Beim Aufkohlen handelt es sich um einen Wärmebehandlungsprozess, bei dem Kohlenstoff in die Oberfläche von kohlenstoffarmem Stahl eingebracht wird, um dessen Härte und Verschleißfestigkeit zu erhöhen. Es gibt fünf Hauptmethoden zum Aufkohlen, jede mit ihren einzigartigen Eigenschaften, Vorteilen und Anwendungen. Zu diesen Methoden gehören Packungsaufkohlung, Gasaufkohlung, Flüssigkeitsaufkohlung, Vakuumaufkohlung und Plasmaaufkohlung. Jede Technik unterscheidet sich hinsichtlich des zum Einbringen von Kohlenstoff verwendeten Mediums, der erforderlichen Ausrüstung und der erzielten spezifischen Ergebnisse. Das Verständnis dieser Methoden ist entscheidend für die Auswahl der am besten geeigneten Technik basierend auf den gewünschten Eigenschaften des Stahls und den spezifischen Anwendungsanforderungen.
Wichtige Punkte erklärt:
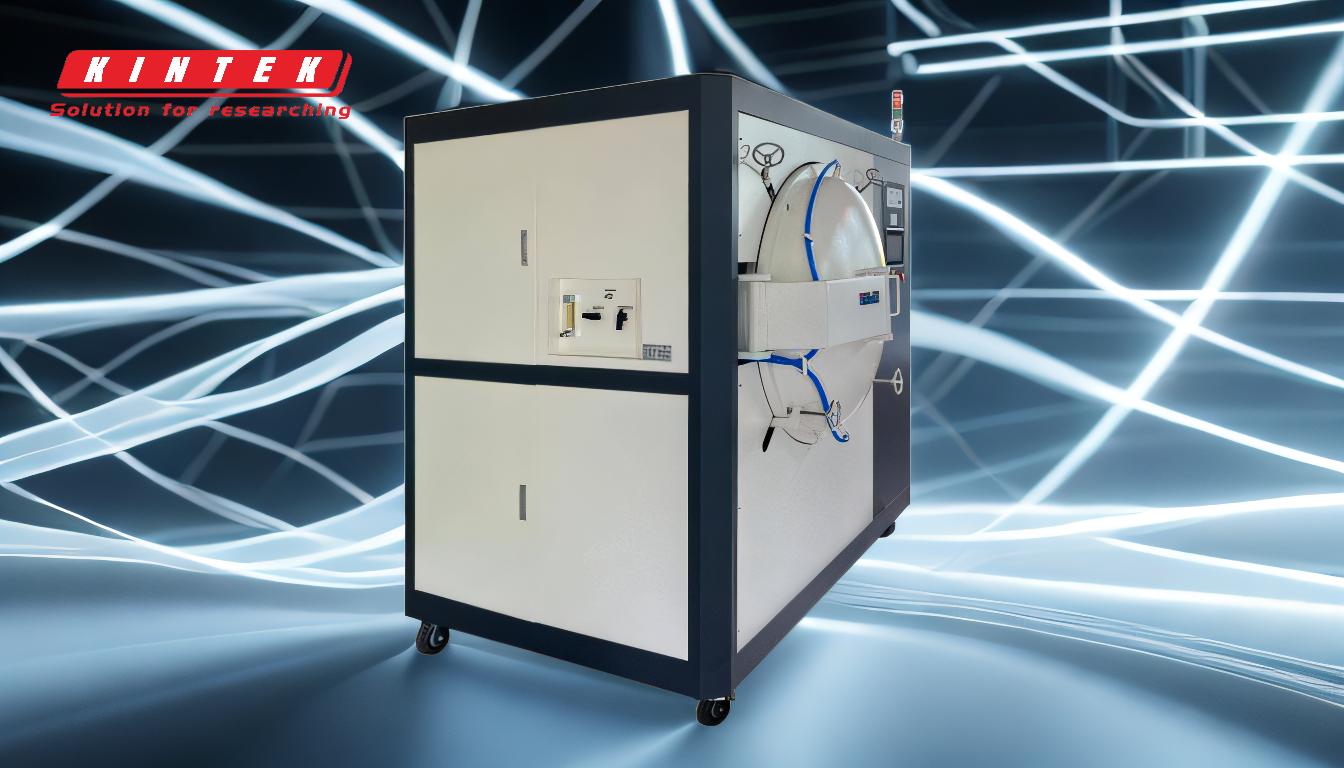
-
Packaufkohlung
- Verfahren: Beim Packaufkohlen werden die Stahlteile in einem Behälter mit einem kohlenstoffreichen Material wie Holzkohle oder Koks verpackt. Anschließend wird der Behälter in einem Ofen auf eine Temperatur zwischen 900 °C und 950 °C erhitzt, wodurch Kohlenstoff in die Stahloberfläche diffundieren kann.
- Vorteile: Diese Methode ist kostengünstig und für große Teileserien geeignet. Es sorgt für eine hohe Härtetiefe, was für Komponenten von Vorteil ist, die eine hohe Verschleißfestigkeit erfordern.
- Nachteile: Der Prozess ist zeitaufwändig und das Kohlenstoffpotenzial lässt sich nur schwer genau steuern. Darüber hinaus kann es sein, dass die Teile nach dem Prozess aufgrund des kohlenstoffreichen Verpackungsmaterials zusätzlich gereinigt werden müssen.
-
Gasaufkohlung
- Verfahren: Beim Gasaufkohlen werden die Stahlteile in einem Ofen mit einer kohlenstoffreichen Gasatmosphäre, typischerweise einer Mischung aus Methan, Propan oder Erdgas, erhitzt. Die Temperatur wird zwischen 850 °C und 950 °C gehalten, wodurch Kohlenstoff in die Stahloberfläche diffundieren kann.
