des Schmiedeteils bewahren.
-
Wärmeausdehnung und Maßgenauigkeit:
- Metalle dehnen sich bei Erwärmung aus und diese Wärmeausdehnung muss beim Schmiedeprozess berücksichtigt werden. Überhitzung kann zu einer übermäßigen Ausdehnung führen, wodurch es schwierig wird, präzise Abmessungen zu erreichen.
- Eine genaue Temperaturregelung sorgt dafür, dass das Schmiedeteil gleichmäßig abkühlt, die Dimensionsstabilität erhalten bleibt und das Risiko von Verformungen oder Verformungen verringert wird.
-
Energieeffizienz und Prozessoptimierung:
- Höhere Schmiedetemperaturen reduzieren den Kraftaufwand für die Verformung und machen den Prozess energieeffizienter. Eine übermäßige Erwärmung kann jedoch zu Energieverschwendung und erhöhten Betriebskosten führen.
- Die Optimierung des Schmiedetemperaturbereichs für bestimmte Materialien und Anwendungen gewährleistet ein Gleichgewicht zwischen Energieeffizienz, Materialeigenschaften und Produktionskosten.
-
Materialspezifische Temperaturbereiche:
- Verschiedene Metalle haben unterschiedliche Schmiedetemperaturbereiche. Beispielsweise wird Stahl typischerweise zwischen 950 °C und 1250 °C geschmiedet, während Aluminiumlegierungen bei niedrigeren Temperaturen (etwa 350 °C bis 500 °C) geschmiedet werden.
- Das Überschreiten des empfohlenen Temperaturbereichs kann zum Schmelzen oder unerwünschten Phasenänderungen führen, während das Schmieden unterhalb des Bereichs zu unzureichender Verformung und schlechten mechanischen Eigenschaften führen kann.
-
Wärmebehandlung nach dem Schmieden:
- Auch die Temperatur beim Schmieden beeinflusst die Notwendigkeit nachfolgender Wärmebehandlungen. Geschmiedete Teile müssen möglicherweise geglüht, abgeschreckt oder angelassen werden, um die gewünschte Härte, Festigkeit und Zähigkeit zu erreichen.
- Durch die richtige Temperaturkontrolle während des Schmiedens wird sichergestellt, dass sich das Material in einem optimalen Zustand für die Nachbehandlungen befindet, wodurch die Leistung des Endprodukts verbessert wird.
Zusammenfassend lässt sich sagen, dass die Temperatur ein entscheidender Faktor beim Schmieden ist und sich auf alles auswirkt, von der Bearbeitbarkeit des Materials und der Mikrostruktur bis hin zur Oberflächenqualität und Maßgenauigkeit. Durch sorgfältige Steuerung der Schmiedetemperatur können Hersteller hochwertige Teile mit den gewünschten mechanischen Eigenschaften herstellen und gleichzeitig Fehler und Energieverbrauch minimieren. Um den Schmiedeprozess zu optimieren und konsistente Ergebnisse zu erzielen, ist es wichtig, die Temperaturanforderungen für bestimmte Materialien und Anwendungen zu verstehen.
Übersichtstabelle:
Aspekt | Einfluss der Temperatur |
---|---|
Materialverarbeitbarkeit | Höhere Temperaturen erhöhen die Duktilität und verringern die Verformungskraft. |
Mikrostruktur | Warmschmieden fördert die Rekristallisation; Übermäßige Hitze führt zu Kornwachstum. |
Oxidation & Oberfläche | Hohe Temperaturen verursachen Oxidation; Kontrollierte Temperaturen bewahren die Oberflächenqualität. |
Maßgenauigkeit | Die Wärmeausdehnung beeinflusst die Präzision; Eine gleichmäßige Kühlung verhindert ein Verziehen. |
Energieeffizienz | Höhere Temperaturen reduzieren die Kraft, können aber Energie verschwenden; auf Kosteneffizienz optimieren. |
Materialspezifische Bereiche | Stahl: 950°C–1250°C; Aluminium: 350°C–500°C. Bei Überschreitung der Grenzwerte besteht die Gefahr von Defekten. |
Behandlung nach dem Schmieden | Die richtigen Schmiedetemperaturen gewährleisten optimale Bedingungen zum Glühen, Abschrecken oder Anlassen. |
Benötigen Sie kompetente Beratung zur Optimierung der Schmiedetemperaturen für Ihre Materialien? Kontaktieren Sie uns noch heute um loszulegen!