Kaltumformung und Warmumformung sind zwei grundlegende Metallumformverfahren mit jeweils unterschiedlichen Vor- und Nachteilen. Bei der Kaltumformung werden Metalle unterhalb ihrer Rekristallisationstemperatur geformt, was die Festigkeit und Härte erhöht, aber die Duktilität verringern kann. Die Warmumformung hingegen findet oberhalb der Rekristallisationstemperatur statt, was eine leichtere Verformung und bessere Duktilität ermöglicht, aber häufig zu einer geringeren Festigkeit führt. Die Wahl zwischen diesen Methoden hängt von den gewünschten Materialeigenschaften, Kostenaspekten und der spezifischen Anwendung ab. Im Folgenden untersuchen wir die wichtigsten Vor- und Nachteile der Kaltumformung im Vergleich zur Warmumformung.
Wichtige Punkte erklärt:
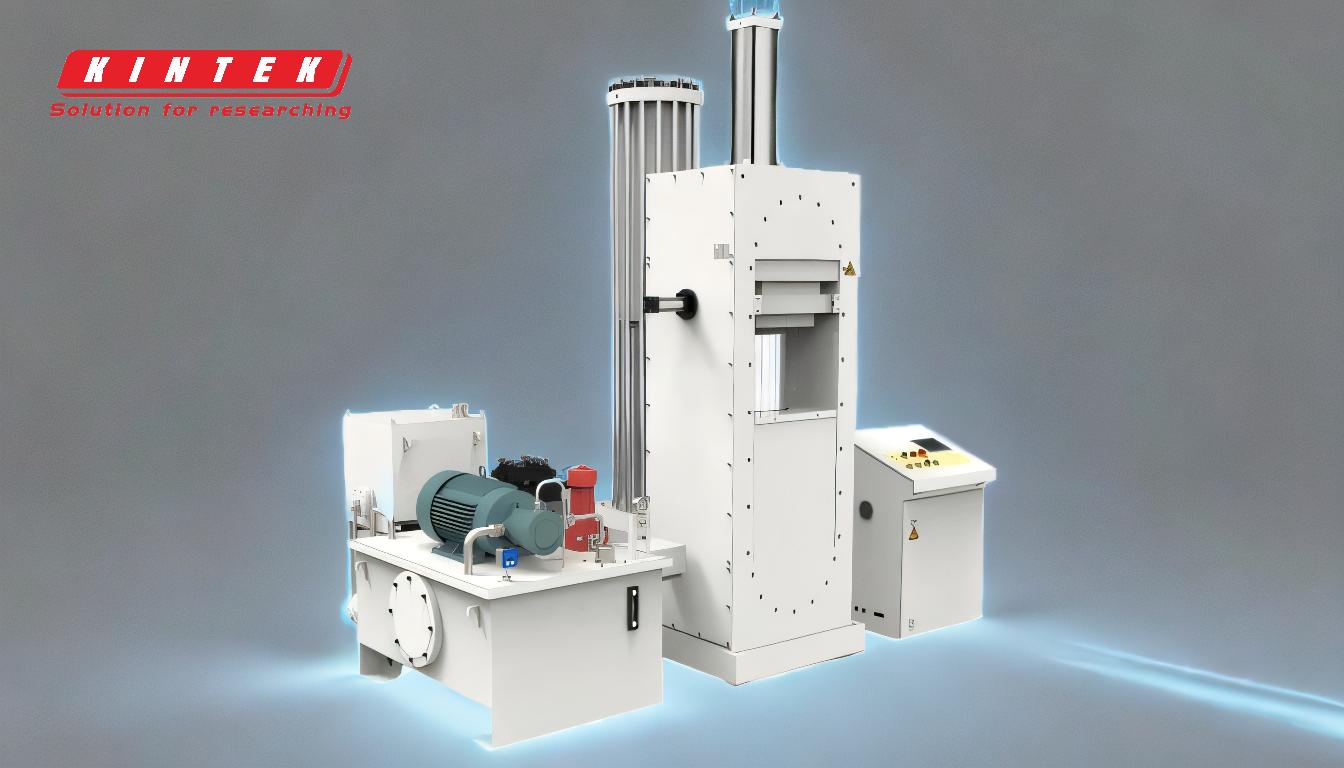
-
Vorteile der Kaltumformung:
-
Verbesserte mechanische Eigenschaften:
- Kaltumformung erhöht die Festigkeit und Härte von Metallen durch Kaltverfestigung. Dadurch eignet sich das Material besser für Anwendungen, die eine hohe Festigkeit erfordern.
-
Bessere Oberflächenbeschaffenheit:
- Der Prozess führt zu einer glatteren und präziseren Oberflächenbeschaffenheit, die oft aus ästhetischen oder funktionalen Gründen wünschenswert ist.
-
Maßgenauigkeit:
- Die Kaltumformung ermöglicht engere Toleranzen und eine präzisere Kontrolle der Abmessungen und eignet sich daher ideal für Anwendungen, die eine hohe Präzision erfordern.
-
Keine Heizung erforderlich:
- Da die Kaltumformung bei Raumtemperatur erfolgt, entfällt die Notwendigkeit einer Erwärmung, wodurch der Energieverbrauch und die mit der Hochtemperaturverarbeitung verbundenen Kosten gesenkt werden.
