Die Pulvermetallurgie (PM) ist ein vielseitiges Fertigungsverfahren mit zahlreichen Vorteilen wie Energieeffizienz, Kosteneffizienz und der Möglichkeit, komplexe Formen mit minimalem Materialabfall herzustellen.Allerdings hat es auch einige Nachteile, die seine Anwendung in bestimmten Szenarien einschränken können.Dazu gehören Größenbeschränkungen, Herausforderungen bei der Herstellung hochkomplexer Formen und eine geringere Festigkeit und Duktilität im Vergleich zu herkömmlichen Guss- oder Schmiedeverfahren.Darüber hinaus kann die Porosität von Sinterteilen deren mechanische Eigenschaften beeinträchtigen, und das Verfahren ist möglicherweise nicht für alle Materialkombinationen oder Endverwendungsanforderungen geeignet.
Die wichtigsten Punkte erklärt:
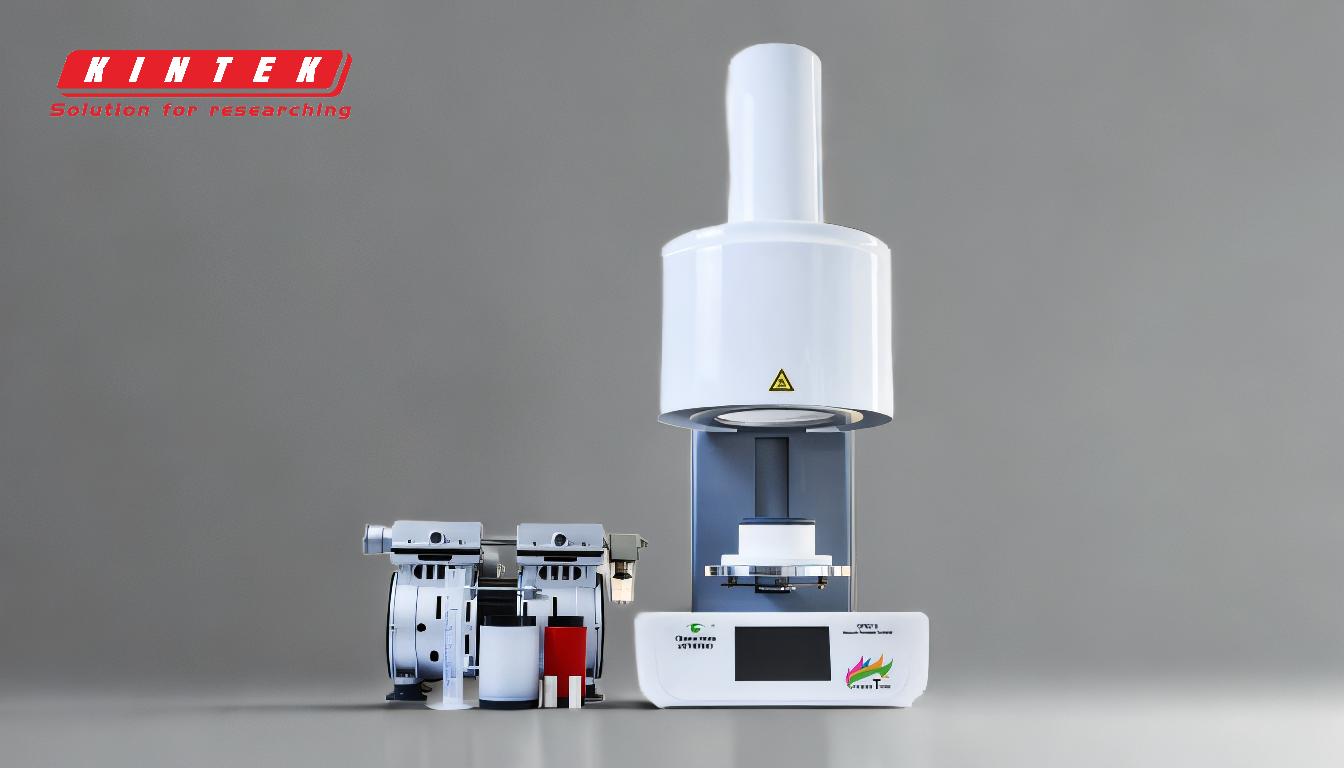
-
Größenbeschränkungen:
- Die Pulvermetallurgie wird durch die Größe der für das Verfahren verwendeten Pressen eingeschränkt.Die größten Pressen in der Industrie haben in der Regel ein Gewicht von etwa 1.500 Tonnen, was die praktische Größe der Teile auf etwa 40-50 Quadratzoll ebene Fläche begrenzt.Das macht PM ungeeignet für sehr große Bauteile, die alternative Fertigungsmethoden wie Gießen oder Schmieden erfordern.