- Vorteile: Diese Methode bietet im Vergleich zur Packungsaufkohlung eine bessere Kontrolle über das Kohlenstoffpotenzial und die Einsatztiefe. Außerdem ist es schneller und effizienter und eignet sich daher für die Massenproduktion.
- Nachteile: Die für die Gasaufkohlung erforderliche Ausrüstung ist komplexer und teurer. Darüber hinaus erfordert der Prozess eine sorgfältige Überwachung der Gaszusammensetzung, um konsistente Ergebnisse sicherzustellen.
-
Flüssigaufkohlung
- Verfahren: Beim Flüssigaufkohlen, auch Salzbadaufkohlen genannt, werden die Stahlteile in ein geschmolzenes Salzbad getaucht, das kohlenstoffreiche Verbindungen wie Natriumcyanid oder Kaliumcyanid enthält. Die Temperatur wird typischerweise zwischen 850 °C und 950 °C gehalten.
- Vorteile: Diese Methode sorgt für eine schnelle und gleichmäßige Erwärmung, was zu einer gleichmäßigen Härtetiefe und Kohlenstoffkonzentration führt. Es eignet sich auch für kleine und komplexe Teile.
- Nachteile: Die Verwendung von Salzen auf Cyanidbasis wirft Umwelt- und Sicherheitsbedenken auf. Darüber hinaus müssen die Teile nach dem Prozess gründlich gereinigt werden, um eventuelle Salzrückstände zu entfernen.
-
Vakuumaufkohlung
- Verfahren: Die Vakuumaufkohlung erfolgt in einem Vakuumofen, in dem die Stahlteile in einer Niederdruckumgebung auf Temperaturen zwischen 900 °C und 1050 °C erhitzt werden. Ein kohlenstoffreiches Gas wie Methan oder Propan wird in den Ofen eingeleitet, um die Kohlenstoffdiffusion zu erleichtern.
- Vorteile: Diese Methode bietet eine hervorragende Kontrolle über das Kohlenstoffpotenzial und die Härtetiefe, was zu qualitativ hochwertigen, konsistenten Ergebnissen führt. Außerdem wird das Risiko einer Oxidation und Entkohlung eliminiert, da der Prozess im Vakuum stattfindet.
- Nachteile: Die für die Vakuumaufkohlung erforderliche Ausrüstung ist teuer und der Prozess ist im Vergleich zu anderen Methoden langsamer. Es wird typischerweise für hochwertige Komponenten verwendet, bei denen Präzision und Qualität entscheidend sind.
-
Plasmaaufkohlung
- Verfahren: Beim Plasmaaufkohlen, auch Ionenaufkohlen genannt, werden die Stahlteile in eine Vakuumkammer gelegt und ein kohlenstoffreiches Gas wie Methan eingeleitet. Durch Anlegen eines elektrischen Hochspannungsfeldes wird ein Plasma erzeugt, das das Gas ionisiert und die Kohlenstoffionen in Richtung der Stahloberfläche beschleunigt.
- Vorteile: Diese Methode ermöglicht eine präzise Kontrolle des Kohlenstoffpotentials und der Einsatztiefe, was zu einer gleichmäßigen und qualitativ hochwertigen Aufkohlung führt. Im Vergleich zu herkömmlichen Methoden ist es außerdem schneller und energieeffizienter.
- Nachteile: Die für die Plasmaaufkohlung erforderliche Ausrüstung ist komplex und teuer. Darüber hinaus ist der Prozess aufgrund der Größenbeschränkungen der Vakuumkammer auf kleine und mittelgroße Teile beschränkt.
Zusammenfassend lässt sich sagen, dass die Wahl der Aufkohlungsmethode von verschiedenen Faktoren abhängt, darunter den gewünschten Eigenschaften des Stahls, der Größe und Komplexität der Teile, dem Produktionsvolumen und Kostenüberlegungen. Jede Methode hat ihre einzigartigen Vorteile und Einschränkungen, weshalb es wichtig ist, die am besten geeignete Technik basierend auf den spezifischen Anforderungen der Anwendung auszuwählen.
Übersichtstabelle:
Verfahren | Prozessübersicht | Vorteile | Nachteile |
---|---|---|---|
Packaufkohlung | Mit kohlenstoffreichem Material gefüllte Stahlteile, erhitzt auf 900–950 °C. | Kostengünstig, große Gehäusetiefe. | Zeitaufwändige und schwierige Kohlenstoffkontrolle. |
Gasaufkohlung | Stahl erhitzt in einer kohlenstoffreichen Gasatmosphäre (850–950 °C). | Bessere Kohlenstoffkontrolle, schneller für hohe Lautstärke. | Teure Ausrüstung, erfordert Gasüberwachung. |
Flüssigaufkohlung | Stahl, eingetaucht in ein geschmolzenes Salzbad mit Kohlenstoffverbindungen (850–950 °C). | Schnelle, gleichmäßige Erwärmung, ideal für Kleinteile. | Umwelt-/Sicherheitsbedenken, Nachreinigung. |
Vakuumaufkohlung | Im Vakuumofen mit kohlenstoffreichem Gas erhitzter Stahl (900–1050 °C). | Präzise Kontrolle, kein Oxidationsrisiko. | Teurer, langsamerer Prozess. |
Plasmaaufkohlung | Stahl in einer Vakuumkammer mit ionisiertem kohlenstoffreichen Gas (Plasma). | Energieeffiziente, gleichmäßige Ergebnisse. | Komplexe Ausrüstung, beschränkt auf kleine/mittlere Teile. |
Benötigen Sie Hilfe bei der Auswahl der richtigen Aufkohlungsmethode für Ihre Anwendung? Kontaktieren Sie noch heute unsere Experten !