Die Vakuumabscheidung ist ein vielseitiges Verfahren zur Abscheidung dünner Schichten oder Beschichtungen auf Oberflächen in einer kontrollierten Umgebung, in der Regel unter Vakuumbedingungen. Die Dicke der abgeschiedenen Schicht kann erheblich variieren und reicht von einer einzelnen Atomschicht (Nanometer) bis zu mehreren Millimetern, je nach dem spezifischen Verfahren, den Materialien und den beteiligten Parametern. Faktoren wie die Dauer des Prozesses, der Energiegehalt, die Materialeigenschaften und die Umgebungsbedingungen (z. B. Vakuumdruck, Temperatur) spielen eine entscheidende Rolle bei der Bestimmung der endgültigen Dicke und Qualität der abgeschiedenen Schicht. Diese Technik wird in vielen Branchen eingesetzt, in denen eine präzise Kontrolle der Schichteigenschaften erforderlich ist, z. B. in der Elektronik, Optik und Beschichtung.
Die wichtigsten Punkte werden erklärt:
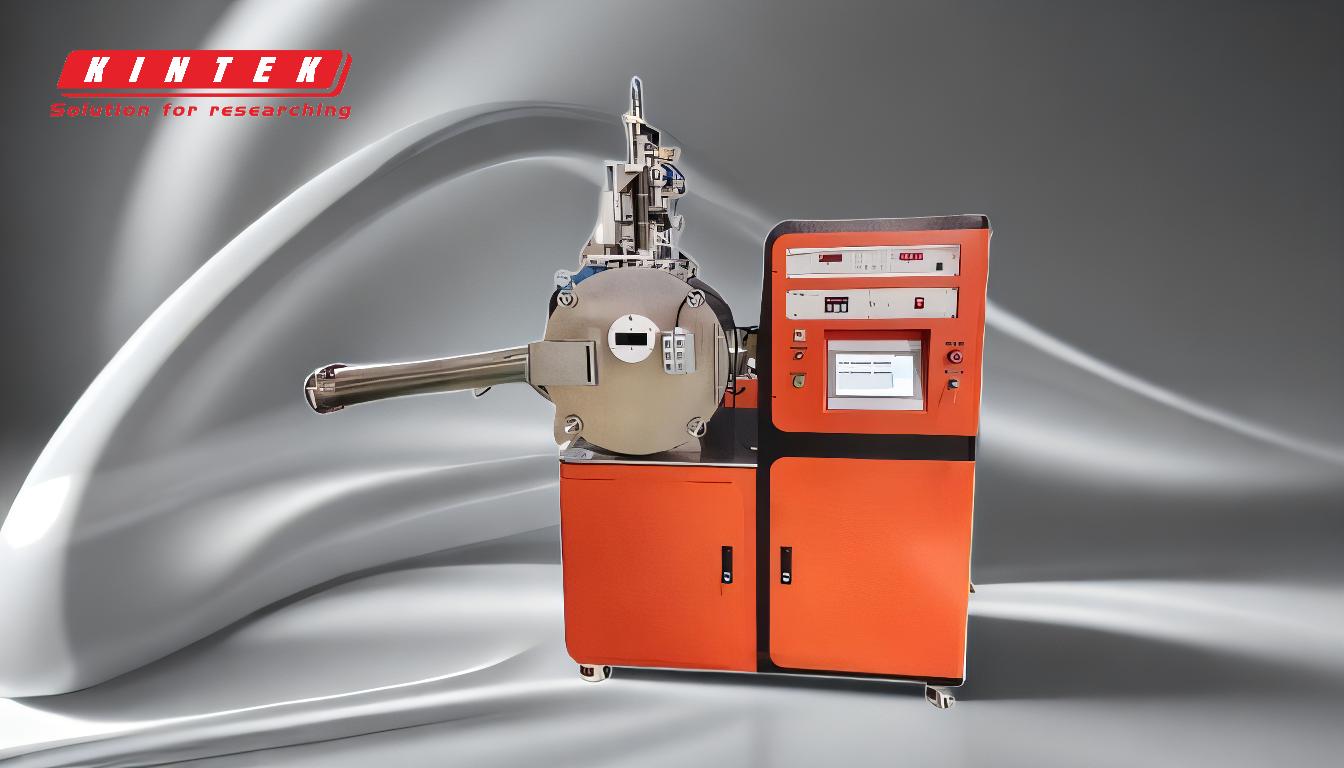
-
Dickenbereich bei der Vakuumbeschichtung:
- Durch Vakuumabscheidung können Schichten mit einer Dicke von einer einzigen Atomschicht (Nanometerbereich) bis zu mehreren Millimetern hergestellt werden.
-
Zum Beispiel:
- Atomare/molekulare Skala: Bei Verfahren wie der physikalischen Gasphasenabscheidung (PVD) oder der chemischen Gasphasenabscheidung bei niedrigem Druck (LPCVD) werden die Schichten Atom für Atom oder Molekül für Molekül abgeschieden, wodurch extrem dünne Schichten (Nanometer) entstehen.