-
Verbesserte mechanische Eigenschaften:
-
Nachteile der Kaltumformung:
-
Reduzierte Duktilität:
- Der Prozess verringert die Duktilität des Metalls erheblich, wodurch es spröder und anfälliger für Risse unter Belastung wird.
-
Höhere Kraftanforderungen:
- Bei der Kaltumformung ist zur Verformung des Metalls mehr Kraft und Energie erforderlich als bei der Warmumformung, was den Maschinenverschleiß erhöhen kann.
-
Begrenzte Formkomplexität:
- Das Verfahren ist für die Bildung komplexer Formen weniger effektiv, da die verringerte Duktilität des Metalls seine Fähigkeit zur umfassenden Verformung einschränkt.
-
Eigenspannungen:
- Durch die Kaltumformung können Eigenspannungen im Material entstehen, die im Laufe der Zeit zu Verformungen oder Ausfällen führen können.
-
Reduzierte Duktilität:
-
Vorteile der Warmbearbeitung:
-
Verbesserte Duktilität:
- Die Warmumformung ermöglicht eine leichtere Verformung von Metallen und eignet sich daher für die Formung komplexer Geometrien und großer Bauteile.
-
Geringere Kraftanforderungen:
- Der Prozess erfordert im Vergleich zur Kaltumformung weniger Kraft, was die Belastung der Maschinen und den Energieverbrauch reduziert.
-
Kornverfeinerung:
- Durch die Warmbearbeitung kann die Kornstruktur des Metalls verfeinert und so seine mechanischen Eigenschaften und die Gesamtleistung verbessert werden.
-
Beseitigung von Eigenspannungen:
- Die hohen Temperaturen bei der Warmumformung tragen dazu bei, innere Spannungen abzubauen, was zu einem stabileren und gleichmäßigeren Material führt.
-
Verbesserte Duktilität:
-
Nachteile der Warmbearbeitung:
-
Geringere Festigkeit und Härte:
- Durch Warmumformung verarbeitete Metalle weisen im Allgemeinen eine geringere Festigkeit und Härte auf als kaltumgeformte Metalle.
-
Schlechte Oberflächenbeschaffenheit:
- Die hohen Temperaturen können zu Oxidation und Ablagerungen führen, was zu einer raueren Oberflächenbeschaffenheit führt, die möglicherweise eine zusätzliche Bearbeitung erfordert.
-
Maßungenauigkeit:
- Die Warmbearbeitung ist weniger präzise, was oft zu größeren Toleranzen und weniger Kontrolle über die Endabmessungen führt.
-
Energieverbrauch:
- Die Notwendigkeit, das Metall auf hohe Temperaturen zu erhitzen, erhöht den Energieverbrauch und die Betriebskosten.
-
Geringere Festigkeit und Härte:
-
Anwendungshinweise:
-
Materialauswahl:
- Die Wahl zwischen Kalt- und Warmumformung hängt von den Materialeigenschaften und den gewünschten Endanwendungseigenschaften ab. Beispielsweise wird die Kaltumformung für hochfeste Anwendungen bevorzugt, während die Warmumformung für komplexe Formen besser geeignet ist.
-
Kosten und Effizienz:
- Kaltumformung kann bei der Produktion in kleinem Maßstab oder wenn hohe Präzision erforderlich ist, kostengünstiger sein, während Warmumformung bei der Produktion in großem Maßstab oft effizienter ist.
-
Umweltauswirkungen:
- Die Kaltumformung hat eine geringere Umweltbelastung, da keine Hochtemperaturverarbeitung erfolgt, was sie in manchen Fällen zu einer nachhaltigeren Option macht.
-
Materialauswahl:
Zusammenfassend lässt sich sagen, dass sowohl die Kaltumformung als auch die Warmumformung ihre jeweiligen Vor- und Nachteile haben und die Wahl zwischen ihnen von den spezifischen Anforderungen der Anwendung abhängt. Die Kaltumformung bietet eine verbesserte Festigkeit, Präzision und Oberflächengüte, allerdings auf Kosten einer verringerten Duktilität und eines höheren Kraftbedarfs. Warmumformen hingegen sorgt für eine bessere Duktilität und leichtere Verformung, kann jedoch zu einer geringeren Festigkeit und einer raueren Oberflächenbeschaffenheit führen. Das Verständnis dieser Kompromisse ist entscheidend für die Auswahl des am besten geeigneten Metallumformverfahrens.
Übersichtstabelle:
Aspekt | Kaltumformung | Heißes Arbeiten |
---|---|---|
Stärke und Härte | Erhöht durch Kaltverfestigung | Im Allgemeinen niedriger |
Duktilität | Reduziert, wodurch das Metall spröder wird | Verbessert, was eine leichtere Verformung ermöglicht |
Oberflächenbeschaffenheit | Glatter und präziser | Rauer aufgrund von Oxidation und Ablagerungen |
Maßgenauigkeit | Engere Toleranzen und bessere Präzision | Weniger präzise, größere Toleranzen |
Energieverbrauch | Niedriger, da keine Heizung erforderlich ist | Höher aufgrund der Hochtemperaturverarbeitung |
Formkomplexität | Aufgrund der verminderten Duktilität eingeschränkt | Besser geeignet für komplexe Formen |
Eigenspannungen | Kann Eigenspannungen einführen | Beseitigt Eigenspannungen |
Benötigen Sie Hilfe bei der Auswahl des richtigen Metallumformverfahrens? Kontaktieren Sie noch heute unsere Experten für maßgeschneiderte Lösungen!