-
Herausforderungen bei komplexen Formen:
- PM kann zwar komplizierte Formen herstellen, aber hochkomplexe Geometrien können schwierig zu realisieren sein.Erfahrene Hersteller können einige dieser Herausforderungen meistern, aber das Verfahren kann immer noch Schwierigkeiten mit Teilen haben, die extrem feine Details oder unkonventionelle Geometrien erfordern.Diese Einschränkung kann die Designflexibilität von PM-Komponenten einschränken.
-
Geringere Festigkeit und Duktilität:
- Pulvermetallurgisch hergestellte Teile haben im Allgemeinen eine geringere Festigkeit und Duktilität als Guss- oder Schmiedeteile.Dies liegt an der inhärenten Porosität von Sinterteilen, die ihre mechanischen Eigenschaften beeinträchtigen kann.Für Anwendungen, die eine hohe Festigkeit oder Zähigkeit erfordern, ist PM möglicherweise nicht die optimale Wahl.
-
Porosität und unvollständige Teile:
- Der Sinterprozess führt häufig zu porösen Strukturen, die das Endprodukt schwächen können.Außerdem kann die Pressphase die gewünschte Komplexität des Endprodukts nicht vollständig nachbilden, was zu unvollständigen oder weniger robusten Komponenten führt.Diese Porosität kann auch die Leistung des Teils in stark beanspruchten Umgebungen beeinträchtigen.
-
Grenzen des Materials:
- PM ermöglicht zwar das Mischen verschiedener Metalle und Nichtmetalle, doch nicht alle Materialkombinationen sind machbar oder ergeben die gewünschten Eigenschaften.Einige Werkstoffe lassen sich möglicherweise nicht verdichten oder effektiv sintern, was den Anwendungsbereich von PM einschränkt.Dies kann ein erheblicher Nachteil sein, wenn bestimmte Materialeigenschaften für ein Bauteil erforderlich sind.
-
Herausforderungen bei Kosten und Produktion:
- Obwohl PM im Allgemeinen kosteneffektiv ist, können die anfänglichen Einrichtungskosten für Formen, Gesenke und Ausrüstung hoch sein.Darüber hinaus kann die Herstellung von Teilen mit sehr engen Toleranzen oder einzigartigen Materialkombinationen spezielle Ausrüstung und Fachwissen erfordern, was die Komplexität der Produktion und die Kosten erhöht.
-
Umweltaspekte:
- PM gilt zwar aufgrund des geringen Materialabfalls (97 % des Materials werden Teil des Endprodukts) als umweltfreundlich, aber das Verfahren kann dennoch energieintensive Schritte wie das Sintern beinhalten.Dies kann einen Teil der Umweltvorteile zunichte machen, insbesondere wenn die verwendete Energie nicht aus erneuerbaren Quellen stammt.
Zusammenfassend lässt sich sagen, dass die Pulvermetallurgie zwar erhebliche Vorteile in Bezug auf Kosten, Effizienz und Materialvielfalt bietet, ihre Nachteile - wie Größenbeschränkungen, geringere mechanische Eigenschaften und Herausforderungen bei komplexen Formen - bei der Auswahl eines Herstellungsverfahrens jedoch sorgfältig berücksichtigt werden müssen.Aufgrund dieser Einschränkungen ist PM eher für spezifische Anwendungen geeignet als eine Einheitslösung.
Zusammenfassende Tabelle:
Benachteiligung | Beschreibung |
---|---|
Größenbeschränkungen | Begrenzt durch die Größe der Presse; Teile typischerweise ≤ 40-50 sq in, was PM für große Komponenten ungeeignet macht. |
Herausforderungen bei komplexen Formen | Schwierig, hochkomplexe Geometrien zu realisieren; schränkt die Designflexibilität ein. |
Geringere Festigkeit und Duktilität | Teile haben im Vergleich zu Guss- oder Schmiedeteilen geringere mechanische Eigenschaften. |
Porosität und unvollständige Teile | Die Sinterung führt zu porösen Strukturen, die das Endprodukt schwächen. |
Einschränkungen bei den Materialien | Nicht alle Materialkombinationen sind machbar, was die Vielseitigkeit der Anwendungen einschränkt. |
Kosten und Produktionsherausforderungen | Hohe anfängliche Einrichtungskosten und Komplexität bei engen Toleranzen oder einzigartigen Materialien. |
Umweltaspekte | Die energieintensive Sinterung kann die umweltfreundlichen Vorteile zunichte machen. |
Brauchen Sie Hilfe bei der Entscheidung, ob die Pulvermetallurgie für Ihr Projekt geeignet ist? Kontaktieren Sie noch heute unsere Experten für eine maßgeschneiderte Beratung!