- Makroskopische Skala: Bei einigen Anwendungen, wie z. B. Schutzschichten oder dekorativen Oberflächen, können dickere Schichten (Mikrometer bis Millimeter) aufgebracht werden.
-
Faktoren, die die Dicke beeinflussen:
-
Die Dicke der abgeschiedenen Schicht wird von mehreren Schlüsselfaktoren beeinflusst:
- Prozess Dauer: Längere Abscheidungszeiten führen im Allgemeinen zu dickeren Schichten.
- Energieniveaus: Höhere Energieniveaus von Beschichtungspartikeln (z. B. zehn bis tausende von Elektronenvolt beim Sputtern) können die Abscheideraten erhöhen und die Dicke beeinflussen.
- Materialeigenschaften: Die Masse und das Molekulargewicht des Ausgangsmaterials beeinflussen, wie schnell es verdampft oder zerstäubt, was sich auf die Dicke auswirkt.
- Unterdruck: Ein höherer Vakuumgrad verbessert den freien Weg der Ausgangsmaterialmoleküle, was zu einer gleichmäßigeren und kontrollierten Abscheidung führt.
- Vorbereitung des Substrats: Die Oberflächenrauheit und -sauberkeit des Substrats kann die Gleichmäßigkeit und Haftung der abgeschiedenen Schicht beeinflussen.
-
Die Dicke der abgeschiedenen Schicht wird von mehreren Schlüsselfaktoren beeinflusst:
-
Prozessspezifische Überlegungen:
- Sputtern: Die Dicke des beim Sputtern abgeschiedenen Metalls hängt von der Zykluszeit und der auf das Target aufgebrachten Leistung ab. Eine höhere Leistung und längere Zyklen führen zu dickeren Schichten.
- Thermische Verdampfung: Bei diesem Verfahren bestimmt die Verdampfungsrate des Ausgangsmaterials zusammen mit dem Vakuumdruck und der Rotationsgeschwindigkeit des Substrats die Dicke und Gleichmäßigkeit der Schicht.
- Chemische Gasphasenabscheidung (CVD): Bei der LPCVD werden die Abscheiderate und die Schichtdicke durch die an der Substratoberfläche ablaufenden chemischen Reaktionen sowie durch die Temperatur- und Druckbedingungen beeinflusst.
-
Qualität und Leistung von Dünnschichten:
-
Die Qualität des abgeschiedenen Films ist entscheidend für seine Leistungsfähigkeit in der Anwendung. Zu den wichtigsten Faktoren, die die Qualität beeinflussen, gehören:
- Reinheit des Ausgangsmaterials: Verunreinigungen können zu Defekten in der Folie führen.
- Abscheidetemperatur und Druck: Eine ordnungsgemäße Kontrolle gewährleistet gleichmäßige und hochwertige Filme.
- Vorbereitung der Oberfläche des Substrats: Eine glatte und saubere Substratoberfläche fördert eine gleichmäßige Ablagerung und eine starke Haftung.
-
Die Qualität des abgeschiedenen Films ist entscheidend für seine Leistungsfähigkeit in der Anwendung. Zu den wichtigsten Faktoren, die die Qualität beeinflussen, gehören:
-
Anwendungen und Implikationen:
-
Die Vakuumbeschichtung wird in einer Vielzahl von Industriezweigen eingesetzt, u. a:
- Elektronik: Zur Herstellung von Dünnschichttransistoren, Halbleiterbauelementen und leitenden Schichten.
- Optik: Für Antireflexionsbeschichtungen, Spiegel und optische Filter.
- Beschichtungen: Für verschleißfeste, korrosionsbeständige und dekorative Beschichtungen.
- Die Möglichkeit, die Schichtdicke auf atomarer Ebene zu kontrollieren, macht die Vakuumabscheidung zu einer entscheidenden Technologie für die moderne Fertigung und Forschung.
-
Die Vakuumbeschichtung wird in einer Vielzahl von Industriezweigen eingesetzt, u. a:
Wenn die Käufer von Geräten und Verbrauchsmaterialien diese wichtigen Punkte kennen, können sie fundierte Entscheidungen über die Materialien und Verfahren treffen, die erforderlich sind, um bestimmte Schichtdicken und Eigenschaften für ihre Anwendungen zu erzielen.
Zusammenfassende Tabelle:
Aspekt | Einzelheiten |
---|---|
Dickenbereich | Nanometer (atomarer Maßstab) bis Millimeter (makroskopischer Maßstab) |
Schlüsselfaktoren | Prozessdauer, Energieniveaus, Materialeigenschaften, Vakuumdruck, Substratvorbereitung |
Prozess-Beispiele | Sputtern, thermische Verdampfung, chemische Gasphasenabscheidung (CVD) |
Anwendungen | Elektronik (Transistoren, Halbleiter), Optik (Spiegel, Filter), Beschichtungen (verschleißfest, dekorativ) |
Sie benötigen präzise Lösungen für die Vakuumbeschichtung? Kontaktieren Sie unsere Experten noch heute um Ihre Anforderungen zu besprechen!